Georg Fischer Automotive Standardizes Quality Management with Opcenter Quality
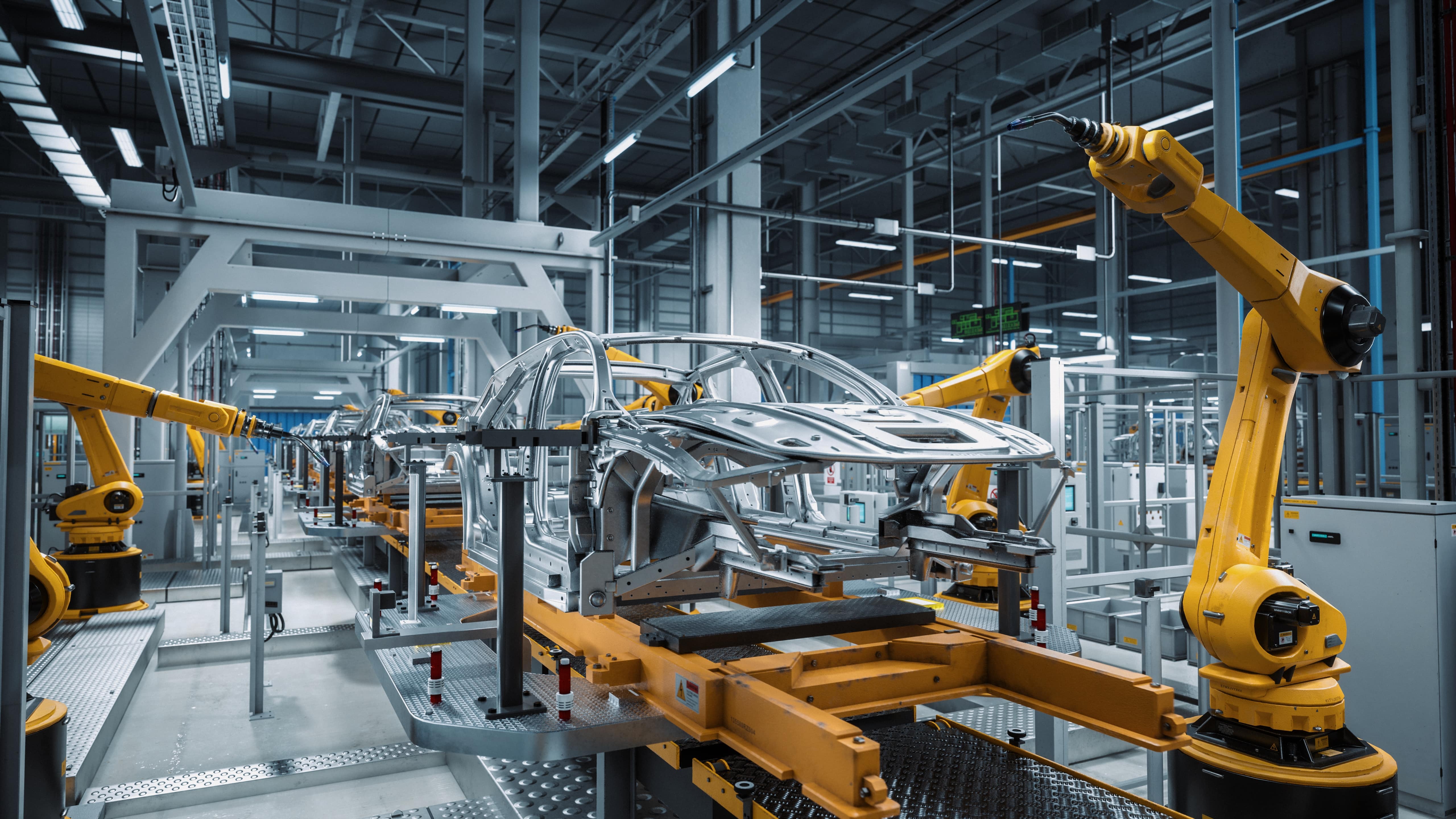
Industry
Manufacturing
Challenge
Georg Fischer Automotive faced the challenge of standardizing quality management across its diverse production sites. The lack of data consistency in their heterogeneous system environment hindered their ability to meet customer and compliance requirements.
Results
Implementing Opcenter Quality allowed Georg Fischer Automotive to standardize their quality management processes, streamline data tracking, and improve customer satisfaction by reducing reaction times. The company saw increased process stability and efficiency, along with higher transparency in quality management.
Key Product
Opcenter Quality
We set our sights on achieving increased process stability and efficiency with the use of standardized CAQ software throughout the division. Using Opcenter Quality has helped us to achieve this ambitious objective.
Joerg Nawrocki
Head of Quality and CoC Logistics, Georg Fischer Automotive
The introduction of Opcenter Quality has enabled us to increase the transparency of quality management at Georg Fischer. Following implementation of the individual modules and monitoring of the corrective actions put in place, we saw an increase in customer satisfaction.
Michael Edbauer
Head of Quality Management and Logistics, Georg Fischer Automotive
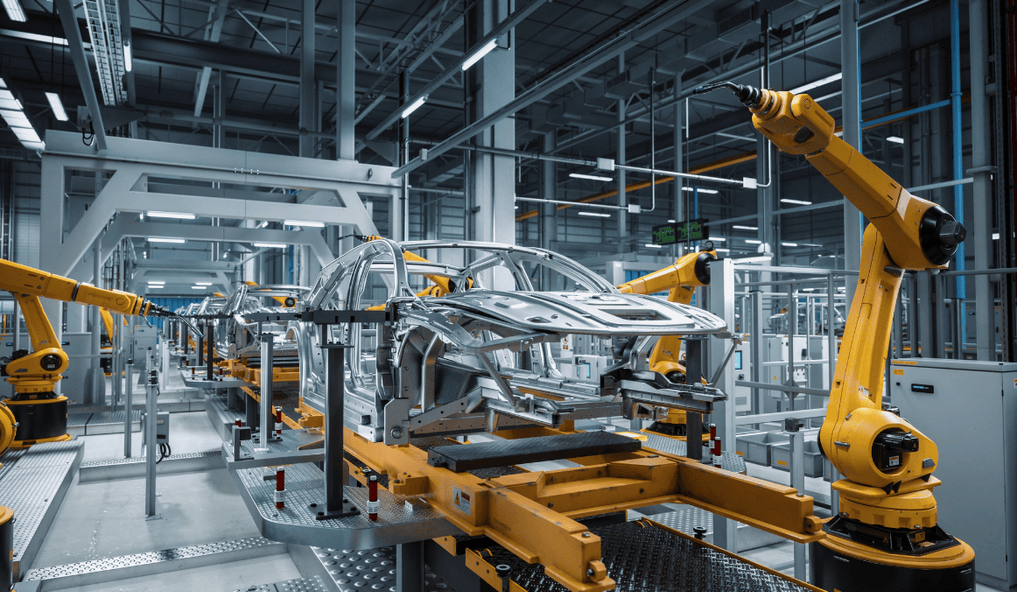
About the Customer
Georg Fischer Automotive, a division of Georg Fischer AG, is an international industrial group based in Schaffhausen, Switzerland. With over 50 production sites and 130 companies worldwide, the company employs approximately 14,000 people. GF Automotive specializes in developing and manufacturing cast iron, aluminum, and magnesium parts for the automotive industry.The Challenge
Georg Fischer Automotive was confronted with the challenge of standardizing quality management processes across its numerous production sites. The company struggled with a heterogeneous system environment, leading to inconsistent data that affected their ability to meet both customer and compliance requirements. This inconsistency presented significant hurdles in maintaining quality standards and ensuring customer satisfaction.
The Solution
To address these challenges, Georg Fischer Automotive decided to implement Opcenter Quality by Siemens Digital Industries Software. After evaluating different solutions, they chose Opcenter Quality for its comprehensive features tailored to standardize and optimize quality processes.
Joerg Nawrocki, Head of Quality and CoC Logistics at Georg Fischer Automotive, stated,
We set our sights on achieving increased process stability and efficiency with the use of standardized CAQ software throughout the division. Using Opcenter Quality has helped us to achieve this ambitious objective. The implementation process was completed in nine months in China, and the company began to see immediate improvements in data consistency and process efficiency.
The Results
After implementing Opcenter Quality, Georg Fischer Automotive successfully standardized its quality management processes. The solution optimized the complete product lifecycle and simplified data tracking.
Michael Edbauer, Head of Quality Management and Logistics at Georg Fischer Automotive, noted, 'The introduction of Opcenter Quality has enabled us to increase the transparency of quality management at Georg Fischer. Following implementation of the individual modules and monitoring of the corrective actions put in place, we saw an increase in customer satisfaction.' The results were evident: increased process stability, enhanced efficiency, and higher customer satisfaction due to reduced reaction times.
The company, with a workforce of 14,000 across 50 production sites and 130 companies worldwide, now enjoys a more streamlined and effective quality management system.