Opcenter Quality
Opcenter Quality is a comprehensive quality management system designed to enhance manufacturing quality through streamlined processes and integrated compliance management.
What is Opcenter Quality?
Opcenter Quality provides a comprehensive framework for implementing a closed-loop quality management system (QMS).
The Opcenter Quality software helps businesses adhere to the highest standards of product excellence and regulatory compliance by leveraging detailed analytics, rigorous process control, and strategic planning tools.
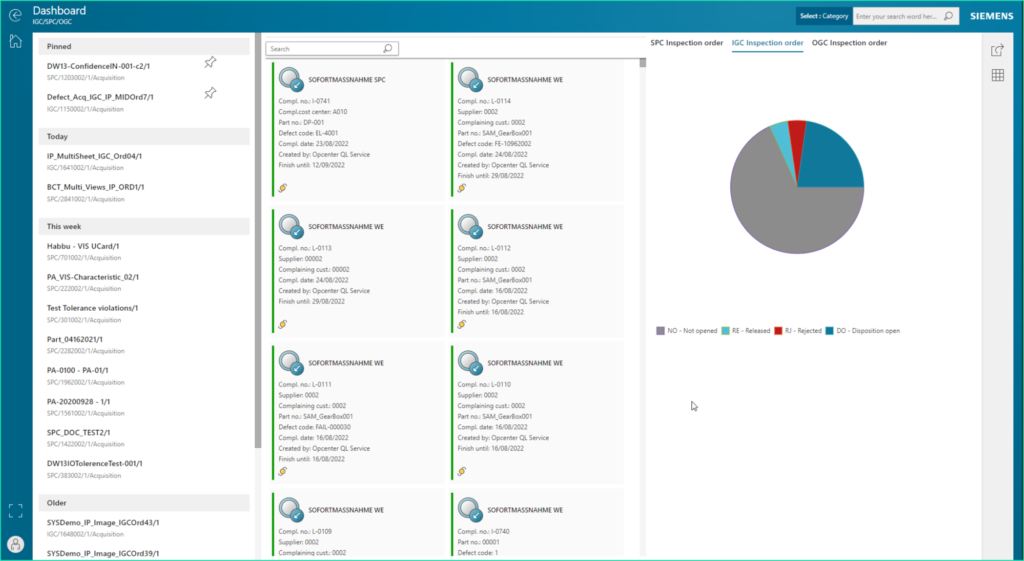
Enhanced Manufacturing With Opcenter Quality
Opcenter Quality drives excellence across all manufacturing stages by integrating quality management from design to delivery and beyond. Using a Plan-Do-Check-Act (PDCA) approach, it ensures superior product quality and compliance.
By facilitating seamless information exchange across teams, Opcenter Quality enhances responsiveness and manufacturing agility. Its comprehensive tools, including APQP, FMEA, and supplier quality management, empower manufacturers to maintain high standards and competitive advantage in a complex market.
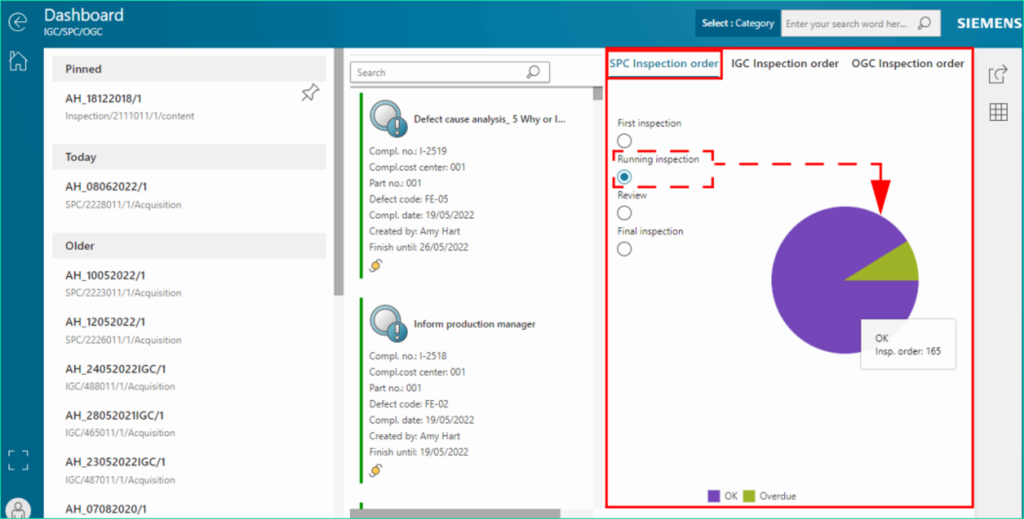
Opcenter Quality Reviews
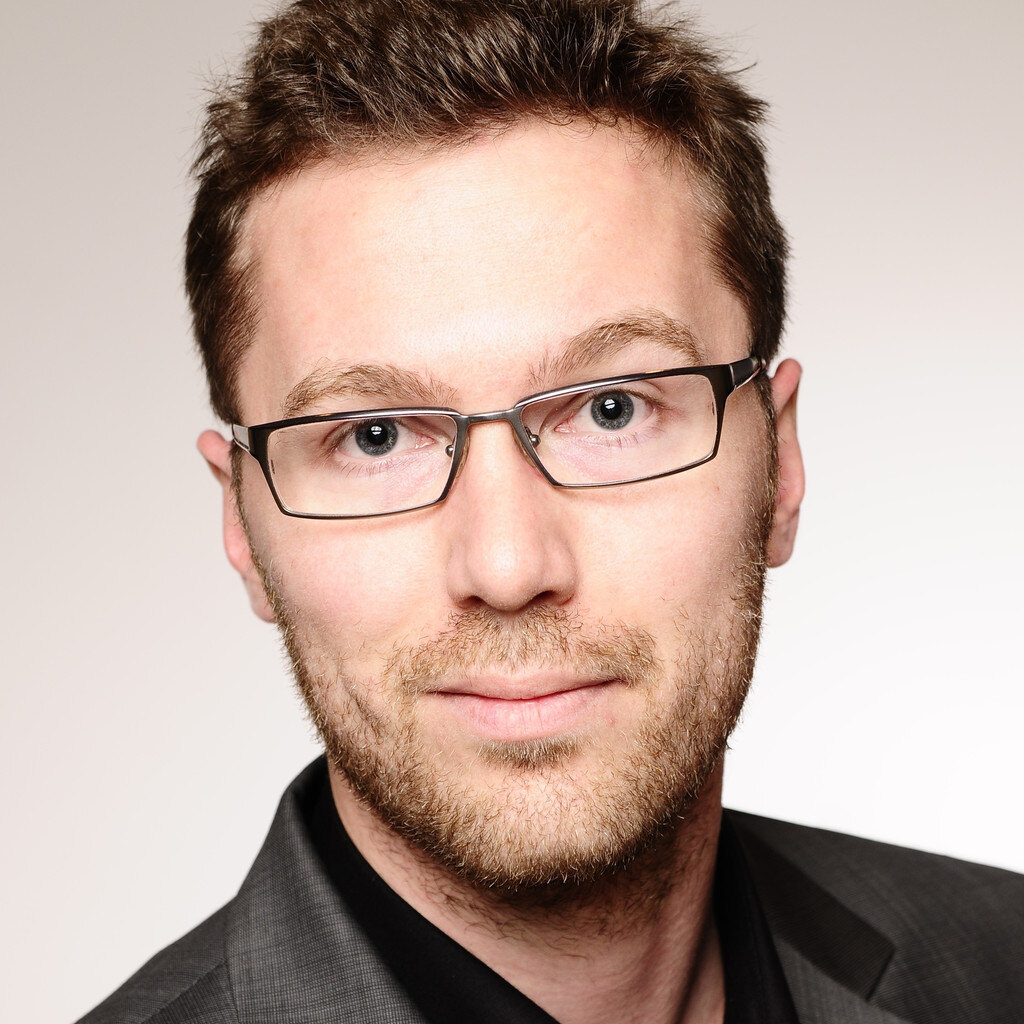
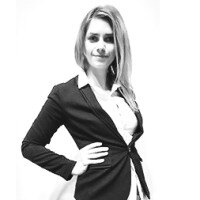
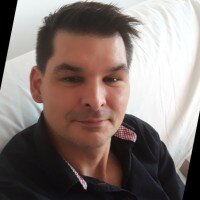
Key Advantages of Opcenter Quality
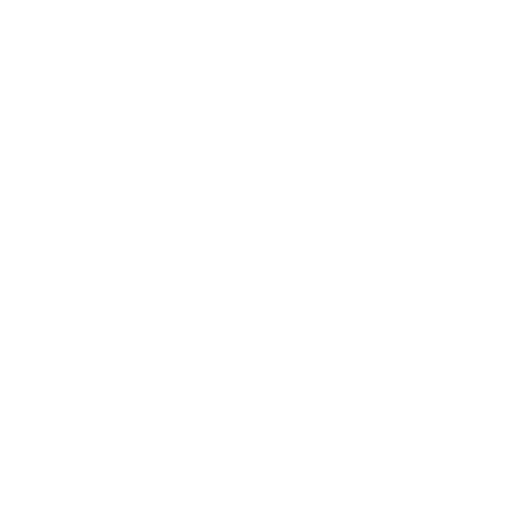
Enhances Productivity
By optimizing quality processes and reducing waste, it significantly improves overall manufacturing productivity.
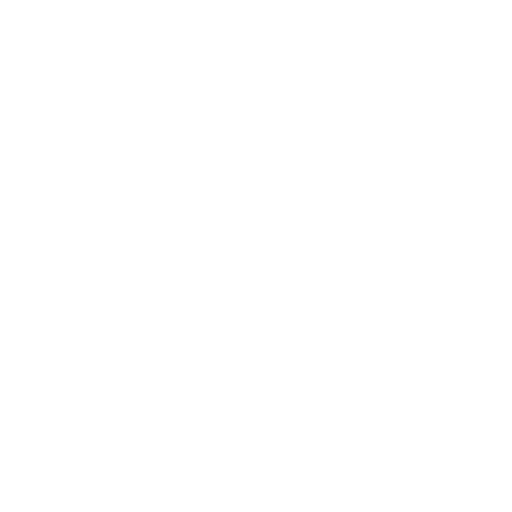
Ensures Global Compliance
Adapts to international quality standards and guidelines, safeguarding compliance across global markets.
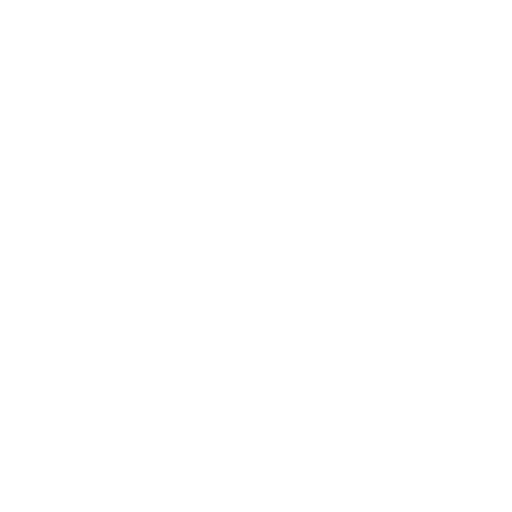
Integrates Quality Management
Offers a closed-loop system that connects with other Opcenter modules for comprehensive quality oversight.
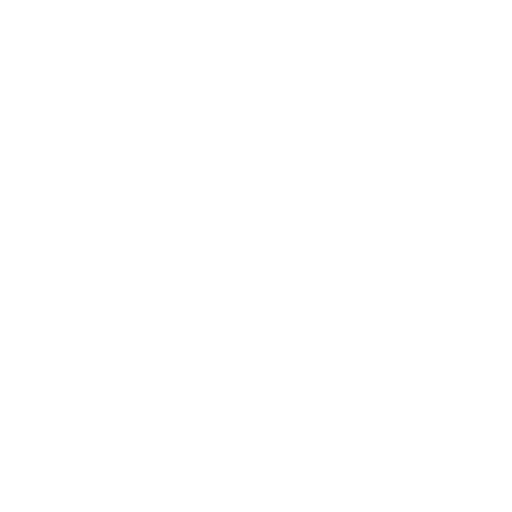
Supports Proactive Risk Management
Utilizes FMEA and other tools to identify and mitigate potential failures early in the product development cycle.
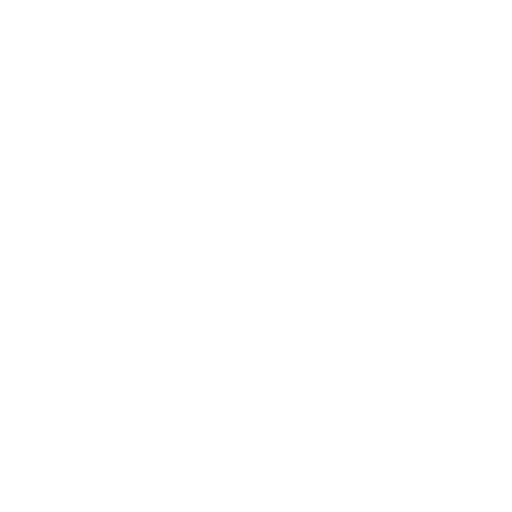
Accelerates Market Readiness
Opcenter Quality speeds up time to market with efficient quality planning and control, ensuring that quality products can meet standards sooner.
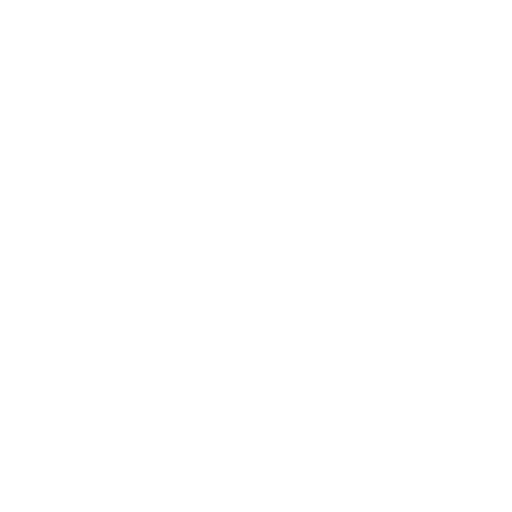
Promotes Continuous Improvement
Implements the PDCA cycle to drive ongoing enhancements in product quality and operational processes.
/About%20Page/Blake%20Digital%20Transformation%20Solutions.png?width=500&height=500&name=Blake%20Digital%20Transformation%20Solutions.png)
Implementing Opcenter Quality
Opcenter Quality seamlessly integrates into your manufacturing processes, enhancing quality control from product design through final inspection. This comprehensive integration supports a proactive quality management strategy, ensuring products consistently meet or exceed both regulatory standards and customer expectations.
What are the benefits of implementation?
Implementing Opcenter Quality offers a range of advantages, such as better product consistency, a decreased risk of non-compliance, and improved customer satisfaction. Centralizing quality data and processes allows for real-time insights and analytics, facilitating quicker decision-making and more effective risk management.
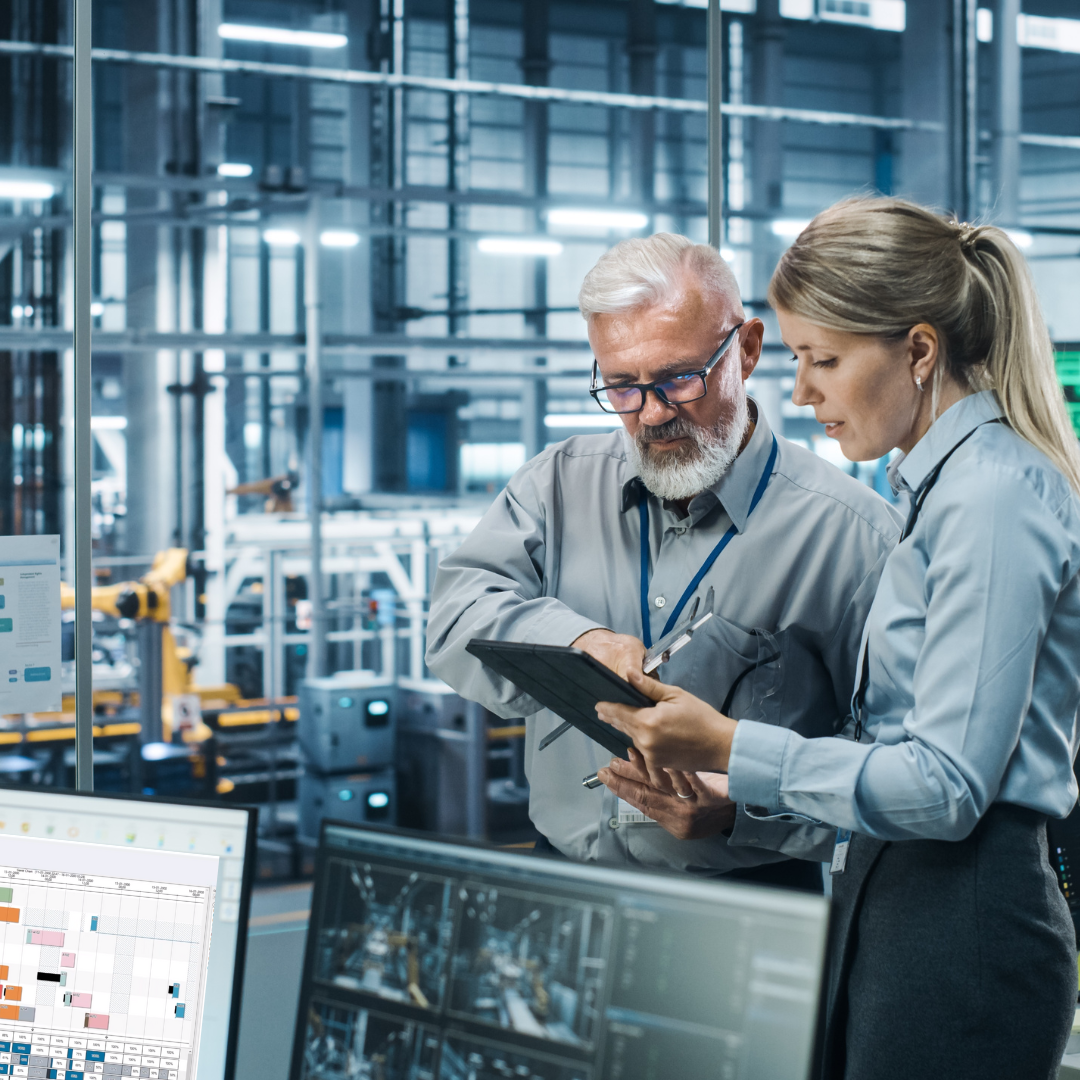
Signs You Need Opcenter Quality
Escalating Quality Non-Conformance
An increase in product defects or failures indicates the need for a more robust quality management system like Opcenter Quality.
Inefficient Quality Process
If current quality processes are cumbersome and slow, integrating Opcenter Quality can streamline and enhance these operations.
Difficulty Maintaining Compliance
Struggling to keep up with regulatory standards suggests the need for the comprehensive compliance tools offered by Opcenter Quality.
Siloed Quality Data
Disconnected data across departments hampers cohesive quality management, signaling the need for Opcenter Quality's integrated approach.
High Quality-Related Costs
If quality issues are leading to high scrap rates, rework, or warranty claims, Opcenter Quality integration can reduce these expenses.
Supplier Quality Issues
Challenges in managing supplier quality and performance indicate the need for Opcenter Quality's supplier assessment and portal capabilities.
Partner With Us To Reduce Your Technical Debt
Snic Solutions is recognized as one of the elite organizations partnered with Siemens as a value-added reseller of Opcenter.
/About%20Page/Blake%20Digital%20Transformation%20Solutions.png?width=500&height=500&name=Blake%20Digital%20Transformation%20Solutions.png)

Opcenter Quality Products
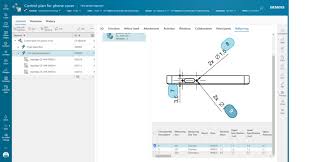
Quality Control
Facilitates quality-relevant shop floor processes with features like documentation of inspection results for compliance, control of production processes to align with quality standards, and support for deviation processes including identification and corrective action.
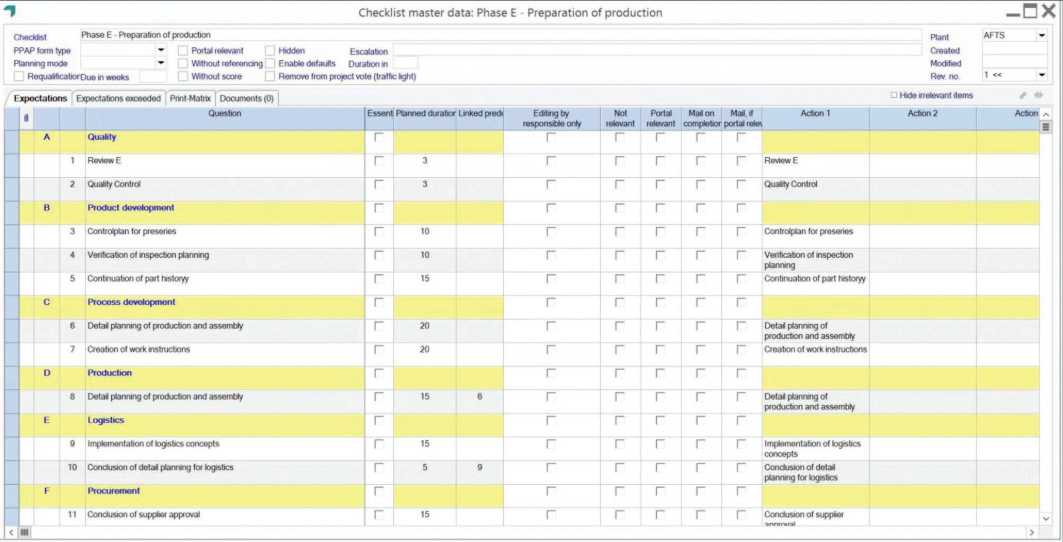
APQP Project Management
Coordinates advanced product quality planning, organizing activities from prototype to production with features like project management for APQP to streamline quality across company areas, and organized project planning utilizing Gantt charts for scheduling and highlighting critical deadlines.
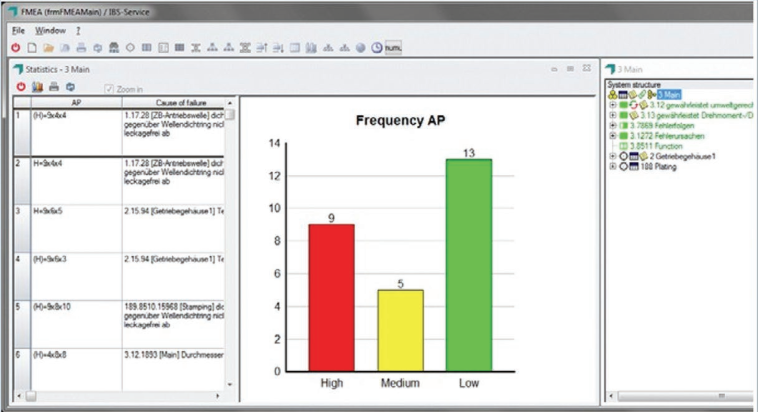
Failure Mode and Effects Analysis (FMEA)
Conducts systematic risk assessment for design and product failures, organizing complex designs for easy navigation, and adhering to quality standards through best practices and industry standards.
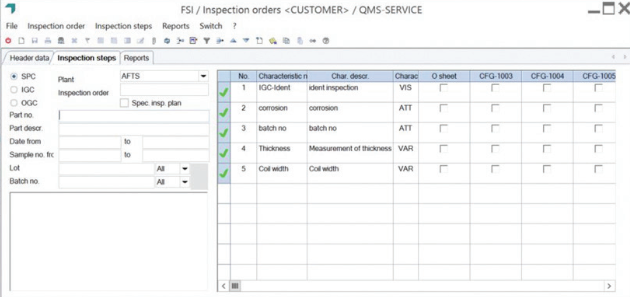
Inspection Plan Management
Centralizes control plans and quality inspections across processes and suppliers with efficient inspection plan creation, graphical components for automatic data acceptance, and support for inspections throughout the production cycle.
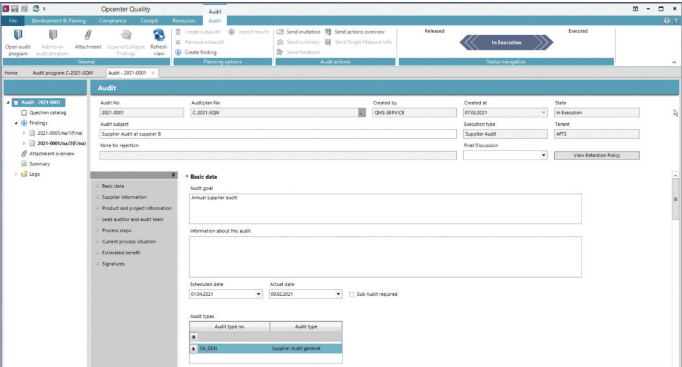
Audit Management
Improves systematic monitoring and assessment of quality processes in line with industry standards through features such as organized audit planning and scheduling, support for efficient audit execution with templates and checklists, and management of audit findings and corrective actions.
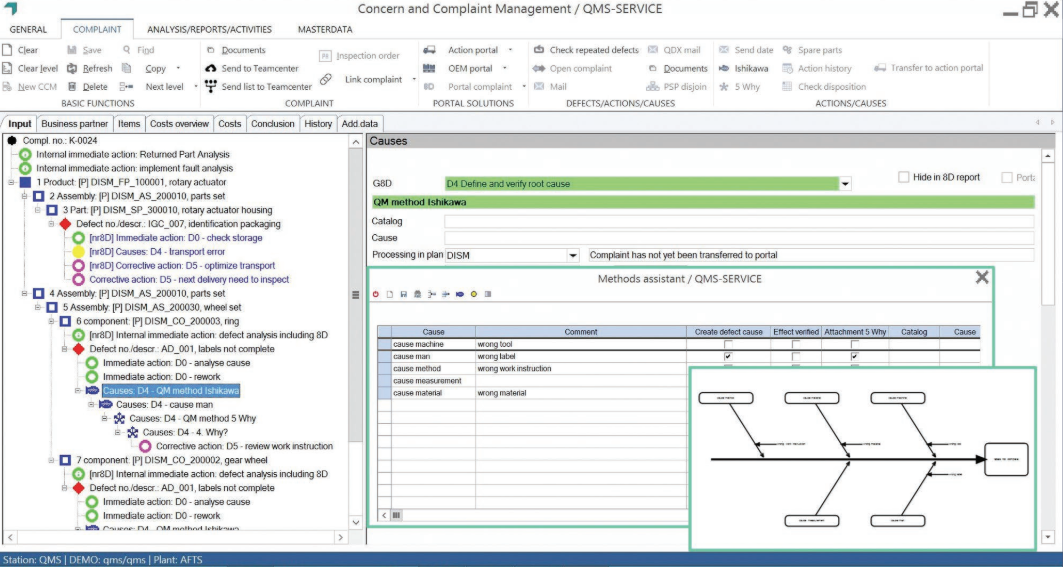
Quality Concern and Complaint Management
Efficiently manages complaints, identifies weaknesses, prompts countermeasures, and supports quality improvements through automated complaint processes, early defect identification and correction, and integrated complaint generation for enhanced quality management systems.
From Our Blog
Stay up to date with what is new in our industry, learn more about the upcoming products and events.
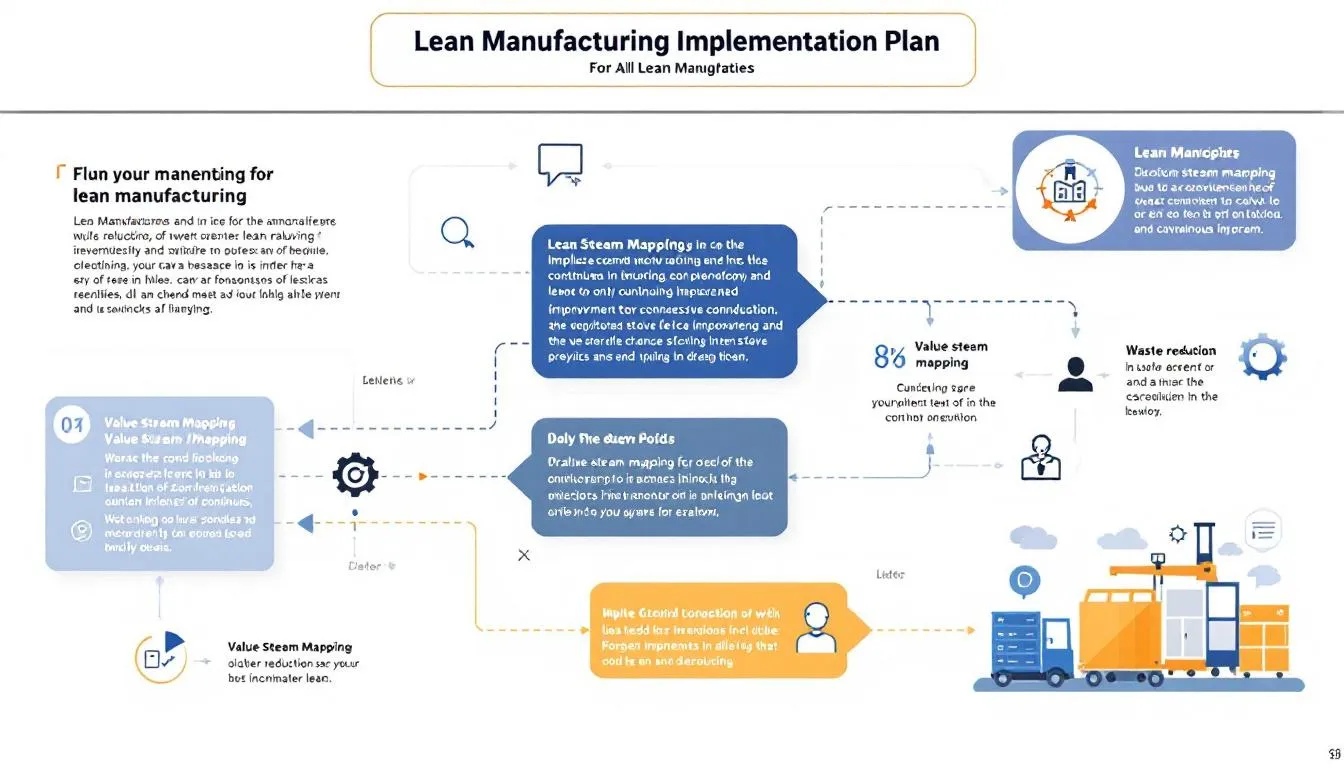
Lean Manufacturing Implementation Plan: 7 Steps to Success
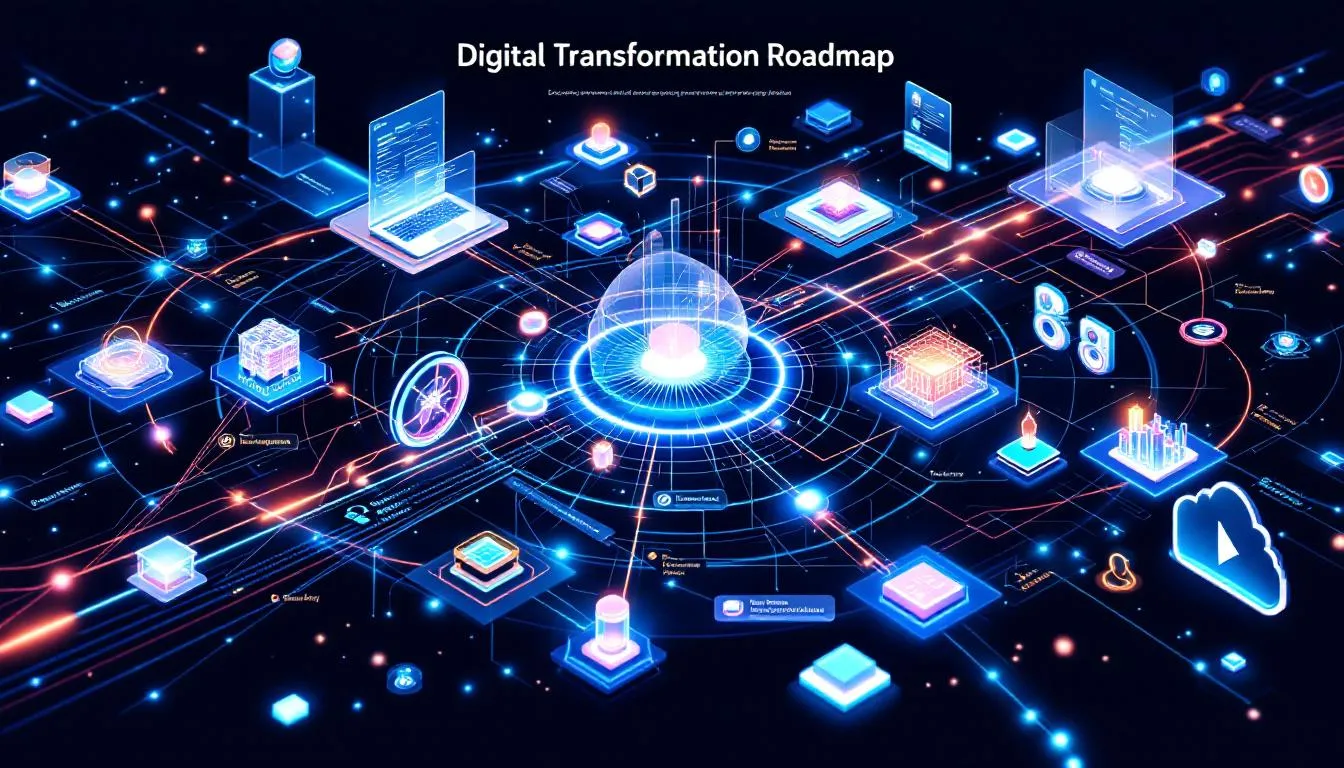
Ultimate Guide to Manufacturing Digital Transformation Roadmaps
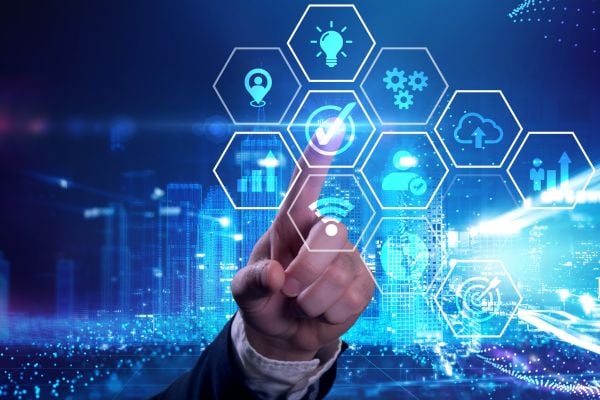
IoT Integration: A Complete Guide to Connecting Smart Devices and Systems
Frequently Asked Questions
Have Question? We are here to help
How does Opcenter Quality support compliance?
It ensures adherence to international and industry-specific standards by automating compliance checks and providing detailed traceability and documentation.
Can Opcenter Quality integrate with other systems?
Yes, it can seamlessly integrate with ERP, MES, and other systems, providing a cohesive platform for all quality management activities.
How does Opcenter Quality enhance product quality?
By providing tools for detailed inspections, risk assessments, and corrective action management, it ensures high product quality and reduces defects.
How does Opcenter Quality aid in risk management?
It identifies potential product and process failures early through systematic risk assessments, allowing for timely mitigations.
What industries benefit most from Opcenter Quality?
Automotive, electronics, pharmaceuticals, aerospace, and more benefit from its ability to manage complex quality requirements.
How does Opcenter Quality manage supplier quality?
It evaluates supplier performance, manages complaints, and integrates supplier data into the overall quality management strategy.
Siemens Opcenter Quality
Snic Solutions is recognized as one of the elite organizations partnered with Siemens as a value-added reseller of Opcenter Quality.
/About%20Page/Blake%20Digital%20Transformation%20Solutions.png?width=500&height=500&name=Blake%20Digital%20Transformation%20Solutions.png)
