Lean Manufacturing Implementation Plan: 7 Steps to Success
Need to implement a lean manufacturing? A successful Lean manufacturing implementation plan requires company-wide commitment and leadership engagement.
This guide will walk you through seven steps to eliminate waste, streamline operations, and boost efficiency in your organization.
Key Takeaways
-
Setting a clear vision and aligning leadership and stakeholders are foundational for successful Lean Manufacturing implementation.
-
Establishing a culture of continuous improvement and providing regular training are essential for sustaining Lean practices across an organization.
-
Measuring success through Key Performance Indicators (KPIs), customer feedback, and cost savings is critical for evaluating the effectiveness of Lean initiatives.
-
Managing Lean implementation as a structured project, with clear plans and cross-functional collaboration, ensures alignment and continuous improvement.
-
Identifying and mitigating risk early in the Lean journey is essential for project success and stakeholder buy-in.
-
Lean manufacturing focuses on delivering value that customers are willing to pay for, eliminating unnecessary costs.
Setting the Stage for Lean Manufacturing
Setting the stage for Lean Manufacturing is akin to laying a strong foundation for a building. Without a clear vision, committed leadership, and a thorough understanding of your current state, your Lean journey might falter before it even begins. Establishing a cohesive vision and securing leadership commitment form the bedrock of effective Lean transformation. Getting everyone on board with your “why” and spreading Lean principles is key to a successful implementation.
The first step for organizations wanting to implement lean manufacturing is gaining alignment across the organization. Such alignment mitigates risks and secures buy-in from all stakeholders, implementing lean manufacturing. Leadership plays a crucial role in fostering a culture dedicated to reducing waste throughout the organization, which is central to Lean manufacturing success.
In the following subsections, we’ll delve deeper into defining your vision and goals, engaging leadership and stakeholders, and assessing your current state.
Define Your Vision and Goals
A well-defined vision guides strategic decisions and serves as a roadmap for overall goals in Lean initiatives. A shared vision among team members fosters unity and drives motivation toward common objectives. Specific goals aligned with the vision ensure all team members work toward the same outcomes.
A clear vision and specific goals align your team and help realize the full potential of Lean practices. This plan serves as a north star, guiding decisions and actions to keep your Lean journey focused and effective.
Engage Leadership and Stakeholders
Leadership must actively engage with teams to foster an environment conducive to Lean principles. Key aspects include:
-
Active leadership involvement to create a supportive framework for effectively implementing Lean methodologies.
-
Regular communication of progress to stakeholders to enhance buy-in during the Lean process.
-
Use of visual management tools to significantly improve communication and collaboration during Lean training.
-
A visible champion of Lean can help inspire others and navigate the challenges of cultural shifts, ensuring sustained commitment to Lean practices.
-
Active leadership involvement to create a supportive framework for effectively implementing Lean methodologies.
-
Regular communication of progress to stakeholders to enhance buy-in during the Lean process.
-
Use of visual management tools to significantly improve communication and collaboration during Lean training.
Leadership and stakeholder engagement is crucial for successful Lean implementation. It ensures that everyone is on the same page and committed to the Lean transformation. Active leadership and clear communication significantly impact the success of Lean initiatives.
Assess Current State
A thorough assessment of current processes identifies inefficiencies and sets a baseline for improvements. This assessment helps you understand where you are starting from and what areas need immediate attention. It’s the first step in creating a roadmap and setting realistic expectations for future improvements.
Building a Lean Culture
Building a Lean culture throughout the organization is crucial for the long-term sustainability of Lean practices. Commitment from all levels of the organization is essential for long-term success in Lean practices. A culture of continuous improvement is vital for the longevity of Lean practices. The 5S methodology focuses on organizing the workplace to eliminate inefficiencies and establish a clean working environment.
In this section, we will explore how to foster a culture of continuous improvement, promote team collaboration, and train and educate employees. Each of these elements plays a vital role in building a robust Lean culture that supports ongoing improvements and innovative solutions.
Foster a Culture of Continuous Improvement
Recognizing both major and minor achievements fosters a culture of continuous improvement. Acknowledging achievements boosts team morale and encourages continuous improvement. Recognition fosters ongoing engagement and drives continuous improvement. Fostering a mindset focused on continuous improvement is vital for Lean manufacturing success.
A culture of continuous improvement not only enhances productivity but also ensures that Lean practices are ingrained in the organizational DNA. It’s about creating an environment where every employee feels valued and motivated to contribute to the ongoing success of Lean initiatives.
Promote Team Collaboration
Cross-department collaboration can lead to:
-
Innovative solutions and reduced waste, enhancing overall efficiency.
-
Quicker problem-solving and innovation through team collaboration.
-
Enhanced communication and diverse perspectives via cross-functional teams.
-
Increased respect among team members, which further enhances collaboration and leads to innovative solutions.
Kanban boards make workflows visible and facilitate team collaboration. Team collaboration is essential for successful Lean implementation. It ensures everyone works toward common goals and leverages each other’s strengths to overcome challenges.
Train and Educate Employees
Frequent training sessions on Lean principles provide several benefits:
-
Keep employees knowledgeable and engaged in continuous improvement.
-
Keep employees informed about the latest Lean methodologies.
-
Keep employees engaged and knowledgeable about best practices through ongoing education.
-
Hands-on training significantly improves practical understanding of Lean methodologies.
Incorporating hands-on training helps employees better understand and apply Lean principles in their daily tasks. Continuous education on Lean tools is crucial for effectively applying Lean principles. Regular training ensures employees remain proficient in Lean methodologies. Training and educating employees enhance their skills and foster a sense of ownership and commitment to Lean initiatives.
Mapping the Value Stream
Value stream mapping is critical for identifying waste and optimizing processes in Lean manufacturing. It:
-
Visually represents all actions involved in delivering a product or service.
-
Assesses the series of actions required to deliver a product or service, highlighting areas for waste reduction.
-
Visualizes the flow of materials and information, making it easier to detect waste.
In this section, we will discuss how to identify value streams, analyze the current state, and design the future state. Each of these steps is crucial for creating a streamlined process that enhances efficiency and minimizes waste. Key tools for implementing Lean manufacturing include value stream mapping and Kanban boards, which are instrumental in visualizing workflows and identifying inefficiencies. Tracking lead time as a key metric is essential for evaluating process efficiency and measuring progress toward Lean goals.
Identify Value Streams
Identifying value streams helps organizations prioritize processes that add value to the customer. It involves recognizing all processes that contribute to creating and delivering value to customers.
Organizations need to consider which processes create value for the customer and align resources accordingly to identify value streams.
Analyze Current State
Mapping the current state:
-
Visualizes inefficiencies and identifies bottlenecks in workflows.
-
Highlights inefficiencies and areas for improvement by representing the existing workflow visually.
-
Requires collecting data on each process step, including cycle and changeover times, to pinpoint inefficiencies.
Analyzing the current state is crucial for identifying areas needing improvement. It provides a clear picture of existing core processes and helps identify specific areas requiring attention.
Design Future State
Designing a future state map optimizes processes to enhance efficiency and minimize waste. It involves:
-
Establishing a vision for an improved process that minimizes waste and enhances value
-
Focusing on reducing lead times and streamlining processes
-
Aligning with Lean principles
Creating a future state map envisions a better, more efficient process. It’s the first step in planning and developing a roadmap for achieving Lean goals.
Implementing Lean Tools
Establishing a visual workflow, such as a Kanban board, is crucial for implementing a pull system effectively. Lean tools streamline processes and reduce waste, enabling organizations to operate more efficiently.
In this section, we will explore the implementation of Kanban boards, WIP limits, and the 5S methodology that have been implemented. These tools are fundamental to achieving a successful Lean transformation.
Kanban Boards
Kanban boards are visual workflow management tools that help in visualizing workflows and managing tasks to identify bottlenecks. Using Kanban boards in Lean manufacturing significantly improves task management and overall productivity.
WIP Limits
Work-In-Progress (WIP) limits on Kanban boards manage capacity. WIP limits are crucial for maintaining productivity and ensuring efficient task completion. Implementing WIP limits helps teams reduce waste and effectively deliver value to customers, aligning with Lean principles of efficiency and customer focus.
They help achieve continuous flows in Lean organizations by preventing bottlenecks and enhancing flow.
5S Methodology
The 5S methodology consists of five steps:
-
Sort
-
Straighten
-
Shine
-
Standardize
-
Sustain Each step enhances workplace improvement. The 5S methodology improves efficiency and reduces waste, leading to a more organized and productive work environment.
Maintaining 5S practices is essential for continuous improvement and long-term success in workplace organization. It creates a workplace that supports Lean principles and enhances overall productivity.
Establishing a Pull System
Transitioning from a push system to a pull system enhances productivity and customer satisfaction by aligning output with actual demand. A pull system allows organizations to respond more flexibly to customer needs and reduces overproduction.
In this section, we will discuss the differences between push and pull systems, how to implement pull mechanisms, and the importance of monitoring and adjusting the pull system.
Understand Push vs. Pull Systems
A pull system improves team productivity by ensuring coworkers finish existing tasks before starting new ones. Continuous delivery in Lean manufacturing aims to create more value for customers through the Toyota production system.
Push and pull systems differ in the following ways:
-
Push systems produce items based on projected demand.
-
Pull systems produce items as needed based on actual demand.
-
In push systems, excess inventory accumulates.
-
In pull systems, inventory levels are optimized based on real-time needs.
Implement Pull Mechanisms
A push system rely on forecasts of future demand, while a pull system focuses on current customer orders to dictate production.
Begin with a single team and gradually implement Lean manufacturing to minimize disruptions and develop pilot changes.
Monitor and Adjust
A pull system leads to significant improvements in productivity, efficiency, and morale with minimal effort, enhancing overall energy. Regular monitoring of the pull system identifies inefficiencies and ensures optimal operations.
Adjustments based on insights gained during monitoring enhance system performance.
Sustaining Lean Practices
A Lean culture emphasizes regular improvement and involves all employees in enhancing processes to meet customer needs. A supportive cultural environment is crucial for successfully adopting Lean principles.
In this section, we will discuss the importance of regular audits and reviews, continuous training and development, and celebrating successes. These elements are essential for sustaining Lean practices and ensuring long-term success.
Regular Audits and Reviews
Regular audits ensure Lean practices are maintained across the organization. Key aspects include:
-
Frequent evaluations identify deviations from Lean standards and foster accountability.
-
Periodic reviews ensure Lean practices are consistently upheld and improved.
-
Monitoring cost reductions and efficiency improvements indicates success in Lean implementation.
Tracking financial metrics, such as cost savings and efficiency improvements, evaluates the overall effectiveness of Lean practices. Regular audits combined with monitoring financial metrics significantly enhance the effectiveness of Lean practices. This approach ensures Lean initiatives are on track and delivering the expected benefits.
Continuous Training and Development
Lean manufacturing advocates a continuous improvement mindset, embracing each failure as a growth opportunity. Celebrating failures within a team fosters an environment prioritizing learning and development. Regular feedback sessions within teams promote continuous improvement and strengthen team dynamics.
Ongoing training and development ensure Lean skills remain current and effectively trained.
Celebrate Successes
Celebrating successes in Lean manufacturing maintains motivation and reinforces team efforts. Recognizing achievements energizes teams and fosters a positive work environment. Celebrations create a feedback loop encouraging ongoing engagement with Lean practices.
Companies must maintain good habits built during the transition to sustain the lean enterprise business culture. Celebrating successes boosts morale and reinforces the importance of continuous improvement and the positive impact of lean practices, which support the overall goals of the organization.
Measuring Success
Identifying and tracking key metrics is crucial for determining the effectiveness of Lean manufacturing practices. Collecting data and using analytics across each process step are essential for tracking performance during Lean implementation. Using a structured method for tracking performance, such as A3 plans or analytics, is essential for systematic improvement. Lean manufacturing metrics and methods can also be adapted to suit the unique needs of other industries, not just manufacturing. Measuring success in Lean implementation involves evaluating how well the organization aligns with Lean principles and delivers value to the customer.
In this section, we will discuss the importance of Key Performance Indicators (KPIs), customer feedback, and cost savings and efficiency gains. These metrics provide a comprehensive view of the success and areas for improvement in Lean initiatives.
Key Performance Indicators (KPIs)
KPIs in Lean implementation serve as goalposts to measure progress. These indicators should be tailored to the specific goals and processes of the organization. They are essential tools for measuring productivity, efficiency, and the overall success of Lean initiatives.
Customer Feedback
Collecting customer feedback is vital for assessing the impact of Lean practices on customer satisfaction. Gathering customer insights can reveal the effectiveness of Lean initiatives and highlight areas needing enhancement. Actively soliciting and analyzing customer feedback helps identify areas for improvement in Lean practices. Utilizing customer feedback is vital for assessing the success of Lean initiatives and identifying potential areas for enhancement.
Customer feedback not only provides insights into the effectiveness of Lean practices but also helps in aligning future improvements with customer’s needs. It ensures that the organization remains responsive to real-time customer demand, resulting in increased customer satisfaction.
Cost Savings and Efficiency Gains
Tracking cost savings is crucial as it gives organizations clear evidence of the financial impact of Lean initiatives. Cost savings metrics should align with the organization’s overall financial goals to demonstrate value. Efficiency gains can be measured by analyzing:
-
Throughput
-
Cycle times
-
Waste reduction Regular assessments should be conducted to quantify improvements in:
-
Workforce productivity
-
Resource utilization.
Utilizing metrics effectively allows organizations to identify areas that require further improvements and sustain Lean practices. Continuous improvement initiatives should incorporate feedback from the metrics to refine processes and strategies. This approach ensures that Lean initiatives continue to deliver value and drive ongoing improvements.
Summary
In summary, implementing Lean Manufacturing involves a comprehensive approach that includes setting clear goals, engaging leadership, building a Lean culture, and effectively using Lean tools. Establishing a pull system, sustaining Lean practices, and measuring success through KPIs, customer feedback, and cost savings are essential for long-term success. By following these steps, organizations can achieve operational excellence, reduce waste, and enhance customer satisfaction. Embrace the Lean journey and transform your organization into a Lean enterprise that thrives on continuous improvement and innovation.
Frequently Asked Questions
Why is it important to define a vision and goals for Lean Manufacturing?
Defining a vision and goals for Lean Manufacturing is crucial as it guides strategic decisions and aligns team efforts towards common objectives, enhancing unity and motivation among members. This clarity ultimately drives successful implementation and continuous improvement.
How can leadership and stakeholder engagement impact Lean implementation?
Leadership and stakeholder engagement significantly influence Lean implementation by fostering a supportive environment and ensuring commitment through effective communication. Their active involvement is essential for successful adoption and sustainability of Lean practices.
What is the significance of value stream mapping in Lean Manufacturing?
Value stream mapping is significant in Lean Manufacturing as it identifies waste and optimizes processes through a visual representation of workflows, facilitating the detection of inefficiencies. This tool ultimately enhances overall operational efficiency.
How do Kanban boards and WIP limits contribute to Lean implementation?
Kanban boards enhance Lean implementation by providing clear visualizations of workflows, while WIP limits effectively prevent bottlenecks and boost productivity through the management of concurrent tasks.
Why is customer feedback important in measuring the success of Lean initiatives?
Customer feedback is crucial in measuring the success of Lean initiatives as it offers valuable insights into the effectiveness of practices and identifies areas for improvement, ensuring the organization remains attuned to customer needs.
Share this
You May Also Like
These Related Stories
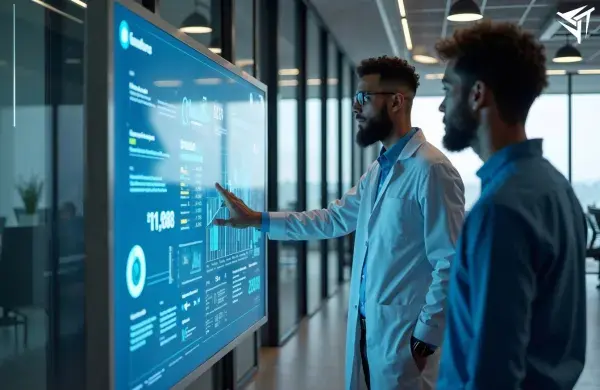
LIMS Implementation Project Plan: Strategies for a Flawless Rollout
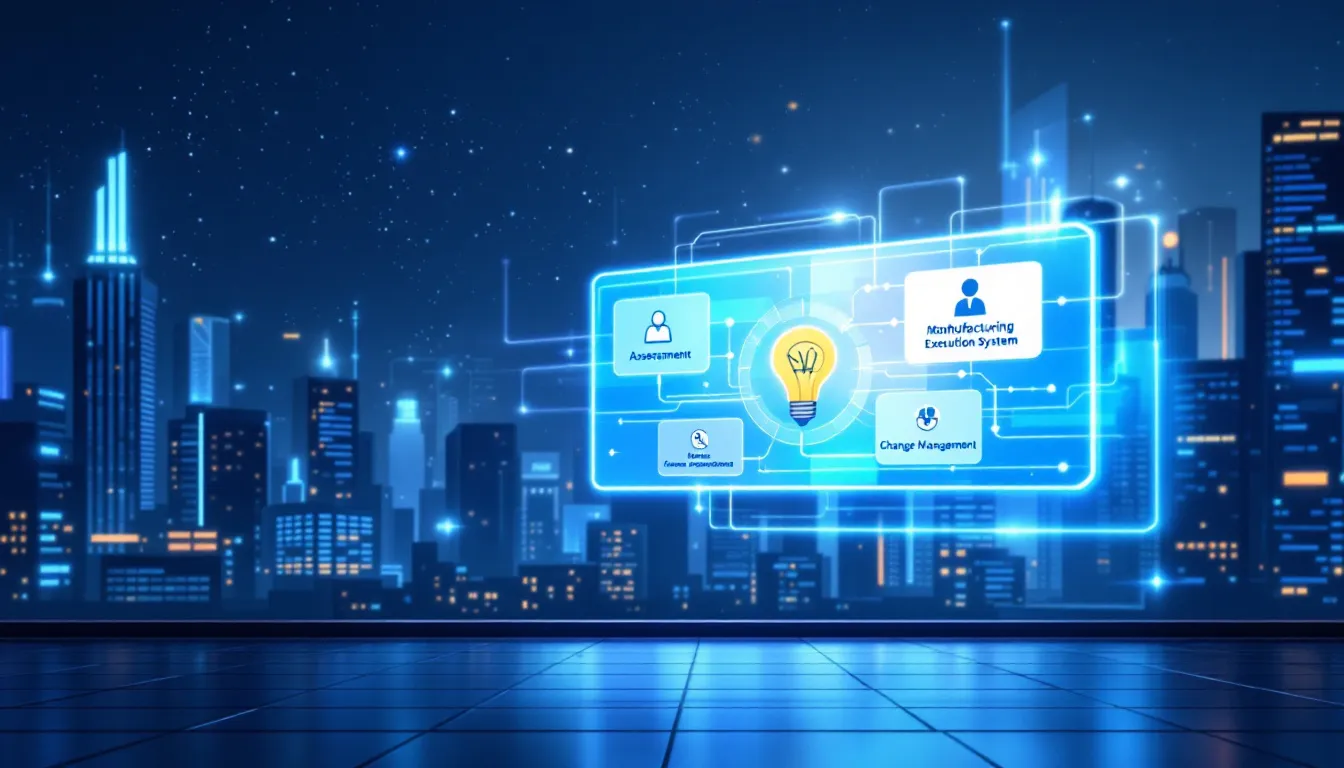
Mastering MES Implementation: Key Steps for Success and Efficiency
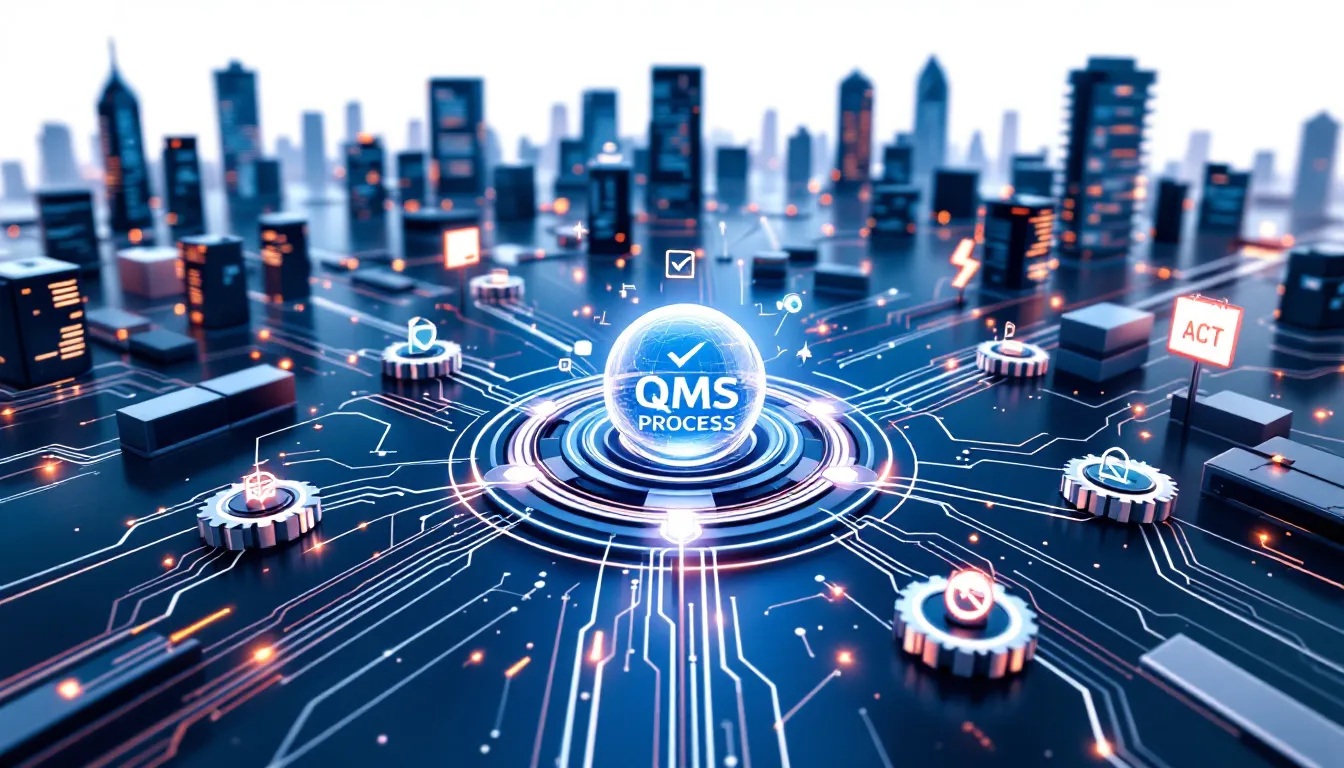
No Comments Yet
Let us know what you think