Boost Factory Productivity: 7 Proven Strategies for Success
Factory productivity is essential for manufacturing businesses aiming to increase output and cut costs.
This article will guide you through proven methods and key metrics to boost factory productivity and drive success.
Key Takeaways
-
Manufacturing productivity is evaluated by comparing output to input, with a focus on enhancing operational efficiency to reduce costs and improve competitiveness.
-
Key metrics such as labor productivity, multifactor productivity (MFP), and overall equipment effectiveness (OEE) are essential for measuring and identifying areas for improvement in factory productivity.
-
Strategies for boosting productivity include optimizing production processes through lean manufacturing, utilizing advanced software for real-time insights, and enhancing employee training and engagement to foster a more efficient workplace.
Understanding Factory Productivity
Manufacturing productivity refers to the rate at which goods are produced by a company, calculate manufacturing productivity by dividing outputs by the inputs used in the production process. High productivity in manufacturing leads to lower unit costs, benefiting consumers through reduced prices, which in turn improves competitiveness in global markets. It’s a win-win situation: businesses thrive, and customers enjoy better-priced products.
Several factors influence manufacturing productivity, including production processes, equipment, employee behavior, and efficient management. Inputs such as labor, materials, capital, and technology are crucial to understanding productivity levels. Examining total factor productivity, which considers output relative to all inputs used, provides businesses with insights into overall operational effectiveness.
Achieving high productivity levels is not just about increasing the number of units produced; it’s about improving operational efficiency. Manufacturing companies must continuously seek ways to boost manufacturing productivity, streamline their production processes, invest in the right technologies, and foster a culture of continuous improvement to improve operational efficiency and remain competitive in the manufacturing business while enhancing manufacturing efficiency.
Key Metrics to Measure Factory Productivity
Accurate measurement is crucial for measuring productivity and improving manufacturing productivity. Labor productivity, which measures real economic output per labor hour, is a fundamental metric. The formula for calculating labor productivity is simple: units of output divided by units of input. An increase in labor productivity is signified by increased output while labor hours remain the same.
Multifactor productivity (MFP) is another key metric that accounts for output in relation to multiple inputs such as labor, capital, and materials. The MFP index is calculated using a specific formula. The MFP index is expressed as (Output index / Combined input index) x 100. Businesses utilize this ratio to assess changes in productivity. It allows them to compare performance across different periods. MFP is often a better measurement than labor productivity alone because it accounts for changes in capital and materials used in production.
Overall equipment effectiveness (OEE) is another vital metric that helps manufacturers understand their equipment’s utilization rates. OEE combines measures of availability, performance, and quality to provide a comprehensive view of equipment utilization in the production process. Monitoring these metrics allows manufacturing companies to identify areas for improvement and implement strategies to boost productivity.
Strategies to Improve Factory Productivity
Improving manufacturing productivity requires a comprehensive approach that considers various factors such as processes, people, technologies, and costs. Optimizing production processes, implementing advanced manufacturing software, and enhancing employee training can lead to significant productivity gains for manufacturing companies.
Three key strategies to improve manufacturing productivity include optimizing production processes, implementing manufacturing software, and enhancing employee training and engagement. Each of these strategies addresses different aspects of the manufacturing process, providing a holistic approach to boosting productivity.
Optimize Production Processes
Lean manufacturing focuses on minimizing waste and costs while maximizing productivity and quality. Lean manufacturing prioritizes minimizing waste, reducing costs, maximizing productivity, and ensuring continuous improvement. Eliminating non-value-adding activities from workflows allows manufacturing companies to achieve significant cost savings and improve production efficiency.
Continuous improvement in manufacturing involves identifying and eliminating waste to enhance performance. Analyzing each production stage for value-added activities helps eliminate bottlenecks in manufacturing. Better organization of materials and parts enhances the picking process and reduces delays, thereby improving productivity.
The convergence of AI and IoT helps optimize production processes by predicting failures and suggesting corrective actions.
Implement Advanced Manufacturing Software
Advanced planning & scheduling software plays a crucial role in monitoring and enhancing overall productivity in factories. Modern technology solutions can measure performance and provide insights into improvement opportunities. Manufacturing software with IoT capabilities enhances prioritization and improves productivity. Edge computing in manufacturing enables real-time data analysis, quicker decision-making, and reduced network bandwidth usage.
Advanced manufacturing software allows companies to streamline processes and make data-driven decisions to boost efficiency. These technologies provide real-time insights into production performance, helping to identify bottlenecks and areas for improvement, ultimately leading to increased productivity.
Enhance Employee Training and Engagement
Effective staff training leads to improved manufacturing productivity. Upskilling employees enhances productivity and creates a better workplace environment. Supervised on-the-job training helps employees follow best practices closely and reduce errors. Proper training and a positive working environment are crucial for higher employee engagement in manufacturing.
Engaged employees are more productive and likely to produce higher quality work. Regular activities promoting togetherness among employees can significantly enhance engagement. A strong workplace culture boosts employee morale and engagement, ultimately driving employee productivity.
Involving employees in productivity initiatives and gathering feedback enhances engagement. Cross-training employees reduces downtime and ensures productivity remains unaffected during absences.
Reducing Downtime
Production downtime represents the total duration when production lines are not operational, which includes both scheduled and unscheduled downtime. Analyzing downtime data allows manufacturers to predict future equipment failures and reduce unexpected stoppages. Manufacturing downtime can be caused by machine breakdowns, wrong components being picked, or delayed components delivery.
A risk audit can identify outdated equipment that may increase downtime risks. IoT enables predictive maintenance by monitoring equipment health, which helps prevent unplanned downtime. A preventive maintenance plan helps catch potential issues before they lead to major equipment failures.
Reducing downtime improves operational efficiency and productivity for manufacturing companies.
Enhancing Supply Chain Efficiency
Effective supply chain management enhances production efficiency and reduces inventory costs. Strong supplier relationships lead to a more robust supply chain and preparedness for unforeseen challenges. Optimal inventory control ensures the right stock quantity to avoid excess and stock-outs. Cloud-based inventory software and demand planning can significantly improve stock levels.
IoT-enabled real-time tracking improves supply chain visibility, ensuring better inventory management and reducing losses. Effective supply chain cost control should target labor, inventory, transportation, and risk management. Reducing transportation costs minimizes excess fees and optimizes delivery processes, significantly improving supply chain efficiency.
Balancing Productivity and Quality
Balancing productivity with product quality is crucial in the quest to improve manufacturing productivity. Defect density tracks the ratio of defective products to the overall volume produced, providing insights into quality control. First Time Yield measures the rate of non-defective products produced without requiring rework, indicating manufacturing quality.
IoT sensors facilitate automated quality control by monitoring production processes, which helps detect deviations early. Solely focusing on productivity may lead to wasted materials and lower quality items. Maintaining a balance between productivity and quality ensures manufacturing companies produce high-quality goods efficiently.
Leveraging Technology for Increased Productivity
Automation enhances productivity and quality by performing repetitive tasks safely and efficiently. IoT integration in manufacturing provides real-time insights that help predict potential issues and streamline operations. A McKinsey study predicts that IoT could create up to $4 trillion in value for the global manufacturing sector by 2030.
Integrating emerging technologies like IoT and automation is crucial for enhancing productivity in manufacturing. Leveraging these technologies enables manufacturing companies to achieve significant productivity gains, streamline processes, and improve product quality.
Real-World Examples of Improved Factory Productivity
Real-world examples highlight how improved factory productivity impacts costs, profitability, and competitive advantage. For instance, a semiconductor manufacturer facing yield inconsistencies and prolonged production cycles optimized processes to enhance yield and reduce cycle times, improving competitiveness. A global manufacturing firm recognized outdated processes causing high operational costs and low customer satisfaction and initiated a process improvement initiative to boost efficiency.
These examples demonstrate how manufacturing companies can achieve significant productivity gains by implementing the discussed strategies. Focusing on optimizing production processes, leveraging advanced manufacturing software, and enhancing employee training allows companies to transform their operations and achieve greater profitability.
Summary
In summary, improving manufacturing productivity requires a comprehensive approach that addresses various aspects of the production process. Key strategies include optimizing production processes, implementing advanced manufacturing software, enhancing employee training, reducing downtime, and enhancing supply chain efficiency. Balancing productivity with quality is also crucial to ensure high-quality output.
By leveraging technology and focusing on continuous improvement, manufacturing companies can achieve significant productivity gains, reduce costs, and improve their competitive advantage. The journey to increased productivity is ongoing, but with the right strategies in place, manufacturers can achieve remarkable results and drive their business to new heights.
Frequently Asked Questions
How do you measure productivity in manufacturing?
Productivity in manufacturing is measured by comparing the rate of output to the amount of input used. Productivity increases occur when the same inputs yield more outputs or when the same outputs are achieved with fewer inputs.
What is productivity in a factory?
Productivity in a factory measures how effectively a manufacturing process produces items within a given timeframe, emphasizing the importance of minimizing waste in time, materials, and energy. This efficiency is crucial for maximizing output and overall performance.
Why is it important to measure factory productivity?
It is crucial to measure factory productivity as it enables businesses to pinpoint areas needing improvement and optimize production processes, leading to increased efficiency and profitability. Understanding these metrics can significantly enhance overall operational effectiveness.
How can implementing advanced manufacturing software improve productivity?
Implementing advanced manufacturing software significantly enhances productivity by providing real-time insights that help identify bottlenecks and areas for improvement. This targeted approach enables more efficient operations and optimized resource utilization.
What role does employee training play in improving manufacturing productivity?
Employee training is essential for enhancing manufacturing productivity, as it ensures that workers are more skilled and engaged, leading to improved quality of work and adherence to best practices. Thus, investing in training directly correlates with increased operational efficiency.
Share this
You May Also Like
These Related Stories
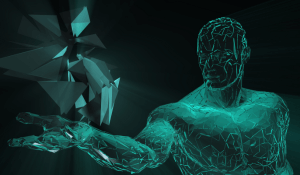
The Future of Sustainable Manufacturing: Best Practices and Strategies
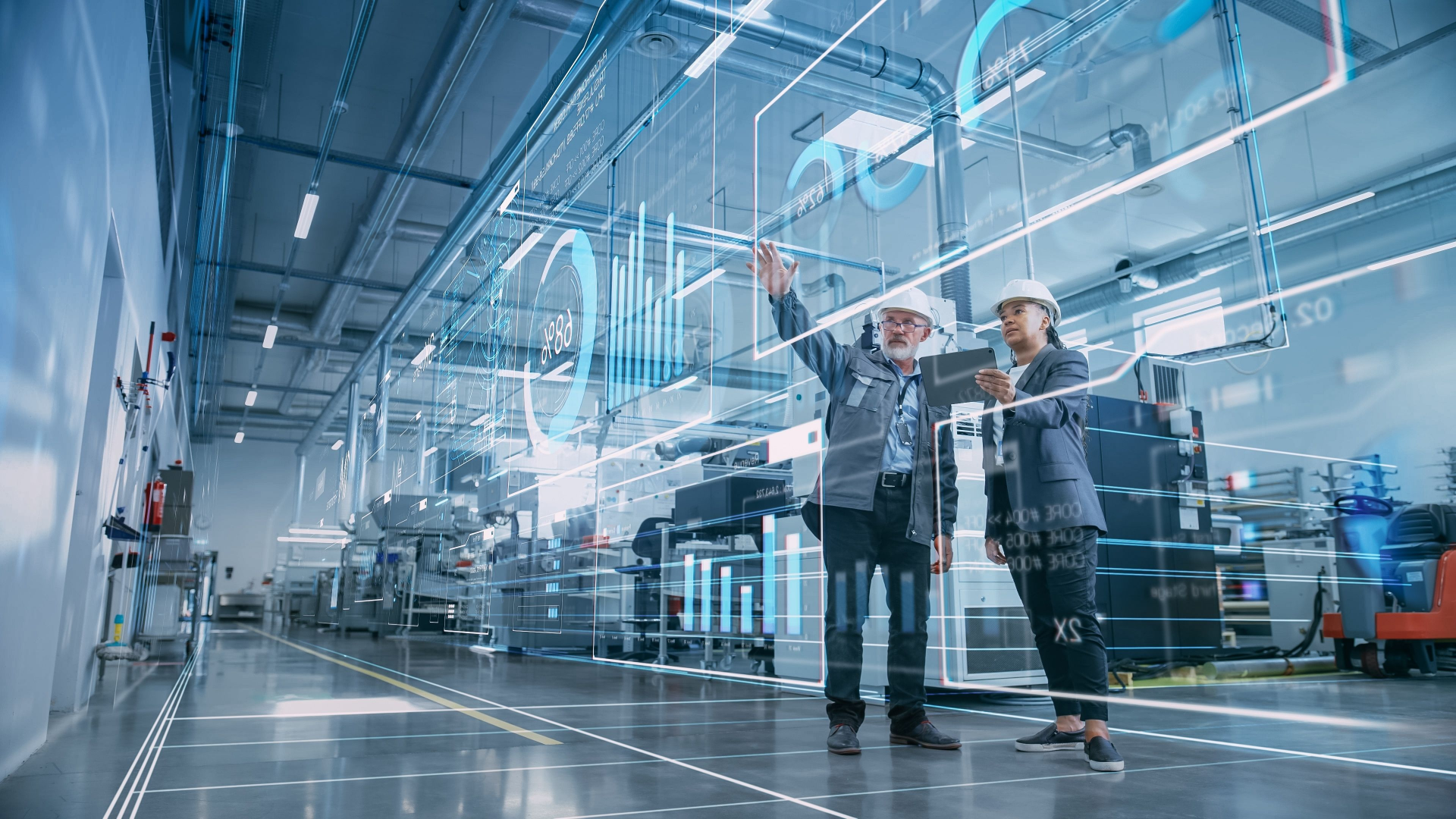
SMT Logistics: Break Silos Between Replenishment and Scheduling
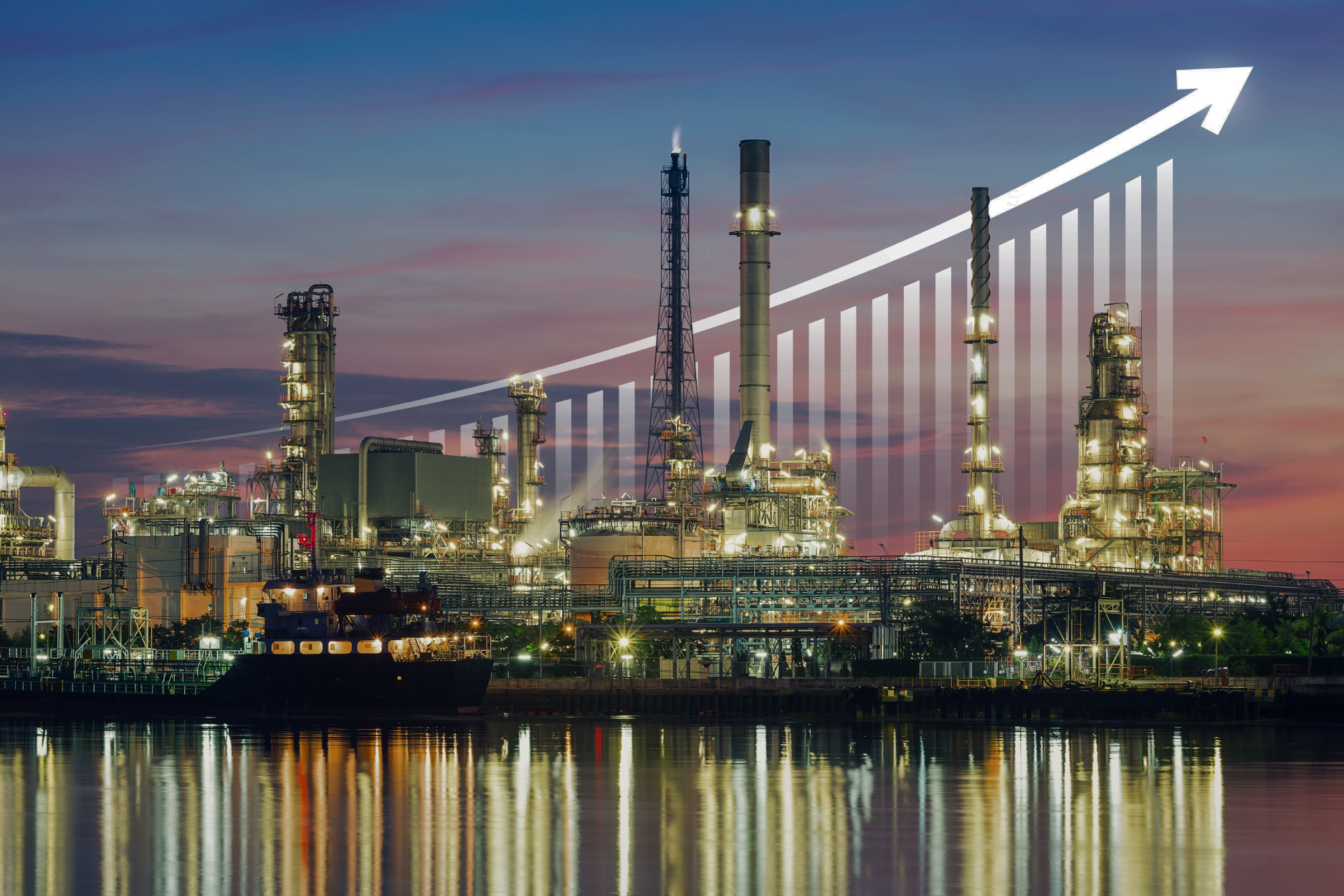
No Comments Yet
Let us know what you think