CAPA Management Software
Corrective and Preventive Action (CAPA) management is essential for organizations aiming to maintain quality, reduce risk, and ensure compliance.
In the era of smart manufacturing, where real-time data and digital systems drive decisions, CAPA software plays a critical role. It simplifies and automates quality processes, making improvements faster, more consistent, and easier to audit.
CAPA Management Challenges
Managing CAPA manually can quickly become overwhelming. Without automation, quality teams often struggle with disjointed documentation, delayed response times, and incomplete records. These inefficiencies can lead to missed compliance deadlines and recurring issues.
.png?width=600&height=400&name=CAPA%20Management%20Challenges%20(1).png)
What Does CAPA Management Software Do?
CAPA software digitizes and streamlines every step of the corrective and preventive action process. It ensures quality issues are documented, investigated, resolved, and tracked through an auditable system. This digital approach aligns perfectly with smart manufacturing goals—bringing agility, traceability, and insight to quality management
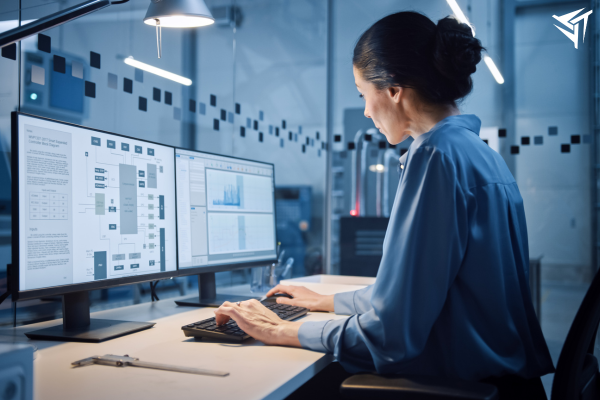
Key Features
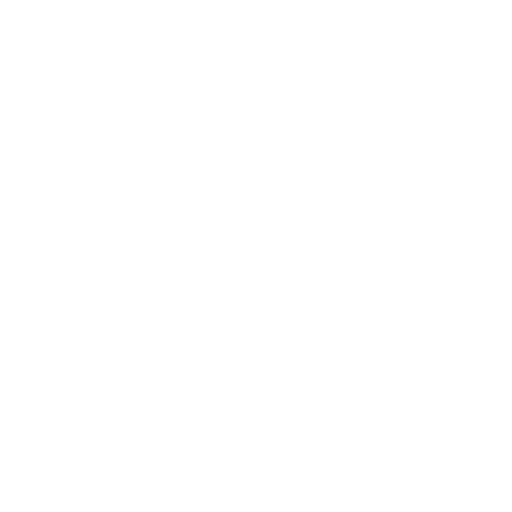
Automated CAPA Workflows
Streamlines task assignments, approvals, escalations, and due dates. Ensures accountability, accelerates resolution, and prevents bottlenecks through consistent, rules-based automation.
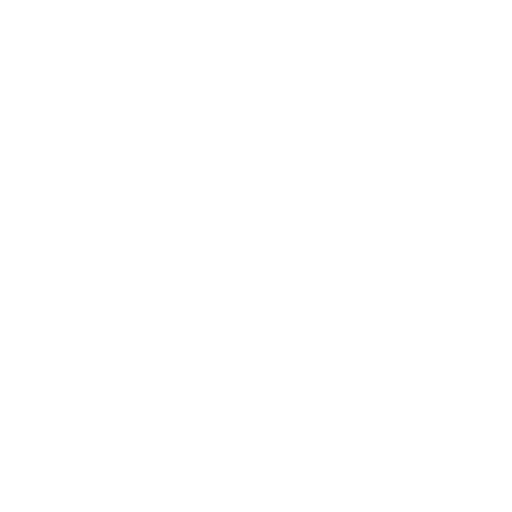
Root Cause Analysis & Investigation Tools
Provides structured tools like 5 Whys and Fishbone diagrams. Facilitates thorough investigations, helping teams accurately identify and eliminate the source of recurring problems.
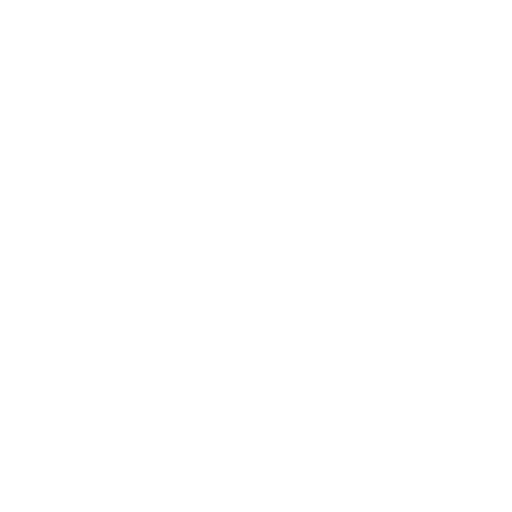
Integrated Compliance & Documentation
Creates traceable, time-stamped records with full audit trails. Supports FDA, ISO, and GMP standards, simplifying audit readiness and regulatory reporting across smart manufacturing environments.
Benefits
Faster Issue Resolution
Automates and tracks CAPA actions, reducing delays and speeding up closure on quality events.
Reduced Recurrence of Problems
Targets the root cause, preventing repeat issues and improving long-term product reliability.
Improved Audit Readiness
Maintains digital records and trails, making audits simpler and more efficient to navigate.
Regulatory Compliance
Supports documentation and workflows that meet ISO, FDA, and GMP requirements with ease.
Greater Team Accountability
Assigns ownership with due dates, notifications, and escalations—ensuring follow-through.
Supports Smart Manufacturing
Integrates with digital systems like QMS and MES to enable real-time quality oversight and control.
Siemens Opcenter Quality
Snic Solutions is recognized as one of the elite organizations partnered with Siemens as a value-added reseller of Opcenter.
/About%20Page/Blake%20Digital%20Transformation%20Solutions.png?width=500&height=500&name=Blake%20Digital%20Transformation%20Solutions.png)

CAPA Integration
CAPA management software becomes even more powerful when integrated with your broader digital ecosystem. By connecting with systems like QMS, ERP, MES, LIMS, and document control platforms, CAPA data flows freely across departments and functions.
What happens when you integrate?
When CAPA software is integrated, quality issues from systems like MES or LIMS automatically trigger immediate action. This real-time connection boosts visibility, speeds resolution, and strengthens audit readiness.
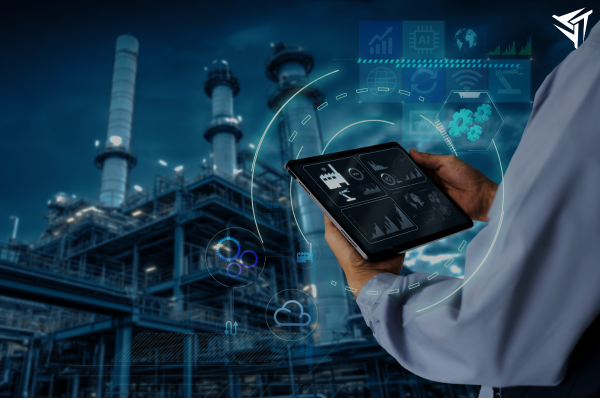
From Our Blog
Stay up to date with what is new in our industry, learn more about the upcoming products and events.
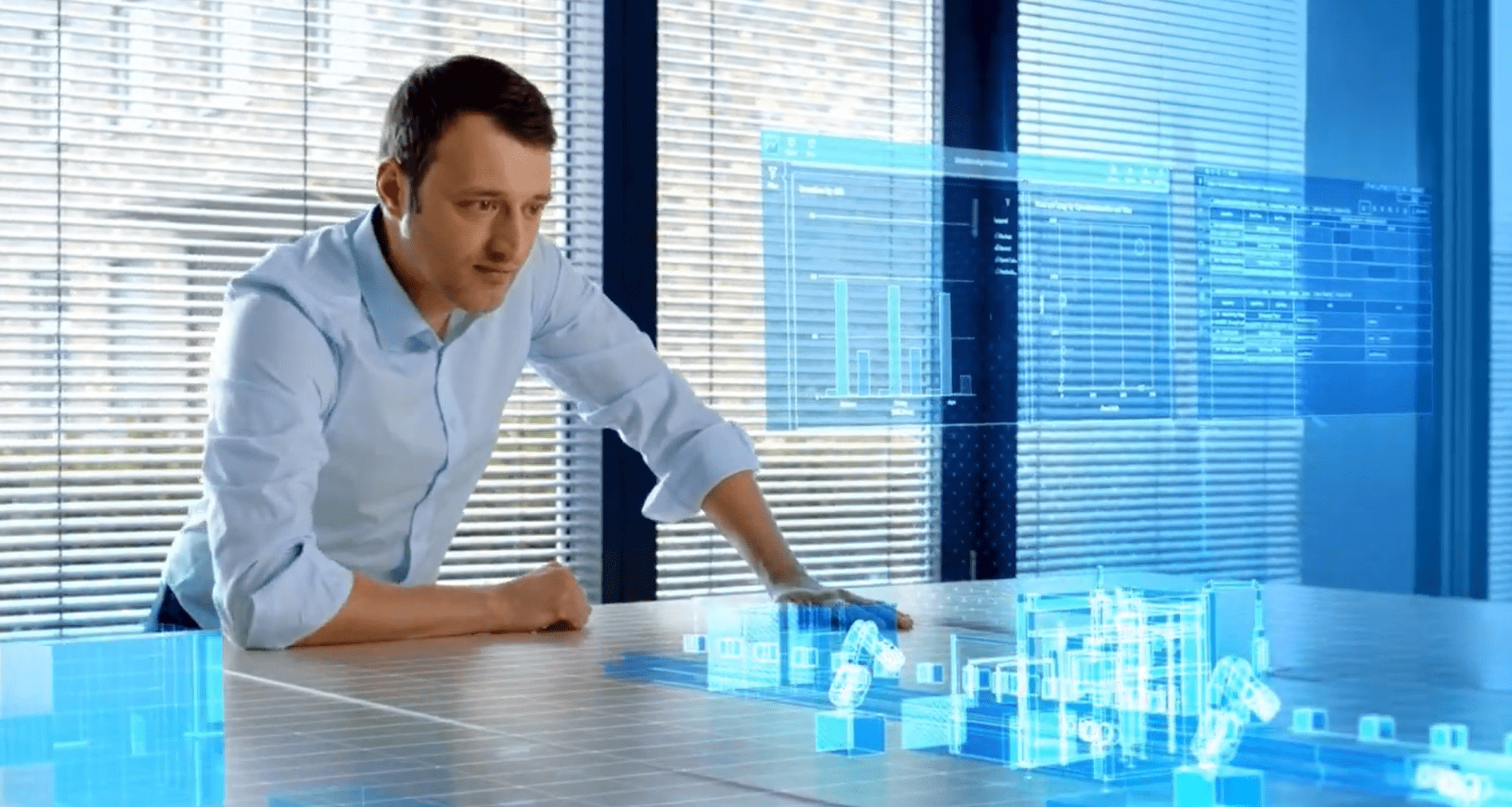
The Ultimate Guide to Benchmarking in Manufacturing
Benchmarking in manufacturing is the process of comparing your company’s operation…
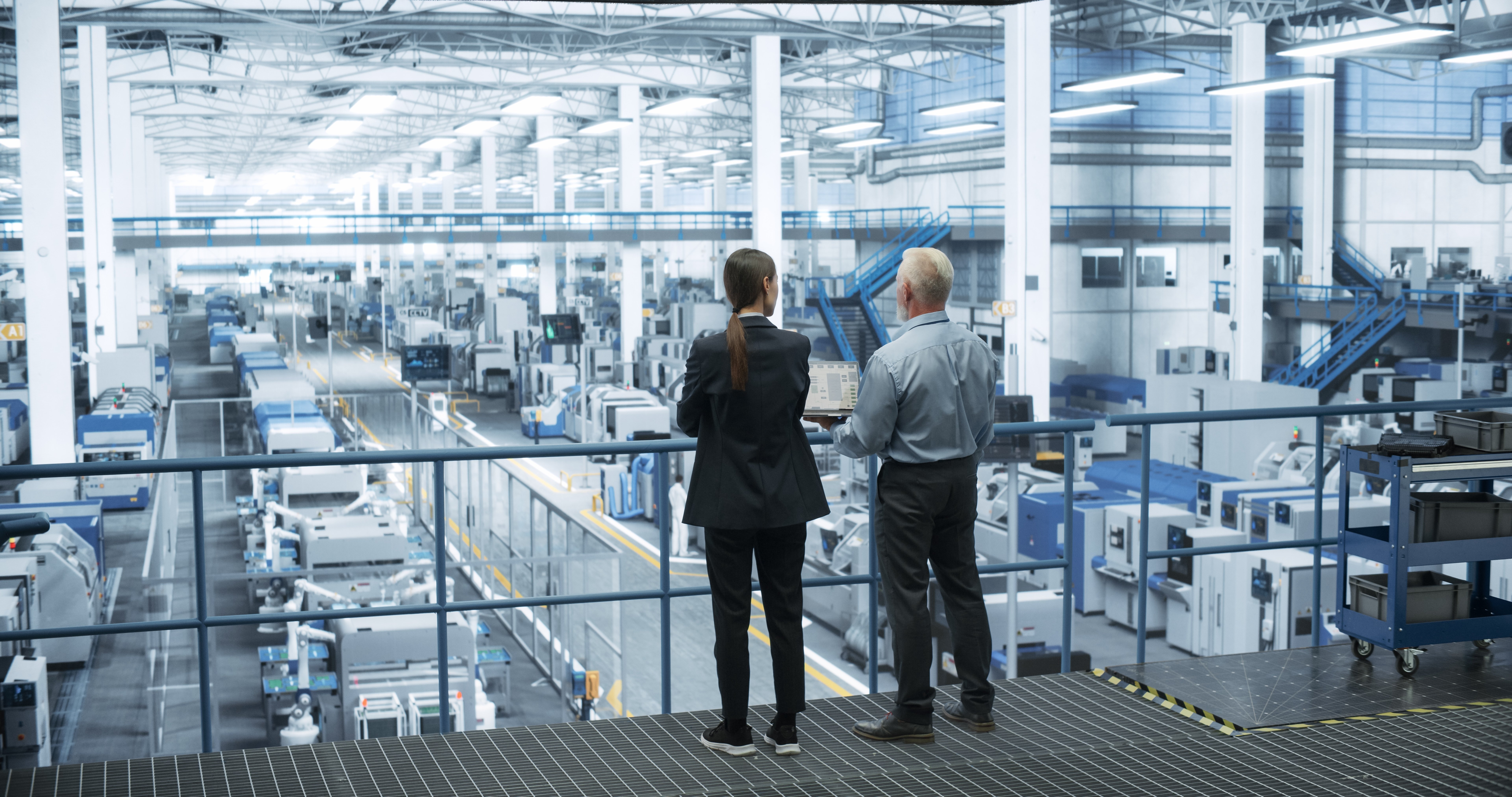
Top Strategies for Boosting Manufacturing Profit
Looking to boost your manufacturing profit?
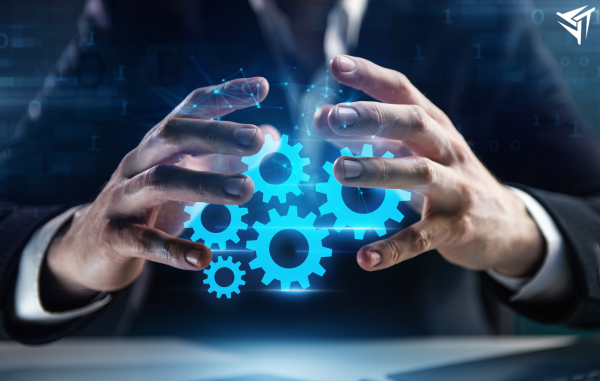
6 Forms of Automation: Benefits, Examples, and How to Choose
Automation comes in several forms of automation, each tailored to improve efficien…
Frequently Asked Questions
Have Question? We are here to help
What is CAPA management software?
CAPA management software is a digital solution designed to streamline the processes of identifying, documenting, and addressing quality issues within an organization. It automates workflows related to corrective and preventive actions, ensuring that problems are efficiently resolved and future occurrences are prevented. This software is often integrated into Quality Management Systems (QMS) to maintain compliance with industry standards and regulations.
What Is the CAPA Program?
A CAPA program is a structured approach within an organization to systematically investigate and rectify quality issues. It involves identifying non-conformities, determining their root causes, implementing corrective actions to address existing problems, and preventive actions to avert potential issues. Such programs are essential for continuous improvement and are often mandated by regulatory bodies like the FDA and standards such as ISO 13485.
Is CAPA Part of Six Sigma?
Yes, CAPA is integral to Six Sigma methodologies. Six Sigma focuses on process improvement and defect reduction, and CAPA provides the framework for identifying and eliminating the root causes of defects. Tools like the DMAIC (Define, Measure, Analyze, Improve, Control) cycle in Six Sigma align closely with the steps in the CAPA process.
What Is the CAPA Tool?
A CAPA tool refers to the specific software or system used to manage the CAPA process. It facilitates the documentation of issues, root cause analysis, action planning, implementation tracking, and effectiveness verification. These tools often include features like automated notifications, audit trails, and integration capabilities with other quality systems.
What Are the Four Stages of CAPA?
The CAPA process typically involves the following stages:
-
Identification: Recognizing and documenting the non-conformity or quality issue.
-
Evaluation: Assessing the significance and impact of the issue.
-
Investigation: Determining the root cause of the problem.
-
Action: Implementing corrective actions to address the immediate issue and preventive actions to eliminate the root cause and prevent recurrence.
What Is a CAPA Example?
An example of a CAPA could be a manufacturing company identifying a recurring defect in one of its products. The company would investigate to find the root cause—perhaps a malfunctioning machine—then take corrective action by repairing or replacing the machine. Preventive actions might include regular maintenance schedules and employee training to prevent future occurrences.
What Does CAPA Stand for in GMP?
In the context of Good Manufacturing Practice (GMP), CAPA stands for Corrective and Preventive Action. It's a critical component of GMP regulations, ensuring that manufacturers have systems in place to identify quality issues, investigate their causes, and implement measures to prevent recurrence, thereby maintaining product quality and safety.
Partner With Us To Reduce Your Technical Debt
Snic Solutions is recognized as one of the elite organizations partnered with Siemens as a value-added reseller of Opcenter.
/About%20Page/Blake%20Digital%20Transformation%20Solutions.png?width=500&height=500&name=Blake%20Digital%20Transformation%20Solutions.png)
