SMT Logistics: Break Silos Between Replenishment and Scheduling
Chances are that you generate good production schedules for SMT Lines and chances are that you also have a lean material replenishment system within your factory. The question is do they seamlessly work with each other?
This smart manufacturing use case for high-tech electronics manufacturing showcases an SMT Line factory implementation where two Opcenter software modules were configured and integrated to improve schedule adherence and overall Industrial efficiency. The importance of soldering the component leads to the pads on the circuit board during the reflow soldering process cannot be overstated. Proper soldering processes are crucial in ensuring the quality and reliability of SMT lines.
SMT Logistics' services extend to Canada, emphasizing their commitment to safe and compliant delivery across North America.
The outcome that Management can expect:
-
Improve collaboration between supply chain & manufacturing operations to gain overall speed and efficiency
Outcomes that supply chain & manufacturing operations teams can expect:
-
Improve production schedule accuracy
-
Easily spot production possibilities based on material availability
-
Easily spot material availability limitations
-
Gain time for material deliveries
-
Fully align work orders from the ERP system
The Importance of Integrated Logistics
Integrated logistics is crucial for businesses that rely on efficient transportation and shipping of goods. It involves the coordination of multiple logistics functions, such as transportation, warehousing, and inventory management, to ensure that goods are delivered to customers on time and in good condition. By integrating logistics, businesses can streamline their supply chain, reduce costs, and improve customer satisfaction.
In today’s fast-paced business environment, companies need to be able to respond quickly to changing market conditions and customer demands. Integrated logistics enables businesses to do just that, by providing real-time visibility into the supply chain and enabling them to make data-driven decisions. By leveraging technology and data analytics, businesses can optimize their logistics operations, reduce errors, and improve overall efficiency.
How is SMT Line Scheduling done using Opcenter SMT Scheduling to Save Time?
Data is combined from three sources to generate a production schedule for SMT Lines, including information on different packages of SMT components:
(1) machine, line configurations and resource availability from the shop floor,
(2) work orders, schedules and work hours from the enterprise resource planning (ERP) system and
(3) material availability and location from the supply chain.
The various package sizes used for different types of SMT components, such as passive components, transistors, diodes, and integrated circuits, impact scheduling by determining the level of interconnectivity required.
The combination of all three enables accurate short-term planning while creating a production plan that includes groups per line, static feeder settings, trolley usage, kanban/work-in-process (WIP) and resource allocation.
How does the Opcenter Scheduling Software Augment Planning and Execution Teams?
-
Facilitates intelligent SMT line grouping to optimize productivity by minimizing machine setup when manufacturing multiple products, including those with integrated circuits
-
Supports the scheduling and placement of surface mount devices on the production line, enhancing efficiency and throughput
-
Provides full SMT line coverage including SMT, test and manual
-
Uses what-if simulation to enable an immediate response to line-down scenarios
-
Delivers long-term planning, capacity forecasting and assistance in new equipment investments
-
Provides actual versus real-time performance analysis for a rapid response to bottlenecks
-
Provides realistic SMT production scheduling based on actual factory capacity
-
Helps in tracking and managing shipments, ensuring efficient and safe delivery of SMT components
What is Opcenter Scheduling SMT?
Opcenter™ Scheduling SMT software is a tool for the surface-mount technology (SMT) manufacturing industry that seamlessly connects the planner to the shop floor. Opcenter Scheduling SMT, which is part of the Siemens Xcelerator business platform of software, hardware and services, supports factory planners as they generate production schedules taking into consideration frequent, real-time changes that occur in the manufacturing stage, especially in high-mix, low-volume production or when introducing a new product.
Source: https://blogs.sw.siemens.com/opcenter/whats-new-in-opcenter-scheduling-smt-2310/
How is Material Replenishment done for SMT Lines using Opcenter Intra-Plant Logistics Software?
Surface-mounted technology (SMT) requires hundreds of SMT components in the electronics assembly process run in mass production. These components, varying in sizes and costs, include smaller components such as resistors and capacitors, which are increasingly in demand to meet the requirements of modern electronics manufacturing. These components have to be transferred from a warehouse to an area for preparation, commonly known as kitting. Oversight in kitting leads to long material replenishment lead time, component loss, and overstocking at the kitting area.
The ideal replenishment process is to replenish the component needed just-in-time (JIT). This can control the inventory at minimal safety stock and safety time. However, it is hard to immediately achieve JIT in real life. Practically, most material is planned to move in smaller batches between the warehouse and supermarkets close to the line and this control is usually in the hands of a material replenisher popularly known as water spiders in lean manufacturing circles and high-value component (HVC) operators in the electronics industry. The challenge in doing all this using manually or by paper is to synchronize all intra-plant logistics activity without having to build up too much inventory in the supermarket near the SMT line.
Siemens Opcenter Intra Plant Logistics (IPL) has a smart material replenishment handling solution to deliver the correct materials at the right time and location.
How does Opcenter IPL Augment Planning and Execution Teams?
-
Reduces inventory and costs while improving efficiency in the PCB assembly process
-
Utilizes automated pick and place machines to position components on the circuit board, reducing manual intervention
-
Improves cross-functional collaboration
-
Reduce total cost of ownership
-
Cut deployment time and cost
-
Facilitates the process of submitting forms and processing submissions, ensuring smooth logistics operations
What is Opcenter IPL?
Logistics management inside of the factory occurs in different places and levels, requiring different types of support to efficiently keep track of your inventory. The Opcenter™ Intra Plant Logistics (IPL) solution addresses this need, providing kanban, changeover, and just-in-time (JIT) principles to manage a consistent material flow to the production lines based on the schedule, actual demand, and consumption. It provides you with logistics capabilities including a flexible solution to address your production needs and significantly reduce inventory, maintain material specification, orchestrate your warehouse activities, and ensure a smooth manufacturing flow.
Source: https://blogs.sw.siemens.com/opcenter/whats-new-in-opcenter-intra-plant-logistics-2210/
Breaking Down Silos
One of the biggest challenges facing logistics companies is the existence of silos within their organizations. Silos refer to separate departments or teams that work independently of each other, often with little communication or coordination. This can lead to inefficiencies, errors, and delays in the logistics process.
To break down silos, logistics companies need to adopt a more collaborative and integrated approach to logistics management. This involves bringing together different teams and departments to work towards a common goal, and leveraging technology to facilitate communication and coordination. By breaking down silos, logistics companies can improve communication, reduce errors, and increase efficiency.
Overcoming Common Challenges
Logistics companies face a number of common challenges, including capacity constraints, driver shortages, and increasing regulatory requirements. To overcome these challenges, logistics companies need to be proactive and innovative in their approach to logistics management.
One way to overcome capacity constraints is to invest in technology, such as transportation management systems (TMS) and warehouse management systems (WMS). These systems can help logistics companies optimize their operations, reduce costs, and improve efficiency. Another way to overcome capacity constraints is to consider outsourcing logistics operations to a third-party logistics (3PL) provider.
Production Scheduling and Material Replenishment in Opcenter
Address material shortages before the production schedule is released to the shop floor
Integrating Opcenter IPL with Opcenter Scheduling SMT allows users to incorporate the latest material availability information into the production schedule, impacting the design and development of new electronic circuits. Ensuring the availability of each SMT component and managing and tracking shipments is crucial for continuous production. This allows users to:
-
See at one glance which orders can be produced
-
Easily spot upcoming material shortages
-
Maximize continuous production
-
Gain time for additional material deliveries
Integrating Opcenter Scheduling SMT with ERP saves the time and effort typically required to coordinate between ERP and your scheduling process. You can extract work orders, required delivery dates, release data, and material stock levels from ERP. You can also update the part reel quantities from SAP by selecting what to import and from where. Required quantity levels for each part in the work order can be displayed, along with inventory levels and the quantity remaining after the work orders are executed.
Case Studies and Success Stories
SMT Logistics has a number of case studies and success stories that demonstrate the importance of integrated logistics and the benefits of working with a logistics company that has expertise in transportation, warehousing, and inventory management.
One example is a food-grade transportation company that was struggling to manage its logistics operations. SMT Logistics worked with the company to implement a transportation management system (TMS) and warehouse management system (WMS), which helped to improve efficiency, reduce costs, and increase customer satisfaction.
Another example is a manufacturing company that was experiencing delays and errors in its logistics operations. SMT Logistics worked with the company to implement a just-in-time (JIT) logistics system, which helped to improve communication, reduce errors, and increase efficiency.
Implementation and Change Management
Implementing a new logistics system or process can be challenging, especially for companies that are used to doing things a certain way. To ensure a smooth transition, logistics companies need to have a clear plan for implementation and change management.
This involves communicating with stakeholders, including employees, customers, and suppliers, to ensure that everyone is aware of the changes and what to expect. It also involves providing training and support to employees, to ensure that they have the skills and knowledge needed to work with the new system or process.
By having a clear plan for implementation and change management, logistics companies can minimize disruptions, reduce errors, and ensure a smooth transition to the new system or process.
Other Software Implementation Guides
-
Mastering MES Implementation: Key Steps for Success and Efficiency
- LIMS Implementation Project Plan: Strategies for a Flawless Rollout
FAQs
What is surface mount technology (SMT) in electronics?
SMT, or Surface-Mount Technology, is a method used in electronics for mounting components directly onto the surface of printed circuit boards (PCBs). It allows for higher component density and more compact designs compared to traditional through-hole technology. SMT involves the use of various other components, including passive, active, and integrated components, which are designed specifically for surface mount applications. This variety of components in surface mount packages has led to a wide selection being available to meet the growing demand.
What is the difference between printed circuit board (PCB) and SMT?
PCB, or Printed Circuit Board, is the board that serves as the foundation for electronic components. SMT, or Surface-Mount Technology, is a technique used to place surface mount devices onto the PCB's surface. In essence, PCB is the physical board, while SMT is the method used to attach components to that board.
Is surface mount devices (SMD) the same as SMT?
SMD, or Surface-Mount Device, refers to the actual electronic components used in Surface-Mount Technology (SMT). SMT components are the electronic parts used in the SMT process, where they are soldered directly onto the board. While SMT is the process, SMDs are the components that are mounted using this process. So, they are related but not the same; SMDs are part of the SMT process.
Share this
You May Also Like
These Related Stories
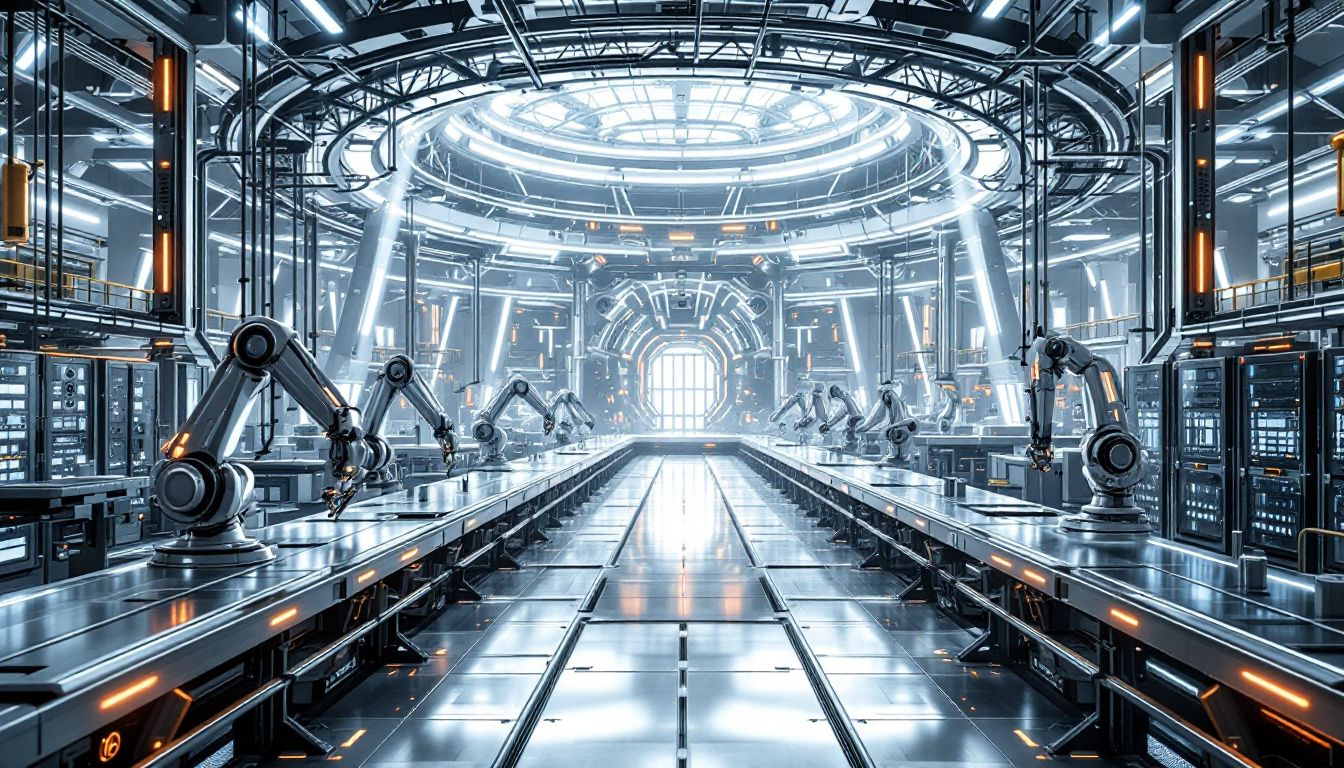
Boost Factory Productivity: 7 Proven Strategies for Success
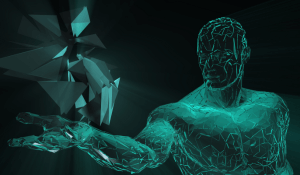
The Future of Sustainable Manufacturing: Best Practices and Strategies
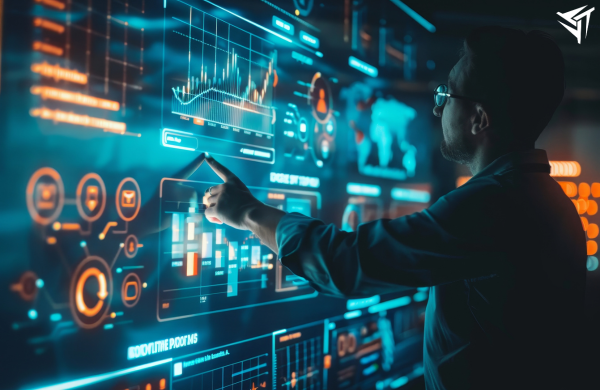
No Comments Yet
Let us know what you think