What is Smart Manufacturing and Why do you need it?
What Is Smart Manufacturing? - Smart manufacturing leverages cutting-edge digital technologies to optimize manufacturing processes across various industries. It integrates advanced systems such as the Internet of Things (IoT), Artificial Intelligence (AI), and big data analytics to create flexible, interconnected, and data-driven production environments.
Key Features of Smart Manufacturing
-
Real-time Data Collection: Continuous gathering of data from machines and processes using sensors and IoT devices.
-
Automation: Utilization of robotics and automated systems to efficiently perform repetitive and complex tasks.
-
Advanced Analytics: Application of AI and machine learning to analyze data, optimize operations, predict maintenance needs, and improve product quality.
-
Interconnectivity: Seamless communication across devices, systems, and personnel to ensure integrated and responsive manufacturing operations.
The Benefits of Smart Manufacturing
-
Increased Efficiency: Streamlining operations to reduce waste and enhance productivity.
-
Improved Quality: Monitoring and controlling production processes precisely to boost product quality.
-
Flexibility: Quick adaptation to changes in market demand and production requirements.
-
Predictive Maintenance: Minimizing downtime by proactively addressing potential failures before they occur.
Smart manufacturing is transformative, turning traditional factories into smart factories. This enables manufacturers to be more efficient, responsive, and competitive.
Goals of Smart Manufacturing
Smart manufacturing enhances decision-making by ensuring real-time data access. It aims to improve efficiency and reduce waste by streamlining processes.
This approach promotes innovation and better workflows through cross-departmental collaboration. It also utilizes predictive maintenance to minimize downtime and extend equipment life.
By adapting swiftly to market changes and efficiently meeting customer demands, smart manufacturing maintains a competitive edge and drives sustainable growth.
To read more about the history and aims of smart manufacturing, click here
What are the Fundamental Components of Smart Manufacturing?
Operations Technology (OT) Layer
Smart manufacturing integrates various levels of connectivity and a multitude of software programs, creating seamless links across all departments, including production, finance, and marketing. This infrastructure supports cutting-edge technologies on the factory floor, optimizing production processes and enhancing maintenance capabilities. Robots, cobots, and intelligent algorithms like machine learning and computer vision are pivotal, in enhancing efficiency and decision-making.
Data plays a crucial role here. Sensors, PLCs, and barcodes collect valuable information from the factory floor. Advanced software processes this data, presenting it on dashboards throughout the business to aid in real-time decision-making and strategic planning.
Information Technology (IT) Layer
The IT layer functions as the strategic hub, centralizing data analysis, and communication. It employs robust systems like ERP, PLM, and SCP to streamline operations and support executive decision-making. Presently, there's a significant shift toward cloud computing, enhancing data accessibility and security across various platforms.
This layer, acting as the System of Record (SOR), ensures that master data is synchronized and up-to-date, facilitating efficient operations and reliable reporting.
Why is Smart Manufacturing Important?
To gain a competitive edge, manufacturers must go beyond product-centric innovation. They must embrace innovative business models that allow them to create and capture value in novel ways.
Removing data silos and connecting the IT & OT Layer serves as the cornerstone for manufacturers before business model changes are initiated. Smart manufacturing represents a transformative shift in the manufacturing industry, driven by the integration of advanced technologies and digitalization.
Removing Data Silos
Historically, the separation between the Operational Technology (OT) layer of the shop floor and process control, as well as the Information Technology (IT) layer, has led to isolated pockets of information. This segregation hindered effective communication and collaboration across different segments of the business.
Smart manufacturing initiatives aim to dismantle these barriers by integrating digital "intelligence"—data communication and analysis—seamlessly across every level of the organization, from the shop floor to top-level administration.
This integration results in a dynamic data flow that enhances real-time communication across all departments, forging a unified network of information throughout the entire value chain. This cohesive flow establishes a single source of "truth" across the company, where no area operates in isolation, thus creating what is known as "digital threads."
MOM — The Essential Link to connect IT and OT
Many manufacturing operations still manage their IT and OT systems separately, which, while functional, restricts the scope for innovation. Manufacturing Operations Management (MOM) solutions are designed to overcome this challenge by serving as a critical link between IT and OT. Traditional Manufacturing Execution Systems (MES) have attempted this integration but often face limitations that restrict the transformation toward fully optimized smart manufacturing.
Modern MOM systems offer a more comprehensive solution. They not only bridge the IT-OT gap but also enhance the factory’s agility and responsiveness to market changes.
By seamlessly integrating IT and OT, MOM systems enable factories to be smarter, facilitating sustainable and substantial improvements in manufacturing operations. These systems pave the way for a new era of manufacturing where enhanced efficiency and innovation are at the forefront.
Predictive Maintenance and Advanced Technologies in Smart Manufacturing
Smart manufacturing employs a range of cutting-edge technologies to transform traditional manufacturing environments into highly efficient, adaptable smart factories. Here are the pivotal technologies defining this revolution:
-
Artificial Intelligence (AI) / Machine Learning (ML): Drives automated decision-making and efficiency.
-
Augmented Reality (AR) / Virtual Reality (VR): Enhances training and operational visualization.
-
Automation and Robotics: Streamlines production and reduces manual labor.
-
Additive and Hybrid Manufacturing (3D Printing): Facilitates rapid prototyping and on-demand production.
-
Big Data Analysis and Predictive Analytics: Optimizes processes through deep insights into operations.
-
Cloud Computing and Data Lakehouses: Offers scalable storage and powerful computational capabilities.
-
CNC Machining: Increases precision in production.
-
Cyber-Physical Systems and IoT/Edge Computing: Integrates physical operations with digital data.
-
Design for Manufacturing (DFM) and Digital Twins: Improves product design and simulation accuracy.
-
Industrial Internet of Things (IIoT) and Blockchain: Secures data transfer and enhances connectivity.
-
Anomaly Detection: Identifies potential faults or irregularities in real-time.
Among these, predictive maintenance stands out by utilizing AI and ML for real-time equipment monitoring and anomaly detection. This technology significantly enhances equipment reliability and operational efficiency by anticipating maintenance needs before failures occur.
Smart manufacturing technologies are continuously evolving. They enable factories to be as dynamic and responsive as the technology sector, with modular and flexible systems that can incorporate new functionalities seamlessly, much like how smartphones operate.
The Advantages of Smart Manufacturing
In this era of rapid changes, manufacturers are constantly facing new challenges. Smart manufacturing provides them with the capability to not only meet the demands of today but also adapt to the demands of the future. It introduces a new level of flexibility into their business structures and operations.
Smart manufacturing practices are foundational approaches that enhance cybersecurity, efficiency, and strategic integration in manufacturing. While the full value of smart manufacturing is realized after a transformation of the business model, it offers immediate benefits that our customers have experienced firsthand. Smart manufacturing solutions are innovative tools and systems that offer manufacturers a competitive edge through improved productivity, quality, and resilience.
Optimizing the Manufacturing Process: A Common Place to Start
Manufacturers often find optimizing operations has the greatest initial potential and appeal.
“Based on our research, the greatest potential for value creation in the factory setting will be optimizing operations in manufacturing — making the various day-to-day management of assets and people more efficient,” says a McKinsey report on the IoT value.
Some specific operational improvements smart manufacturing offers include the following:
-
Enhanced management and visibility of the shop floor in real time.
-
Improved control and oversight of the supply chain.
-
Accelerated and cost-effective product development.
-
Increased organizational resilience and more informed strategic decision-making.
-
Quicker response to customer needs, superior quality control, more precise delivery forecasts, and reduced time to market.
Reaching a Single Truth
To unlock the maximum short-term operational benefits and prepare for business-wide advantages, it's essential to bridge the OT/IT gap with a MOM system. These nifty decision support tools empower everyone to work with the same real-time data and the ultimate source of truth.
By fostering digital connectedness throughout the entire business, from operations to high-level management, a business can easily adapt to present and future changes, ensuring long-term competitiveness.
What Is the Difference Between Smart Manufacturing and Smart Factories?
Smart Manufacturing refers to the comprehensive use of digital technologies to enhance every aspect of the manufacturing process. It includes integrating IoT, AI, and big data analytics to improve design, production, logistics, and service.
A Smart Factory is a specific example within the broader concept of smart manufacturing. It applies these technologies on the factory floor to create a highly automated, interconnected production environment. The smart factory is where the principles of smart manufacturing are put into practice to optimize the manufacturing process in real-time.
What Is a Smart Factory?
A smart factory is a highly digitized and connected manufacturing facility that uses a network of machines, communication mechanisms, and computing power to collect and analyze data continuously. This setup enables real-time decision-making, predictive maintenance, and streamlined operations. Key features of a smart factory include:
-
Automation: Utilizes robotics and automated systems to perform repetitive and complex tasks.
-
Real-time Data Collection: Implements sensors and IoT devices to gather data throughout the production process.
-
Data Analysis: Employs advanced analytics to optimize production processes and improve product quality.
-
Interconnectivity: Ensures seamless communication between various systems and machines within the factory.
What Is an Example of a Smart Factory?
The Siemens Electronics Works Amberg (EWA) in Germany is a prime example of a smart factory. This facility showcases the future of manufacturing through its use of Siemens' Digital Enterprise solutions. Key highlights include:
-
High Production Volume: EWA handles 350 production changeovers daily, producing approximately 17 million Simatic components annually.
-
Advanced Technologies: The facility uses Industrial Edge computing, AI, and cloud solutions to manage and optimize production. For instance, AI algorithms predict the quality of soldered joints on PCBs, reducing the need for end-of-line testing.
-
Predictive Maintenance: Edge computing and AI help in predictive maintenance by analyzing data from production equipment to prevent unscheduled downtime.
-
Digital Twin: Digital twin technology simulates and optimizes production processes, ensuring components are produced within a target cycle time.
-
Integrated Systems: EWA's seamless integration of hardware, software, industrial communication, cybersecurity, and services makes it a leading example of a Digital Enterprise.
By leveraging these advanced technologies, the Siemens Electronics Works Amberg demonstrates how smart factories can achieve high efficiency, precision, and adaptability in modern manufacturing.
Source: Siemens. (n.d.). Electronics & the Digital Enterprise: Shaping the Future of Manufacturing. Retrieved from https://www.siemens.com/global/en/company/stories/industry/electronics-digitalenterprise-futuretechnologies.html
Moving Forward: Optimal Strategies for Modern Manufacturing
Initial Steps: How to Begin Your Smart Manufacturing Journey
Manufacturers in all industries are convinced that “smart” methods will give them the ability to keep up with rapid economic and industry changes.
The common question is - "Where do I start?"
Exploring the theory of constraints model to identify and automate the bottleneck is one way to do it. The theory of constraints model has worked well for manufacturers where demand is constant.
In cases, where demand uncertainties have increased, batch sizes have reduced and production complexity has increased, here are a few Industries specific examples providing the initial implementation outcomes that manufacturers can consider:
Automotive Manufacturing Implementation
While OEMs may have traceability to avoid recalls as their highest ranking benefit for Automotive Tier I & II there are even better starting points for smart manufacturing.
Currently, for automotive Tier I and II manufacturers, the highest-ranking benefits are monitoring production efficiency and quality, adding automation, and improving data analytics.
Medical Equipment & Pharmaceutical Manufacturing Implementation
Large Medical equipment manufacturers already have many enterprise systems due to FDA 21 CFR 11 Compliance but work in silos today. For Medical device manufacturers, while compliance remains mission-critical during execution, the highest-ranking initial benefits are capacity utilization and inventory turns.
According to Deloitte, MedTech manufacturers can benefit the most from focusing on five key areas in their supply chain:
-
Inventory Management
-
Logistics and Distribution
-
Device Maintenance
-
Product Development
-
Warehouse Operations
Implementation for Small and Medium-sized Manufacturing Businesses (SMB)
Even small and medium-sized manufacturing businesses can reap the benefits of smart methods. Introducing these innovative approaches can lead to a significant return on investment (ROI) for SMBs. While these businesses may face practical constraints such as limited internal resources and budgets, prioritization during adoption can lower the barriers to entry and kickstart their journey towards Industry 4.0. Let's take a look at a couple of examples of how manufacturers have embraced smart methods:
One well-respected bicycle manufacturer realized that their existing way of working was hindering their growth. However, after investing in digital tools, they were able to effectively manage twice the amount of work with the same team. Learn more about their success story.
Another manufacturer, specializing in timber products, implemented new Advanced Planning and Scheduling (APS) software. By integrating it with their existing Enterprise Resource Planning (ERP) system and shop floor data collection systems, they experienced a 10% increase in sales and improved profitability through enhanced visibility and resource utilization accuracy. Find out more about their journey.
Making the Implementation Process Manageable
Figuring out the first few steps and navigating them need not be overwhelming. You should consider consulting with outside experts, drawing up a long-term road map to avoid wasting early efforts — and starting small.
Curious about where to begin with your factory or shop floor? Why not start by taking advantage of our complimentary digital maturity assessment to gain valuable insights and guidance.
Short of time and need to act quickly? Book a meeting with our team.
Read More: LIMS Implementation Process
FAQs
Is Industry 4.0 the Same as Smart Manufacturing?
Industry 4.0 and smart manufacturing are closely related but not the same. Industry 4.0 refers to the broader concept of the fourth industrial revolution, which encompasses the integration of digital technologies like IoT, AI, and cloud computing into industrial sectors. Smart manufacturing is a component of Industry 4.0 that specifically focuses on using these technologies to enhance manufacturing processes through automation, real-time data monitoring, and optimized production efficiency.
What Is Intelligent Manufacturing?
Intelligent manufacturing involves the use of advanced information and manufacturing technologies to enable flexibility and dynamic response to changes in the market or production demands. This approach leverages technologies such as artificial intelligence (AI), machine learning, robotics, and big data analytics to improve the manufacturing ecosystem's efficiency, quality, and productivity. It aims to create highly customizable and self-optimizing manufacturing systems.
What Is Another Word for Smart Manufacturing?
Another term often used interchangeably with smart manufacturing is "advanced manufacturing." Both phrases emphasize the use of cutting-edge technologies and methodologies to increase the efficiency and intelligence of manufacturing processes. "Intelligent manufacturing" is also used synonymously, highlighting the integration of smart technologies to enhance decision-making and operational workflows.
What Is IIoT for Smart Manufacturing?
The Industrial Internet of Things (IIoT) for smart manufacturing refers to the network of interconnected sensors, instruments, and devices embedded in manufacturing equipment that communicate with each other and with management systems. IIoT enables the collection, analysis, and utilization of vast amounts of data in real-time to improve manufacturing operations. It supports predictive maintenance, enhances operational efficiency, and fosters innovative new business models in smart factories.
What Is Smart Manufacturing and How Will We Benefit from It?
Smart manufacturing integrates digital technologies like IoT and AI with industrial production, improving efficiency, reducing waste, and enhancing product quality through data-driven insights and automation.
What Is a Smart Manufacturing Plant IoT?
A smart manufacturing plant IoT (Industrial Internet of Things) leverages networked sensors and machines to monitor and optimize manufacturing processes. This setup facilitates real-time data analysis, enabling predictive maintenance, enhanced operational efficiency, and improved decision-making specific to production needs.
Share this
You May Also Like
These Related Stories
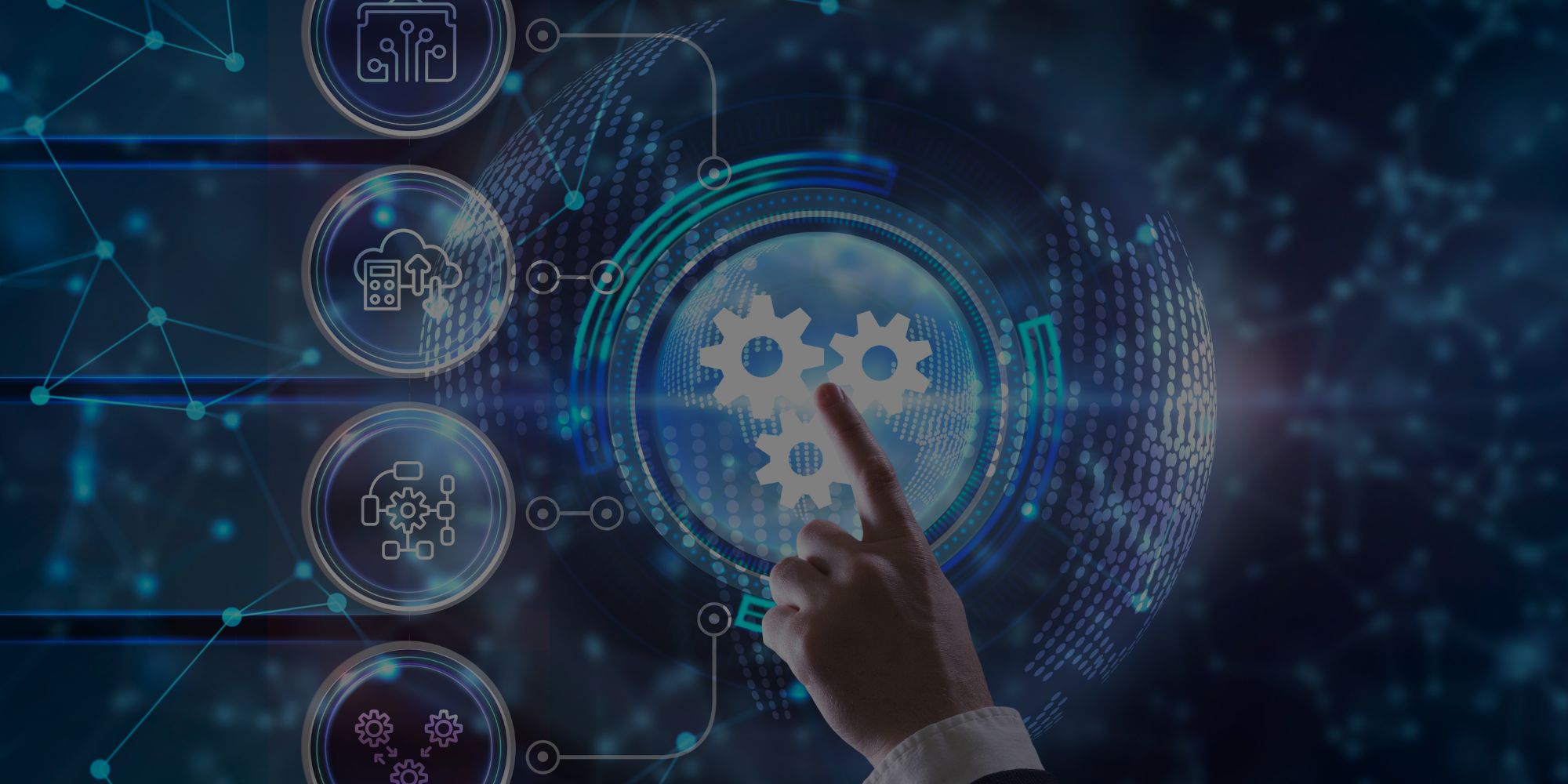
Manufacturing Operations Technology is Changing the Modern Factory
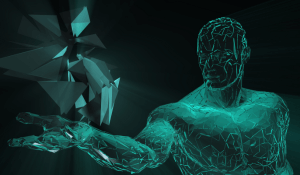
The Future of Sustainable Manufacturing: Best Practices and Strategies
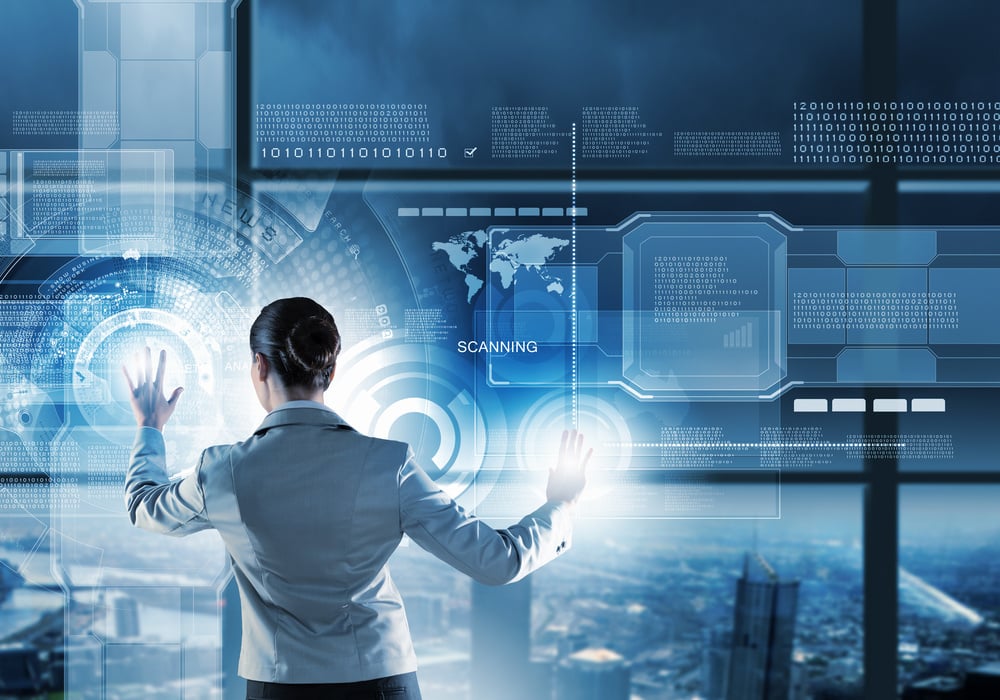
No Comments Yet
Let us know what you think