Agility Manufacturing: A Blueprint for Manufacturers in 2024
Agility Manufacturing
Manufacturers going into 2024 are facing more challenges than ever. Despite investing in data collection, many are struggling to use that data for fast and cost effective decision making. The gap between IT and business users and the talent shortage makes it even harder. According to a report from the National Association of Manufacturers (NAM) 53% of manufacturers feel their data utilization is inadequate and is hindering their operational efficiency and decision making.
To overcome these hurdles, leaders must be agile, data-driven, and adept at adapting to the rapid changes in the industry.
This article will show you how to transform your operations by using data, improving IT-business alignment and attracting the talent for innovation.
Embracing Agility in Manufacturing
In today’s rapidly changing market, embracing agility is no longer optional for manufacturers—it’s critical. Agility empowers companies to swiftly respond to customer and market demands, adapt to supply chain issues, and continuously innovate to stay ahead of the competition. By fostering an agile approach, manufacturers can enhance their ability to respond to unexpected events, such as material shortages or natural disasters, thereby reducing the risk of supply chain disruptions.
For instance, during the recent global supply chain crisis, companies that had embraced agility were able to pivot quickly, finding alternative suppliers and adjusting production schedules to meet customer needs. This ability to adapt not only mitigates risks but also positions manufacturers to seize new opportunities as they arise.
The Data Dilemma: From Overload to Actionable Insights
Manufacturers collect data from various components such as machines, sensors, and production systems. But many struggle to turn that data into business insights. A World Economic Forum report says only 29% of manufacturers globally are effectively using data analytics to drive decision making in their operations.
Focus on High-Value Data
Rather than trying to make sense of all data, focus on the streams that impact your business most. According to the CESMII (Clean Energy Smart Manufacturing Innovation Institute) companies that focus on key actionable data have seen 20-25% increase in operational efficiency and 15% reduction in downtime through targeted data insights.
Start by asking:
-
What metrics impact operations and the bottom line?
-
Which data streams can prevent downtime?
-
What helps us respond faster to customer demand?
For example, As reported by US Chamber of Commerce, Lockheed Martin implemented a data driven strategy in one of their advanced manufacturing plants and saw 15% productivity gain through real-time monitoring of key data points.
Automate Low-Level Decisions
Low level decisions – machine maintenance scheduling or inventory reordering – can be automated. CESMII found that manufacturers who automated routine tasks saw 30% faster decision making and 50% reduction in manual errors. This reduces the cost of decision making and allows leadership to focus on strategic decisions that drive growth and competitiveness.
Building a Strong Foundation for Business Agility
Building a strong foundation for business agility starts with a commitment to digital transformation, continuous improvement, and supply chain optimization. Investing in digital technologies like enterprise resource planning (ERP) and advanced scheduling systems enhances a company’s ability to respond to changing market conditions swiftly and efficiently.
Continuous improvement is another cornerstone of agility. By fostering a culture of innovation and experimentation, manufacturers can encourage their teams to develop new solutions and processes that drive efficiency and adaptability. Additionally, optimizing supply chains to be more resilient and flexible helps reduce the risk of disruptions and improves the ability to adapt to market changes.
For example, companies that have integrated digital transformation into their operations often see significant improvements in their ability to manage supply chains, leading to reduced lead times and increased customer satisfaction.
IT-Business Alignment
Manufacturers often have a gap between IT and business functions. IT looks after infrastructure and business users want faster solutions without having to do technical work. This slows innovation and decision making.
Cross-Functional Data Teams
One way to do this is to create cross functional teams that combine IT expertise with business knowledge. According to US Chamber of Commerce, manufacturers with integrated IT-business teams have seen 35% faster decision making and 20% more real-time data usage ().
As per a NAM report, General Motors (GM) did this and created cross functional teams that aligned IT and business strategies. Result was 20% reduction in operational costs and a more streamlined decision making process.
No-Code and Low-Code Platforms
To reduce dependence on IT, manufacturers can use no-code or low-code platforms. US Small Business Administration (SBA) data shows small and medium sized manufacturers using low-code platforms have 25% faster problem solving and 40% more agility in responding to operational challenges. Business users can build tools and dashboards quickly without waiting for IT support.
Managing the Supply Chain for Agility
Managing the supply chain for agility involves a strategic focus on flexibility, adaptability, and collaboration. Manufacturers must cultivate strong relationships with their suppliers, enhancing communication and cooperation to build a more resilient supply chain. Implementing digital technologies, such as supply chain management software, allows manufacturers to track and manage their supply chains in real-time, providing the visibility needed to respond quickly to changes.
Risk management is also crucial. By identifying potential supply chain risks and developing contingency plans, manufacturers can mitigate the impact of disruptions. For example, having alternative suppliers and flexible logistics solutions in place can help maintain operations during unexpected events.
The Talent Challenge: Attracting Tomorrow’s Workforce
Manufacturing faces a talent shortage. Younger workers are attracted to industries perceived as more innovative, leaving manufacturing behind in the talent race. According to the National Association of Manufacturers, 77% of manufacturers can’t find the workforce they need to keep up with new technology demands.
Rebrand Manufacturing as a High-Tech Industry
Today manufacturing is not just about the factory floor – it’s about robotics, artificial intelligence, digital twins and real-time analytics. Companies must highlight the high-tech aspects of modern manufacturing to attract young talent. According to US Chamber of Commerce, Ford rebranded its manufacturing as a tech driven innovation hub and saw 30% more applications for its engineering and digital manufacturing roles.
Upskill and Retain Current Employees
Upskilling the existing workforce is just as important. According to CESMII, manufacturers who invested in training and upskilling programs saw 25% reduction in turnover and 15% improvement in production quality. Training in data analytics, automation and digital tools can help manufacturers build a more capable and agile workforce.
Creating a Culture of Agility
Creating a culture of agility within an organization requires a focus on innovation, experimentation, and continuous improvement. Manufacturers must empower their employees to think creatively and develop new solutions, fostering an environment where innovation thrives. Encouraging experimentation and learning from both successes and failures helps build a more adaptable and resilient organization.
Prioritizing employee development is also key. Providing training and resources to help employees develop the skills needed for an agile environment ensures that the workforce is capable of meeting the challenges of a rapidly changing market. This focus on continuous improvement not only enhances operational efficiency but also drives long-term growth and competitiveness.
Reducing the Cost of Decision Making
Leaders are worried about the cost of decision making – time and resources. With so much data out there, it can be hard to make fast decisions. World Economic Forum says companies using real-time data systems have reduced decision making time by 40%.
Real-Time Data Analytics
Real-time analytics gives decision makers up to date information on production lines, supply chains and customer interactions. CESMII found manufacturers using real-time analytics saw 25% reduction in downtime and 20% improvement in operational efficiency. This allows companies to respond quickly to disruptions, minimize losses and improve overall agility.
Standardize Data Governance
Standardizing data governance ensures data is consistent, reliable and clean across the organization. A NAM report says strong data governance frameworks reduce time spent on data validation by 35%, improving decision making accuracy and speed. By building trust in data, manufacturers can act more and make faster decisions.
Measuring Success and Driving Improvement
In an agile manufacturing environment, measuring success and driving improvement hinges on tracking key performance indicators (KPIs) and committing to continuous improvement. Manufacturers should monitor KPIs such as lead time, inventory levels, and customer satisfaction to gauge their performance and identify areas for enhancement.
Continuous improvement involves regularly reviewing processes and seeking opportunities for optimization. By prioritizing customer feedback, manufacturers can gain valuable insights that drive innovation and improvement. For example, using customer satisfaction data to refine production processes can lead to higher quality products and better customer experiences.
By focusing on these areas, manufacturers can build a more agile, responsive, and competitive organization, ready to meet the challenges of 2024 and beyond.
Conclusion: Turning Challenges into Opportunities
The challenges facing manufacturing leaders in 2024 are big but manageable. By focusing on the right data, improving IT-business alignment and rebranding manufacturing as a tech driven industry, leaders can turn today’s problems into tomorrow’s competitive advantages.
The key is agility. Manufacturers who use data for real-time decision making and adapt to market changes will win. By addressing data overload, IT-business friction and the talent gap, manufacturers can seize new opportunities and drive long term growth.
--
Want to get more agile and data driven? Read our blog on data virtuazliation
Share this
You May Also Like
These Related Stories
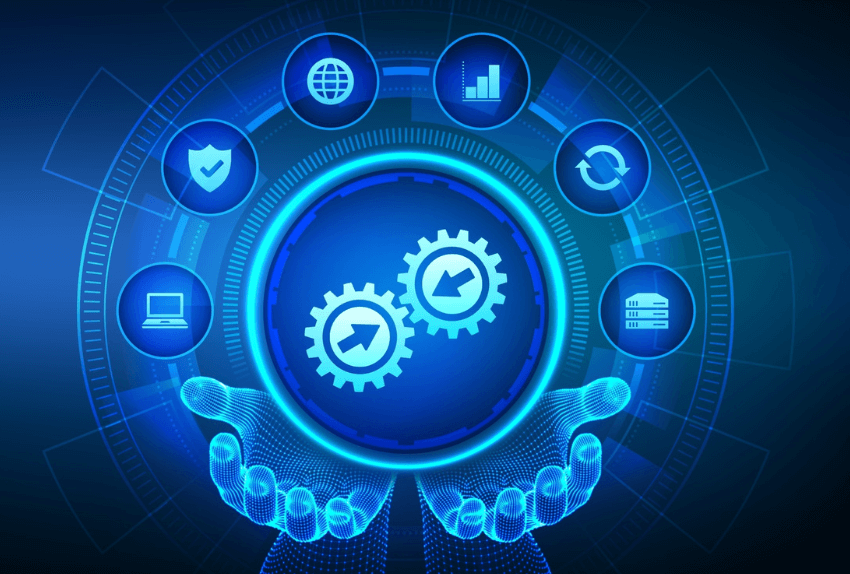
Traditional Manufacturing vs Smart Manufacturing: The Future Explained
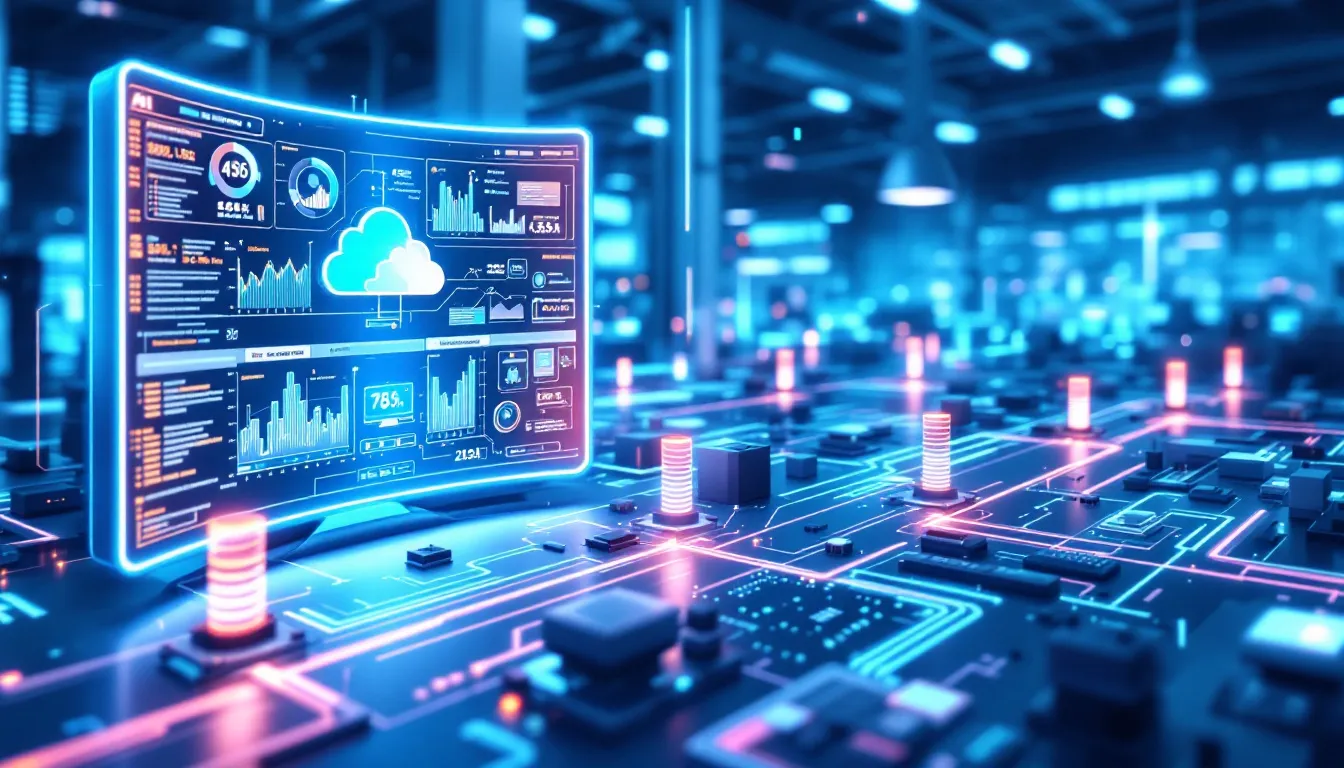
Cloud Computing in Manufacturing
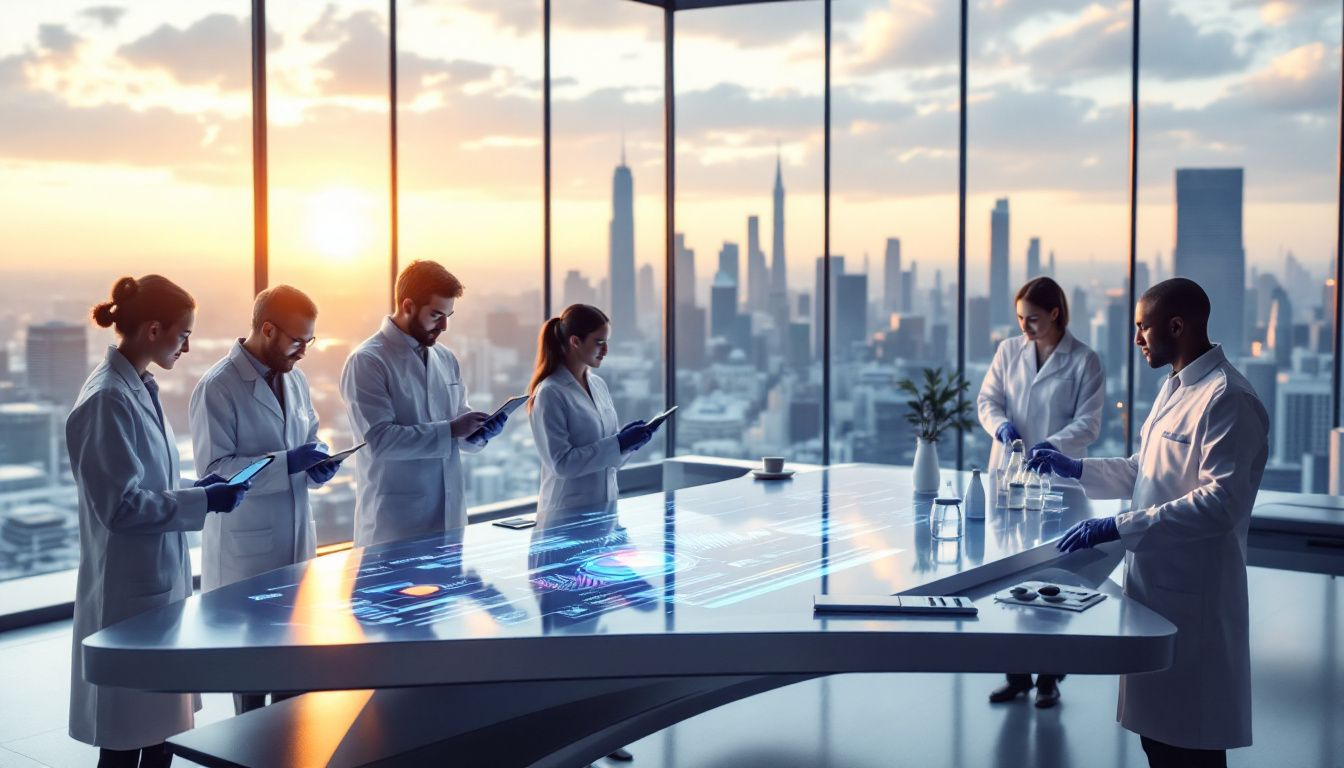
No Comments Yet
Let us know what you think