Traditional Manufacturing vs Smart Manufacturing: The Future Explained
Discover the key differences between smart and traditional manufacturing and how businesses can revolutionize their operations for success in a changing market landscape.
Evolving Customer Expectations in Manufacturing
As the manufacturing landscape and customer behavior continues to evolve, manufacturers must adapt to meet the changing expectations of their target market. In traditional manufacturing, the focus was primarily on mass production and cost-efficiency. However, with the rise of smart manufacturing, customers now expect greater customization, faster delivery times, and higher product quality.
To stay competitive and meet these evolving customer expectations, businesses need to adopt smart manufacturing principles. By leveraging advanced technologies and data-driven insights, manufacturers can transform their operations and deliver products that align with the unique preferences and demands of their customers.
Overview of Traditional Manufacturing Processes
Traditional manufacturing processes have been fundamental to industrial success, focusing primarily on efficiency and scalability. This approach has shaped the landscape of production for decades, where the emphasis has been on high-volume output and cost minimization.
Traditional methods typically involve assembly lines where human workers and mechanized systems perform repetitive tasks to produce large quantities of identical items. These processes are designed to maximize productivity and reduce operational costs, often at the expense of flexibility and customization.
As markets evolve and consumer demands shift towards more personalized products, the limitations of traditional manufacturing systems have become more apparent, prompting a shift towards more advanced, adaptable methods.
Key Principles of Traditional Manufacturing
Traditional manufacturing principles revolve around achieving efficiency and cost-effectiveness in mass production. Some key principles include:
Standardization: Traditional manufacturing relies on standardized processes and components to ensure consistent output.
Specialization: Workers are often specialized in specific tasks to improve productivity and reduce errors in human labor.
Lean Manufacturing: Lean principles, such as just-in-time production and waste reduction, aim to streamline business operations and minimize costs.
While these principles have served manufacturers well in the past, they may not be sufficient to meet the demands of today's dynamic market.
Introduction to Smart Manufacturing
Smart manufacturing represents a new era in the manufacturing industry, driven by advancements in technology and automation. It involves the integration of various digital technologies, such as artificial intelligence, internet of things (IoT), and cloud computing, to create a connected and intelligent production ecosystem.
The key objective of smart manufacturing is to optimize the entire value chain, from product design to delivery, by harnessing real-time data and insights. It enables manufacturers to make data-driven decisions, automate processes, and achieve greater operational efficiency.
By embracing digital technology and smart manufacturing, businesses can gain a competitive edge in today's fast-paced market and meet the ever-changing expectations of customers.
Benefits of Implementing Smart Manufacturing Principles
Implementing smart manufacturing systems and principles offers numerous benefits for businesses, including:
Enhanced Agility: Smart manufacturing enables companies to quickly adapt to market changes and customer demands, allowing for faster product innovation and customization.
Improved Efficiency: By leveraging data analytics and automation, manufacturers can optimize their production processes, reduce waste, and enhance overall operational efficiency.
Increased Product Quality: Smart manufacturing process that allows for real-time monitoring and quality control, leading to higher product quality and customer satisfaction.
Cost Savings: Through predictive maintenance and optimized resource allocation, businesses can minimize downtime, reduce energy consumption, and lower production costs.
By harnessing the power of smart manufacturing, companies can achieve sustainable growth and long-term success. To learn more about smart manufacturing principles, visit https://www.cesmii.org/about/what-is-smart-manufacturing/
Role of Cyber-Physical Systems in Smart Manufacturing Adoption
Cyber-physical systems play a crucial role in the adoption of smart manufacturing principles. These systems integrate physical processes with digital technologies, creating a connected environment where machines, sensors, and software work together seamlessly. By using manufacturing data and leveraging cyber-physical systems, manufacturers can achieve real-time monitoring, predictive maintenance, and autonomous decision-making, leading to enhanced operational efficiency and productivity.
In smart manufacturing, cyber-physical systems enable the collection of vast amounts of data from various sources along the production line. This data is then analyzed using advanced analytics and machine learning algorithms to uncover valuable insights that drive strategic decision-making. By utilizing cyber-physical systems in smart factories, businesses can optimize their processes, reduce downtime, and improve overall performance.
Furthermore, cyber-physical systems facilitate the implementation of digital twins, virtual representations of physical assets and processes. These digital twins allow manufacturers to simulate and optimize production scenarios, identify potential issues before they occur, and test new strategies in a risk-free environment. By embracing cyber-physical systems and digital twins, businesses can innovate and adapt quickly to meet the evolving demands of the market, ultimately leading to sustainable growth and success.
Relation Between Cyber-Physical Systems and Manufacturing Operations Management
Cyber-physical systems play a pivotal role in revolutionizing manufacturing operations management (MOM) by bridging the gap between physical processes and digital technologies. By integrating cyber-physical systems into MOM, businesses can achieve seamless connectivity and automation across their production lines. These systems enable real-time data collection, analysis, and decision-making, empowering manufacturers to optimize their operations for maximum efficiency and productivity.
With the integration of cyber-physical systems into MOM, businesses can monitor and control their manufacturing processes with unprecedented visibility and precision. This level of connectivity allows for predictive maintenance, proactive decision-making, automated processes, and streamlined workflows. By leveraging the power of cyber-physical systems in MOM, manufacturers can not only improve operational performance but also drive continuous innovation and adaptation to meet the evolving demands of the market.
In essence, the relationship between cyber-physical systems and manufacturing operations management is symbiotic, with the former providing the technological foundation and connectivity needed for the latter to thrive in the era of smart manufacturing and industry 4.0. Through this integration, businesses can unlock new possibilities for efficiency, agility, and competitiveness in an ever-changing market landscape.
FAQs
How does smart manufacturing differ from traditional manufacturing?
Smart manufacturing uses advanced technologies like IoT, AI, and automation to enhance efficiency, flexibility, and decision-making, while traditional manufacturing relies on manual processes and less integrated systems.
What is the difference between traditional manufacturing and digital manufacturing?
Traditional manufacturing relies on physical tools and manual processes, whereas digital manufacturing integrates digital tools, simulations, and data-driven technologies to optimize production workflows.
What is the difference between traditional manufacturing and advanced manufacturing?
Advanced manufacturing employs cutting-edge technologies such as robotics, 3D printing, and nanotechnology, while traditional manufacturing uses conventional methods and tools without these innovations.
What is the difference between smart manufacturing and advanced manufacturing?
Smart manufacturing focuses on real-time data, connectivity, and automation for adaptive processes, while advanced manufacturing emphasizes innovative technologies and materials for enhanced production capabilities.
Share this
You May Also Like
These Related Stories
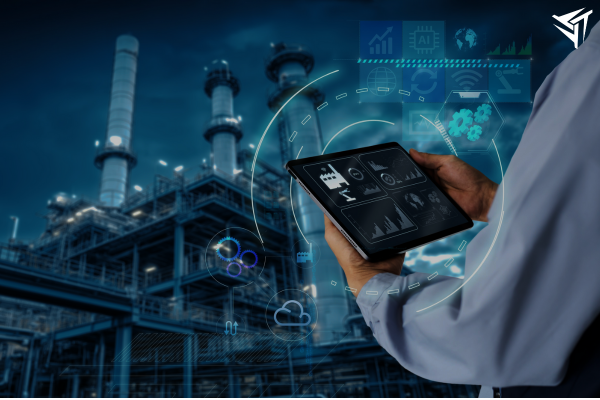
What is Smart Manufacturing?
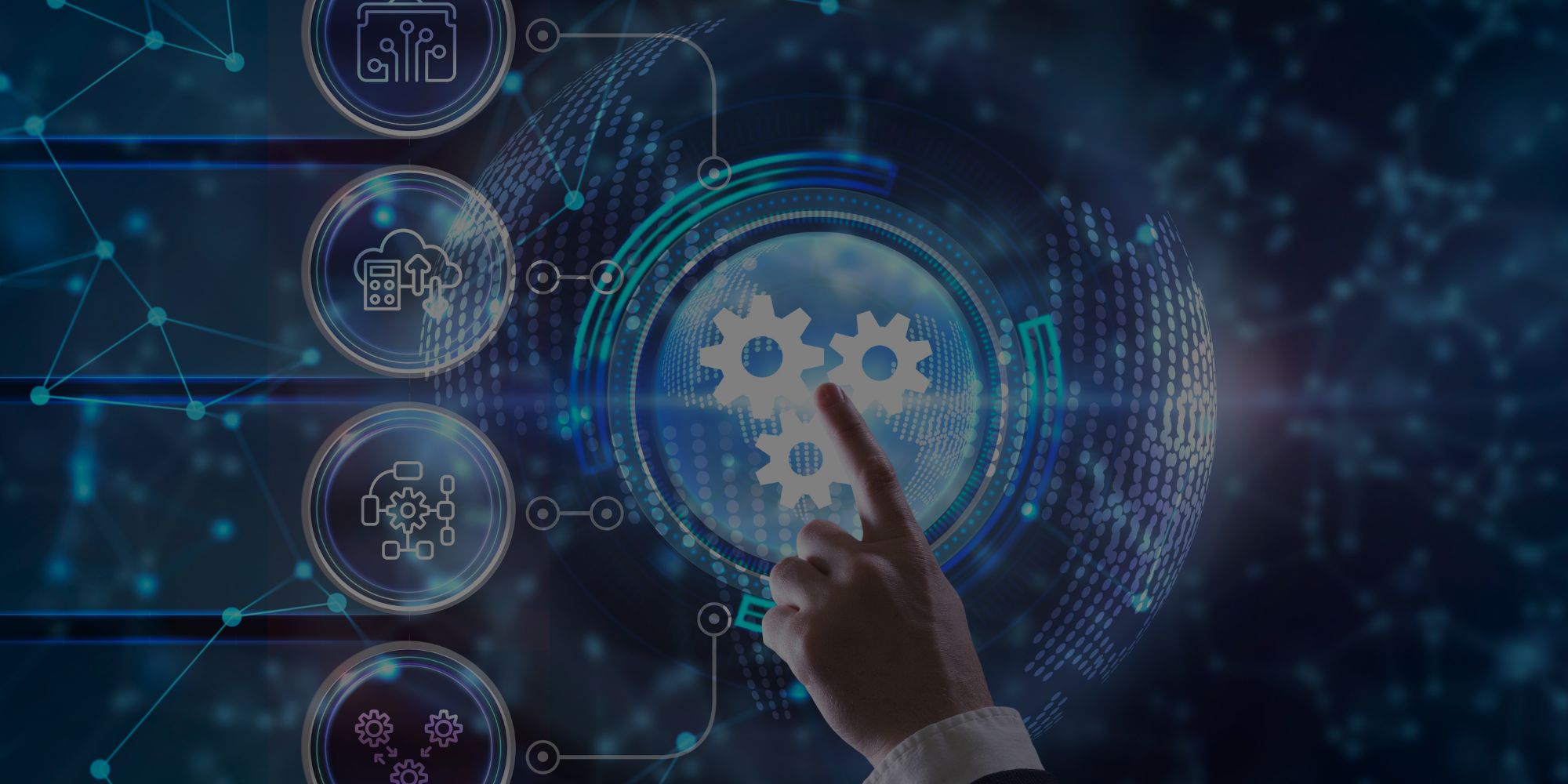
Manufacturing Operations Technology is Changing the Modern Factory
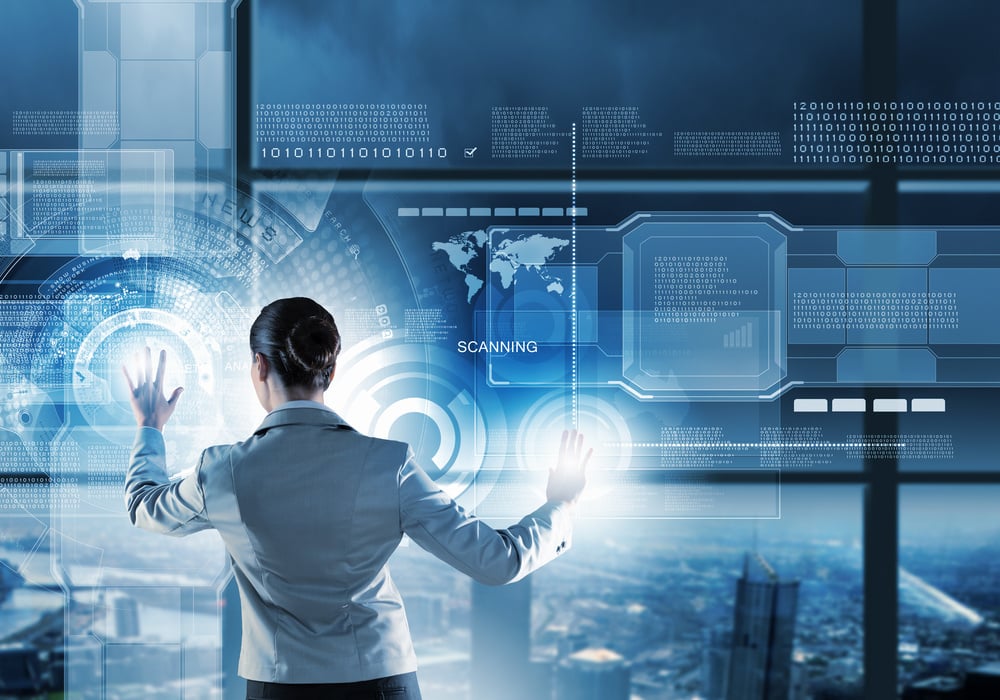
No Comments Yet
Let us know what you think