Digitizing Batch Manufacturing Records for a Paperless Pharma Factory
A batch manufacturing record (BMR) is crucial for pharmaceutical manufacturing as it ensures compliance with regulatory standards, provides a detailed record of each production batch, and guarantees product consistency, traceability, and quality control.
Types of Manufacturing Records
Manufacturing records are essential for maintaining quality, traceability, and compliance in manufacturing, particularly in regulated industries like pharmaceuticals, food production, and medical devices.
Understanding the different types of batch records is crucial for ensuring that each stage of the production process is accurately documented and meets regulatory standards.
Master Batch Record (MBR)
The Master Batch Record (MBR) acts as the blueprint for manufacturing, providing a standardized guide to ensure consistency across all batches. It includes:
-
Raw material specifications (e.g., ingredient lists, approved suppliers)
-
Equipment settings and usage instructions
-
Step-by-step manufacturing procedures
-
Required quality checks and tests
The MBR is created and approved by quality assurance (QA) teams and serves as a template for producing individual batch records.
Batch Production Record (BPR)
The Batch Production Record (BPR) is generated for each production batch and documents the actual manufacturing process. It is based on the MBR but contains real-time production data.
BPRs include:
-
Actual quantities of raw materials used
-
Environmental conditions and equipment details
-
Production timelines (times and dates of each step)
-
Deviations from standard procedures
Once production is complete, the BPR is reviewed and signed by authorized personnel to confirm the batch meets all quality and compliance standards.
Packaging Batch Record (PBR)
The Packaging Batch Record (PBR) ensures the correct labeling, storage, and final packaging of a product. It provides:
-
Packaging instructions (e.g., type of container, labeling requirements)
-
Storage conditions (e.g., temperature, humidity)
-
Lot and expiration date tracking
-
Inspection and quality control checks before distribution
PBRs help ensure that the final product meets regulatory and branding requirements before it reaches the consumer.
Electronic Batch Records (EBR)
With digital transformation, Electronic Batch Records (EBRs) are replacing traditional paper-based batch records.
EBRs provide:
-
Automated real-time data capture
-
Reduced transcription errors
-
Faster review and approval processes
-
Improved audit readiness
EBRs are fully compliant with regulatory guidelines, such as FDA’s 21 CFR Part 11, which ensures data integrity, security, and traceability.
Device History Record (DHR)
Used primarily in the medical device industry, the Device History Record (DHR) is a specific type of record that:
-
Documents the complete history of a medical device's production
-
Ensures each device is manufactured according to its Master Device Record (MDR)
-
Includes assembly, testing, and final inspection data
DHRs are critical for FDA compliance and ensure that every medical device meets safety and performance standards.
Batch Manufacturing Records (BMR) for Specialized Industries
Batch Manufacturing Records (BMRs) vary depending on the industry. Some specialized batch records include:
-
Battery Industry: Used for tracking material sourcing, assembly, safety tests, and compliance with sustainability standards (e.g., Battery Passport Initiative).
-
Food Industry: Known as Electronic Device History Records (eDHR), these track ingredient traceability, safety checks, and regulatory compliance.
Key Differences Between Record Types
Record Type |
Purpose |
Key Components |
---|---|---|
Master Batch Record (MBR) |
Acts as a manufacturing blueprint |
Materials, equipment, step-by-step instructions, quality checks |
Batch Production Record (BPR) |
Documents actual production details for each batch |
Actual quantities, process conditions, deviations |
Packaging Batch Record (PBR) |
Ensures correct final packaging and labeling |
Storage conditions, packaging specifications, final QC checks |
Electronic Batch Record (EBR) |
Digital version of batch records for efficiency and accuracy |
Real-time data capture, compliance automation, audit readiness |
Device History Record (DHR) |
Used in medical device manufacturing |
Tracks entire device production, testing, and compliance |
Industry-Specific BMRs |
Tailored for industries like food, batteries, and pharmaceuticals |
Specialized data for regulatory and safety tracking |
Understanding the different types of batch records is crucial for maintaining compliance, ensuring quality, and improving traceability.
Whether using paper-based records, electronic systems, or industry-specific solutions, implementing best practices in batch documentation helps manufacturers streamline operations, enhance product safety, and meet regulatory standards.
Components of a BMR
A batch manufacturing record is more than a document; it’s a collection of critical data associated with the entire manufacturing process. This data covers everything from raw materials to finished products, including a list of all raw materials and packaging components used.
The Packaging Batch Records, part of the Batch Manufacturing Records, contain the packaging instructions storage conditions, and expiration dates. But it’s not just about the materials and the packaging.
A batch record even includes the process manufacturing equipment settings and personnel involved in the process, tracked through the Batch Production Record (BPR). This ensures the equipment used throughout the process is up-to-date and calibrated. Any unexpected or atypical events that occur during the process are documented, along with the investigation, conclusions and CAPA.
Batch Record Life Cycle
The life cycle of a batch record is:
-
Full documentation of the process, including raw materials used, equipment settings, and GMP.
-
Tracking every step of the process and documenting any deviations.
-
Transparent and accountable record.
The life of a batch record doesn’t end when the product is manufactured. These records must be kept for at least 5 years as part of compliance documentation and as a reference for any audits or reviews. Imagine a time capsule, with all the information of a specific batch, ready to be retrieved when needed. That’s the life cycle of a batch record.
BMRs for Pharmaceutical Manufacturing
Batch records are critical for quality control in the pharmaceutical industry. By documenting the full process, they ensure products are made consistently and to specification. But their importance goes beyond quality control. Batch records also provide a documented and complete history of the production, testing, and distribution of each drug batch, so traceability is possible.
Beyond the quality control tests and traceability, batch records are also required for compliance. Regulatory bodies like the FDA require full and accurate manufacturing documentation, which batch records deliver.
Compliance and Quality Assurance
Batch records are the foundation of quality assurance and regulatory compliance in the pharmaceutical industry. They ensure drugs are made safely and efficiently, within the robust regulatory framework.
To keep future batches of pharmaceutical products safe and intact, batch records will record:
-
Raw materials and intermediates
-
Packaging components
-
Storage conditions
-
Expiration dates
It’s like a passport for each product, documenting its life from start to finish.
Example of BMR template
Tracking and Traceability
Batch records document the full history of a drug product, every ingredient and every stage of production.
This is for:
-
Tracking product issues
-
Responding to regulatory requests
-
Keeping consumers safe by tracking the entire life of a drug
By documenting every step of the pharmaceutical production process, batch records enable traceability so you can track down the source of quality issues during manufacturing.
Master Formula Records (MFR) vs. Batch Manufacturing Records (BMRs)
What is a Master Formula Record (MFR)?
The MFR is essentially the roadmap for product creation. It provides detailed instructions on how to manufacture a specific batch of a product. Think of it as a comprehensive blueprint that outlines every ingredient, every step in the process, and every parameter necessary to achieve the desired outcome.
The MFR includes:
-
Precise quantities of raw materials.
-
Specific equipment settings.
-
Detailed processing steps.
-
Required environmental conditions (like temperature and humidity).
What is a Batch Manufacturing Record (BMR)?
While the MFR offers a plan, the BMR acts as the diary of the actual execution. It records what actually transpired during the manufacturing of a specific batch.
The BMR captures:
-
The exact quantities used.
-
Timelines of each step taken.
-
Any deviations from the original plan.
-
Quality control results and observations.
Key Differences
-
Purpose: The MFR is prescriptive (telling you how to do it), while the BMR is descriptive (detailing what was done).
-
Function: The MFR is designed before production begins, guiding the process. The BMR is filled out during and after production to report outcomes.
-
Content: The MFR is static and consistent for each batch; the BMR is dynamic, varying with each batch due to real-time conditions and occurrences.
An Analogy
Imagine baking a cake. The MFR serves as the recipe—listing ingredients and instructions on mixing, baking time, and oven temperature. The BMR, in contrast, would log notes on the actual process: the number of cakes produced, any batter spilled, and adjustments made based on real conditions in the kitchen.
In summary, the MFR sets the stage, while the BMR captures the performance. Understanding both is crucial to ensuring a product is made correctly and consistently every time.
Security and Audit Control in Managing BMRs
Security and audit controls are essential in managing batch manufacturing records to ensure both process integrity and compliance with regulatory standards.
Key Functions:
Access Restriction:
Throughout various stages of production, access to specific tasks can be limited to certain employees. This restriction helps maintain control over who can make changes to MFRs and BMRs.
Dual Verification:
For critical activities like safety checks, sanitization, and ingredient measurements, having a second person confirm the process ensures accuracy and safety.
Role-Based Permissions:
Implementing role-based permissions means that individuals only have access to the information and controls necessary for their role, reducing the risk of unauthorized changes.
Authentication Protocols:
Features like two-factor authentication further secure systems by ensuring only verified users can access or modify BMRs.
Audit Trails and Compliance:
Specialized BMR software for the chemical and process manufacturing sectors provides comprehensive audit trails. These logs automatically document every change with timestamps and user identification, ensuring adherence to regulations such as those set by the FDA.
Utilizing these controls not only safeguards data but also fortifies the entire manufacturing process against potential errors and non-compliance issues.
BMRs for Battery Manufacturing
The battery industry uses BMRs as documentation tools that capture every step of the battery process and comply with regulations. These are for quality, health, and safety hazards and traceability throughout the life of the battery.
Batch Manufacturing Records Data for Battery Passports
In the fast-growing battery industry, especially for electric vehicles and renewable energy storage, the concept of a “battery passport” is becoming a reality. This is a detailed and standardized record that follows each battery throughout its life, from manufacture to end-of-life recycling or disposal. The importance of batch record data in battery passports is:
-
Traceability: Batch records contain the information that is required for the traceability of each battery. This includes the materials used, the process, and the assembly of the battery. Traceability is critical for safety, warranty, and tracking the battery’s performance over time.
-
Quality Assurance: The data in batch records ensures each battery meets strict quality standards. This includes test results, quality checks, and safety regulations. This data is needed not just for initial quality control but also for maintenance and recycling.
-
Regulatory Compliance: With regulations around battery safety and environmental impact increasing, batch records provide proof of compliance. Especially in regions with tough standards for battery production and disposal.
-
Sustainability Reporting: Battery passports have information on the origin of raw materials and the environmental impact of the process. This is for companies that practice sustainability and for regulations that require environmental impact assessments.
So the data from batch records is key to creating battery passports that provide transparency, safety, and environmental responsibility for battery use and recycling. These passports are a data repository for better management and control throughout the life of the battery.
BMRs in the Food and Medical Device Industry
BMRs for Food & Beverage Manufacturers
For the food industry, batch records are called Electronic Device History Records (eDHR). These records capture data on ingredients, process conditions and quality checks to maintain food safety and regulatory compliance.
An eDHR for food production will include:
-
Ingredient and Material Tracking: Records of all ingredients used in a batch.
-
Process Conditions: Times, temperatures and equipment settings during production.
-
Quality Checks: Sensory, microbiological and chemical test results throughout the process.
eDHRs provide traceability and compliance by capturing every detail of the process. By automating data collection and integrating with MES software or ERP, food manufacturers can achieve better compliance with food safety standards.
This means better product reliability and faster response time during food safety incidents, safer and higher quality food products.
Batch Records In The Medical Device Industry
For medical device manufacturing, batch records are called Electronic Device History Records (eDHR). These are required by medical device manufacturers and regulatory bodies like FDA to ensure devices are manufactured to specifications.
An eDHR for MD Manufacturing will include:
-
Component and Material Tracking: Records of all materials and components used in the process.
-
Assembly and Inspection Data: Assembly line operations, inspection results, and test data.
-
Compliance and Approval Signatures: Electronic signatures for each process stage and quality control approval.
eDHR systems help chemical and process manufacturers, comply with regulations, and improve traceability and overall process quality. By automating data collection and integrating with other systems (like MES or ERP) companies can achieve better compliance to industry standards.
How Do Industry-Specific Compliance Management Tools Work Within BMR Software?
Industry-specific compliance management tools within Batch Manufacturing Record (BMR) software are designed to streamline regulatory adherence by automating the complex process of information collection and documentation. Here’s how they operate:
-
Automation of Compliance Data: These tools automatically gather essential data needed for regulatory standards, such as the FDA's stringent requirements. This automation ensures that all necessary information is accurately captured and organized.
-
Integration of Safety Protocols: At various stages of production, health and safety hazards are assessed, and requirements for Personal Protective Equipment (PPE) are clearly outlined, helping to safeguard workers and maintain compliance with industry safety standards.
-
Real-Time Updates: BMR software incorporates automatic updates, ensuring that compliance information remains current with evolving regulations. This minimizes the risk of falling behind on compliance due to outdated standards.
-
Tailored Industry Features: The tools are equipped with features that cater to specific industries, enabling businesses to address unique compliance challenges efficiently. This includes predefined checklists and documentation templates tailored to meet sector-specific needs.
By incorporating these functionalities, BMR software plays a crucial role in simplifying the compliance management process, allowing companies to focus on production while ensuring they meet all necessary legal and safety regulations.
Regulatory Compliance in Manufacturing
Manufacturers must document and track all production details within batch records to meet regulatory requirements. Adhering to Good Manufacturing Practice (GMP) standards ensures compliance, with records securely maintained for at least five years.
Quality assurance representatives review and sign batch records for accuracy, aligning with ICH Q7 guidelines for pharmaceutical ingredients. 21 CFR Part 211 mandates detailed documentation of every manufacturing step to uphold regulatory standards.
Comprehensive batch records enable full traceability, from raw materials to finished products, simplifying audits and demonstrating compliance efficiently.
Electronic Batch Records: Changing Documentation
The digital revolution is happening everywhere and pharma is not an exception. Electronic batch records (EBR) is at the forefront of this revolution, bringing huge improvements in operational efficiency and data integrity. Successful deployment reduces the cognitive load for quality assurance personnel and reduces review time in process testing results.
EBRs give you:
-
Efficiency
-
Flexibility
-
Scalability
-
Customised solutions
-
Current and future business needs
-
Beat the competition
-
Access to valuable data
While the initial stages of digital transformation can be tough, going electronic batch records puts you in a position to get these benefits.
From Paper to Electronic
Electronic systems like EBRs provide automatic data capture, reduced errors, better data accessibility, and can impact the bottom line of the company by increasing efficiency and profitability. These systems can be integrated with other tools like manufacturing execution systems, supporting functions like automatic lot number generation and production execution via mobile devices and financial platforms for full management.
Mobile BMRs enhance these electronic systems by leveraging the capabilities of mobile devices, offering several significant advantages:
-
Real-Time Accessibility: Access batch manufacturing records from anywhere, ensuring critical data is always at your fingertips, whether you're in the office or on the move.
-
Instant Updates: Record formula changes immediately, maintaining accurate and up-to-date records that prevent costly errors and streamline operations.
-
Paperless Efficiency: Eliminate hard copies, reducing clutter and the risk of losing important documents, which enhances both security and environmental sustainability.
-
On-the-Go Inventory Management: Check inventory levels while on the go, allowing for quick adjustments and informed decision-making in real-time.
By integrating these mobile capabilities, businesses can achieve a more agile and responsive production environment, further boosting productivity and operational efficiency.
Data Integrity with EBRs
Electronic Batch Records (EBRs) ensure data integrity by following ALCOA principles, where records are:
-
Attributable
-
Legible
-
Contemporaneous
-
Original
-
Accurate
Batch Manufacturing Records as part of EBRs includes a full Bill of Materials to meet cGMP requirements. A single batch manufacturing record is part of this in-process manufacturing part.
Life sciences and pharma software solutions provide full audit trail and batch reporting to support FDA regulations, and further compliance through EBRs. With features like automatic calculations and electronic signatures, EBRs build trust and make it usable. Successful implementation of EBRs depends on full training of end users which is critical for proper use and overall success of the system.
EBRs help to achieve ‘right-the-first-time’ records by showing exception trends and enabling corrective actions to pre-empt deviations. The automated triggered review in EBRs allows focused attention on deviations and promotes a culture of continuous improvement in the process.
Key to a Full BMRs
Creating a full batch manufacturing record is an art. A good batch record should capture all production batch details well:
-
Material and components used
-
Process steps
-
Personnel involved
-
Health and Safety
-
Actual vs expected results
-
Packaging and labeling
-
Audit trail
This will ensure the process manufacturer's final product meets quality requirements.
Raw materials, processed data, and storage conditions must be documented accurately to maintain product quality. Accurate data within batch records is critical for decision-making and transparency of chemical and process manufacturing. The change log in the batch record will track all changes during production. Planned deviations are allowed, and EBRs must be flexible to various process flow scenarios.
Raw Materials Detailing
A full batch record is not complete without raw materials detailing.
This includes:
-
Actual lot numbers which is critical for product quality and traceability
-
Raw materials documentation should include quantity
-
Material lot numbers
-
Expiration dates
-
Lab results to verify quality before use in manufacturing.
Imagine a detective piecing together clues to solve a case. In the same way each raw material detail is a clue in the process. Every bit of information adds to the story, to paint a full picture of the finished product and journey.
Production and Testing Data
Production parameters and testing results must be accurately recorded to verify the pharmaceutical manufacturers' product quality and consistency. Each step of the process must be recorded to ensure the batch was manufactured according to the master batch record which is part of the same cycle as the master production record.
The quality control section of batch manufacturing records is for:
-
All product tests
-
How to do these tests
-
Equipment required
-
Outcomes and any observations
Just like an inspector checking quality in a factory, these records will ensure each product out of the production line meets quality standards.
Packaging Components and Storage Conditions
Creating master packaging records forms the foundation for packing instructions of finished pharmaceutical products, ensuring consistency and compliance. Each batch packaging master formula record has specific instructions for the pharmaceutical product batch, composition, and packaging requirements.
To achieve this, these records function similarly to manufacturing formula records MFRs and BMRs but are tailored for the packaging process. They outline detailed guidelines that are crucial after the raw material has been manufactured. This includes specifying how much raw material should be pressed into a tablet, determining the number of tablets per bottle, and deciding on the type of cap to use.
These documents are essential for documenting the results of the packaging process, ensuring that every step is executed accurately and consistently. By following these comprehensive instructions, pharmaceutical companies can maintain the integrity of the product through each stage of its journey to the consumer, emphasizing quality and regulatory compliance.
Components of a Master Formula Record
To produce a consistent and safe product, a master formula record (MFR) should include:
-
Bill of Materials: This comprehensive list details all ingredients and components required at each stage of production, specifying size, weight, and measures.
-
Health and Safety Information: Proper handling of materials is critical, including guidelines on heating, cooling, and storage temperatures, along with necessary personal protective equipment (PPE).
-
Maintenance, Cleaning, and Sanitizing Instructions: Before manufacturing begins, clear instructions on necessary maintenance, cleaning, and sanitizing procedures must be included to ensure equipment readiness.
-
Step-by-Step Manufacturing Instructions: Detailed, clear, and orderly instructions from start to finish help maintain precision and consistency in the manufacturing process.
-
Estimated Costs and Labor: Including an estimate of costs associated with each step, derived from equipment expenses and labor hours, is vital for budgeting and resource management.
By integrating these elements, the master formula record not only supports efficient manufacturing but also upholds the highest standards of safety and quality, pivotal for any pharmaceutical production process.
Batch Record Best Practices
Batch record best practices are key to:
-
Product quality and safety
-
Minimizing contamination
-
Accurate documentation
-
Tracking process
-
Process improvement
They are the benchmark for batch records, not just compliance but efficiency and reliability.
Regular Audits and Updates
A batch record is not a static document. Batch manufacturing records must be updated and reviewed regularly to comply with regulations and to identify areas for process improvement. A full batch record should include deviations and exceptions that occurred during production.
EBR systems can detect exceptions and process deviations and flag them for quality review and expedite resolution for faster manufacturing. Pharmaceutical companies must review batch records to ensure procedural and regulatory compliance and to catch errors before product release. Personnel must get non-confrontational feedback on documentation errors to encourage accurate records and concise documentation within the company.
Documenting Personnel Training
Documenting personnel training is key to preventing costly mistakes and compliance. Well-trained personnel are better at recording information accurately and therefore the quality of batch records. Personnel must get regular training on the latest documentation practices to stay up to date with industry standards.
Hands-on training like mentoring and shadowing experienced staff provides practical experience in the documentation processes. Cross-training between departments will give a broader understanding of the role of documentation in the pharmaceutical manufacturing process. Training effectiveness must be measured through regular evaluation and practical assessment to ensure employees stay competent in documentation.
Software for Batch Manufacturing Record Management
In the digital age, software is becoming more important to simplify record management. Manufacturing Operations Management (MOM) software plays a vital role in optimizing batch manufacturing processes.
MOM solutions integrate Manufacturing Execution Systems (MES), Quality Management Systems (QMS), Advanced Planning and Scheduling (APS) software, and Laboratory Information Management System (LIMS) software to provide a unified platform for managing BMRs.
By using MOM software solutions, manufacturers can:
-
Automate data entry and validation to reduce human errors.
-
Improve real-time visibility into production and compliance tracking.
-
Enhance traceability from raw materials to finished products.
-
Ensure regulatory compliance through built-in validation and reporting tools.
-
Integrate seamlessly with Electronic Batch Records (EBR) to enable faster, paperless documentation.
APS software enhances production efficiency by optimizing scheduling and resource allocation, ensuring that materials, equipment, and labor are utilized effectively.
LIMS software streamlines laboratory workflows by managing sample data, automating quality control, and ensuring compliance with regulatory requirements.
MOM software provides centralized data storage, automated workflows, and real-time analytics, helping companies ensure regulatory compliance while improving operational efficiency.
By incorporating MOM, APS, and LIMS solutions, manufacturers can reduce manual paperwork, accelerate batch release, and enhance overall production quality.
Key Features to Consider When Choosing BMR Software
When selecting BMR software for the chemical and process manufacturing industries, understanding essential features can guide you to make the best choice. Here's what to look for:
Tailored Process Instructions
Look for software with detailed step-by-step guides that auto-populate from master formula records. This feature ensures seamless navigation through the production stages without needing to switch between applications while maintaining the integrity of the process with logged sign-offs and permissions.
Compliance Management Tools
Industry-focused compliance management is crucial. The software should handle documentation for regulatory bodies automatically, including integrating safety precautions like PPE requirements at each manufacturing step. Regular updates for compliance standards ensure ongoing alignment with regulations such as those set forth by the FDA.
Robust Security and Audit Features
Prioritize software that offers granular security controls with role-based permissions. Critical steps in the manufacturing process, including any amendments made to MFRs and BMRs, should only be accessible to authorized personnel. An audit trail that logs and timestamps changes with user IDs enhances security and compliance.
Integrated Inventory Management
Effective BMR software should sync with inventory management systems to update material usage dynamically. This capability allows for real-time inventory tracking, adjusting material quantities and yields automatically as batch records are completed.
Mobile Accessibility
Choose software with mobile capabilities that allow users to manage batch records anytime, anywhere. This feature facilitates on-the-go access to data, and real-time updates, and reduces reliance on paper documentation.
Quality Assurance Tools
Quality management features are essential for monitoring quality testing data and deviations from standard records. The system should also support tracking variance sources and enabling effective management of byproducts and co-products to maintain product integrity and compliance.
Equipment Integration
Check for seamless integration with manufacturing equipment like scales and sensors. Direct data transfer from equipment to records reduces manual entry, saving time and ensuring high accuracy in measurements such as weight and temperature.
Automatic Unit Conversions
Ensure the software can handle unit-of-measure conversions automatically to facilitate accurate inventory handling. This feature is critical for managing formulas, and ensuring precise calculations for pricing and sales.
Dynamic Fields and Scaling
The software should support dynamic fields that link data from previous steps for continuous calculations and comparisons. A scaling function is advantageous for adjusting master formulas based on required product yields, enhancing flexibility.
Packaging Record Management
For industries requiring specialized packaging, seek out BMR software that includes functionality for master and batch packaging records. These records encompass instructions for processes like forming tablets or packaging bulk goods, ensuring thorough documentation from production through to final product distribution.
Selecting BMR software with these features will ensure your systems are efficient, compliant, and streamlined for the unique demands of the chemical and process manufacturing industries.
How Quality Management Features in BMR Software Help Maintain Product Standards
Quality management features in Batch Manufacturing Record (BMR) software are essential tools for maintaining high product standards. They ensure that each product meets customer expectations, preserves the company's reputation, and complies with industry regulations.
Key Benefits of Quality Management Features
Data Monitoring and Testing
Quality management tools allow for the detailed tracking of quality testing data. This enables organizations to closely monitor product quality at every production stage.
Deviation Tracking
By identifying any deviations from the standard manufacturing processes, companies can quickly address discrepancies. This helps in preventing defective products from reaching consumers.
Root Cause Analysis
Efficiently identifying and investigating the source of variances is crucial. Quality management software provides capabilities for root cause analysis, ensuring prompt corrective actions.
Co-products and Byproducts Management
With features that manage byproducts and co-products, companies can optimize use and reduce waste—an essential aspect of maintaining sustainable practices.
How Do Unit of Measure Conversions Within BMR Software Ensure Accuracy in Manufacturing?
In the chemical and process manufacturing sectors, precision is paramount. Manufacturing record management software plays a crucial role in maintaining this precision by converting various units of measure automatically.
This capability is essential for several reasons:
-
Standardization Across Processes: By converting units and packaging into standardized base units, the software ensures that all data related to inventory is uniform and consistent across the board. This eliminates discrepancies that could arise from manual conversions.
-
Accurate Inventory Tracking: Accurate unit conversions are pivotal for maintaining correct inventory levels. BMR software implements this by consistently tracking inputs and outputs in uniform units, thereby reducing the risk of stock discrepancies and stockouts.
-
Precision in Cost Calculation: Converting units automatically allows for more accurate pricing calculations. With standard units, determining the cost of raw materials, production, and final products becomes seamless, leading to reliable financial insights.
-
Enhanced Quality Control: Manufacturing processes often rely on precise recipes and formulas. By converting measurements accurately, the software aids in adhering to these precise specifications, ensuring product quality and consistency.
-
Comprehensive Analytics: Accurate data conversion translates to reliable analytics. This means you can trust the insights drawn from your sales and inventory, aiding in strategic business decisions.
-
Centralized Data Storage: Centralized data storage within Electronic Batch Record (EBR) systems improves collaboration and facilitates data access among various departments involved in the manufacturing process.
Overall, BMR software facilitates a higher level of accuracy and efficiency in manufacturing processes, ensuring that operations run smoothly and products meet the highest quality standards.
FAQs
What is a batch record?
A batch record is a full document that captures the entire production process of a specific batch of products, to ensure the batch is quality and safe. It is a detailed account of the manufacturing steps and quality control measures.
Why batch records in pharmaceutical manufacturing?
Batch records are important in pharmaceutical and manufacturing processes because they ensure product quality and safety, reduce risk of contamination and document production process, to improve process.
What are the advantages of EBRs?
Transitioning to EBRs will bring operational efficiency, data integrity, enhanced efficiency, and compliance by automating critical steps and reducing errors.
What is software role in batch record management?
Software simplifies batch record management by integrating with equipment, automates manual data entry and collection and provides real time visibility to production (no date).
How to maintain batch records?
Review and update batch records regularly, record all raw materials, production and quality testing data and train documentation personnel to follow batch records important and record best practices.
How does integrating inventory management with BMR software improve manufacturing processes?
Integrating inventory management systems with Batch Manufacturing Records (BMR) software can significantly improve manufacturing processes. By connecting these systems, you gain the ability to update material usage instantly as each batch is processed. This ensures that your inventory levels are accurate at all times, reducing the chances of stockouts or overstocking.
Why are dual sign-offs important in the context of BMRs?
Dual sign-offs serve as a critical verification step to ensure that multiple qualified individuals have reviewed and approved key stages of the manufacturing process, enhancing accountability and accuracy.
What specific elements are verified through BMRs?
Elements verified through BMRs include the adherence to health and safety procedures, the execution of quality control testing, appropriate handling of ingredients, employee clearance levels, and the completion of necessary dual sign-offs.
How do FDA regulators use BMRs?
FDA regulators utilize BMRs to confirm that health and safety protocols have been correctly followed, quality control tests have been executed, and proper procedures for ingredient handling are observed.
What is the purpose of BMRs in the context of FDA regulations?
The primary purpose of BMRs is to ensure the health, safety, and quality of consumable and topical products, aligning with FDA requirements.
What types of products are subject to FDA regulations regarding BMRs?
FDA regulations concerning batch manufacturing records apply to products such as pharmaceuticals, packaged foods, nutritional supplements, and personal care items like deodorants and shampoos.
What are the immediate benefits of using mobile devices for batch record management?
Mobile devices enable the elimination of physical paperwork and allow for real-time updates to formula changes, ensuring that the most current information is always available.
Share this
You May Also Like
These Related Stories
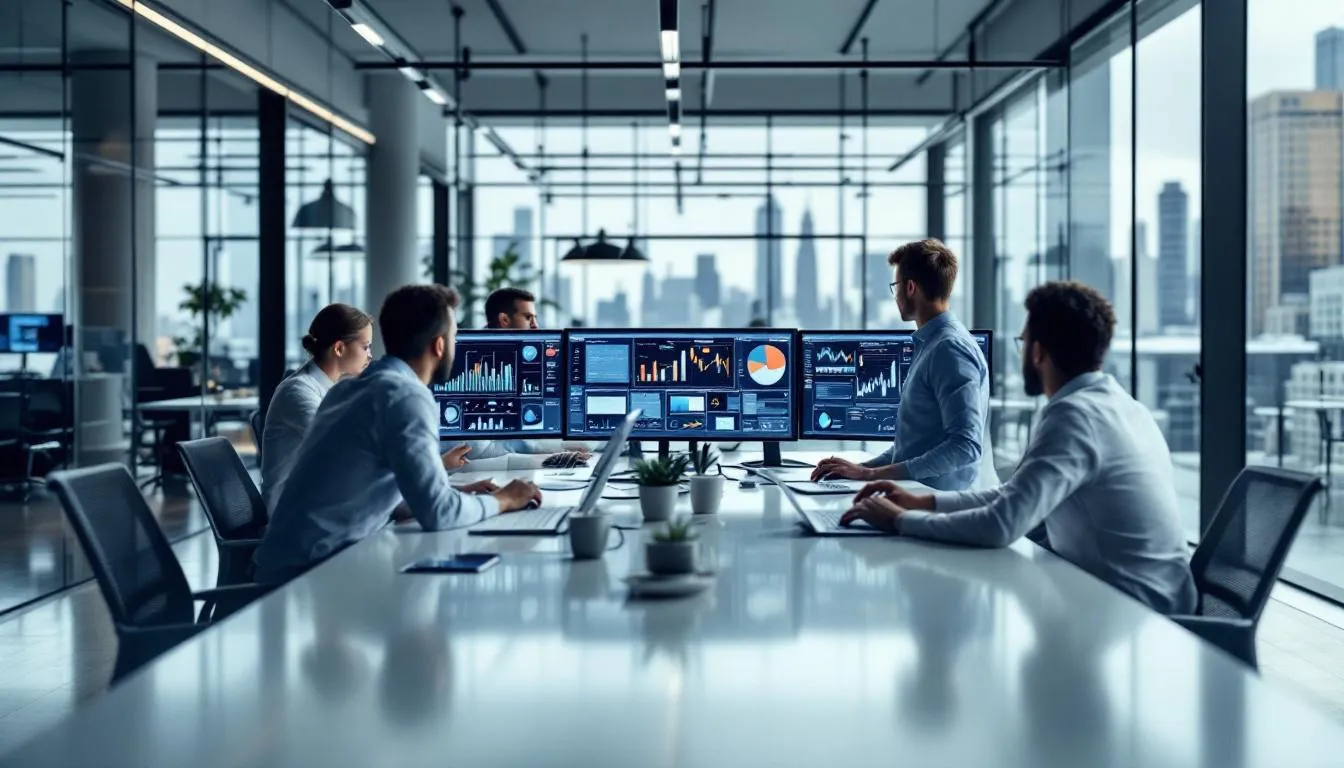
Metadata Framework: A Complete Guide to Structured Data Management
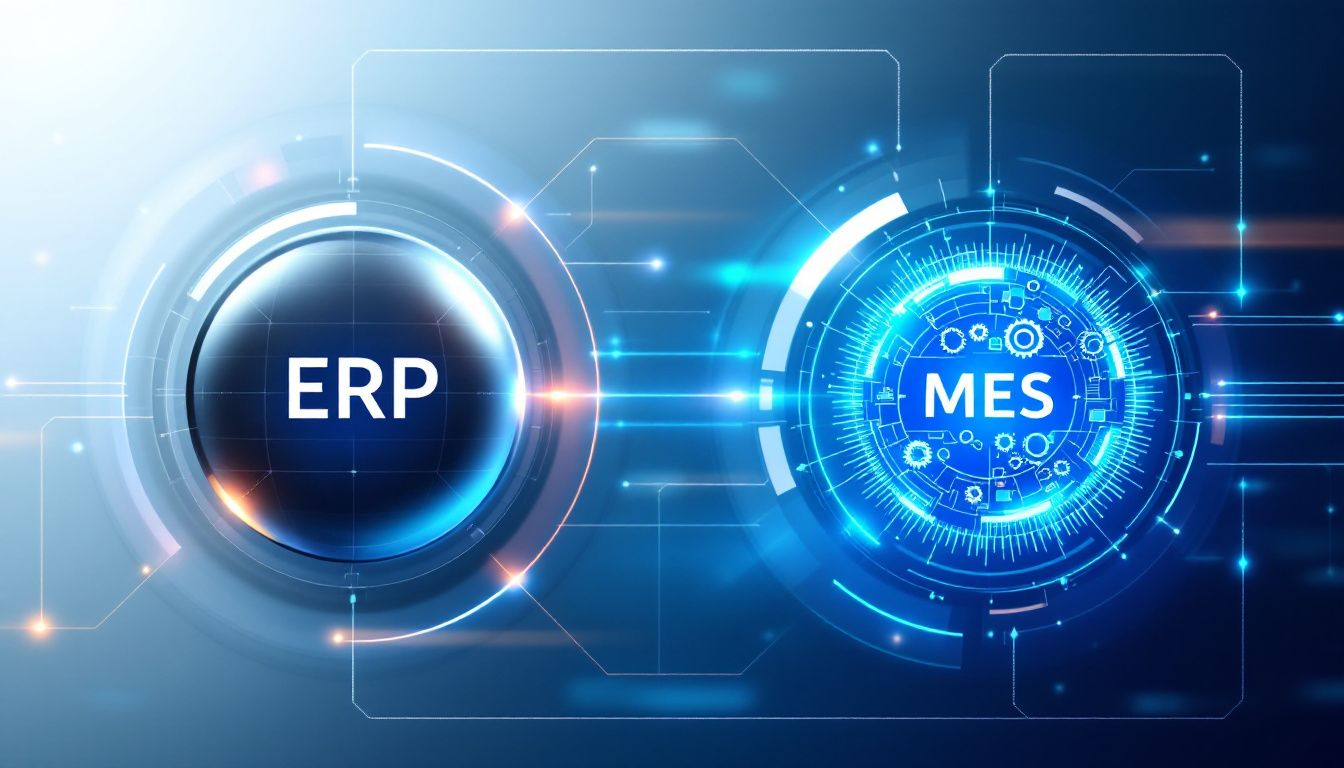
ERP vs MES: Key Insights to Choose the Right System for Your Business
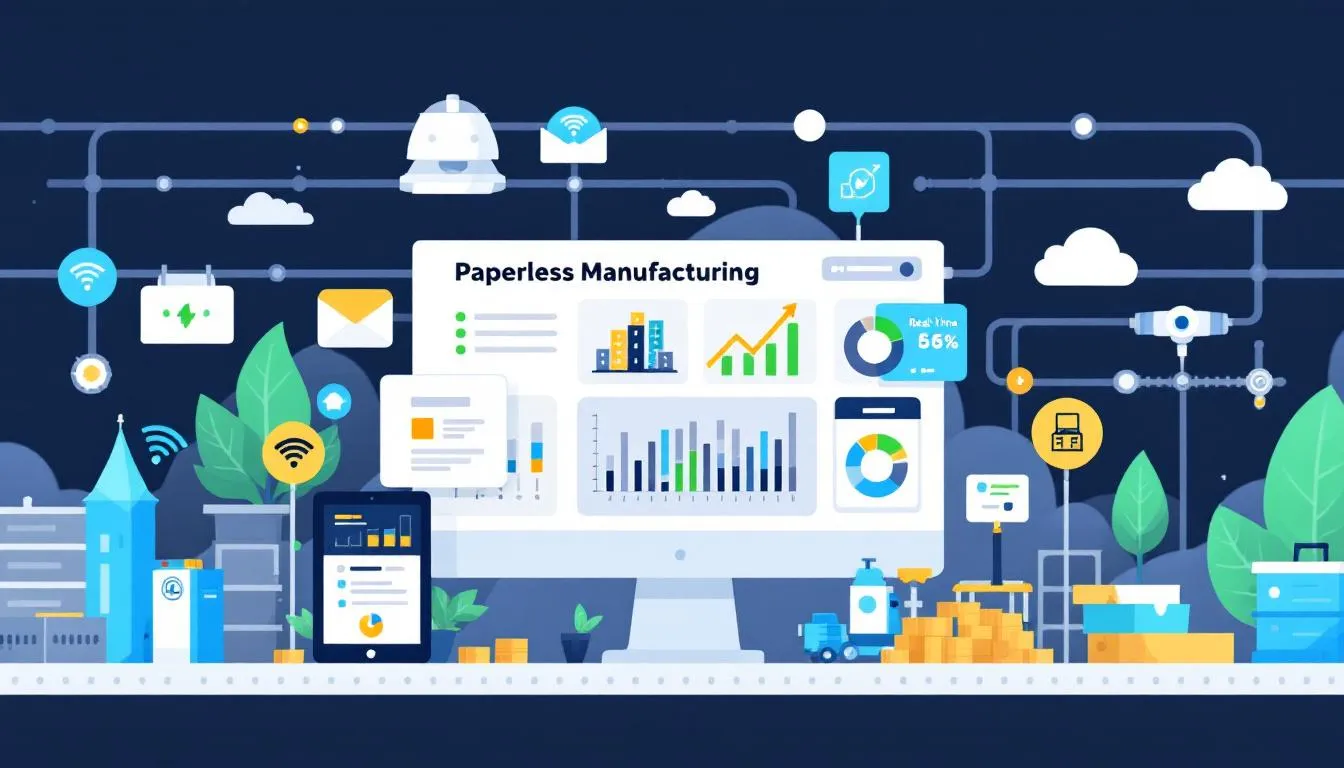
No Comments Yet
Let us know what you think