Best Practices for Manufacturing Systems Integration
Discover essential strategies for integrating manufacturing software to enhance efficiency and productivity.
By leveraging the right integration techniques, you can streamline your manufacturing systems, ensuring seamless communication between existing systems, automation systems, and enterprise resource planning tools. This not only boosts operational efficiency but also positions your company for success in a rapidly evolving industry.
Why Systems Integration in Manufacturing Matters
In today’s manufacturing world software integration is key to optimising and driving efficiency. By integrating all your manufacturing systems including ERP and automation systems you can streamline your processes, improve communication and overall productivity. Software integration allows systems to talk to each other and share data in real time, visibility, data analysis and decision making.
Manufacturing companies benefit from software integration as it gives data consistency, collaboration and optimisation of product development and production processes. Software integration reduces manual data entry and minimises errors so manufacturing processes are more accurate and reliable. It also enables better departmental collaboration and supply chain management. Integrating new solutions with existing systems is key to operational efficiency and Digital Transformation.
By understanding software integration in manufacturing you can unlock your manufacturing systems and get ahead of the competition. Integrating Product Lifecycle Management (PLM) systems helps manage product data throughout its lifecycle so product development and release processes are more efficient. Systems integrators play a big part in this by connecting automation and controls in manufacturing operations so all the technical components work together seamlessly.
ERP Integration Challenges
Software integration has many benefits but it also has its own challenges. Understanding these challenges is key to successful integration. Some of the key integration challenges in manufacturing are:
-
Different systems and software versions not compatible, which can break the manufacturing process with automation, robotics and other advanced technologies
-
Data inconsistency and duplication which can slow down production processes, monitoring, data exchange on production orders and quality control
-
No standard data formats
-
Long and complicated integration processes
-
Employee resistance to change
Managing complex projects requires the expertise of manufacturing systems integrators. These integrators streamline processes and optimise automation systems so businesses can focus on their core activities and get projects done on time and budget.
By understanding these challenges you can develop a strategy to overcome them and get a smooth integration.
Data Standardisation and Centralisation Practices
One of the key practices for software integration in manufacturing is data standardisation and centralisation. Standardising data formats and having data consistency across all systems is key to integration. It allows for easy data exchange and eliminates data duplication and inconsistency. Quality control in data standardisation is important for monitoring and maintaining standards so operational efficiency and downtime reduction.
Having data in one central repository or database allows real time access and data integrity. It also simplifies data management and ensures all departments have access to the same accurate and up to date information. Data standardisation and centralisation practices not only enables integration but also data analysis and decision making. This centralised architecture is commonly known as “Unified Name Space” (UNS) in the manufacturing world.
Implementing Unified namespace as a data standardisation strategy involves creating a centralised system for naming conventions and data structures across all manufacturing software applications. By having a unified naming convention organisations can ensure data formats are consistent so information can be exchanged between systems. This approach reduces data duplication and inconsistency and improves data quality and integrity. Unified namespace standardisation enables efficient data management and departmental collaboration so data analysis and decision making is more accurate and streamlined. By implementing a Unified namespace strategy you can optimise your software integration efforts through system integration and get the most out of a connected manufacturing system.
Automation and AI for Operational Efficiency
Automation and AI technologies are key to seamless manufacturing operations. By using automation you can automate repetitive tasks, reduce manual errors and overall efficiency. Automation can exchange data between systems and ensure real time data synchronisation and no delays.
AI technologies like machine learning and predictive analytics can analyse large amounts of data and provide insights for decision making. These technologies can optimise manufacturing processes, identify patterns and predict potential issues so proactive measures can be taken.
Manufacturing systems integrators are key to production efficiency and quality in automated manufacturing environments. By using automation and AI technologies you can get higher level of integration, operational efficiency and innovation in your manufacturing processes.
Scalability and Flexibility in Software Integration Solutions
Scalability and flexibility is important when implementing software integration solutions in manufacturing. As businesses grow and change their integration needs will change. A project manager is key to ensuring integration solutions are scalable and flexible for future requirements.
Scalable integration solutions can handle growing data volumes and add more systems. They allow you to add new functionality and expand your integration capabilities without disrupting existing processes.
Flexibility in integration solutions is just as important. It allows you to integrate different systems including legacy systems, third party software and cloud based applications. Flexible solutions can also accommodate changes in business processes and customisation to meet specific integration requirements.
By having scalability and flexibility in software integration solutions you can future proof your integration and adapt to the changing needs of your manufacturing processes.
From Monolithic to Microservices
Monolithic architecture is traditional single tiered systems in manufacturing. Microservices architecture breaks applications into independent services for flexibility, scalability and resilience. Each service does one thing and communicates through APIs so it’s easier to adapt to changing requirements. Organisations get better resource utilisation, cost efficiency and faster response to market demands and innovation and agility.
As manufacturing organisations continue to evolve and adapt to the digital age many are moving from traditional monolithic systems to more agile and flexible microservices architecture. This is a key part of systems integration and allows businesses to break down complex systems into smaller independent services that can be developed, deployed and scaled independently.
Microservices have many advantages over monolithic systems, scalability, resilience and agility. By decoupling services and allowing them to communicate through APIs you can scale individual components based on demand and get better resource utilisation and cost efficiency.
Also microservices allow you to respond quickly to changing market demands and innovation opportunities. With smaller more focused services development teams can work independently on different components and get faster deployment times and more flexibility.
But moving from monolithic systems to microservices is not without its challenges. You need to plan and execute the migration carefully to minimize disruption to operations. This means identifying dependencies between services, re-architecturing applications and implementing robust monitoring and management systems.
Despite the challenges the benefits of microservices in manufacturing are clear. By going for a more modular and scalable architecture you can future proof your systems, drive innovation and stay ahead of the competition in today’s fast changing manufacturing landscape.
FAQ: Manufacturing Systems Integration
Why is systems integration important in manufacturing?
Systems integration in manufacturing optimises operations and efficiency by ensuring information systems including ERP talk to each other seamlessly and exchange data, communication, data analysis and decision making.
What are the benefits of software integration for manufacturing companies?
Software integration ensures data consistency, collaboration, product development and production process optimisation, reduces manual data entry and minimises errors and increases accuracy and reliability.
Manufacturing Execution Systems (MES) are key to operational excellence in manufacturing systems by integrating with other applications like MOM, PLM and ERP to enhance workflows, optimise resource allocation and support decision making with real time data.
Why is scalability and flexibility important in software integration solutions?
Grow and adapt.Grow and adapt.Grow and adapt. Grow and adapt.
Share this
You May Also Like
These Related Stories
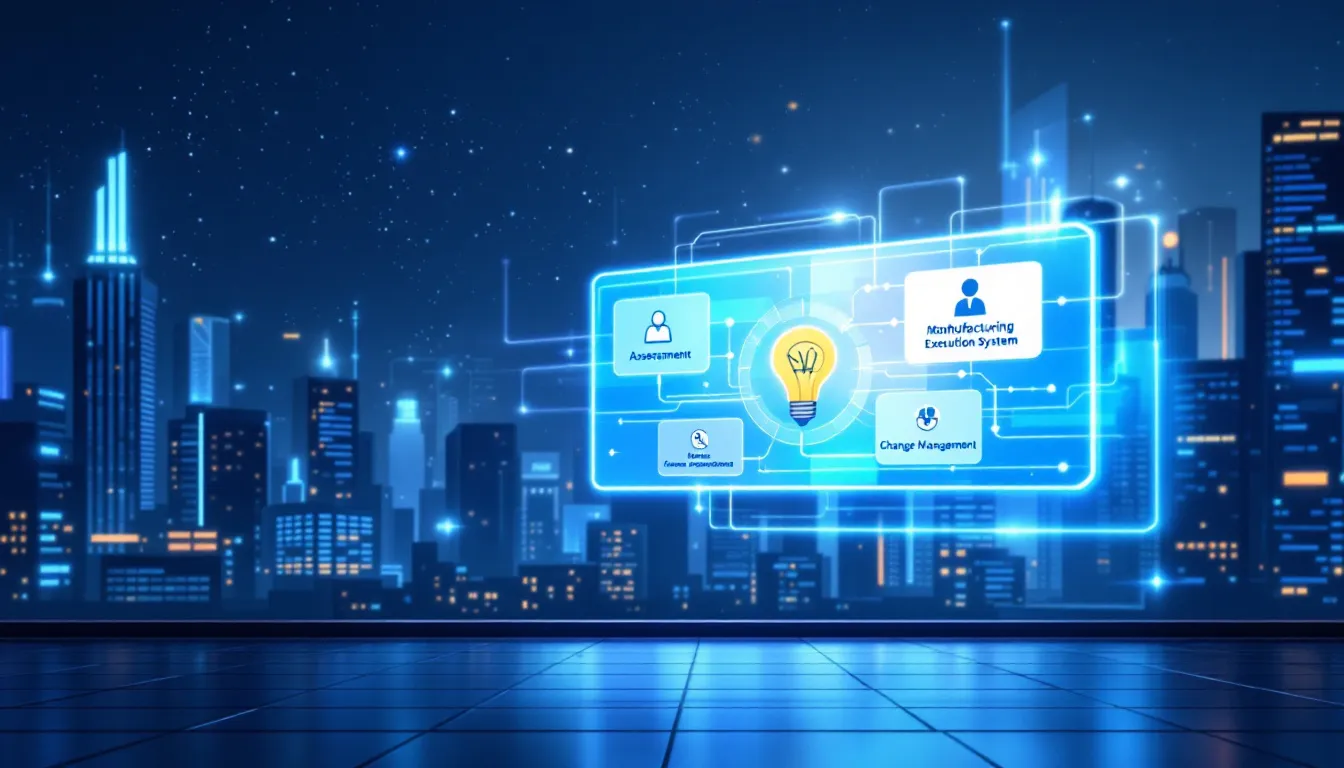
Mastering MES Implementation: Key Steps for Success and Efficiency
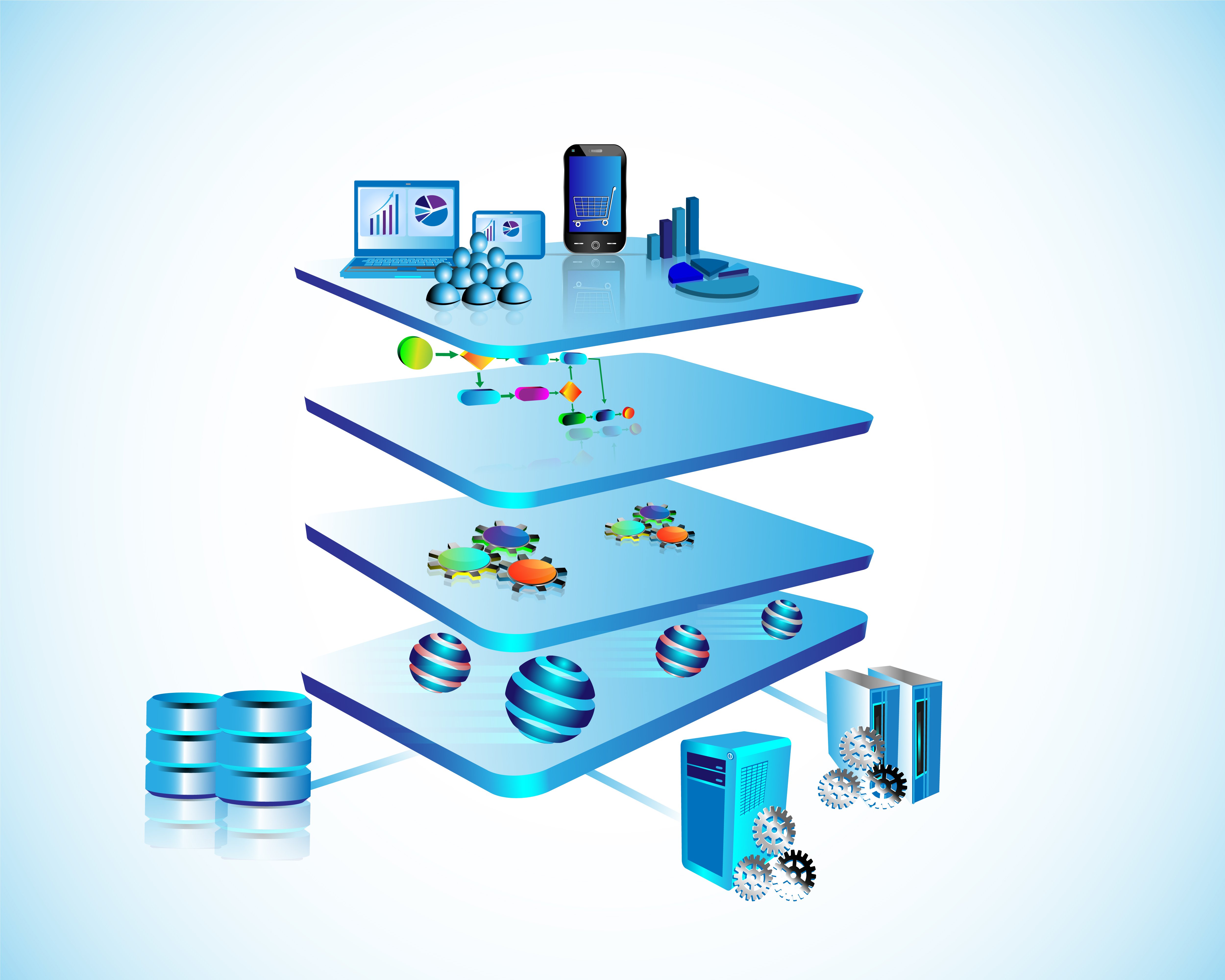
Data Virtualization for Manufacturing Efficiency
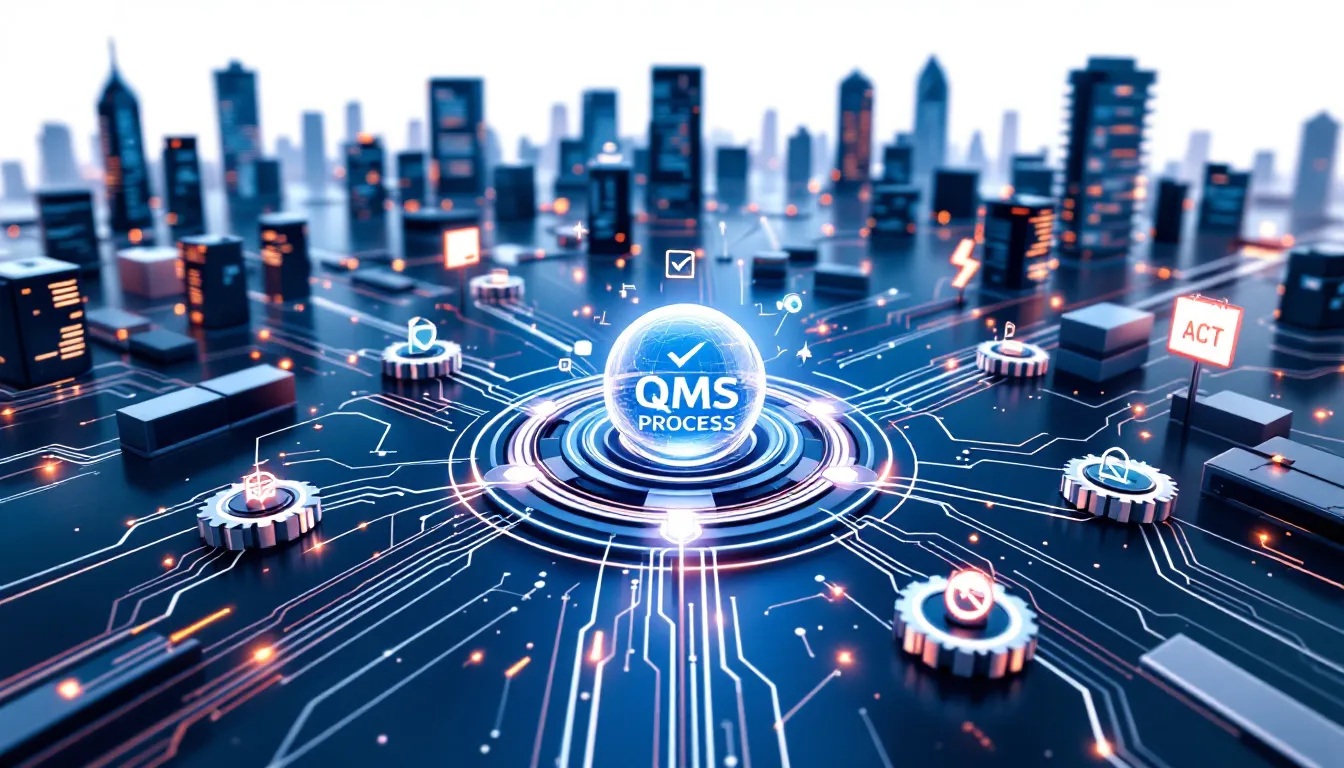
No Comments Yet
Let us know what you think