Mastering MES Implementation: Key Steps for Success and Efficiency
Wondering how to make your manufacturing process more efficient? Implementing Manufacturing Execution System (MES) software could be your answer.
This article breaks down the essential steps for successful MES implementation. You’ll discover how to identify your business needs, choose the right MES, assemble a project team, and tackle common challenges. Find out how MES can revolutionize your operations.
Key Takeaways
-
Manufacturing Execution Systems (MES) optimize operations by providing real-time monitoring, predictive analysis, and improved decision-making capabilities.
-
Successful MES implementation requires defining business objectives, conducting thorough pre-implementation analysis, securing executive sponsorship, and forming a competent project team.
-
Ongoing support, effective training, and continuous data analysis post-implementation are key to maximizing the benefits of MES, such as enhanced efficiency and improved quality control.
Understanding MES Implementation
Manufacturing Execution Systems (MES) are critical for modern manufacturers aiming to optimize operations and boost productivity. An MES is a digital system that monitors and controls manufacturing processes, facilitating real-time management and monitoring.
This real-time insight allows manufacturers to make informed decisions concerning maintenance and production efficiency, ultimately enhancing operational performance.
The integration offered by MES promotes better visibility and coordination across different manufacturing processes, helping to identify production bottlenecks and enabling targeted improvements throughout the entire production process. Additionally, MES systems provide predictive analysis capabilities, forecasting quality issues before they arise and optimizing production workflows.
With real-time data analytics, manufacturers can improve decision-making and quickly adjust production strategies.
Unlike the traditional Waterfall methodology, which emphasizes completing distinct project phases sequentially, Agile implementation focuses on iterative, incremental progress. Agile encourages flexibility, collaboration, and adaptability, making it particularly suited for MES implementation in dynamic manufacturing environments. By breaking the project into smaller, manageable phases called sprints, manufacturers can continuously deliver functional components, address issues early, and adapt to evolving requirements.
Initial Steps for MES Implementation
Implementing a Manufacturing Execution System (MES) requires several foundational steps. Recognizing the needed MES solution, desired outcomes, and implementation approach are key considerations. Initial steps include identifying business objectives, conducting a pre-implementation analysis, and securing executive sponsorship to streamline the process.
Identifying Business Objectives
Identifying business objectives is the first step in any MES implementation. This involves pinpointing existing challenges and defining outcomes like enhanced productivity, quality, and traceability.
Manufacturers should set specific objectives before selecting an MES, ensuring that the system aligns with their strategic goals. This stage is crucial for integrating MES with other business systems like enterprise resource planning (ERP) and business intelligence tools.
With agile implementation, these objectives can evolve throughout the implementation process. Teams should prioritize key objectives for initial sprints, allowing flexibility to adapt and refine goals based on feedback and results from early iterations.
Conducting a Pre-Implementation Analysis
Conducting a comprehensive pre-implementation analysis is crucial for MES success. This analysis covers all production areas, documenting the current state and defining desired outcomes. It helps establish a dynamic backlog of prioritized objectives and tasks. Agile teams use this backlog to guide each sprint, ensuring that high-value features are delivered first. Additionally, selecting essential features and modules tailored to specific operational needs is vital during this phase.
Preparing for existing process changes and training staff are critical during the initial stages. Pre-implementation employee training ensures that users are effective in utilizing the MES from the outset.
Assessing the total cost of ownership (TCO), including both initial and ongoing expenses, is also important to facilitate a smooth transition.
Securing Executive Sponsorship
Executive sponsorship is vital for successful Agile MES implementation. Sponsors must champion the Agile approach, supporting the iterative process and ensuring alignment with overarching business goals. Frequent check-ins with sponsors during sprint reviews foster transparency and keep the project on track.
Selecting the Right MES Solution
Choosing the right MES solution is a critical step in the implementation process. Key factors to consider include specific manufacturing needs and integration capabilities. There are various MES options available, from canned solutions tailored for specific industries to configurable solutions that can be adapted to any industry.
Successfully integrating the MES solution requires a well-structured successful implementation plan with a clear timeline.
Evaluating MES Software Options
Evaluating MES software options ensures that the selected system aligns with specific manufacturing needs and objectives. The procurement process involves negotiating terms between customers, vendors, and integration companies, focusing on pricing and legal considerations.
Starting the procurement process early, even before finalizing the MES software vendor, can ensure a smooth transition.
Considering Integration with Existing Systems
Integrating with existing systems like ERP and SCADA is essential for seamless operation and effective data flow within an MES. A clear integration strategy ensures successful connection with existing systems, outlining technical solutions and processes. Middleware solutions can bridge compatibility gaps between MES and legacy systems, addressing significant challenges.
Legacy systems often pose significant integration challenges during MES implementation. A well-defined integration strategy can help manage these challenges, making the integration process less complex and time-intensive. Thoroughly outlining the new MES architecture, including technical solutions and integration processes, is crucial for successful integration.
Custom vs. Off-the-Shelf Solutions
Selecting an MES solution requires choosing between custom and off-the-shelf options. Custom MES solutions meet specific business needs, providing tailored functionalities that align closely with organizational requirements. They also offer better protection for sensitive business information compared to off-the-shelf products.
Building the Project Team
Building a competent project team is essential for leading MES implementation. This team oversees the entire project, from initial planning to final deployment and beyond.
Assembling the right team ensures that all aspects of the MES implementation are handled efficiently and effectively.
Assembling Key Stakeholders
Involving key stakeholders is vital for successful MES implementation. This includes anyone who uses or interacts with the MES system, such as line operators, shift supervisors, and upper management. Building internal teams within the end-customer’s organization fosters the strong collaboration necessary for project success.
In an Agile framework, stakeholders play a crucial role in providing feedback during sprint reviews. Involving stakeholders in these iterative checkpoints ensures that the MES solution aligns with evolving business needs.
Input from key stakeholders is vital for defining clear objectives and expectations for the MES.
Developing Necessary Competencies
Developing necessary competencies within the project team ensures all members understand their roles and responsibilities. Agile implementation requires cross-functional team members who understand both technical solutions and Agile principles. Agile coaches or Scrum Masters can help the team effectively adopt Agile practices.
Project Management Methodologies
Implementing MES in phases minimizes disruptions and allows for troubleshooting. Project management methodologies like PRINCE2 and Agile effectively guide projects. A phased rollout emphasizes gradual implementation, enhancing project management effectiveness.
Effective project management is crucial for MES implementation success. Breaking down the project into manageable phases helps companies handle implementation complexities. This approach also allows for continuous improvement and adaptation, ensuring the MES system meets evolving manufacturing needs.
Agile methodology, with its iterative approach, ensures continuous improvement and adaptability. The team should adopt frameworks like Scrum or Kanban to manage workflows, maintain transparency, and foster collaboration.
Implementation Phase
In the implementation phase, planning and preparation come to fruition. This phase involves budget allocation, resource planning, collaboration, communication, testing, and optimization to ensure successful mes implementation projects.
The timeline for MES implementation typically spans around 8 to 12 weeks, depending on the software’s complexity and the characteristics of the production line.
Budget Allocation and Resource Planning
Proper budget allocation is vital for successful MES implementation. This includes ongoing costs for support, maintenance, and renewals to accurately represent total costs.
Utilizing cloud solutions can reduce operational costs by eliminating the need for maintaining local servers.
Agile MES implementation allows manufacturers to distribute budgets incrementally. This phased approach ensures resources are allocated to the most critical functionalities first, reducing the risk of overspending on unnecessary features.
Collaboration and Communication
Effective collaboration and communication are vital for successful MES implementation. The Project Manager coordinates between departments and monitors implementation progress.
Establishing workflows and training staff are also vital for ensuring smooth collaboration during the implementation process.
Agile thrives on regular communication. Daily stand-ups, sprint planning meetings, and retrospective sessions foster collaboration and ensure alignment among cross-functional teams.
Testing and Optimization
Continuous testing and optimization are integral to Agile. Teams should test functionalities at the end of each sprint to ensure early detection and resolution of issues. Pilot projects can be treated as iterative sprints for maximum flexibility.
Automated systems for tracking downtime events accurately track downtime and minimize errors, aiding quality control. Industrial automation and control systems in MES implementation reduce manual tasks, optimize production schedules, and identify bottlenecks.
With MES, quality control information is transmitted immediately, allowing companies to stop production instantly upon identifying any issues.
Post-Implementation Activities
Post-implementation activities ensure that the MES system meets its intended objectives and delivers real benefits. These activities include ongoing support and maintenance, training and skill development, and data analysis for continuous improvement.
Maintaining quality and reliability of data is crucial, as poor data can lead to operational inefficiencies.
Ongoing Support and Maintenance
Continual support and maintenance are necessary for long-term MES success. Agile principles emphasize ongoing support and iterative updates. Post-implementation sprints can focus on refining the MES system, incorporating user feedback, and addressing newly identified requirements.
Ongoing support and effective change management are essential for sustained MES effectiveness and efficiency.
Training and Skill Development
Effective training plays a crucial role in MES implementation success. It significantly influences overall outcomes. Employees responsible for an MES system must possess knowledge and skills to utilize the system’s capabilities effectively. Training plans should consider the workload and daily responsibilities of the staff undergoing training.
Pre-testing the MES system can serve as an effective training tool for the staff.
Data Analysis and Continuous Improvement
Ongoing data analysis post-MES implementation identifies opportunities for further optimization and efficiency improvements. Data analysis allows organizations to spot areas for improvement, driving continuous manufacturing process improvement. AI-driven MES analytics provide deep insights, detect patterns, identify suspicious activity, and forecast changes.
Continuous improvement is fundamental to MES implementation, enabling manufacturers to stay competitive and adapt to evolving industry demands. Leveraging data analytics and AI helps manufacturers make informed decisions, enhancing production performance, quality management, and overall operational efficiency.
This ongoing process ensures the MES system remains a valuable asset over time.
Agile thrives on continuous improvement through retrospective analysis. Post-implementation reviews should include sprint retrospectives to analyze performance and identify opportunities for optimization.
Benefits of MES Implementation
Implementing an MES system offers numerous benefits, from enhanced production efficiency to real-time data access and improved quality control. Manufacturers adopting MES solutions typically experience significant improvements in operational efficiency, ranging from 15% to 20%.
The integration of IIoT and cloud-based MES platforms further enhances these benefits by enabling real-time monitoring and remote management of production processes.
Enhanced Production Efficiency
MES enhances production efficiency by generating real-time insights that lead to cost savings. Non-disruptive analysis and reporting capabilities optimize operations, maximize asset utilization, and reduce production costs. Integrating third-party solutions in MES implementation streamlines operations and enables cross-system data sharing.
Continuous monitoring and alerting for issues or unusual activities optimize manufacturing processes. AI helps identify hidden patterns and trend changes, contributing significantly to process optimization in MES.
Financial savings and increased employee morale are unexpected benefits companies might discover post-MES implementation.
Real-Time Data Access and Decision Making
Real-time data access is crucial in modern manufacturing, enabling immediate visibility into operations and swift responses to changes. Access to real-time data enhances decision-making by providing accurate and up-to-date information, allowing for better-informed and quicker decisions. Real-time insights facilitate rapid problem-solving, helping managers identify issues promptly and take corrective action without delay.
Integrating real-time data significantly improves operational effectiveness, reducing waste and increasing productivity. Real-time data access aids in monitoring key performance indicators (KPIs), allowing immediate adjustments to enhance productivity. This capability is valuable for maintaining high standards of operational efficiency and quality control.
Improved Quality Control
MES enables detailed tracking and traceability, vital for maintaining high product quality standards. MES provides detailed tracking of production processes, ensuring compliance with quality standards and facilitating smart manufacturing. Effective quality control is crucial for ensuring product consistency and customer satisfaction.
Overall, MES enhances quality control by providing data-driven insights and accountability throughout the manufacturing process. Real-time monitoring and control allow manufacturers to quickly address defects and improve overall equipment effectiveness, resulting in higher quality products and greater customer satisfaction.
Common Challenges and How to Overcome Them
Common challenges arise during MES implementation that must be addressed for successful integration, including managing change, technical integration issues, and ensuring user adoption.
Addressing these challenges is crucial to the overall success of MES implementation.
Managing Change
Securing executive sponsorship is crucial as it provides valuable momentum and support for overcoming resistance to change. Integration can improve collaboration between departments, fostering a better environment for change management.
Conducting an upfront cost analysis is vital to minimize unforeseen surprises from required changes during MES implementation.
Agile reduces resistance to change by delivering value in small, incremental improvements. Early successes in initial sprints can build trust and momentum across teams.
Technical Integration Issues
Integrating with existing systems like ERP and SCADA is critical for MES functionality. Custom integration increases complexity, development labor, and maintenance resources needed. Effective planning and resource allocation help manage integration complexity. Utilizing standardized interfaces and middleware can ease the process, making it more manageable and less resource-intensive.
Technical integration issues can pose significant challenges during MES implementation. Effective project management and resource allocation are crucial for addressing these issues and ensuring a smooth integration process. Leveraging advanced technologies and middleware solutions helps manufacturers overcome technical hurdles and achieve seamless integration with existing systems.
Agile’s iterative nature allows teams to address integration issues progressively. Middleware solutions and APIs can be tested and optimized over multiple sprints, minimizing risk.
Ensuring User Adoption
Agile encourages user involvement through iterative testing and feedback during sprint reviews. Regular engagement fosters ownership and ensures the system aligns with user needs.
Latest Trends in MES Implementation
The latest trends in MES implementation are driven by advancements in Industry 4.0, IIoT, and cloud-based solutions. These trends are transforming the manufacturing landscape, enabling smart manufacturing and enhancing the capabilities of MES systems. By staying informed about these trends, manufacturers can leverage new technologies to optimize their operations and gain a competitive edge.
Industrial Internet of Things (IIoT)
IIoT enhances MES capabilities and supports Industry 4.0 initiatives. The integration of IIoT within MES allows for improved data collection and analysis, essential for driving informed decision-making. IoT devices assist in automating warehouse management operations, enhancing efficiency and accuracy.
IIoT devices enable process automation and provide continuous control, leading to optimized manufacturing operations and manufacturing processes.
Cloud-Based MES Solutions
Cloud-based MES solutions are designed to enhance operational efficiency by leveraging the flexibility of cloud infrastructure. One key advantage of cloud-based MES solutions is seamless scalability, allowing manufacturers to adjust their resources based on current needs without significant downtime.
Cloud solutions provide enhanced security measures, protecting critical manufacturing data from potential threats and breaches. Remote accessibility granted by cloud-based MES systems enables users to monitor and manage operations from any location, providing flexibility for modern manufacturing demands.
Artificial Intelligence and Machine Learning
AI and ML integration in MES allows for better prediction of equipment failures and optimization of production schedules. AI in MES supports the automation of complex decision-making processes based on large datasets.
Machine learning algorithms in MES can provide timely insights that improve manufacturing efficiency and resource allocation. By leveraging AI and ML, manufacturers can enhance their MES systems’ capabilities and achieve greater operational efficiency.
If you've enjoyed this guide, check out our guide on LIMS Implementation.
Summary
In conclusion, implementing a Manufacturing Execution System (MES) is a multifaceted process that requires careful planning, collaboration, and execution. From identifying business objectives and conducting a pre-implementation analysis to selecting the right MES solution and building a competent project team, each step is crucial for ensuring a successful implementation. Post-implementation activities, such as ongoing support and data analysis, are essential for continuous improvement and maintaining the MES system’s effectiveness.
By understanding the benefits of MES implementation, such as enhanced production efficiency, real-time data access, and improved quality control, manufacturers can optimize their operations and stay competitive in the evolving industrial landscape. Embracing the latest trends, such as IIoT and cloud-based solutions, further enhances the capabilities of MES systems and drives digital transformation in manufacturing. We hope this guide provides valuable insights and practical steps to help you achieve a successful MES implementation.
Other Software Implementation Guides
Frequently Asked Questions
What is a Manufacturing Execution System (MES)?
A Manufacturing Execution System (MES) is vital for real-time monitoring and control of manufacturing processes, significantly improving operational performance. Implementing an MES enables manufacturers to optimize their production efficiency effectively.
Why is executive sponsorship important for MES implementation?
Executive sponsorship is essential for MES implementation as it secures the necessary resources and support from senior management, ensuring the project's success through strong backing.
What are the benefits of cloud-based MES solutions?
Cloud-based MES solutions provide seamless scalability, enhanced security, and remote accessibility, which significantly streamline manufacturing processes and adapt to evolving demands effectively.
How does MES improve quality control in manufacturing?
MES improves quality control in manufacturing by offering real-time monitoring, detailed tracking and traceability, and data-driven insights, which help maintain high product quality standards.
What are common challenges during MES implementation?
Managing change, technical integration issues, and ensuring user adoption are common challenges during MES implementation. Successfully addressing these challenges is essential for achieving a positive outcome.
Share this
You May Also Like
These Related Stories
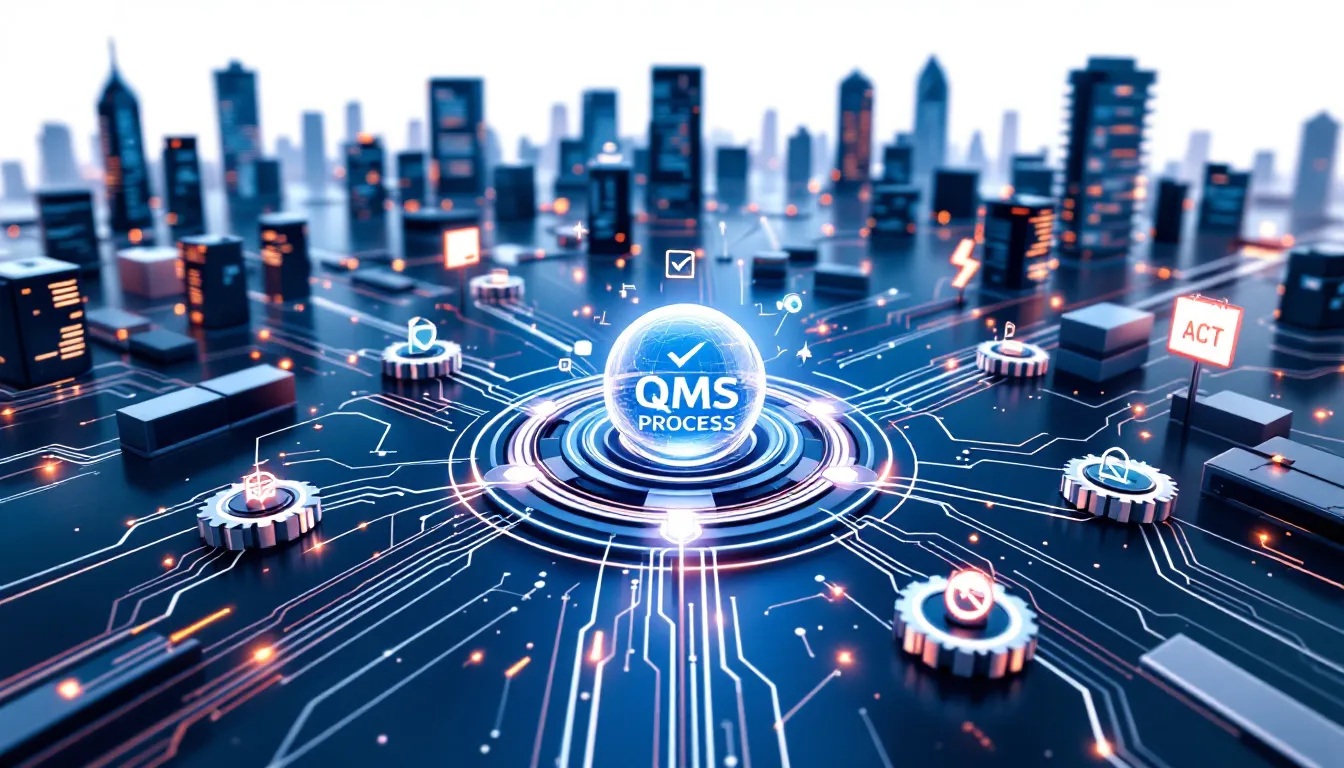
Top Strategies for Successful QMS Implementation
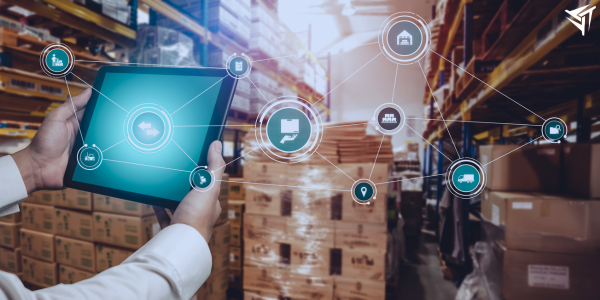
Best Practices for Manufacturing Systems Integration
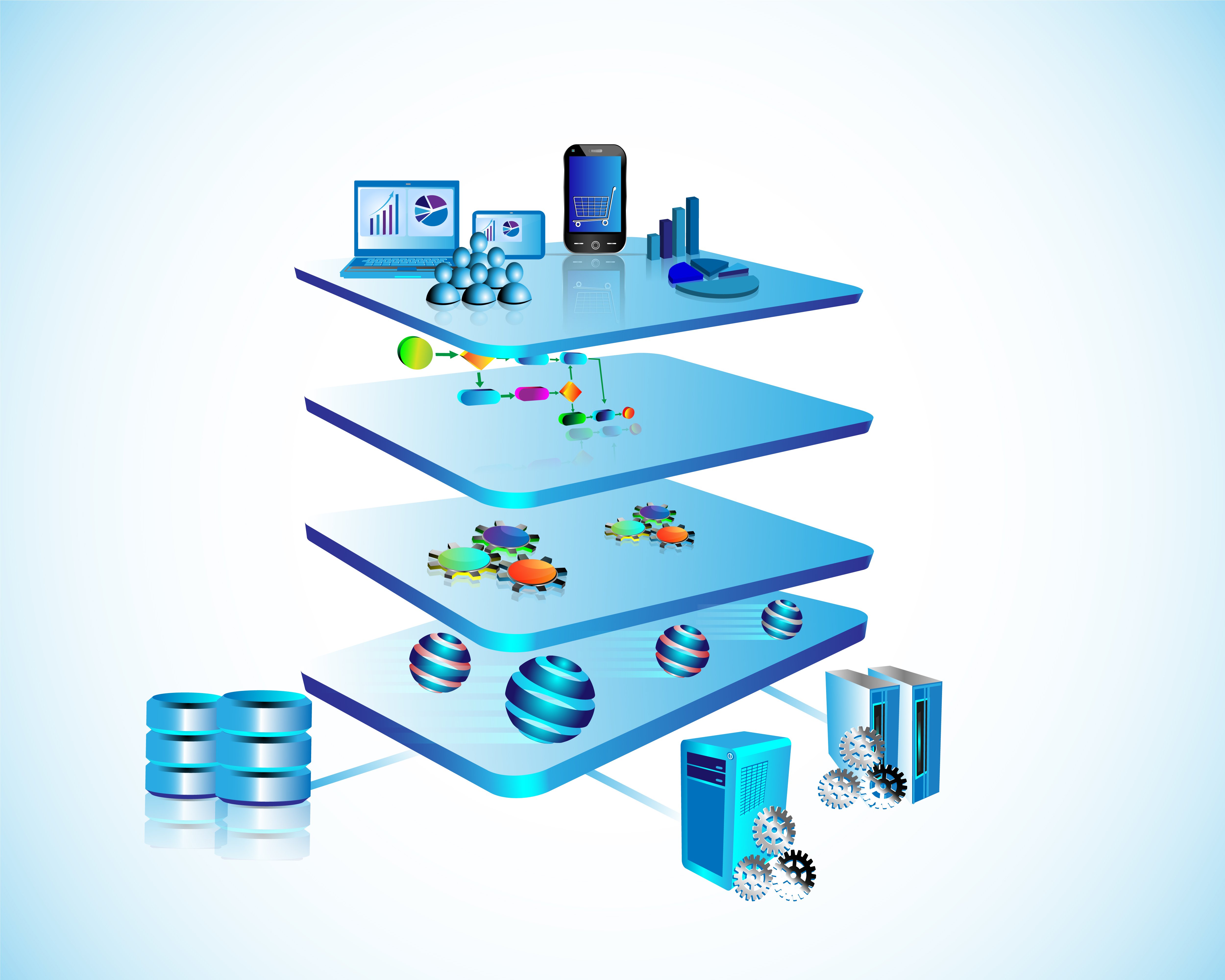
No Comments Yet
Let us know what you think