Scaling Production Processes for Small Business Manufacturers
Introduction
Scaling production processes is a crucial yet challenging step for small manufacturers and startups seeking sustainable growth. Transitioning from initial prototype or small-batch production to larger-scale manufacturing involves more than simply increasing output—it requires strategic foresight, precise optimization, and targeted investments.
This ultimate guide equips manufacturing professionals with essential insights and actionable strategies to scale effectively, achieve sustainable growth maintain high-quality standards, and enhance operational efficiency.
What Is Manufacturing Scalability?
Understanding the Fundamentals of Production Scalability
Manufacturing scalability in the manufacturing industry refers to the ability of a manufacturing operation to efficiently increase its production output without a proportional rise in associated costs.
Key characteristics include:
-
Efficient handling of increased production volumes.
-
Cost-effectiveness in maintaining profitability margins.
-
Consistency in product quality irrespective of volume.
-
Flexible responsiveness to market demands and customer needs.
Clearly defining the steps involved in scaling production processes is crucial to streamline operations, eliminate bottlenecks, and create action plans that contribute to overall efficiency and scalability. Anticipating growth through market trend forecasting aids in defining the level of scaling required for effective resource allocation.
A truly scalable manufacturing process leverages technology, robust quality control measures, optimized workflows, and flexible systems to ensure long-term growth and profitability.
Why Scalability Matters for Small Manufacturers and Startups
Scalability significantly influences the competitiveness and sustainability of small manufacturers and startups by:
-
Enabling cost reductions through economies of scale.
-
Improving response time to market changes and customer demands.
-
Providing flexibility in adapting production to new opportunities.
-
Enhancing resource utilization and minimizing waste.
-
Strengthening market positioning and growth potential.
Scalability also affects the reach of production capacity and timelines, particularly in meeting the growing market demands.
Without scalability, manufacturers risk stagnation, higher production costs, and diminished customer satisfaction.
Assessing Current Manufacturing Operations
Evaluating Your Production Capabilities
A comprehensive assessment of current operations and quality control measures provides clarity on existing capabilities and identifies opportunities for improvement. Critical evaluation areas include:
Workflow Efficiency
-
Analyze process flow to detect redundancies and inefficiencies.
-
Streamline operations to minimize bottlenecks and downtime by incorporating automation technologies. These technologies, including robotics and AI, can enhance efficiency, reduce downtime, and improve quality control, ensuring that your processes are optimized for better scalability.
Equipment Capacity Utilization
-
Assess whether existing equipment maximizes its operational potential by evaluating its production capacity.
-
Identify underutilized machinery and explore options for increasing output.
Labor Productivity
-
Evaluate worker performance metrics and productivity levels.
-
Identify training needs to enhance worker efficiency and adaptability. Performance monitoring systems offer data-driven feedback for continuous improvement, empowering employees to enhance their skills and contribute to overall operational efficiency.
Quality Control Effectiveness
-
Examine current quality assurance protocols and their efficacy.
-
Implement measures to maintain consistent quality standards as production scales. Neglecting scalability in quality assurance can result in increased defect rates and production inefficiencies. Statistical process control (SPC) methods identify variation patterns, allowing for timely corrective actions.
Space Utilization
-
Optimize factory layout to ensure maximum efficiency and workflow.
-
Plan for scalable expansion and efficient space management.
Identifying Common Production Bottlenecks
Common production bottlenecks frequently experienced by small manufacturers include:
-
Equipment limitations and breakdowns.
-
Skill gaps and labor shortages.
-
Inefficient or redundant processes.
-
Limited production space.
-
Supply chain vulnerabilities.
Identifying these bottlenecks early is crucial for addressing them proactively during scaling. Additionally, scalable manufacturing operations can efficiently adjust to market fluctuations and demand variability, ensuring quality and cost management while handling growth spurts and changing market conditions.
Strategic Planning for Manufacturing Growth
Establishing Clear Objectives and Metrics
Clear, measurable objectives form the cornerstone of successful scaling. This involves:
Defining SMART Goals for Scalability
SMART (Specific, Measurable, Achievable, Relevant, Time-bound) goals align scaling efforts with a well-defined strategy for achieving operational growth and efficiency in manufacturing, ensuring clarity and practicality.
Key Performance Indicators (KPIs) for Manufacturing Growth
Critical KPIs include:
-
Production throughput and volume.
-
Efficiency rates and cycle times.
-
Quality rates and defect frequencies.
-
Cost per unit produced.
-
Resource utilization metrics.
These KPIs facilitate informed decision-making and ongoing assessment of scaling effectiveness.
Developing a Phased Scaling Approach
Benefits of Incremental Scaling
-
Allows for manageable growth without overwhelming resources.
-
Reduces risk by enabling adjustments based on real-time feedback.
-
Ensures alignment between production capabilities and market demand.
Step-by-Step Method for Gradual Expansion
-
Optimize existing processes before expansion. Embracing new ideas can help businesses adapt and thrive by optimizing these processes effectively.
-
Implement automation selectively in critical processes.
-
Gradually scale production volumes and product lines.
-
Continuously evaluate outcomes and adjust strategies accordingly.
Balancing Quality, Cost, and Production Volume
Maintaining Quality Control at Scale
Strategies for Consistent Quality Assurance
Implementing robust quality control systems that are designed to scale with your operations is essential for ensuring quality control. These systems should be capable of adapting to higher production volumes without compromising accuracy or reliability. Automated inspection systems improve defect detection rates and maintain consistent quality during production scaling.
Equally important is training employees thoroughly on standardized quality procedures. A well-trained team ensures that quality expectations are upheld consistently, even as output increases. Automated quality control measures detect defects early in the production cycle, reducing waste and improving overall product quality.
Maintaining real-time visibility into quality metrics enables you to detect and address deviations quickly. Swift corrective action minimizes the impact of defects and keeps processes on track.
Continuous process improvement and statistical process control should be embedded in your operations. Regularly refining and optimizing procedures helps sustain high-quality output as your production scales.
Cost-Efficiency in Scalable Production
Managing Costs During Growth Phases
Start by identifying and eliminating activities that don’t add value. Streamlining operations in this way reduces waste and enhances overall efficiency.
Integrating automation and supply chain management software into key stages of production can significantly lower labor and overhead costs. Automation not only boosts throughput but also supports consistency and reliability.
Using predictive analytics can improve your decision-making around operations and inventory. Anticipating demand patterns and production needs helps you avoid overstocking or underproduction.
Finally, consider the long-term financial impact of investing in additional manufacturing space, new processes, equipment, and employee training. Thoughtful, strategic spending in these areas often yields sustainable growth and a strong return on investment. Investing in advanced manufacturing space may be necessary for physical capacity expansion.
Optimizing Volume Without Overextending Resources
-
Plan and project resource requirements meticulously.
-
Employ flexible manufacturing systems to adjust rapidly to volume changes.
-
Regularly review operational performance to ensure optimal resource allocation.
This structured and detailed approach will help small manufacturers and startups successfully navigate the complexities of scaling production, ensuring sustainable and efficient growth.
Optimizing Manufacturing Processes
Standardizing Processes and Documentation
Creating Robust Standard Operating Procedures (SOPs)
-
Document precise, detailed instructions for consistent operational execution.
-
Regularly review and update SOPs to reflect process enhancements and regulatory changes.
-
Utilize visual aids and easy-to-access digital formats to improve clarity and adherence. Documenting standard operating procedures (SOPs) preserves best practices and ensures consistency as operations scale.
Implementing Lean Manufacturing Principles
Key Lean Concepts
-
Kaizen: Continuous incremental improvements to eliminate waste and enhance efficiency.
-
Just-in-Time (JIT): Minimize inventory and reduce waste through timely production aligned with demand.
-
Poka-yoke: Implement error-proofing mechanisms to reduce defects and improve overall product quality. Similar to the meticulous process of baking, where specific ingredients must be precisely combined to achieve the perfect cake, each step in manufacturing must be executed with careful consideration to maintain quality and efficiency.
Regular Process Auditing and Continuous Improvement
How to Establish an Ongoing Improvement Culture
-
Schedule regular audits to identify inefficiencies and improvement opportunities.
-
Encourage employee involvement in suggesting process improvements.
-
Establish clear communication channels to facilitate rapid implementation of corrective actions.
Leveraging Technology and Automation
Stages of Automation Adoption
Manual Workstations
Human-centric, minimal automation, suitable for flexible, low-volume production. This stage relies on a skilled and adaptable workforce for nearly every task, making it ideal for prototyping, custom jobs, or early-stage startups. While cost-effective initially, it can limit scalability and consistency over time.
Manumation: Partial Automation
Combination of manual and automated tasks to enhance efficiency without significant capital expenditure. Manumation allows manufacturers to streamline repetitive or physically demanding tasks while retaining human oversight for quality and decision-making. It’s often a practical middle ground that enables measurable productivity gains with modest investments.
Islands of Automation
Independent automated systems addressing specific production tasks for incremental improvements. These isolated units—such as automated packaging, inspection, or machining stations—help reduce cycle times and errors in key bottlenecks. Islands of automation can be integrated gradually, allowing companies to test automation’s ROI before scaling further.
Fully Integrated Automated Production Lines
Comprehensive automation with minimal human intervention, maximizing throughput and consistency. The efficiencies gained through advanced technology in mass production further enhance these benefits, ensuring high levels of standardization and quality control.
Selecting the Right Technology Investments
Choosing the right technologies for supply chain management is critical for sustainable growth. Businesses should focus on solutions that align with both short-term operational goals and long-term scalability.
Key Considerations for Scalable Technology Choices
-
Scalability and adaptability of technologies to future needs.
-
Ease of integration with existing processes and systems.
-
Cost-effectiveness and achievable ROI.
Make sure technologies can grow with your production demands and support modular upgrades. Prioritize platforms with strong vendor support and active development roadmaps.
Digital Transformation Opportunities
Digital transformation isn't just a buzzword—it’s a competitive necessity for manufacturers aiming to improve their scaling process efficiently. Embracing digital tools can unlock new levels of productivity, insight, and agility.
Role of AI, IoT, Robotics, and Data Analytics in Scaling
-
Enhance decision-making with predictive analytics and real-time data.
-
Automate repetitive tasks and optimize operational efficiencies with robotics.
-
Use IoT technologies for real-time tracking and management.
-
Stay current with technological advancements to enhance decision-making and operational efficiency.
Together, these technologies create a data-rich, responsive environment where scaling becomes more proactive and less reactive. They also support continuous improvement by uncovering patterns and opportunities invisible to the human eye.
Benefits of Digital Twins and Cloud Computing
-
Digital twins enable accurate process simulations and proactive problem-solving.
-
Cloud computing provides scalable data storage and analytics capabilities, reducing infrastructure costs.
These technologies enable remote collaboration, rapid prototyping, and greater system transparency while ensuring consistent product quality. By mirroring real-world processes digitally, manufacturers can test changes and predict outcomes without interrupting production. Smart manufacturing combines real-time data analysis with automated systems to enhance production capabilities.
Manufacturing Operations Management (MOM) Software Integration
Understanding MOM Systems
Core Functions: Production Planning, Execution, Quality, Logistics
Manufacturing Operations Management (MOM) software provides a unified digital platform designed to streamline and optimize your entire manufacturing lifecycle—from initial production planning and real-time execution through rigorous quality control and logistics management.
By integrating various processes, MOM ensures seamless collaboration between departments, enabling smooth and efficient operations.
How MOM Enhances Scalability
Real-Time Data Utilization
MOM software leverages real-time data and advanced analytics, empowering manufacturers with immediate insights for rapid, informed decision-making. This capability significantly enhances operational responsiveness, facilitating process optimization that drives scalability and sustainable growth. Having comprehensive and actionable information is crucial for improving manufacturing effectiveness and the ability to scale operations.
Comprehensive Operational Visibility
The software offers a holistic view of your entire production environment, making it easy to quickly identify bottlenecks, inefficiencies, and opportunities for improvement. Such comprehensive operational visibility ensures that manufacturers can boost efficiency and scale production smoothly, efficiently addressing challenges before they escalate.
Key Features and Benefits of MOM Software
Shop Floor Monitoring and Control
With our MOM software solution, shop floor operations are continuously monitored in real-time, offering precise tracking of production activities without the need for manual data inputs. This immediate visibility supports agile decision-making and significantly improves operational responsiveness.
Performance Analytics and Reporting
Snic Solutions integrates predictive analytics within its MOM platform, including material handling, aggregating data from production, quality, and inventory management systems. These insights provide actionable intelligence to strategically guide continuous improvement initiatives, optimizing overall manufacturing performance.
Inventory and Materials Management
The software efficiently tracks raw materials, components, and finished products, ensuring robust inventory management and enhanced supply chain visibility. Integrated software systems enable real-time supply chain monitoring, facilitating proactive issue resolution and accurate inventory tracking. Timely procurement minimizes waste, prevents production delays due to material shortages, and contributes to maintaining lean, cost-effective operations.
Integration of MOM with MES, ERP, APS, and QMS
Our MOM software solutions seamlessly integrate with critical manufacturing systems such as Manufacturing Execution Systems (MES), Enterprise Resource Planning (ERP), Advanced Planning and Scheduling (APS), and Quality Management Systems (QMS).
This integration ensures uninterrupted data flow across departments, real-time coordination, and consistency throughout production planning, execution, quality assurance, and logistics management.
Human Resources and Organizational Development
Employee Training and Skill Development
Essential Training Programs for Scalable Manufacturing
-
Technical skills training for advanced machinery and automation.
-
Continuous education in lean principles and quality management.
-
Attracting and retaining top talent is a crucial factor for the success and scalability of manufacturing businesses. Establishing clear career development paths helps maintain employee engagement and motivation during periods of expansion.
Building an Adaptable Workforce
Cross-Training and Flexible Staffing Models
-
Cross-train employees to enhance adaptability and reduce labor shortages.
-
Employ flexible staffing solutions to match production demands dynamically.
Fostering Cross-Functional Collaboration
Breaking Down Departmental Silos
-
Implement integrated communication tools and regular interdisciplinary meetings.
-
Establish shared goals and collaborative problem-solving frameworks.
Supply Chain Strategies for Scaling
Building a Resilient Supply Chain
Diversifying Suppliers and Risk Mitigation
-
Establish relationships with multiple suppliers to mitigate supply chain disruptions.
-
Regularly assess supplier performance and diversify sourcing strategies.
-
Plan for potential disruptions during supply chain transitions to ensure smooth operations and maintain production efficiency. Comprehensive supplier assessments are vital for effective supply chain management during scaling.
Visibility and Predictive Analytics for Supply Chains
-
Implement supply chain visibility tools to track inventory and logistics in real-time.
-
Leverage predictive analytics to anticipate disruptions and manage inventory proactively.
Effective Supplier Relationship Management
Collaborative Forecasting and Vendor Partnerships
-
Engage in collaborative forecasting with key suppliers to align production and inventory management.
-
Foster long-term vendor partnerships through clear communication and mutually beneficial agreements.
Inventory Management During Scaling
Strategic Inventory Techniques
-
Adopt Kanban systems for visual inventory management and replenishment.
-
Utilize Just-in-Time (JIT) inventory practices to minimize waste and reduce inventory costs.
Overcoming Common Scaling Challenges
Navigating Skilled Labor Shortages
-
Develop comprehensive training and apprenticeship programs to cultivate a skilled workforce.
-
Partner with educational institutions for continuous skill development and recruitment.
Mitigating Financial Risks and Managing Cash Flow
-
Perform thorough financial forecasting to anticipate funding requirements and manage expenditures carefully.
-
Implement strong cash flow management practices, including rigorous budget monitoring.
-
Monitor profit margins to ensure that growth efforts are sustainable and positively impact the bottom line.
Ensuring Operational Efficiency
-
Continuously evaluate and streamline manufacturing processes to reduce operational inefficiencies.
-
Implement automation and technology solutions to enhance productivity and reduce manual tasks.
-
Track defect rates as a critical key performance indicator when scaling production operations. Monitoring defect rates provides valuable insights into product quality and operational effectiveness, aligning with overall business objectives such as improving quality and increasing customer satisfaction.
Technology Adoption and Cybersecurity
-
Invest in secure, scalable technologies that meet current and future manufacturing needs.
-
Develop robust cybersecurity strategies to protect sensitive manufacturing data.
Meeting Evolving Customer Expectations
-
Stay agile by regularly engaging customers for feedback and adapting product offerings accordingly.
-
Implement flexible manufacturing systems capable of quick adaptation to customer demands.
Navigating Regulatory Compliance Issues
-
Regularly review and comply with relevant manufacturing regulations and standards.
-
Maintain thorough documentation and implement comprehensive compliance management systems.
Scaling Insights from Industry Leaders
Tesla: Speed and Vertical Ambition
Tesla’s Shanghai Gigafactory, built in 10 months, exemplifies scaling through:
-
Radical Vertical Integration: Controlling 70% of battery production (vs. 10% for legacy automakers) reduced supply chain vulnerabilities during 2022’s lithium shortages (Trefis).
-
Iterative Automation: While trailing Toyota in assembly automation, Tesla’s “Gigapress” die-casting machines consolidated 171 parts into 2, cutting Model Y production time by 30% (Trefis).
-
Capacity Buffering: Maintaining 20% excess capacity at Fremont allowed rapid Model 3 output hikes when European demand spiked (Trefis).
However, Tesla’s $22B+ scaling costs (2019–2023) highlight risks small manufacturers mitigate through phased investments (Trefis).
Apple: Supply Chain Choreography
Apple’s supply chain mastery, responsible for 92% on-time delivery rates, relies on:
-
Co-Developed Innovation: Joint investments with TSMC secured exclusive early access to 3nm chips, enabling 20% faster iPhone 15 Pro performance versus Android rivals (Disfold).
-
Dynamic Sourcing: During 2021’s global chip shortage, Apple’s diversified supplier network and prepaid capacity reservations maintained 85% production targets while competitors faced 40% shortfalls (Disfold).
-
Demand-Shaping Inventory: Holding 45–60 days of premium component stock lets Apple launch products globally—a tactic smaller firms adapt through consignment agreements with local distributors (Disfold).
Frequently Asked Questions (FAQs)
How Can MOM Software Drive Lean Manufacturing and Six Sigma Initiatives?
MOM software facilitates real-time data tracking and analysis, supporting Lean and Six Sigma methodologies by identifying inefficiencies and enabling continuous improvement.
How Do You Measure Overall Equipment Effectiveness (OEE) at Scale?
OEE is measured by assessing equipment availability, performance efficiency, and product quality, enabling manufacturers to identify and address productivity losses effectively.
What's the Difference Between MES and MOM Software?
MES focuses specifically on real-time monitoring of manufacturing processes, whereas MOM encompasses broader functionalities including planning, scheduling, quality management, and logistics.
What Role Does Industry 4.0 Play in Scaling Production?
Industry 4.0 integrates advanced technologies such as IoT, AI, robotics, and big data analytics, significantly enhancing operational efficiency, flexibility, and scalability.
How Do Small Manufacturers Begin Digital Transformation?
Small manufacturers initiate digital transformation by identifying key areas for technological improvement, selecting scalable technologies, and gradually integrating digital solutions into existing processes.
Share this
You May Also Like
These Related Stories
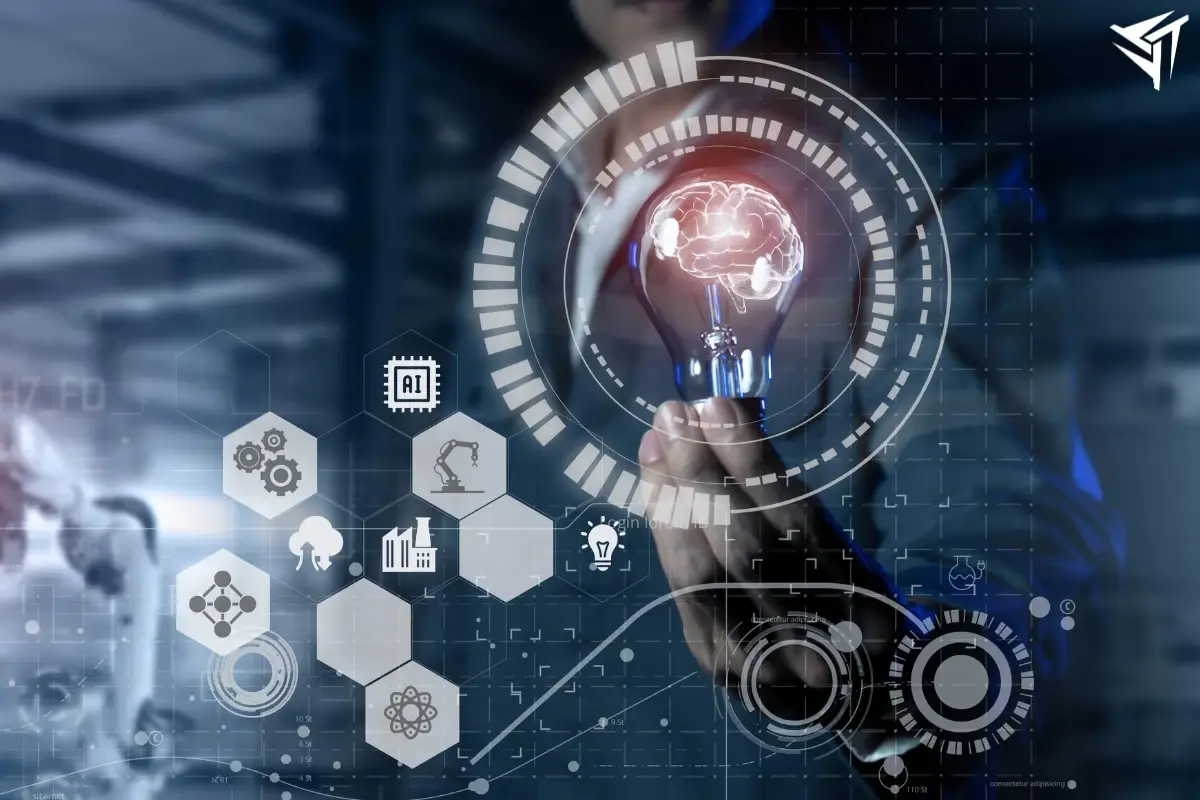
MOM Software for Lighting Manufacturers
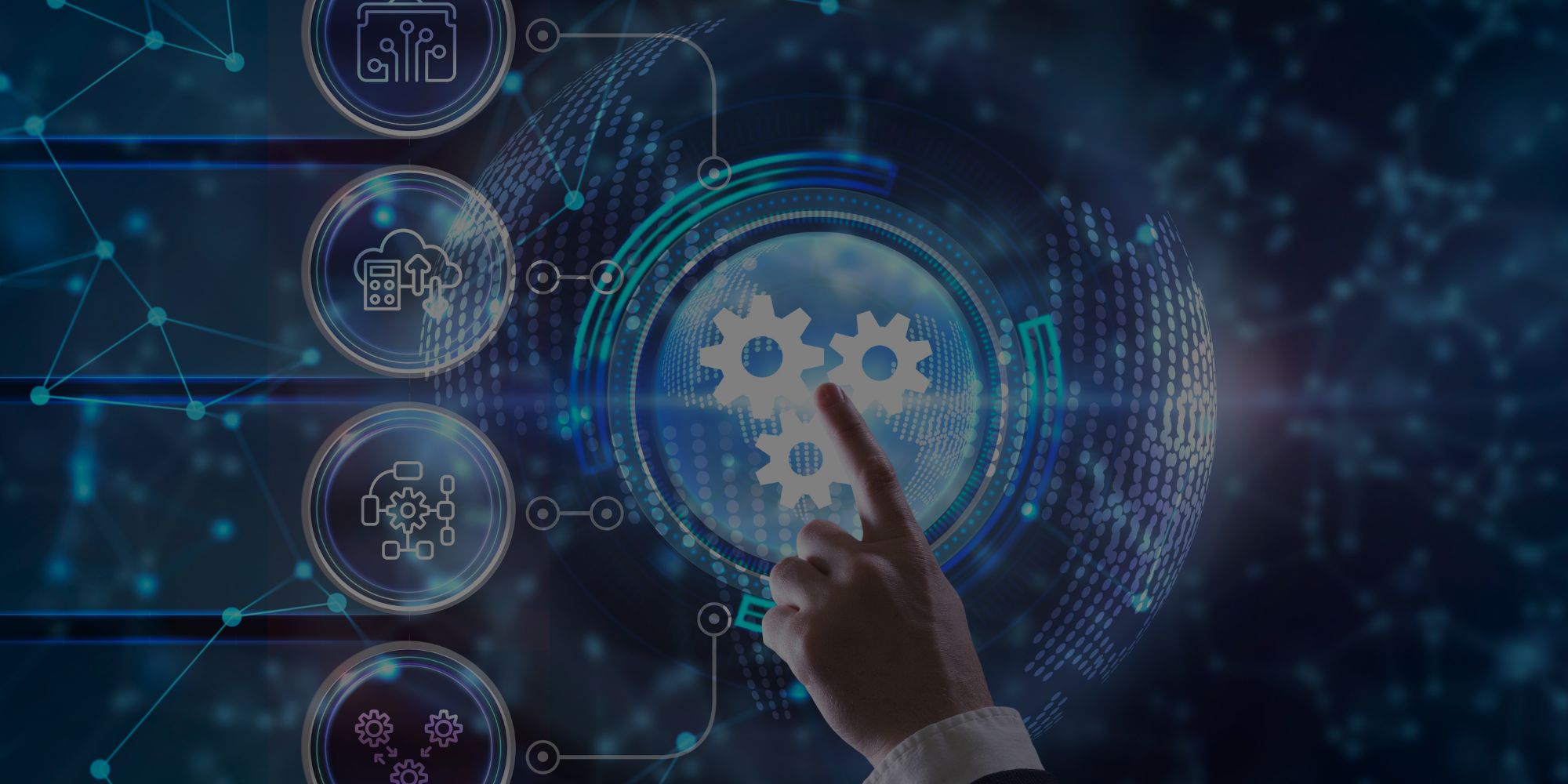
Manufacturing Operations Technology is Changing the Modern Factory
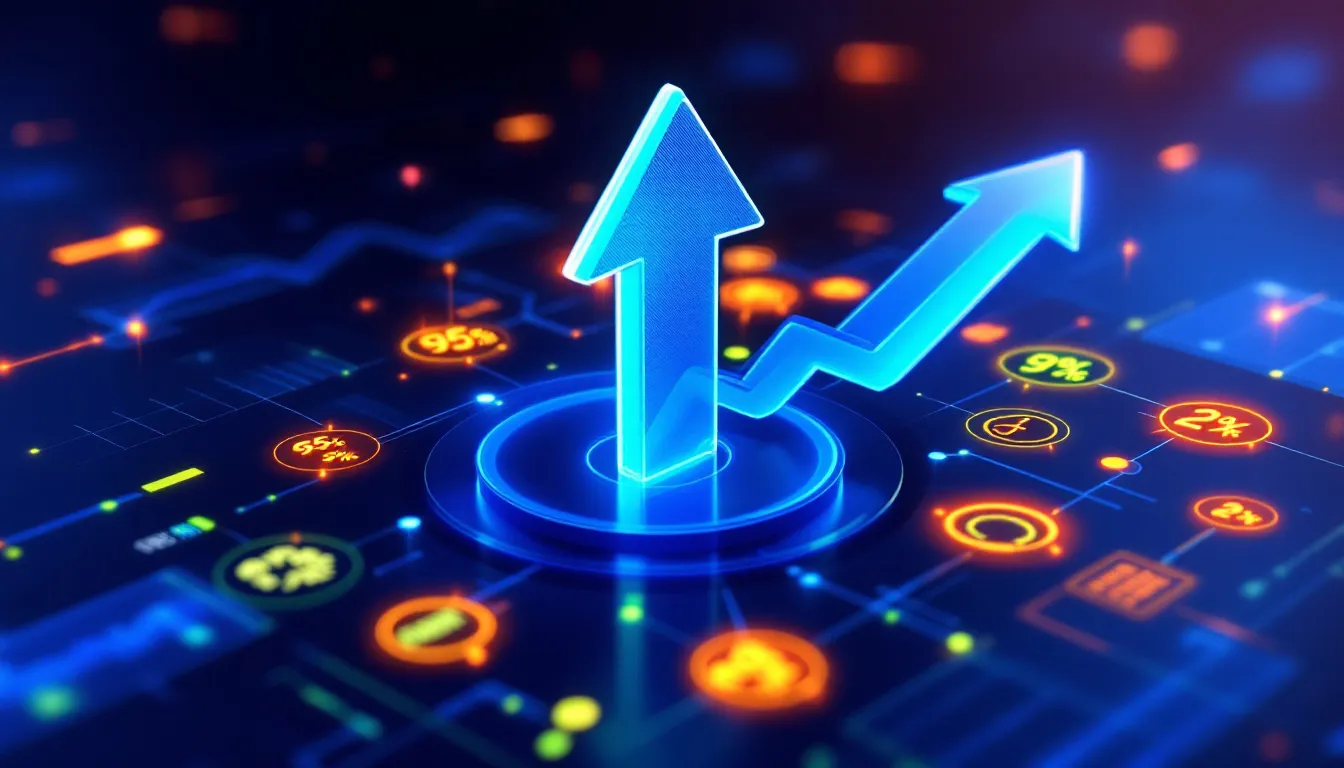
No Comments Yet
Let us know what you think