Why Lighting Manufacturers Need Flexible Manufacturing Operations Management Systems
Trends like smart lighting and human-centric lighting are pushing lighting companies to design, manufacture, and ship an increased number of product variants. This growing demand for custom lighting products is resulting in smaller batch sizes and rising production costs across the industry.
Traditional & Legacy MOM/MES
A traditional Manufacturing Operations Management (MOM) or Manufacturing Execution System (MES) is typically a homegrown or custom-built solution provided by an automation vendor, machine builder, or a bespoke software development company. A legacy MES connects directly to machines or a SCADA (Supervisory Control and Data Acquisition) system, offering manufacturing professionals—such as operators—visibility into the shop floor's real-time activities. Production control elements like machine utilization, availability, Andon status, and parts per hour are commonly visible in these traditional MES systems. However, even with modernization to cloud-native SaaS (Software-as-a-Service) options, these systems remain rigid, offering limited flexibility for making quick adjustments or changes on the fly.
Modern Flexible MOM/MES
A Manufacturing Operations Management (MOM) system, also known as MOM/MES, is a more modern software platform designed to help manufacturers configure and model their operations, adapting to changing business needs. Unlike traditional systems, a modern MOM/MES integrates not only with machines but also connects physical resources like sensors and people to critical IT business applications such as ERP, PLM, MCS, and CMMS systems. This system provides the capability to manage, sequence, track, trace, control, and audit every product manufactured on a single platform. By breaking down departmental silos, a modern MOM/MES fosters greater collaboration across all functions within a factory, enhancing efficiency and flexibility.
Trends in the Lighting Industry
New products are being designed by lighting manufacturers at a much faster pace than ever, which helps reduce waste . Demanding factories to reduce their lead times for new product introduction and delivery while being cost effective.
Increase in human-centric lighting products
The kind of lighting in our environment influences our physical and emotional state, refines the space, and alters how architecture is perceived. Dim and slight flickering of old fluorescent lamps can lead to corrosive concentration and unrest, whereas spaces with the best lighting evoke positive emotions of happiness and enthusiasm.
As architects, designers, and builders understand light’s effects on humans, they are increasingly adopting human-centric lighting to help people become more efficient and productive. Whether it’s healthcare, workspaces, or education centers, LED-based human-centric lighting (HCL) has powerful applications that can help improve productivity .
Increase in special purpose lighting products for indoor farming and automobiles
The global food system accounts for a quarter of the world’s greenhouse gas emissions. Besides, the expansion of metropolitan hubs is gradually reducing arable lands, creating the need for more alternative farming practices such as vertical and indoor farming. Increased efforts towards sustainable agriculture have led to increased indoor farming adoption that utilizes less energy, water, and land than traditional farming methods.
Using artificial LED lights in horticulture, farmers can either supplement natural daylight or replace it entirely to produce a wealth of benefits, such as the ability to fine-tune quality and increase yield.
LED lights continue to mark their entry into the automotive industry due to their benefits, such as enhanced brightness, which facilitates safer driving. Automobile manufacturers are incorporating intelligence into their lighting systems and leveraging advanced technology like Adaptive Driving Beam for improved safety of drivers. Digitalization of cars is driving the megatrend of Advanced Front Lighting Systems that introduce new approaches to safety, comfort, and communication capabilities and put great emphasis on exterior lighting.
New Product Innovations with IoT-Based Smart Lights
The manner in which light is produced and delivered has made incremental improvements. As business owners and facility managers are becoming more conscious of the economical, convenient, and safe use of energy, they are implementing some type of lighting control system as a part of the building management system (BMS). The smart lighting system helps managers create a set schedule for the lights to save energy and reduce costs.
LED bulbs are at the center of intelligent lighting strategy as they use up to 75% less energy than incandescent bulbs, last 25 times longer, and produce better quality light. The smart LED bulbs consist of software that connects to an application or smart home assistant or other accessories, which gives one the flexibility to control the lights remotely, eliminating the use of traditional switches. With the rising penetration of connectivity such as cameras, audio equipment, thermostats, or home assistants, the use of smart lighting systems is set to increase in the coming years.
New Market Innovations with LED as a Wi-Fi Communication Device (Li-Fi)
LiFi is a novel lighting technology that ensures high-speed, bi-directional, and wireless data communication faster than conventional Wi-Fi internet connectivity. LED capabilities with IoT connectivity enable design engineers to simultaneously provide illumination and transmit data.
Integrating LiFi into the LED lighting world creates an alternate path for internet connectivity in commercial spaces and offices. While Wi-Fi uses radio waves for data transmissions, LiFi uses infrared, ultraviolet, and visible light waves, providing high-quality transmission speeds up to >30Mbps. Besides, the data can be stored anywhere there is LED light, which also applies to streetlamps that can be used as LiFi hotspots.
LiFi solutions are expected to witness growth in the years owing to their greater efficacy and the advent of machine-type communication (MTC). As governments are increasingly taking initiatives in the ICT sector to improve the functioning of the electricity grid and optimize the efficiency of city operations, the market players are forced to invest and innovate in LiFi.
The Role of Manufacturing Operations Management (MOM) Systems
MOM creates a digital foundation for enabling enforceable, proactive, and paperless manufacturing. It identifies, analyzes, and prevents errors, integrating advanced planning and scheduling as well as manufacturing intelligence capabilities to create the most efficient production environment possible. It is built for manufacturers who want one system to optimize their entire factory and provides capabilities that can help increase productivity, reduce loss, and lower production costs.
Manufacturing Operations Management (MOM) enables organizations to analyze and generate accurate schedules that consider constraints around resources like people, machines, tooling, and materials. Manufacturers are then able to ensure they obtain the best use of their available capacity to deliver to customers on-time and in the most cost-effective way, with reduced production costs.
Five Key Capabilities of MOM for Lighting Manufacturers
-
Orchestration – MOM provides the orchestration and planning of manufacturing and quality operations.
-
Vertical integration – MOM bridges the gap between enterprise systems and shop floor automation.
-
Genealogy – MOM automatically generates the electronic records using e-signature, supporting more rapid compliance processes.
-
Digital twin – MOM implements the comprehensive digital twin of the physical production realm, creating a digital representation of the manufacturing process.
-
Analytics – MOM transforms big data into IoT actionable information (smart data) and provides continuous improvement and innovation intelligence.
A 360˚ View of Production
MOM/MES Use Cases in the Lighting Industry
Given the complexity of both products and the increasing regulatory environment, MOM/MES capabilities are essential for any lighting manufacturer—from large enterprises to SMBs. The lighting industry use cases provide an understanding of the benefits MOM/MES and effective supply chain management can bring to a lighting manufacturer.
Remove silo systems from the factory
The lighting industry uses highly automated machines like SMT machines to make the PCBs, and depending on the type of lighting manufactured, box-build assembly operations could be manual or automated. Legacy MES systems have primarily existed on the SMT lines with barcode systems or spreadsheets in downstream operations. Integration of MOM/MES to the ERP and to the automation layer that collects data from PLCs, sensors, and barcode systems removes multiple master maintenance and possibilities for data duplication. This is a foundational use case in starting a digital transformation journey.
Split production orders into batches
Production in reality never flows in the same way a production order is defined. 10,000 LED lights may be one production order in the ERP, flows as a batch of 2,000 units but is actually produced in lots of 500. This unit of measure changes across the production process, but there is additional complexity when it comes to traceability. For genealogy, this unit of measure has to extend until lot size 1 to achieve single-piece flow traceability. MOM/MES is capable of defining such complex containers of the unit of measure to create an audit trail that is compliant during recalls, rework, or rejections.
Production Scheduling
Sequencing traditionally has been left to production supervisors based on a dispatch plan for each supervisor who is tasked with maximum capacity utilization in their own area. SMT machine departments in the lighting industry set up each department as a mini factory. PCB manufacturing machines will produce to serve a Kanban supermarket, and box build assemblies based on the dispatch plan consume from the supermarket. MOM/MES provides the ability to publish a production schedule for all departments considering material availability, manufacturing constraints, and dispatch plan dates. Planned schedule vs. actual can provide insights into profitability through metrics like schedule attainment, the impact of rush orders on delays, and overall capacity utilization.
Material Management
This capability provides full visibility into the movement and consumption of materials across the factory. Material management is critical for factory productivity, tracking the use of materials, evaluating production line capacity, and replenishing material as needed.
Self-auditing Electronic Batch Records (eBR)
Electronic batch records are paperless electronic systems in the MOM/MES that enforce production processes and capture all information associated with as-built production records. The self-auditing nature of electronic batch records (eBR) refers to its capability to error-proof and provide real-time visibility to produce consistent product quality. Should product quality issues arise, eBR can quickly contain suspect products—either in process or in the field—to take action to address the issue.
Tracking-and-Tracing
Tracking the status of production and the disposition of work creates the foundation for the eBR. Status information on qualified personnel, component materials, production conditions, alarms, rework, or other exceptions related to the product (essentially the as-built record) is tracked in the system. This detailed production information enables forward and backward traceability of components and their use in each end product.
Sample Data Collection
MOM/MES data collection and acquisition capabilities track the real-time status of production equipment and processes as part of the production history. This capability saves time and prevents errors due to manual processes, maximizing productivity while building quality into your products.
In-line Statistical Process Control (SPC)
Manufacturers can solve production problems before they decrease quality, yield, or throughput by using live production information. Operators view real-time charts that provide immediate feedback, and engineers can review historical charts when analyzing specific events. Leveraging industry-standard statistical analysis tools makes it possible to recognize adverse trends before they lead to poor quality.
Nonconformance Management
MOM/MES improves quality consistency by adhering to global quality policies and orchestrating quality operations. When deviations are detected, nonconformance management software provide exception management and enforce protocols to correct the non-conformance. All collected data on the shop floor can be reused to initiate a problem-solving process (CAPA) by supporting root cause analysis, identifying the proper CAPA, and initiating the change management process. This enables the changes to be distributed to all stakeholders in the loop so that the product development process continuously improves. This focus on prevention further reduces the cost of quality, streamlines compliance, and reduces regulatory and product risk.
Electronic Work Instructions (EWI)
Comprehensive manufacturing work instructions are provided for the shop floor to create clear process steps. As a result, most of the current work instructions are instantaneously available where they need to be. Process documentation is automatically updated with revision management, enforcing changes quickly and easily.
Electronic Kanban (eKanban)
eKanban allows manufacturers to efficiently manage their inventory locations and properly replenish support material. eKanban helps control the flow of consumable materials on the manufacturing floor, supports lean manufacturing, and provides automatic consumption of materials per product bill-of-materials (BOM). Multiple manufacturing process styles are supported, from discrete to batch processes. Given the growing and hybrid nature of the lighting industry, this cross-functional support is critical.
Maintenance Management
Track equipment usage and manage preventive and corrective maintenance and calibration activities. It enables you to automatically detect conditions that necessitate maintenance to keep equipment performing at peak efficiency. It enables you to define and track resource-centric maintenance requirements based on the calendar date, usage time, and throughput. After maintenance or calibration, requirements are assigned to resources (enforcement occurs during manufacturing).
Training and Certification Management
Establish manufacturing roles, define training requirements for various roles and process certification requirements, maintain training records, and establish certification expirations. This eliminates errors due to expired training and makes sure you are not at risk for processing issues and non-compliance.
About Snic Solutions
Snic Solutions is a global digital transformation technology provider focused on manufacturing operations management (MOM) systems to accelerate Industry 4.0 adoption in manufacturing organizations.
Snic focuses on its expertise in MOM/MES and Advanced Planning & Scheduling (APS) systems and brings in Supply Chain Planning (SCP), Enterprise Resource Planning (ERP), Product Lifecycle Management (PLM), and Industrial Automation partners to take up end-to-end IT-OT transformation projects.
For high-mix high/low-volume manufacturing enterprises globally, Snic goes to market using “Opcenter MO” and is an expert partner to Siemens Digital Industries Software for Opcenter MES and Opcenter APS.
For automotive Tier I and II suppliers in India, Snic goes to market with “Plex” MOM software from Rockwell Automation.
A combination of manufacturing domain knowledge, production know-how, software implementation services, and the ability to build industry-specific accelerators makes Snic Solutions the go-to partner of manufacturing organizations across the globe.
With customers in over 12 countries across six continents, Snic Solutions offers guidance and support every step of the way as a trusted advisor.
Why Light Industry Manufacturers are Thinking About MOM Software
Every lighting manufacturer, big or small across the globe is trying to keep up with the demand for more LEDs and faster delivery times. Production scheduling, a part of the MOM software platform, addresses constraints like demand fluctuations, the need for new product introduction, and scheduling issues that appear daily. MOM software creates a flexible manufacturing ecosystem to help push products out faster and in top-notch quality.
Read our whitepaper about why more lighting manufacturers are thinking about MOM software, and how it changes top-line revenue.
3 Ways MOM Software Impacts Top-Line Revenue
In today’s fast-paced manufacturing environment, staying competitive means more than just cutting costs—it’s about driving growth. One powerful tool helping manufacturers do just that is Manufacturing Operations Management (MOM) software. Beyond operational efficiency, MOM plays a direct role in increasing top-line revenue. Here are three core ways it makes that happen:
Use Technology to Increase Throughput & Attract & Retain Talent
Staying competitive and attracting talent are some of the top challenges that lighting manufacturers face. Including economic uncertainty, the COVID-19 pandemic, pickier workers, rise in regulations, reduced development costs, and looking to improve margins.
Adopting the right technology will not only increase your throughput but answer the above challenges. Even with the rise in orders, properly utilizing your capacity with fewer highly skilled workers, and a production scheduling software system that can handle all of the production floor constraints, lighting manufacturers can still keep their customers happy.
Manufacturers Succeed with MOM Software
Many manufacturers across the LED lighting industry face intense competition from both domestic and international players, which puts immense pressure on profit margins. Even with complex supply chains, involving multiple suppliers and partners, challenging delivery schedules, and meeting customer demand, LED lighting manufacturers can still succeed using manufacturing operations management (MOM) software.
You can improve one small area or your entire manufacturing process when you implement manufacturing operations management (MOM) software. This case study showcases how one LED lighting manufacturer succeeded with MOM.
Gain a Flexible Business Model
APS Software has revolutionized the way businesses operate by enabling flexible business models.
Advanced planning and scheduling (APS) technology creates events that are not isolated events only affecting manufacturing processes. With the help of APS, businesses can quickly adapt to market changes, optimize resources, and efficiently manage their supply chains. By utilizing real-time data analysis, business leaders can make informed decisions, reduce costs, and improve customer satisfaction. Business flexibility is essential in the modern business landscape, where competition is fierce, and customer expectations are high. With production planning and production scheduling, manufacturers can stay ahead of the curve and remain competitive.
Watch our team dive deep into the features of APS, which showcases the advantages and benefits of how manufacturers can boost their business through production.
Share this
You May Also Like
These Related Stories
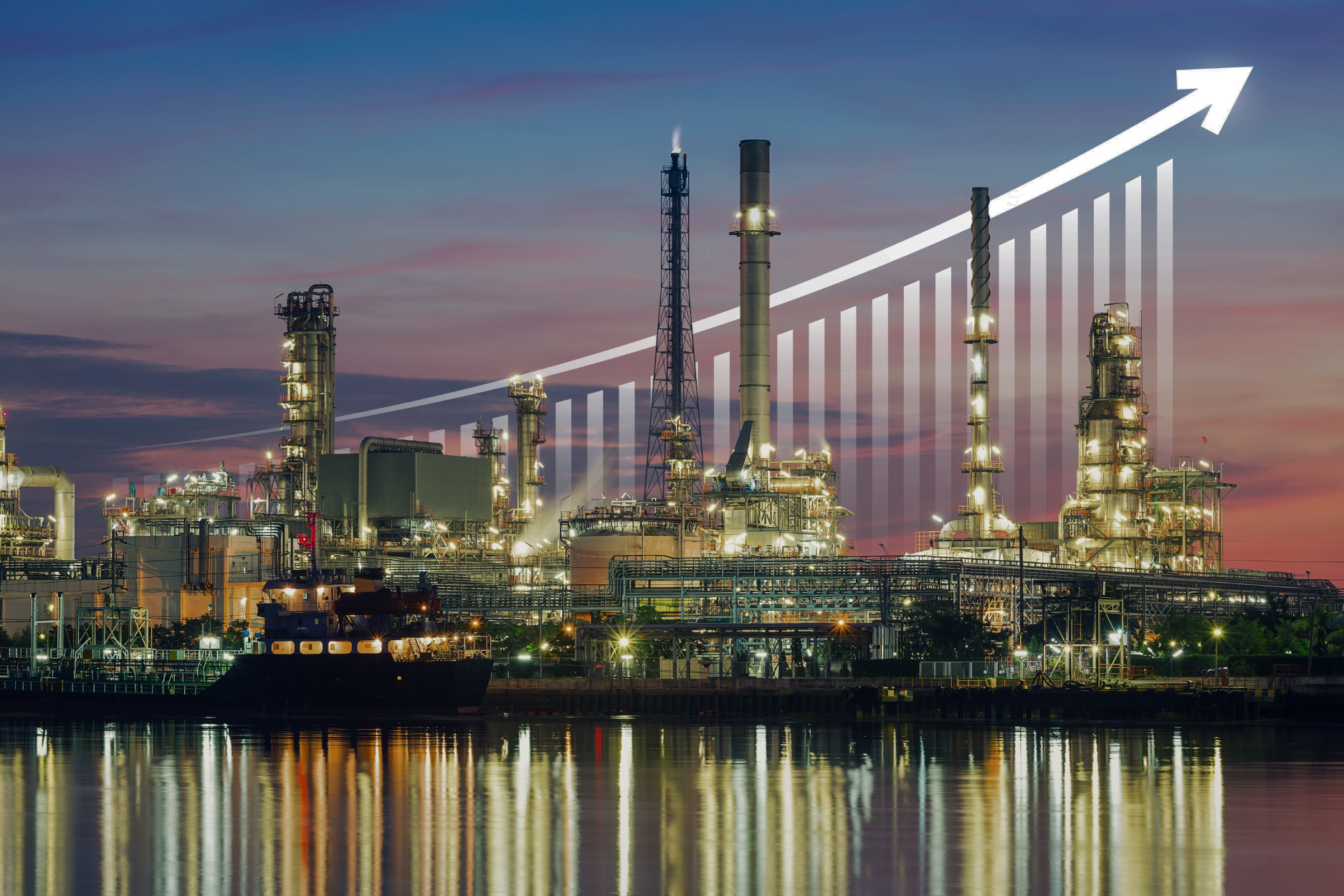
Scaling Production Processes for Small Business Manufacturers
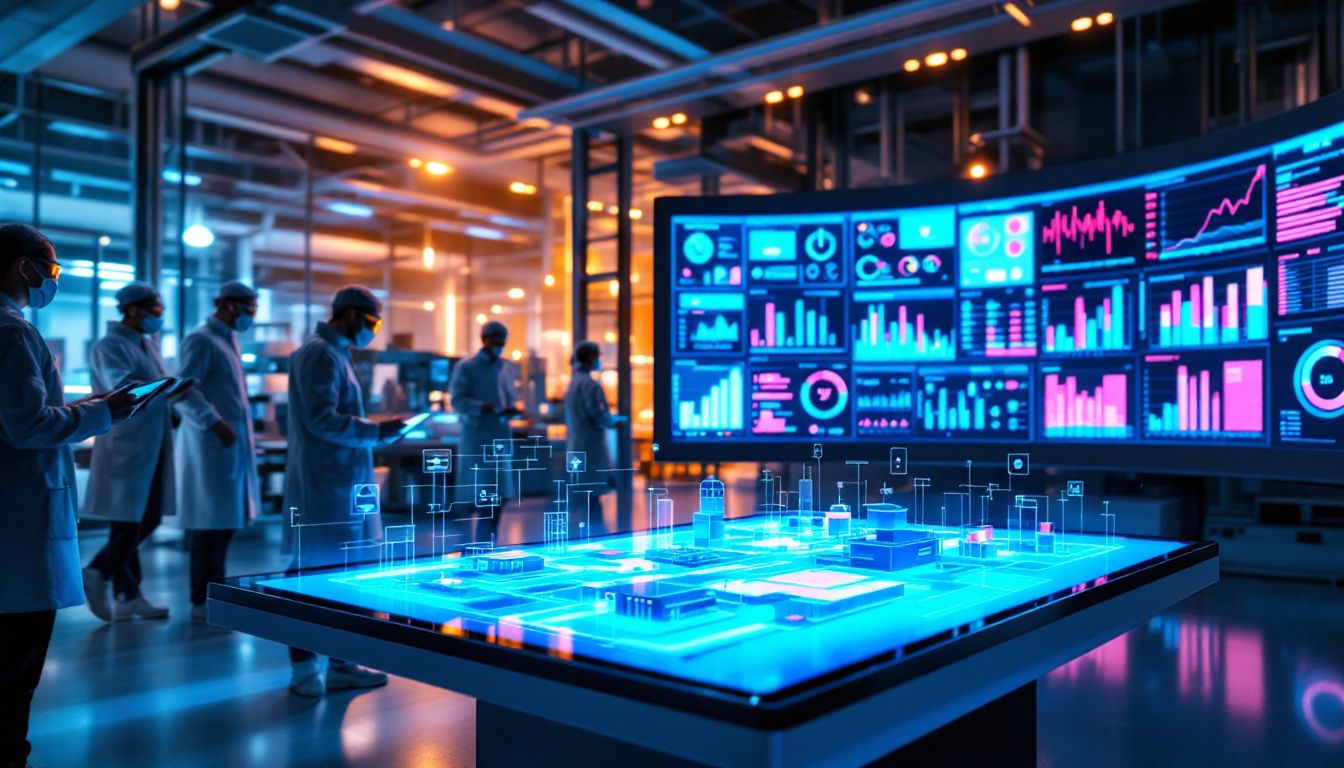
Manufacturing Scheduling Software for Small Business
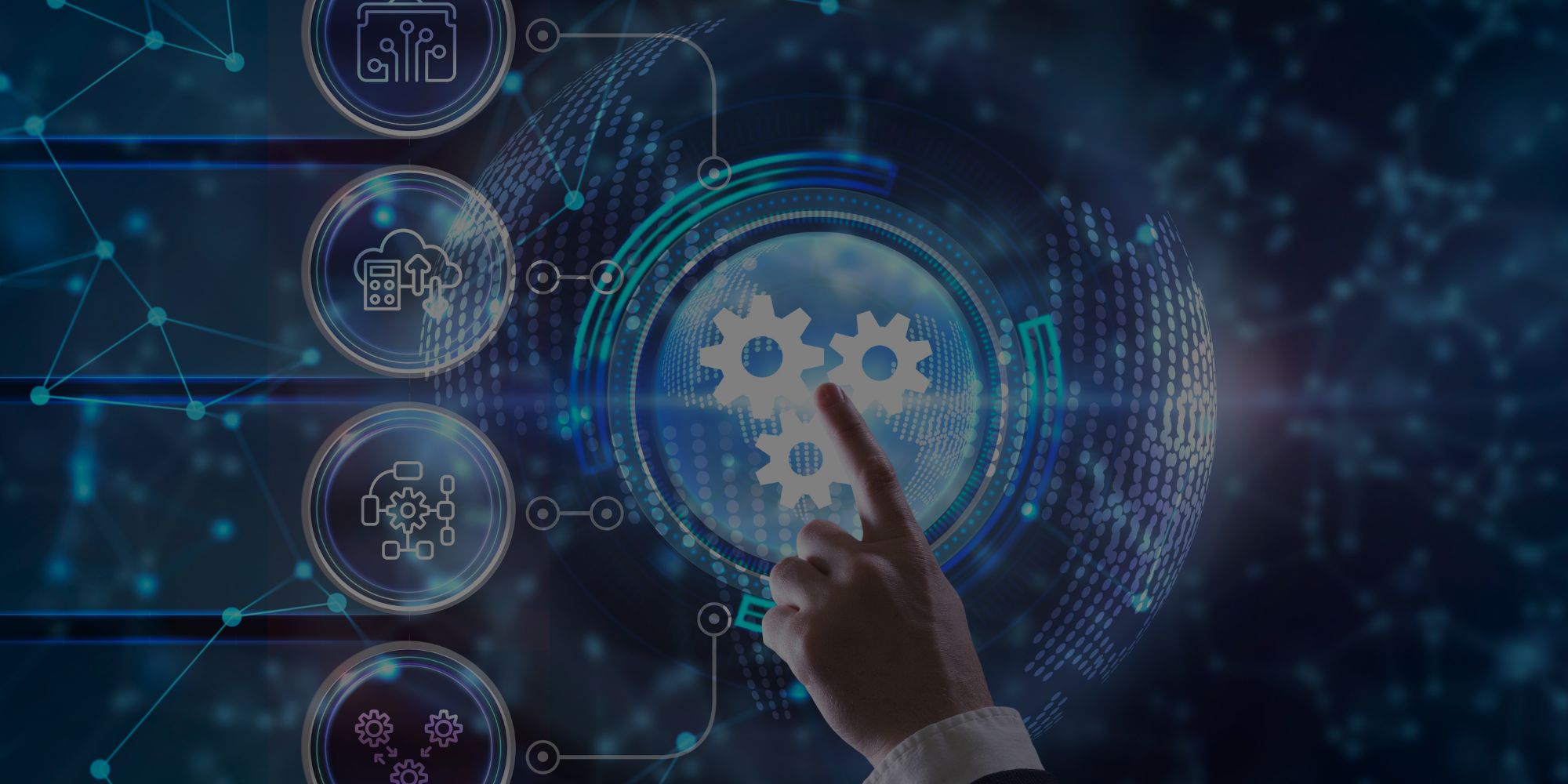
No Comments Yet
Let us know what you think