ERP vs MES: Key Insights to Choose the Right System for Your Business
ERP and MES systems both play crucial roles in manufacturing, but they serve different purposes. ERP systems manage overall business processes. MES systems focus on the shop floor, optimizing production operations and ensuring quality control.
This article will help you understand the differences between ERP and MES and guide you on choosing the right system for your manufacturing needs.
Key Takeaways
-
ERP systems focus on overall business process management, integrating various functions like finance and supply chain, while MES systems specialize in real-time monitoring and optimization of production processes.
-
Integrating ERP and MES systems enhances production efficiency, improves decision-making, and fosters better communication across departments, ultimately aligning manufacturing operations with business goals.
-
When selecting a system, manufacturers must assess their specific requirements, budget considerations, and potential integration capabilities to determine whether to prioritize ERP, MES, or both.
Understanding ERP and MES Systems
ERP and MES systems are essential for manufacturing efficiency. ERP systems manage core business processes and enable data flow and automation across departments, whereas MES and erp system concentrate on production details, ensuring compliance, quality monitoring, and process optimization.
While often confused, these manufacturing execution systems have distinct, complementary roles vital for smooth manufacturing operations.
What is an ERP System?
ERP systems are robust platforms that integrate data from multiple departments into a unified system. They automate essential processes like sales and order management, ensuring seamless information flow for tasks such as inventory management, production planning, scheduling, and quality control. This unification of data sources enhances operational efficiency and offers real-time insights for strategic decision-making.
The modern ERP system is modular, allowing companies to start with essential functions and expand as needed. This flexibility makes ERP systems ideal for organizations looking to consolidate various business functions under a single platform. Key functionalities include financial management, supply chain management, and human resources management, all of which contribute to streamlined operations and improved business performance.
What is an MES System?
MES systems are specialized tools for monitoring and controlling shop floor operations. They ensure smooth production processes, improve efficiency, and manage inventory by extracting data directly from machinery, tracking part genealogy, and enforcing quality control through continuous monitoring. This real-time data collection allows prompt responses to deviations, maintaining high standards of quality and efficiency.
Unlike ERP systems that focus on broader business processes, MES systems are tailored to the specific needs of manufacturing environments. They establish machine controls and monitor process changes, providing granular insights essential for optimizing operations and ensuring compliance with industry standards.
Key Differences Between ERP and MES
ERP and MES systems, though complementary, have distinct functionalities. ERP systems manage operations from a top-down perspective, integrating functions such as finance, HR, and supply chain management. In contrast, MES systems focus on the shop floor, directly managing and monitoring production processes.
Recognizing these differences is key to selecting the right system for specific manufacturing challenges and enhancing operational efficiency.
Functional Focus
ERP systems offer extensive functionality throughout the enterprise, integrating various business functions like finance, supply chain management, human resources, and sales. They manage operations from production planning and resource allocation to financial management and sales forecasting, enabling businesses to streamline core processes and boost efficiency.
Conversely, MES systems specifically optimize and control manufacturing operations, offering real-time visibility into production processes. This enables quick adjustments to schedules based on sales changes. Integrating MES with ERP reduces production delays and ensures materials are prepared according to sales orders, enhancing efficiency and product quality.
Data Capture and Delivery
A key difference between ERP and MES systems is their approach to data capture and delivery. MES systems emphasize immediate monitoring and action for production processes, capturing shop floor exceptions and highlighting issues in real-time. This allows for prompt responses, ensuring smooth operations and maintaining high quality standards.
ERP systems, while capable of tracking production data, generally provide reports over longer periods, such as hours, days, or years. This long-term data supports future goals and resource planning, offering valuable insights for strategic decisions.
Integrating MES with ERP enhances the alignment of production schedules with sales and procurement needs, improving inventory management and demand forecasting.
Integration Capabilities
Integration capabilities also distinguish ERP and MES systems. ERP systems integrate with various business applications, including customer relationship management, marketing, and HR software, to streamline processes and enhance data visibility, creating a cohesive system that supports multiple functions and improves performance.
MES systems, in contrast, integrate directly with production machinery, capturing real-time data and controlling processes. When combined with ERP systems, MES provides real-time data that aligns production with inventory, procurement, and financial operations.
A thorough analysis of both ERP and MES systems helps manufacturers understand their functionalities and integration capabilities, ensuring seamless and efficient operations.
Core Features of ERP Systems
ERP systems feature a wide array of tools designed to streamline processes, enhance data visibility, and boost efficiency. Key features include financial management, supply chain management, and human resources management, each contributing to improved performance and growth.
Financial Management
Financial management is a critical component of ERP systems, offering capabilities for accounting, budgeting, reporting, and financial analysis. Modern ERP systems automate financial processes like tax management and forecasting, reducing administrative workload and errors. By integrating accounting functions, ERP systems streamline processes, enhancing financial transparency and efficiency.
Manufacturing ERP solutions provide real-time financial analysis, enabling quick, informed decisions. This insight helps optimize resource allocation and improve cash flow planning, supporting business growth and efficiency through enterprise resource planning.
Supply Chain Management
ERP systems are vital for supply chain management, offering real-time insights into procurement, production, and distribution. By managing supplier relationships and streamlining procurement, they improve efficiency and reduce costs. They also enhance demand forecasting, helping manufacturers align supply with customer needs, avoiding stockouts or overproduction.
ERP systems’ visibility into supply chain processes ensures quick responses to changes in demand and supply, enhancing customer satisfaction and continuous improvement.
Overall, ERP systems optimize supply chain management, enhancing operational efficiency and business performance.
Human Resources Management
Human resources management is another vital feature of ERP systems, automating HR tasks to reduce workload and improve efficiency. They streamline recruitment by automating candidate tracking and application management, ensuring quick and efficient hiring. These systems also facilitate employee management through modules that track performance, benefits, and payroll.
Integrating HR functions with other business processes, ERP systems enhance overall performance and support strategic human resource planning. This erp integration ensures accurate, up-to-date employee data, enabling better decision-making and improving satisfaction and retention.
Core Features of MES Systems
MES systems optimize manufacturing processes by providing real-time data and insights from the production floor. Core features include real-time production monitoring, quality control, and inventory and material management, each enhancing production efficiency and product quality through a manufacturing execution system.
Real-Time Production Monitoring
Real-time production monitoring is a hallmark of MES systems, enabling instantaneous data collection and analysis from the factory floor. MES systems integrate directly with machinery, providing real-time visibility into performance and allowing prompt responses to issues. This enhances decision-making, helping manufacturers optimize workflows and improve efficiency.
Integrating AI and machine learning in MES systems further enhances real-time monitoring. These technologies enable predictive maintenance, optimize production schedules, and minimize downtime. Leveraging real-time data and AI insights, MES systems help manufacturers maximize efficiency and maintain high product quality.
Quality Control
Quality control is a critical feature of MES systems, ensuring products meet required standards. MES systems track deviations and integrate with external quality management to maintain high product quality. Real-time monitoring allows timely data capture and corrective actions, preventing defects and ensuring compliance.
Tracking raw materials, batch numbers, and product compliance, MES systems offer comprehensive quality control throughout production. Continuous monitoring and data capture help maintain high standards and improve customer satisfaction.
MES systems play a crucial role in managing quality, ensuring products are consistently produced to high standards.
Inventory and Material Management
Effective inventory and material management is crucial for smooth manufacturing operations. MES systems excel by integrating with shop floor applications like IoT devices and sensors, enhancing tracking capabilities. Real-time data on material usage and availability helps prevent delays and ensures accurate inventory levels.
By maintaining accurate inventory levels and supporting timely decisions, MES systems improve efficiency and reduce waste. Integrating MES with real-time data sources enables manufacturers to optimize material usage and streamline production, ensuring efficient resource use.
Benefits of Integrating ERP and MES Systems
Integrating ERP and MES systems offers numerous benefits, providing a comprehensive view of operations. This integration fosters seamless data exchange, enhances production efficiency, and improves decision-making and communication across departments.
Enhanced Production Efficiency
Integrating ERP and MES systems significantly enhances production efficiency by optimizing schedules, reducing waste, and improving resource allocation. MES tracks real-time performance, while ERP provides enterprise-wide data, allowing manufacturers to adjust schedules based on sales fluctuations and prevent stockouts. This ensures manufacturers can meet customer expectations without excessive inventory.
Aligning production with supply chain management, integrated systems reduce waste and improve efficiency. Real-time visibility into performance fosters better responsiveness to market changes, enhancing operational efficiency and supporting growth.
Better Decision-Making
Integrated ERP and MES systems provide a holistic view of data, facilitating timely and informed decision-making. Real-time data from MES on production processes, machines, materials, and labor, combined with ERP’s strategic insights, enables decisions based on accurate information. This synergy improves decision quality, supporting efficiency and customer satisfaction.
Actionable insights derived from both real-time and historical data enhance decision-making capabilities, enabling businesses to proactively address issues and optimize business operations. This informed decision-making supports continuous improvement and drives better business performance.
Improved Communication Across Departments
Integrated ERP and MES systems play a critical role in enhancing communication and coordination across multiple departments. MES provides real-time shop floor data to ERP, facilitating informed decision-making and aligning production with other business functions. This seamless data exchange ensures that departments such as sales, production, and procurement are always on the same page, improving overall operational efficiency.
When a sales order triggers production, MES ensures that the necessary materials are ready, streamlining communication between sales and production departments. This improved communication helps prevent production delays and supports better coordination across the entire production process and manufacturing process.
Choosing the Right System for Your Manufacturing Business
Selecting the right system for your manufacturing business requires a thorough understanding of the differences between MES and ERP systems and an evaluation of your specific needs. The primary decision is whether to implement MES, ERP, or both, based on factors such as current infrastructure, budget, and long-term goals.
The following subsections provide guidance on assessing business requirements and considering budget and resources.
Assessing Business Requirements
When assessing business requirements, a manufacturing company needs to consider various factors, including:
-
production efficiency
-
quality
-
integration capabilities
-
real-time manufacturing data tracking
-
scalability
-
industry compliance
If the primary goal is to optimize shop floor operations and ensure quality, an MES system may be the best choice. However, if a comprehensive business solution is required to manage multiple business functions, an ERP system should be considered first.
Manufacturers looking to improve production efficiency may prioritize implementing an MES system initially, while those seeking to consolidate various business functions under a single platform may opt for an ERP system. Assessing these requirements helps determine the most suitable system for addressing immediate and long-term business needs.
Considering Budget and Resources
Budget and resource considerations are crucial when selecting between ERP and MES systems. Generally, ERP systems are less expensive to implement compared to MES systems, as the latter may require more customization and integration with other systems. The costs associated with implementing ERP or MES systems can vary significantly based on business size and system complexity.
Initial costs for MES implementation can reach thousands to millions of dollars depending on the scope, with long-term costs potentially increasing due to additional integration requirements.
When selecting an ERP system, essential considerations include support for business processes, integration capabilities, customization, scalability, provider reliability, and user-friendliness. Evaluating these factors helps ensure that the chosen system aligns with budgetary constraints and resource availability.
Implementation Best Practices
Implementing ERP and MES systems can be complex, but following best practices enhances the likelihood of success. This includes setting clear goals, providing ongoing training and support, and ensuring effective communication throughout the implementation process.
The following subsections will outline these best practices in more detail.
Setting Clear Goals
Defining clear goals before implementing MES or ERP systems is essential as it keeps the project focused and aligned with business needs. Establishing a timeline for implementation by breaking the project into phases with realistic deadlines helps maintain momentum and ensures that each phase is completed on time.
Clear goals and timelines are vital for tracking progress and achieving successful implementation.
Training and Support
Providing ongoing training and support post-implementation is crucial to ensure that employees effectively utilize ERP and MES systems. Establishing measurable objectives helps track the success of the implementation project and ensures that the systems are used to their full potential. Regular training sessions and support resources help employees stay updated with system functionalities and best practices.
Defining project milestones assists in maintaining momentum throughout the implementation process and ensures that progress is regularly monitored. Continuous support and training help address any issues that arise and ensure that the systems continue to meet the evolving needs of the business.
Future Trends in ERP and MES Systems
The future of ERP and MES systems is shaped by emerging technologies such as cloud-based solutions and AI-powered analytics. These trends are driving significant changes in how manufacturing businesses operate, offering enhanced flexibility, scalability, and operational efficiency.
The following subsections will explore these trends in more detail.
Cloud-Based Solutions
Cloud-based ERP and MES solutions represent a shift towards more scalable and flexible manufacturing technologies. Modular cloud-based systems provide flexibility without overextending resources, making them ideal for small manufacturers. The scalability of these solutions allows manufacturers to adapt to changing business needs and growth opportunities, significantly enhancing operational efficiency and resource allocation.
Implementing cloud-based ERP and MES solutions also facilitates easier upgrades and maintenance due to their hosted nature. This shift towards cloud-based solutions ensures that manufacturers can stay competitive by leveraging the latest technological advancements and continuous software updates.
AI and Machine Learning
AI and machine learning are transforming ERP and MES systems by enabling advanced data analysis and automation. AI-enhanced MES can predict equipment failures before they occur, allowing manufacturers to proactively address issues and reduce downtime. The use of predictive analytics leads to increased efficiency and optimized production processes.
Integrating AI and machine learning in ERP and MES systems not only enhances operational performance but also drives innovation across the manufacturing industry. These technologies enable manufacturers to harness the power of data, making smarter decisions and continuously improving their operations.
Summary
In conclusion, both ERP and MES systems play vital roles in modern manufacturing, each offering unique capabilities that enhance operational efficiency and business performance. Understanding the differences between these systems and their integration possibilities can help manufacturers choose the right solution for their specific needs. By leveraging the strengths of both ERP and MES, manufacturers can optimize production processes, improve decision-making, and stay competitive in an ever-evolving industry.
Frequently Asked Questions
What is the main difference between ERP and MES systems?
The main difference between ERP and MES systems is that ERP systems provide a broad integration of various business functions across departments, whereas MES systems are specialized in monitoring and controlling manufacturing processes on the shop floor.
Can ERP and MES systems be integrated?
Absolutely, integrating ERP and MES systems facilitates seamless data exchange, which significantly enhances operational efficiency and improves decision-making across departments.
Which system should a manufacturer implement first, ERP or MES?
A manufacturer should primarily implement an ERP system for comprehensive business management first, unless the immediate need emphasizes optimizing shop floor operations, in which case an MES system may take precedence.
What are the cost considerations for implementing ERP and MES systems?
Implementing ERP systems is typically less costly than MES systems due to the latter's requirement for greater customization and integration. Overall costs will depend on the size of the business and the complexity of the systems, with MES implementations potentially reaching substantial financial investments.
How do cloud-based solutions benefit manufacturing ERP and MES systems?
Cloud-based ERP and MES systems significantly enhance manufacturing operations by providing scalability and flexibility, allowing for seamless adaptation to evolving business needs. These solutions also promote operational efficiency through easier upgrades and continuous software updates, ensuring competitiveness in the market.
Share this
You May Also Like
These Related Stories
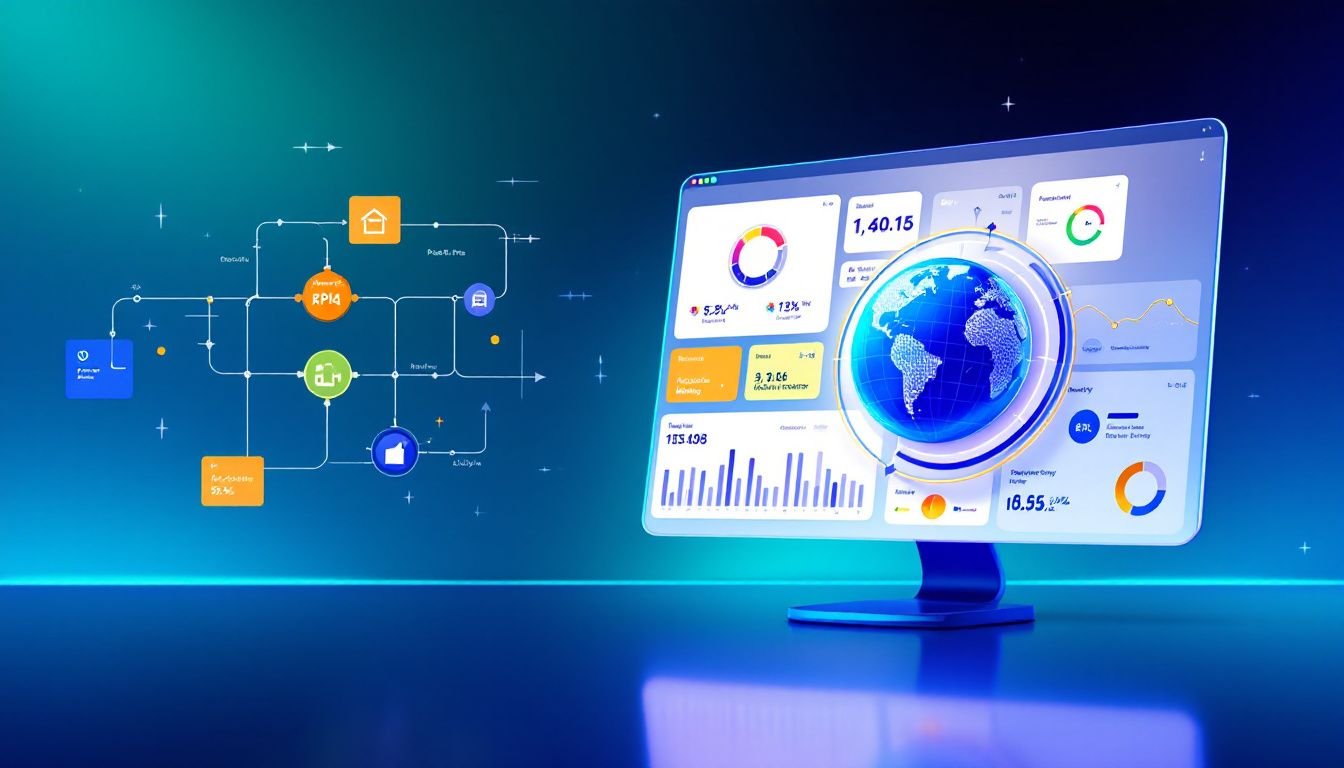
MES Software for Small Business Manufacturers
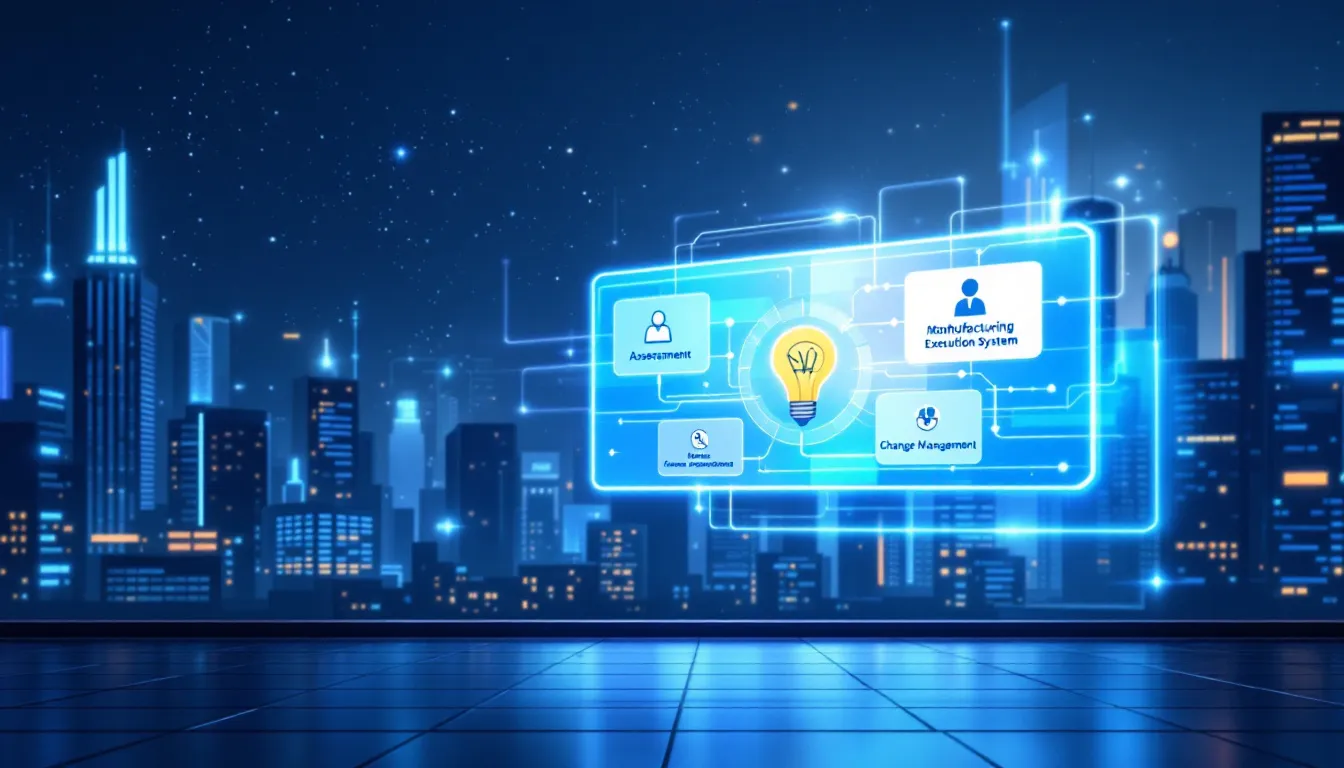
Mastering MES Implementation: Key Steps for Success and Efficiency
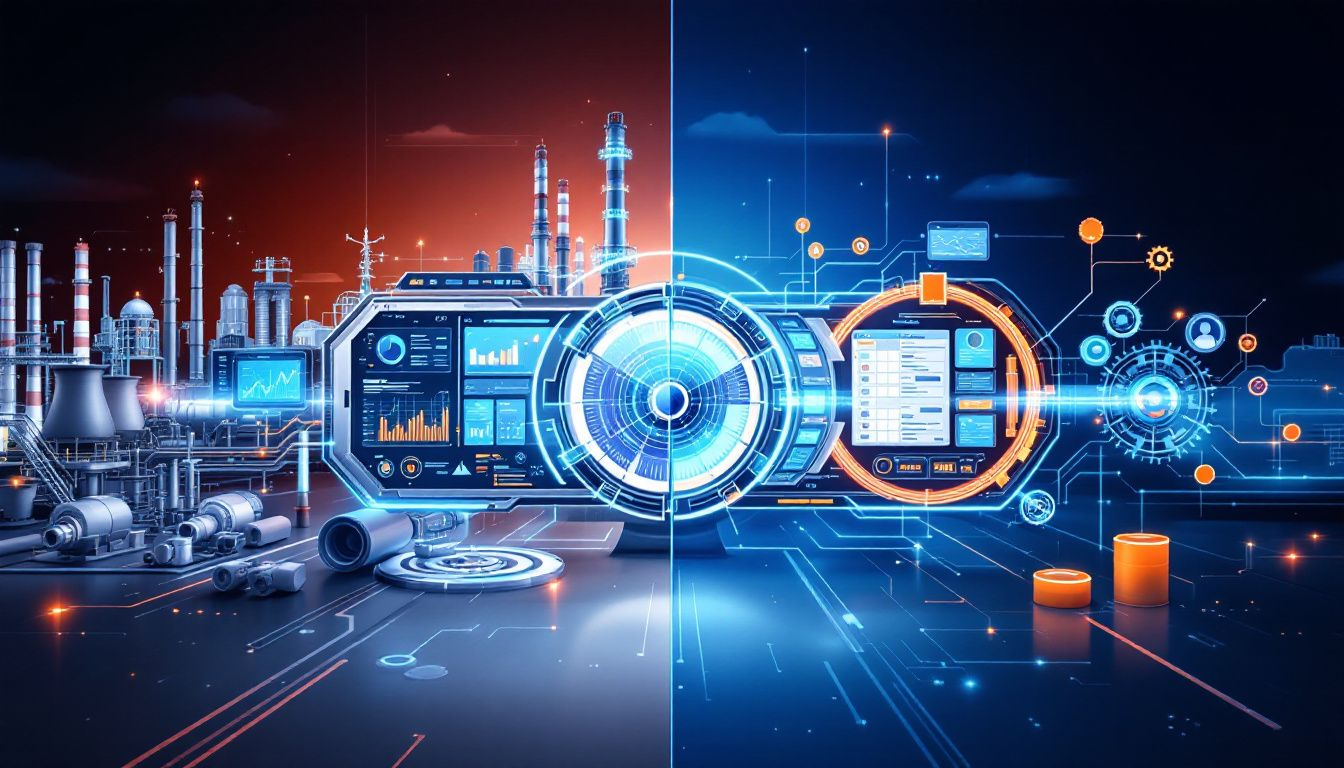
No Comments Yet
Let us know what you think