SCADA vs MES: Key Differences for Optimizing Manufacturing Efficiency
When choosing industrial automation systems, understanding the differences between SCADA and MES is crucial. SCADA focuses on real-time monitoring and control of industrial processes, while MES manages and optimizes manufacturing operations.
This article will clarify how these systems work, where they overlap, and which might be better for your specific manufacturing needs.
Key Takeaways
-
SCADA systems focus on real-time monitoring and immediate process control, while MES systems manage comprehensive production processes and workflows.
-
Integrating SCADA and MES enhances operational efficiency, improves quality control, and facilitates better decision-making through seamless data flow.
-
Choosing between SCADA and MES should be based on specific manufacturing goals, with consideration for integration with existing systems and effective change management.
Overview of SCADA Systems
SCADA stands for Supervisory Control and Data Acquisition, an essential framework for tracking and managing various industrial operations in expansive venues like manufacturing sites, power distribution networks, water processing facilities, and petroleum refineries. These SCADA systems are pivotal as they provide instant data which enables operators to fine-tune machinery to heighten both output levels and safety measures. With components such as sensors and Programmable Logic Controllers (PLCs), these systems aggregate live data from a wide array of equipment thereby elevating the productivity of operations.
Within the realm of manufacturing, SCADA systems assume responsibility for centralized supervision including oversight on control apparatuses, collection of information at different stages while providing monitoring capabilities alongside management alerts system-wide. They accrue a range of data parameters like heat level indicators pressure gauges or rotational velocity that assist maintenance protocols plus contribute to efficiency reports. The crux behind scada systems lies within their commitment to refining said processes so as to bolster overall effectiveness.
Furthermore, integrated aspects within any SCADA setup—are visual depictions outlining comprehensive enterprise activities encompassing machine functions operator engagements facility configurations along with upkeep tasks remain vital attributes inherent in such setups offering instantaneous visualization across plant floors thus becoming invaluable assets supporting adept supervisory regulation paired up with prompt acquisition endeavours regarding pertinent stats.
Overview of MES Systems
Manufacturing execution systems (MES) serve as the crucial link between the enterprise level and shop floor, ensuring efficient management and refinement of manufacturing processes. These MES systems are pivotal for arranging production plans, setting schedules, and boosting optimization within production workflows by providing real-time insight into ongoing production actions. By decreasing waste and raising profit margins, they have become an indispensable element in contemporary manufacturing.
By providing manufacturers with immediate data insights from operations, MES software significantly elevates operational efficiency through superior decision-making abilities and effective monitoring that bolsters overall equipment productivity. The integration of MES software solutions with both ERP and SCADA systems ensures uninterrupted data flow across various platforms, which is instrumental in augmenting productivity levels as well as efficacy throughout manufacturing activities.
Scope and Functionality Comparison
SCADA systems are designed with an emphasis on real-time monitoring and the control of processes, whereas MES (Manufacturing Execution Systems) concentrate on handling operational procedures and overseeing production workflows. When these two types of systems operate in conjunction, they synergistically enhance the overall efficiency within a manufacturing setting.
Subsequent sections will explore Comparisons between these systems, ranging from aspects such as data acquisition to differences in their user interfaces.
Data Acquisition vs. Production Management
SCADA systems are adept at gathering data in real time and providing immediate control over single machines or entire systems within a production environment. They handle the acquisition of crucial parameters such as temperature, pressure, and machine functionality to maintain operational efficiency and swiftly react to any arising issues.
In contrast, MES systems oversee the entirety of the production process with an emphasis on refining outcomes and adhering to manufacturing schedules. While SCADA prioritizes instantaneous data collection and prompt adjustments in real-time operations, MES aims at improving overall management by streamlining production processes for better performance outcomes.
Integrating both SCADA and MES into one’s system infrastructure allows for comprehensive oversight of manufacturing procedures which bolsters decision-making capabilities while boosting productivity levels.
Real-Time Control vs. Comprehensive Management
SCADA systems are pivotal for controlling processes, emphasizing instant monitoring and modification capabilities. These systems furnish operators with instantaneous data regarding equipment status and various tracking features, allowing for swift reactions to alterations or problems within operations. The ability to respond promptly is essential in ensuring seamless activity on the factory floor.
On the other hand, MES provides a wider perspective of manufacturing operations by managing aspects such as production planning, inventory control, and distribution of resources. This highlights a clear distinction: while SCADA excels at real-time control over process management, MES offers an extensive approach to managing overall operational functions.
User Interfaces for Different Roles
SCADA systems come with user interfaces known as Human-Machine Interfaces (HMI), which are crafted to be intuitive for operators within the manufacturing realm. They present data visually and enable control in real time, streamlining the process of overseeing and fine-tuning machinery on the fly.
On the other hand, MES systems are equipped with interfaces that serve production managers, planners, and executives by delivering a more comprehensive set of capabilities. Through these interfaces, users gain access to extensive information about production timelines, stock quantities, and operational efficiency across various levels. This aids them in making informed decisions and formulating long-term strategies.
Benefits of Integrating SCADA and MES
The combination of SCADA and MES systems within manufacturing operations substantially improves the effectiveness of production processes. This synergy bolsters operational efficiency, diminishes wastage, and amplifies visibility throughout the stages of production. It facilitates real-time surveillance and proficient control over production activities, resulting in refined plant functions with an increased capacity to adapt swiftly to modifications in production demands.
Segments will explore these advantages more thoroughly.
Enhanced Data Flow and Decision Making
Integrating MES and SCADA systems enhances the efficiency of operations by allowing for rapid detection of production problems and prompt decision-making. Having access to real-time data from these systems aids in making well-informed choices, giving managers the agility to quickly address fluctuations on the factory floor. Such improved exchange of information simplifies procedures and fosters ongoing advancements within manufacturing processes.
By combining these systems with enterprise resource planning (ERP) platforms, their advantages are significantly expanded upon, delivering a comprehensive perspective over the whole manufacturing process. This integration supports decisions that are based on robust data analysis throughout an organization’s entire scope of operations.
Improved Quality Control and Compliance
The fusion of SCADA and MES systems is critical for enhancing quality control and achieving compliance with manufacturing regulations. Through real-time monitoring, these systems ensure that product quality remains consistently high and regulatory non-compliance risks are minimized throughout the production process.
For MES to be effective, it requires precise data collection since subpar data can cause operational inefficiencies and result in compliance challenges. By providing an all-encompassing perspective on production processes, integrated SCADA and MES systems amplify operational efficiency overall while facilitating ongoing enhancements in manufacturing operations.
Choosing the Right System for Your Needs
Selecting the right system—SCADA or MES—depends on specific manufacturing goals and needs. If the focus is on real-time data collection and immediate process control, a SCADA system might be the best choice. However, for comprehensive production management and optimization, an MES system would be more suitable. Manufacturers should evaluate their requirements for remote access, data visualization, and integration with existing systems like ERP and SCADA when making this decision.
Effective change management and training are crucial to overcoming user resistance and ensuring successful MES adoption. Customization of MES solutions should be balanced with standardization to avoid delays and cost overruns, and project planning should include a contingency fund to manage budget issues during implementation.
Case Studies of SCADA and MES Integration
Examples from the field illustrate the considerable advantages of combining MES and SCADA systems. For instance, when an automotive parts producer incorporated these systems, they saw a 30% decrease in their production cycle time. Meanwhile, a food and beverage manufacturer witnessed their production line efficiency soar by 20%, demonstrating how significant operational enhancements can be achieved through such integration.
After adopting integrated MES and SCADA technologies, another enterprise within the food and beverage sector experienced waste shrinkage by 25% along with a boost in product quality by 10%. A related study within the automobile industry observed that product defects fell by 20%, underscoring how merging SCADA with MES can beneficially influence both product excellence and manufacturing effectiveness.
Common Challenges and Solutions
The combination of SCADA and MES systems within manufacturing processes can be fraught with difficulties such as ensuring seamless system interoperability, maintaining consistent data flow, and aligning processes. System integrators are key in overcoming these obstacles by tailoring, deploying, and weaving new technologies into existing frameworks for production. These specialists provide customized solutions that resonate with distinct manufacturing operations and organizational objectives to ensure a harmonious fusion of SCADA with MES.
Professional expertise is crucial in surmounting the typical hurdles associated with integrating these systems, thereby enhancing the efficiency and productivity of both SCADA and MES systems within manufacturing environments.
Future Trends in SCADA and MES Systems
Advancements in the domains of SCADA and MES systems are paramount for updating industrial automation within manufacturing processes, fostering significant improvements in productivity. The continuous analysis provided by MES systems contributes to improved decision-making abilities and increases operational efficiency. Enhanced data analytics coupled with adherence to Industry 4.0 benchmarks propel these developments forward, allowing manufacturers to predict maintenance needs ahead of time, thereby reducing machine downtime and boosting overall production efficacy.
In the realm of industrial automation transformation, innovations within SCADA and MES platforms promise transformative impacts on how the manufacturing industry evolves. These technological strides present fresh avenues for inventive solutions that can spur growth across this vital economic sector.
Summary
Grasping the distinctions between SCADA and MES systems is vital for improving manufacturing processes. Whereas SCADA concentrates on gathering real-time data and controlling process, MES deals with overseeing complete production workflows. The synergy of these systems bolsters operational proficiency, ensures quality control, and augments the capacity to make informed decisions.
In the ever-evolving landscape of manufacturing, fusing SCADA with MES will be instrumental in spurring innovation and attaining enhanced efficiency levels. Utilizing these technologies enables manufacturers to maintain a competitive edge while adapting to swift industry transformations.
Frequently Asked Questions
What is the primary difference between SCADA and MES systems?
The primary difference between SCADA and MES systems is that SCADA focuses on real-time data acquisition and process control, whereas MES manages and optimizes the entire production process.
This distinction underscores the different roles each system plays in manufacturing operations.
How does integrating SCADA and MES systems improve manufacturing operations?
Integrating SCADA and MES systems significantly improves manufacturing operations by enhancing operational efficiency, reducing waste, and improving quality control through seamless data flow.
This integration ultimately supports more informed decision-making.
What industries benefit most from SCADA systems?
In industries such as manufacturing, power generation, water treatment, and oil refining, SCADA systems significantly improve operational efficiency and augment monitoring capabilities.
What challenges might manufacturers face when integrating SCADA and MES systems?
Manufacturers may face challenges such as interoperability issues, data consistency problems, and difficulties in process alignment when integrating SCADA and MES systems. Engaging expert assistance and developing tailored solutions can effectively address these challenges.
What future trends are emerging in SCADA and MES technologies?
Future trends in SCADA and MES technologies include advanced data analytics, continuous data analysis capabilities, and seamless integration with Industry 4.0 standards, which will enhance efficiency and innovation in manufacturing.
Share this
You May Also Like
These Related Stories
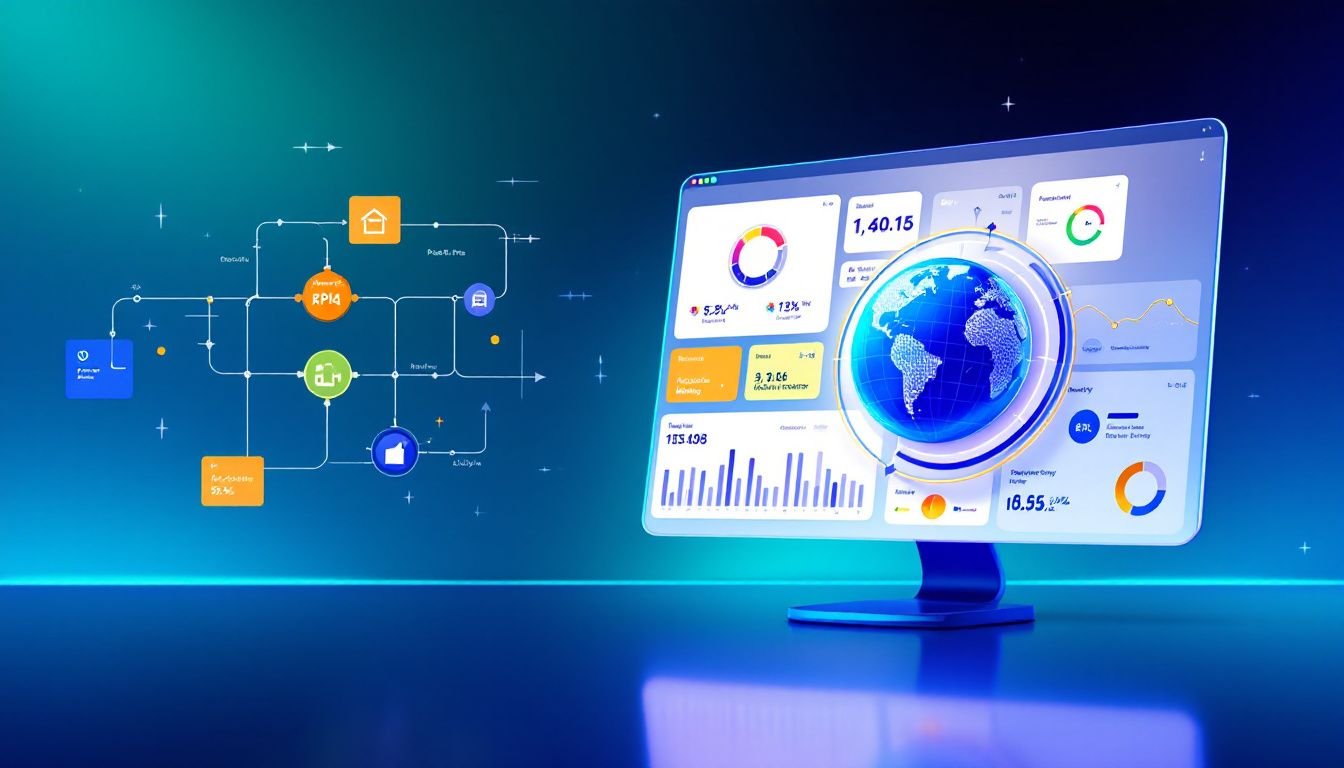
MES Software for Small Business Manufacturers
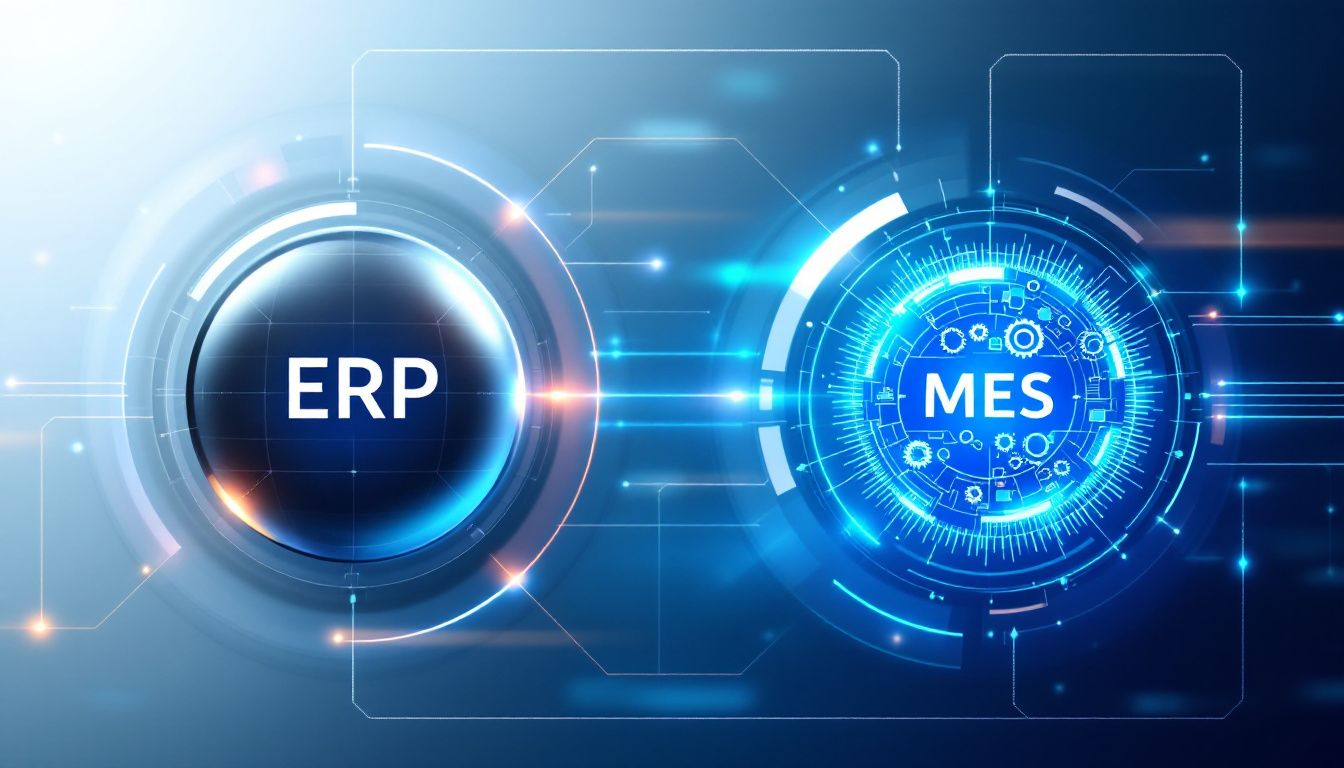
ERP vs MES: Key Insights to Choose the Right System for Your Business
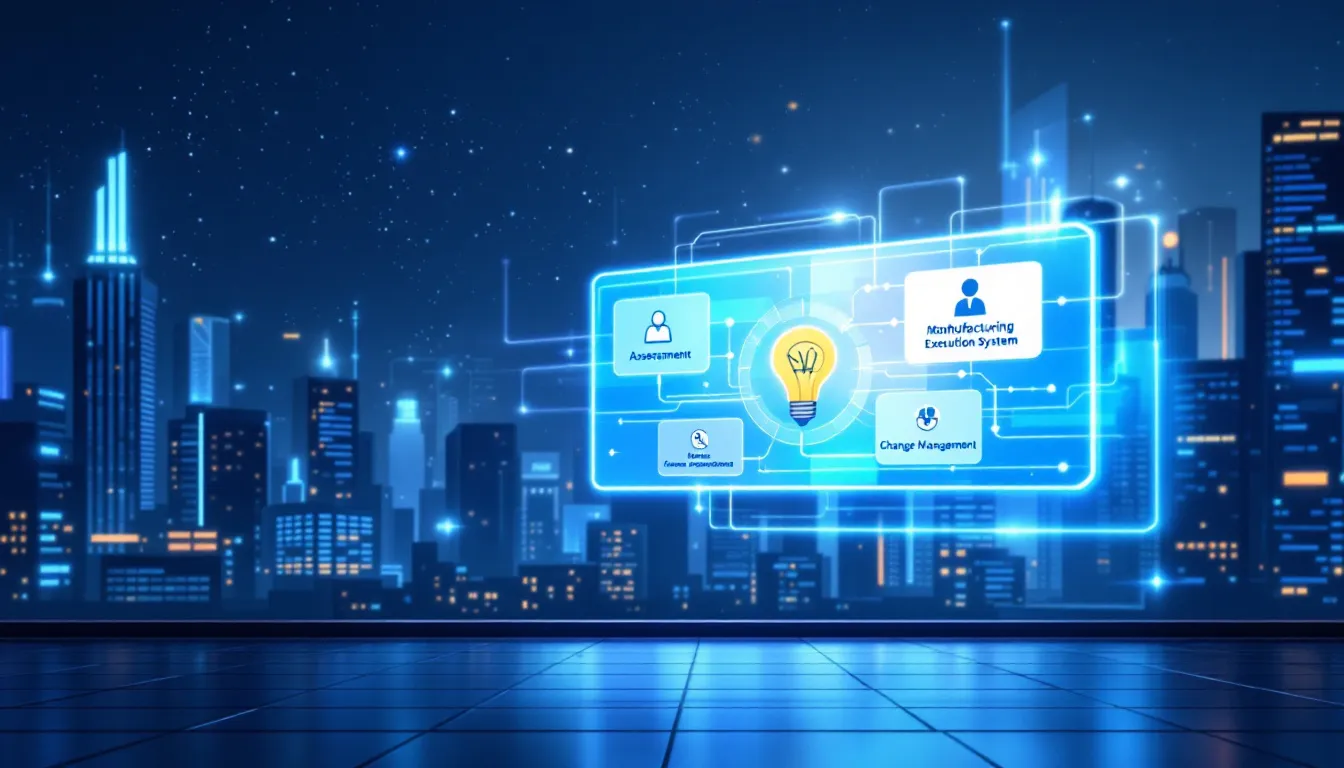
No Comments Yet
Let us know what you think