Ultimate Guide to Manufacturing Digital Transformation Roadmaps
Embarking on digital transformation in manufacturing? Start with a manufacturing digital transformation roadmap.
This guide covers assessing your current state, setting objectives, and implementing changes effectively.
Key Takeaways
-
A digital transformation roadmap is essential for aligning digital initiatives with business objectives, ensuring efficient integration and maximizing operational efficiencies, especially within the manufacturing business environment.
-
Key elements of a successful roadmap include setting clear milestones, reskilling personnel, incorporating agile processes, and assessing current digital maturity to tailor technology selection.
-
Having a clear vision of digital transformation goals helps align stakeholders and ensures support during the process.
-
A digital transformation strategy necessitates stakeholder buy-in to demonstrate its long-term value.
-
Continuous training and monitoring progress are vital for adapting to changes and overcoming challenges, ultimately leading to enhanced productivity, better decision-making, and improved competitiveness in the manufacturing sector.
Understanding the Importance of a Digital Transformation Roadmap
In the increasingly digital world of manufacturing, a digital transformation roadmap unlocks the full potential of digital initiatives. It serves as a strategic guide, helping organizations manage the transformation of processes, business models, and customer experiences effectively. Manufacturing companies rely on such roadmaps to guide their digital transformation projects, ensuring strategic planning, collaboration, and the selection of the right technology partners. Without a roadmap, many digital transformation initiatives can become fragmented and lose momentum, leading to missed opportunities and inefficiencies.
A well-defined digital transformation roadmap facilitates the integration of digital projects across the entire organization, ensuring that all efforts are aligned with business objectives. This alignment can lead to significant operational efficiencies and large-scale change, moving beyond solving isolated issues to achieve comprehensive transformation. Companies that align their business objectives with their digital transformation roadmap are better positioned to track important benchmarks and KPIs, ultimately driving successful transformation. Additionally, investment in digital tools and technologies improves asset efficiency, further enhancing operational outcomes.
Moreover, a robust digital transformation strategy addresses the challenges of disconnected processes in manufacturing, enhancing the overall efficiency and effectiveness of operations. A clear path outlined in a digital transformation roadmap ensures manufacturers transition smoothly through their digital journey, meeting and sustaining their sustainable digital transformation goals. Manufacturing leaders play a crucial role in championing these efforts, often seeking experienced partners to guide and implement successful digital transformation projects.
Key Elements of a Successful Digital Transformation Roadmap
A digital transformation roadmap serves as a strategic guide for integrating digital technology into business operations. A clear roadmap outlines essential steps and milestones crucial for a successful digital transformation strategy. Proper planning of the budget is crucial to account for the complexity and cost of each implementation, ensuring that resources are allocated effectively.
The implementation strategy should include:
-
Specific milestones, deliverables, and timelines to track progress effectively.
-
Mechanisms to allow organizations to monitor their advancement and make necessary adjustments along the way.
-
Incorporation of agile processes.
-
Reskilling of personnel.
-
Updating the technology stack.
-
Integration of connected devices such as IoT and robotics to enable organizations to leverage modern technologies and enhance operational capabilities.
These components are critical to a successful roadmap, ensuring that the organization remains adaptable and responsive to changes.
Digital transformation roadmaps typically include common elements found across various industries, such as a clear vision, well-defined objectives, and a structured approach to technology adoption. Effective data capture, enabled by IoT sensors and other technologies, is essential for data-driven decision-making and process optimization. Following these elements helps organizations develop a comprehensive roadmap that guides their digital transformation journey and drives successful outcomes in their digital strategy and digital strategies.
Assessing Your Current Digital Maturity
Before starting a digital transformation journey, assessing your current digital maturity is crucial. This assessment helps tailor your technology selection to meet the specific needs and capabilities of your organization. Manufacturing organizations experience multiple stages of digital maturity, ranging from emergent to integrated. The integrated stage is characterized by operations that have most processes digitized along with advanced uses of AI and IoT. Manufacturers at this stage also use robust data analytics capabilities to drive operational decisions. Once manufacturers reach the connected stage of digital maturity, they exhibit greater integration of digital technologies across operations.
During the digital maturity assessment, it is crucial to identify pain points, inefficiencies, and opportunities for growth. This evaluation should also consider the existing technological capabilities and readiness for digitalization. Understanding your current state helps plan the steps needed to advance to higher levels of digital maturity and achieve a successful transformation. For example, augmented reality (AR) can guide warehouse employees to the exact location of products in inventory control, showcasing how digital tools can address specific operational challenges.
Furthermore, assessing your current infrastructure’s capabilities, including existing systems, is vital to support digital transformation effectively. This involves evaluating cloud technologies, IoT integration, and data analytics analysis capabilities, essential for driving operational decisions and optimizing processes.
Setting Clear Objectives and Vision
Setting clear objectives and vision is a fundamental step in developing a digital transformation roadmap. A clear roadmap helps avoid fragmented initiatives and ensures alignment with business priorities. Prioritizing customer experience by adapting to their evolving needs drives success in digital transformation.
Defining specific timelines and milestones enhances accountability and keeps teams focused during the transformation journey. Communicating objectives effectively secures support for transformation initiatives, ensuring stakeholders work towards common business goals.
Identifying and Prioritizing Digital Technologies
Identifying and prioritizing digital technologies is key to a successful digital transformation. Evaluating the potential impact of digital technologies on productivity and their alignment with business objectives is essential. Factors to consider include the technology’s alignment with overall business strategy and its potential to drive significant improvements in manufacturing processes.
Cloud computing is becoming crucial for integrating IoT solutions within manufacturing processes. It processes large volumes of data from manufacturing facilities, facilitating insight-driven decision-making. Other digital technologies such as AI, big data analytics, and robotics should also be evaluated for their potential to enhance manufacturing operations in the context of the industrial internet. Artificial intelligence (AI) and machine learning (ML) are principal technologies streamlining digital transformation in manufacturing. AI enables predictive maintenance that reduces downtime in manufacturing operations. Machine learning analyzes large datasets to identify patterns and improve performance over time, making it a valuable tool for optimizing processes.
Virtual reality is also playing an increasing role in manufacturing digital transformation, with applications in visualization, immersive training, and design validation to improve efficiency and collaboration.
Using digital twins can enhance the prototyping process during the initial phases of technology implementation, saving time and money. Adopting a structured approach to technology selection minimizes disruption and ensures new technologies contribute to digital transformation goals.
Developing an Implementation Plan
A comprehensive implementation plan guides successful digital transformation. The plan should include:
-
Phases, milestones, and deadlines for executing initiatives, ensuring efforts are coordinated and aligned with the transformation roadmap.
-
Establishing cross-functional implementation teams to ensure a collaborative approach.
-
Involving employees from different departments in the process of implementing digital transformation.
Organizations should:
-
Actively seek employee feedback and involve them in the transformation process to navigate challenges.
-
Plan for hiring or partnering with external resources if skill gaps cannot be addressed internally.
-
Develop training programs for upskilling employees to facilitate smooth technology adoption.
A digital twin for prototyping and testing saves time and money during the pilot project phase. A well-defined plan mitigates risks arising from the lack of a structured change management strategy during digital transformation.
Creating a Phased Approach
A phased approach to technology implementation allows for gradual adoption and minimizes disruption to the entire production process. This approach enhances overall success rates for digital transformation initiatives by ensuring that each phase is carefully planned and executed.
Resource availability ensures necessary resources are allocated for each phase of the implementation when developing a phased approach. Faster product development, a key benefit of agility in the digital transformation process, allows organizations to respond quickly to market demands.
Assigning Roles and Responsibilities
Clear roles and responsibilities enhance stakeholder engagement and ensure the effectiveness of the implementation process. Designating specific roles and responsibilities streamlines the implementation process and ensures all team members know their tasks and contributions.
Establishing cross-functional teams enhances the effectiveness of the implementation process. These teams bring together diverse perspectives and expertise, which can improve the overall success of the digital transformation initiatives.
Ensuring Data Management and Infrastructure Readiness
Data management and infrastructure readiness are critical for the success of digital transformation initiatives. Real-time data collection and data analysis are crucial for informed data-driven decision-making during the manufacturing transformation process. Real-time data access improves synchronization between production steps. Effective data and analytics utilization provides insights that drive innovation and informed decision-making.
Organizations that invest in digital architecture can achieve better employee collaboration, reporting, and analytics. Evaluating and improving technology infrastructure is essential for successful digital transformation implementation. This includes assessing existing capabilities and infrastructure requirements to ensure digital transformation readiness.
Cloud computing enables manufacturers to monitor essential data such as production, material usage, and customer service, enhancing overall data management. Robust data security measures are necessary to protect critical information during digital transformation. Digital transformation leads to enhanced customer satisfaction due to improved delivery times.
Training and Upskilling the Workforce
Continuous training and upskilling of the workforce maintain a competitive edge in digital transformation initiatives. A focus on ongoing learning fosters a workforce that is adaptable, improving resilience and engagement in the face of change. Investing in employee training helps retain talent and drive overall digital transformation success. Manufacturers must develop training programs to address skill gaps related to new technologies during transformation.
Agility and adaptability are necessary for teams involved in digital transformation to keep up with evolving technologies. Many employees feel unprepared for new skill requirements brought about by digital transformation, making career advancement opportunities through skill enhancement crucial for future success and retention.
Upskilling enhances current abilities, while reskilling equips employees with new competencies for different roles. This dual approach ensures that the workforce is well-prepared to support the organization’s digital transformation goals.
Conducting Pilot Projects
Pilot projects are a strategic step in digital transformation initiatives. They:
-
Test and refine digital solutions before full-scale implementation.
-
Help organizations manage digital transformation more effectively.
-
Allow the workforce to adapt without disruption by being small-scale.
A clear timeline, budget, and scope of work are essential for the success of a pilot project. Outsourcing components of a pilot project can alleviate challenges and provide access to expertise not available internally.
After testing, organizations can start full-scale implementation and integration of successful implementation pilot projects. Feedback from pilot projects informs broader roll-out strategies, ensuring full-scale implementation is based on proven solutions and best practices, ultimately enhancing overall equipment effectiveness and supporting such initiatives.
Monitoring Progress and Making Adjustments
Monitoring progress and making adjustments are crucial for continuous improvement of digital transformation efforts. Key actions include:
-
Establishing key performance indicators (KPIs) to measure the success of digital transformation initiatives.
-
Regularly reviewing progress against objectives and KPIs to assess digital transformation advancement.
-
Identifying areas needing improvement based on the reviews.
A flexible digital transformation roadmap allows adjustments based on evolving business goals and technological advancements. Real-time monitoring of implementation enables prompt identification of issues and necessary changes, ensuring the transformation stays on course.
Benefits of a Well-Executed Digital Transformation Roadmap
A well-executed digital transformation roadmap offers significant long-term benefits, substantially improving a manufacturing digital transformation organization’s performance. Automating repetitive tasks enhances efficiency and frees up employees for more strategic responsibilities. Real-world examples, such as Beta Manufacturing Co. achieving a 40% increase in production efficiency and a 30% improvement in customer satisfaction scores, highlight the tangible benefits of digital transformation.
Digital transformation enhances product quality by minimizing rework and scrap, and improving data management and consistency through new digital processes and new technology to streamline processes. Driving digital transformation, a strong digital culture fosters increased efficiency, reduced costs, and improved product quality, providing a competitive advantage through enhanced customer experience and meeting market demand. Additionally, digital transformation in manufacturing plays a crucial role in these improvements, driven by digital transformation drivers. Robotic automation is utilized by manufacturers to perform repetitive tasks, improving reliability and production capacity, further contributing to these advancements.
Organizations undergoing digital transformation can expect improved profitability and reduced operational costs due to enhanced supply chain visibility, operational efficiency, and cost savings.
Overcoming Common Challenges
Overcoming common challenges is crucial for a successful transformation. Resistance to change can be a significant barrier, particularly among employees accustomed to traditional processes. Change management is a significant hurdle for manufacturers during digital transformation. A cultural transformation within the organization is crucial, as outdated mindsets can slow the adoption of new technologies. Manufacturers that haven't yet started their digital transformation journey can be recognized by their reliance on manual processes and traditional manufacturing methods, highlighting the need for a shift towards digital solutions.
A major challenge is the skill gap, as many companies struggle to find employees with the necessary technical expertise. Security threats increase with new digital solutions, necessitating strong cybersecurity measures. Budget limitations can impede the progress of digital transformation initiatives, especially for smaller businesses.
Summary
In summary, developing a digital transformation roadmap is crucial for guiding manufacturing organizations through their digital journey. By following the steps outlined in this guide, manufacturers can assess their current digital maturity, set clear objectives, prioritize digital technologies, and develop a comprehensive implementation plan.
The benefits of a well-executed digital transformation roadmap are significant, including improved operational efficiency, enhanced product quality, and a competitive advantage. Overcoming common challenges and continuously monitoring progress will ensure that digital transformation goals are met and sustained. Embrace the digital transformation journey and unlock the full potential of your manufacturing operations.
Frequently Asked Questions
Why is a digital transformation roadmap essential for manufacturing?
A digital transformation roadmap is essential for manufacturing as it effectively manages the transformation of processes and aligns with business objectives, ensuring a cohesive integration of digital initiatives across the organization. This structured approach enhances overall operational efficiency and customer experience.
What are the key elements of a successful digital transformation roadmap?
A successful digital transformation roadmap must have a clear vision and well-defined objectives along with a structured technology adoption approach. It should also include specific milestones, deliverables, timelines, budget planning, and a focus on reskilling personnel.
How can manufacturers assess their current digital maturity?
Manufacturers can effectively assess their current digital maturity by evaluating their technological capabilities, identifying operational inefficiencies, and analyzing the readiness of their infrastructure for digital transformation. This comprehensive approach enables a clear understanding of their digital standing and areas for improvement.
What role does training and upskilling the workforce play in digital transformation?
Training and upskilling the workforce are essential for the success of digital transformation, as they enhance adaptability, ensure effective technology adoption, and help retain talent. This strategic focus on continuous learning allows organizations to maintain a competitive edge in an evolving landscape.
How do pilot projects contribute to digital transformation?
Pilot projects significantly contribute to digital transformation by enabling organizations to test and refine digital solutions prior to full implementation, allowing for manageable adaptations and informed strategies based on feedback. This incremental approach minimizes disruption and enhances overall effectiveness.
Share this
You May Also Like
These Related Stories
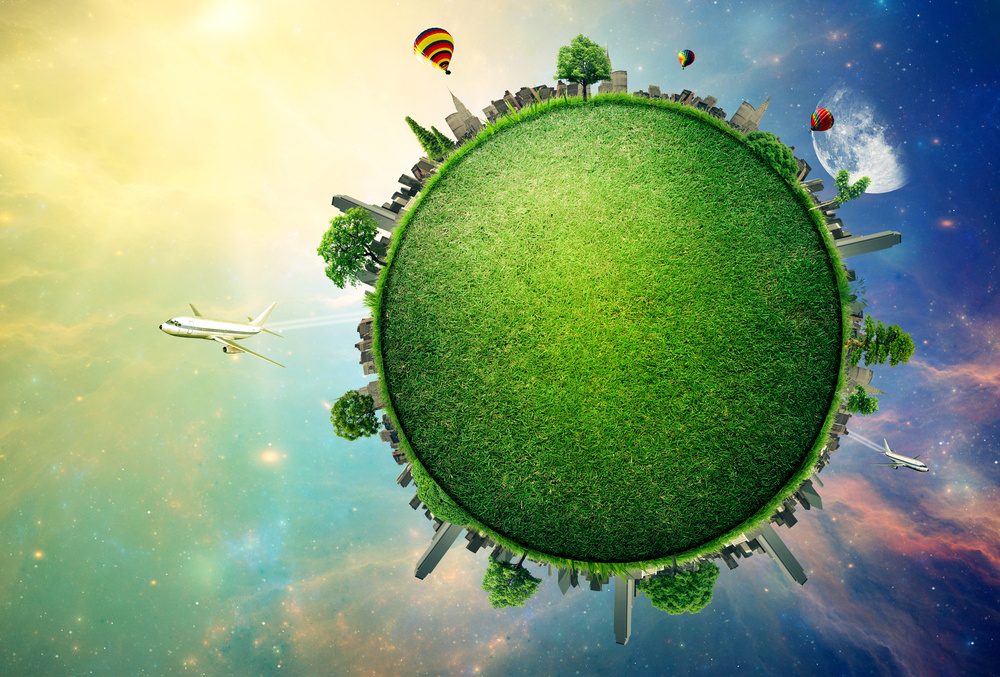
How to Achieve Sustainable Digital Transformation in Your Organization
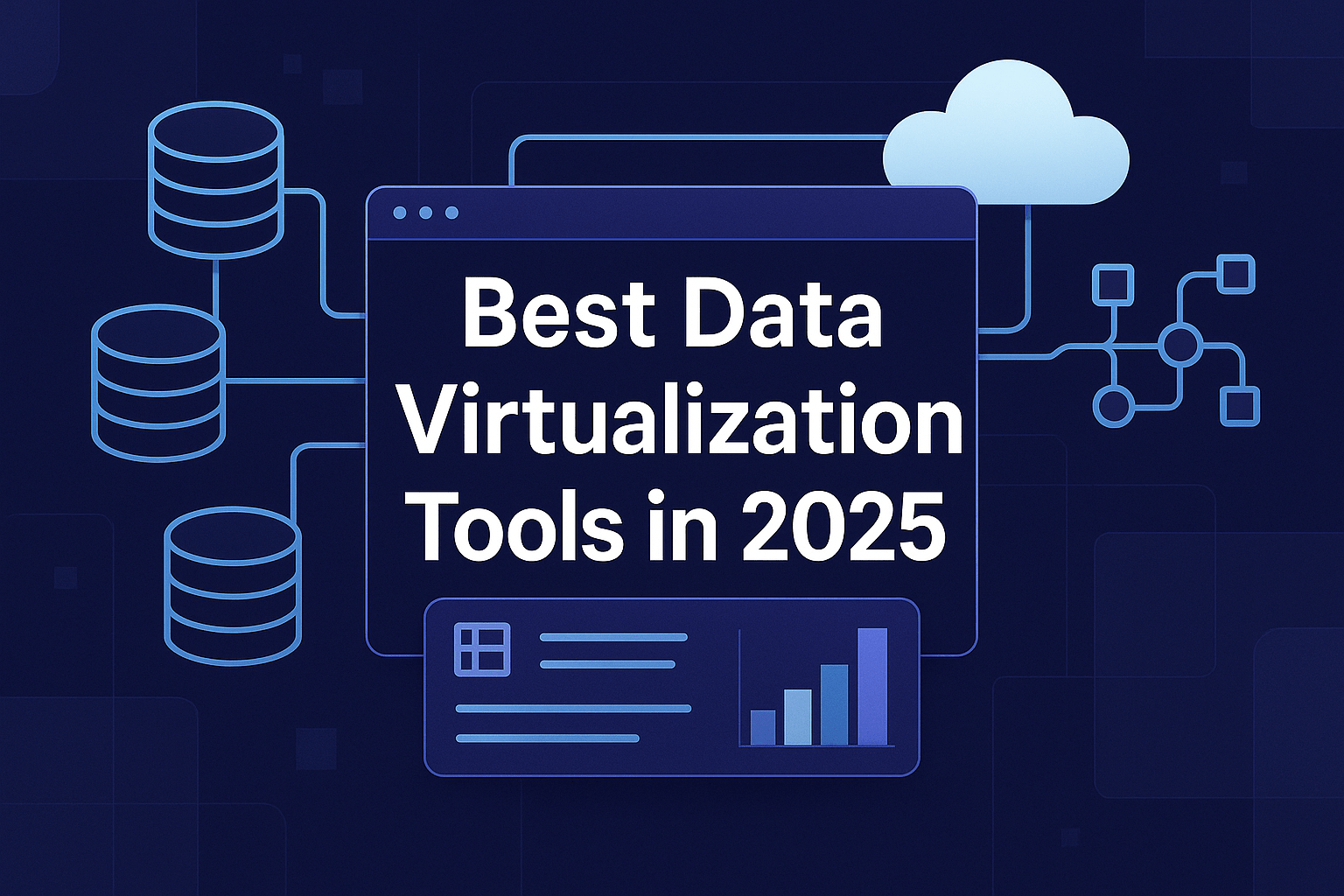
Best Data Virtualization Tools in 2025
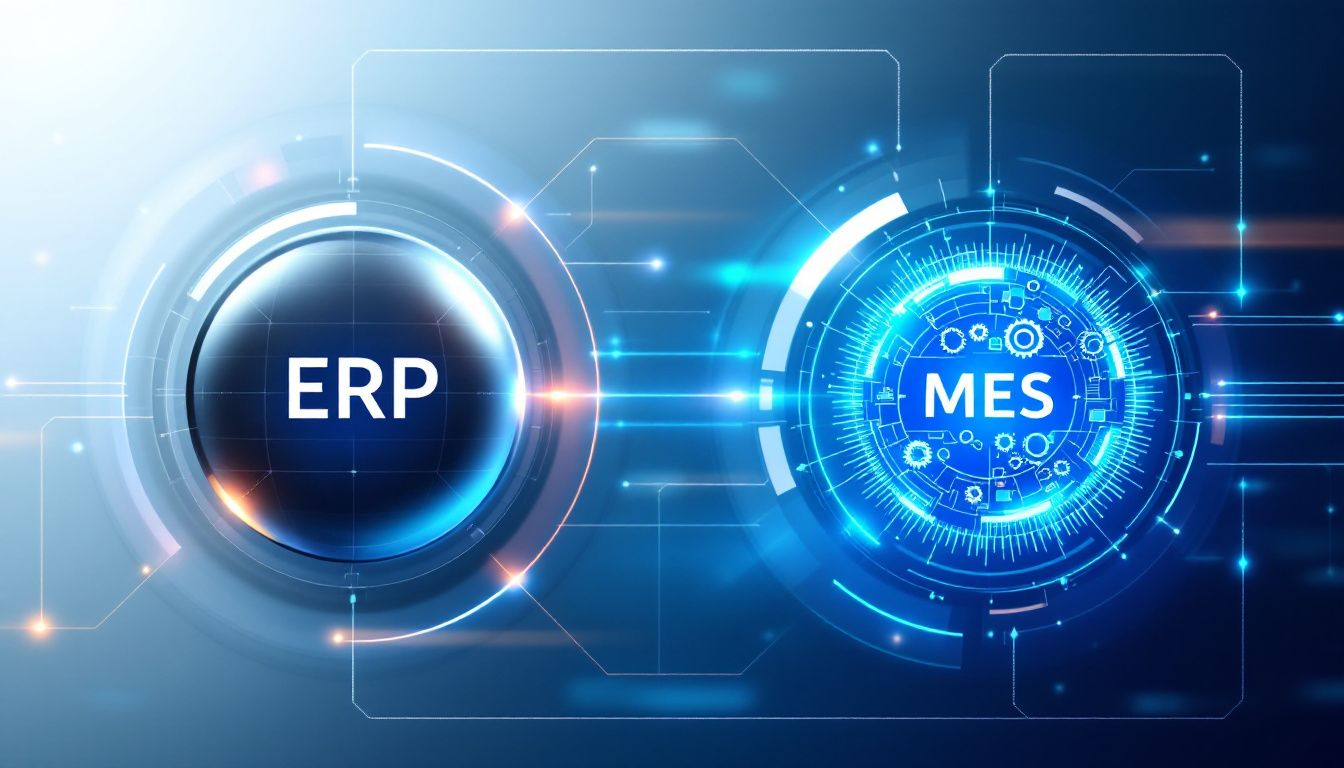
No Comments Yet
Let us know what you think