Quality Management System
A Quality Management System (QMS) enhances smart manufacturing by integrating advanced technologies and maintaining compliance with global standards, preparing for future environmental and regulatory needs.
This approach optimizes resource use, minimizes waste, and supports economic stability and quality of life.
Quality Management Challenges
Quality management in manufacturing faces challenges such as integrating advanced technologies, adapting to market and regulatory changes, and analyzing large volumes of data from connected devices.
Compliance with diverse global standards, managing complex supply chains, and human variability in quality assessments further complicate quality control. Maintaining high quality while managing costs requires strategic investments in technologies like Manufacturing Operations Management (MOM) systems.
.png?width=850&height=574&name=Smart%20manufacturing%20technologies%20close%20the%20loop%20on%20digital%20transformation%20journeys%20for%20organizations%20of%20all%20sizes.%20(1).png)
What Does a QMS Software Do?
A Quality Management System (QMS) is a framework that helps organizations consistently meet customer and regulatory quality standards.
It streamlines operations, reduces errors, and ensures continual improvement through documented processes and procedures. A QMS supports quality assurance activities like audits and corrective actions, and enhances decision-making with data-driven insights.
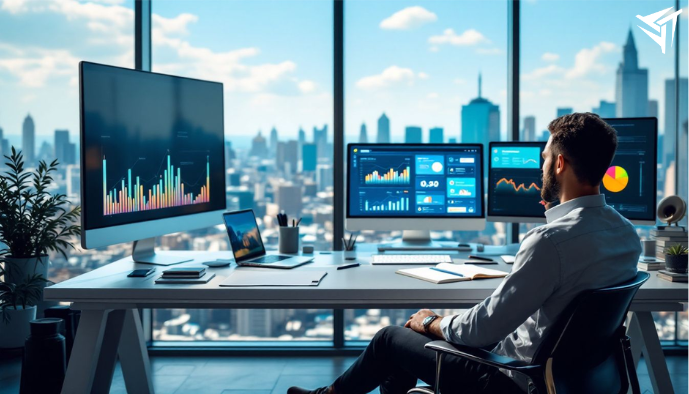
Features
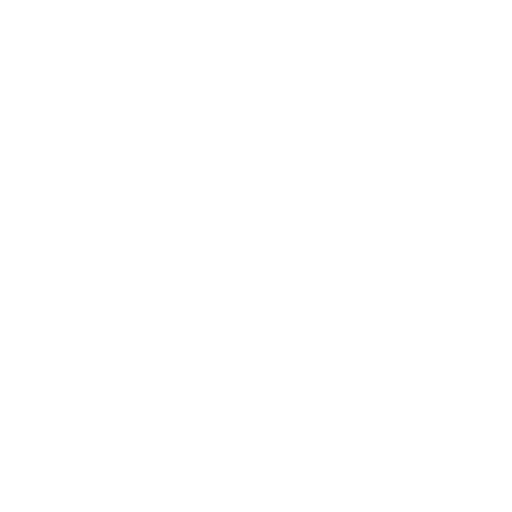
Document Control
Ensures all quality documentation, such as procedures, work instructions, and quality standards, are current and accessible. This system manages revisions and approvals to prevent the use of obsolete documents.
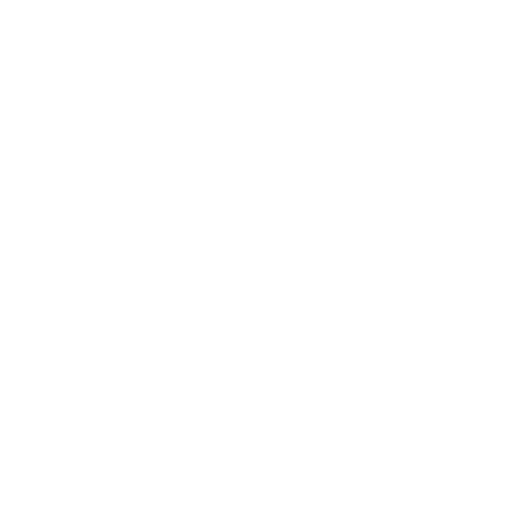
Quality Corrections
Allows manufacturers to identify, track, and manage corrective actions to address non-conformities and implement preventive measures to mitigate potential risks before they affect the quality.
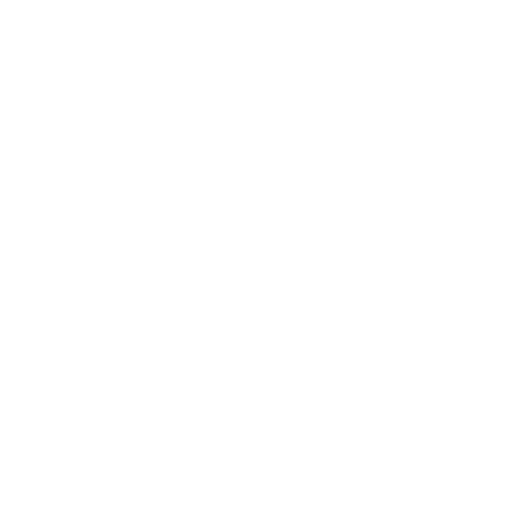
Audit Management
Facilitates the planning, execution, and follow-up of internal and external audits. This feature ensures compliance with regulatory standards and helps maintain certifications by systematically addressing any findings.
Benefits
Improved Product Quality
Standardized processes and strict controls ensure products meet quality standards and customer expectations.
Enhanced Customer Satisfaction
Reliable product quality reduces complaints and returns, boosting customer trust and satisfaction.
Regulatory Compliance
Ensures compliance with industry regulations, reducing legal risks and fines.
Efficiency and Cost Reduction
Streamlined processes lower operational costs by reducing rework and errors.
Data-Driven Decision Making
Analyzing quality data supports informed decisions for continuous improvement.
Competitive Advantage
A QMS differentiates manufacturers by demonstrating a commitment to quality.
Siemens Opcenter Quality
Snic Solutions is recognized as one of the elite organizations partnered with Siemens as a value-added reseller of Opcenter.
/About%20Page/Blake%20Digital%20Transformation%20Solutions.png?width=500&height=500&name=Blake%20Digital%20Transformation%20Solutions.png)

QMS Integration
Quality Management System (QMS) software plays a crucial role in the smart manufacturing ecosystem by integrating seamlessly with other systems like ERP, MES, MOM, and APS.
What happens when you integrate?
Integrating a Quality Management System (QMS) enhances data visibility and accuracy, facilitating seamless information flow across different functions. This interconnectivity ensures that actions in one area, like production adjustments or supplier changes, are reflected across all relevant systems, maintaining data integrity and consistency.
-1.png?width=600&height=508&name=SNic%20Solutions%20specializes%20in%20smart%20manufacturing%20solutions%20which%20include%20manufacturing%20operations%20management%2c%20detailed%20scheduling%2c%20and%20manufacturing%20execution%20systems.%20(1)-1.png)
From Our Blog
Stay up to date with what is new in our industry, learn more about the upcoming products and events.
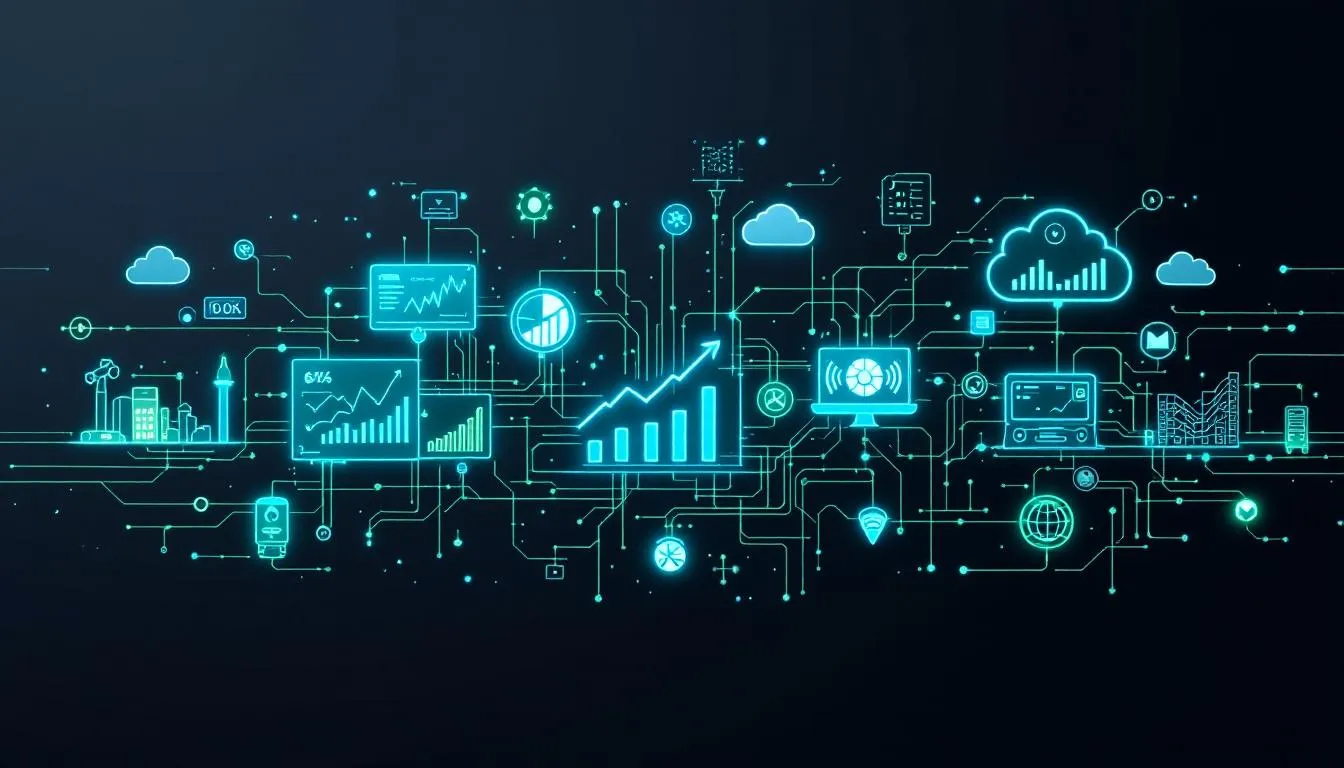
Maximizing Efficiency with Predictive Analytics in Manufacturing
Predictive analytics in manufacturing uses data to forecast trends and disruptions…
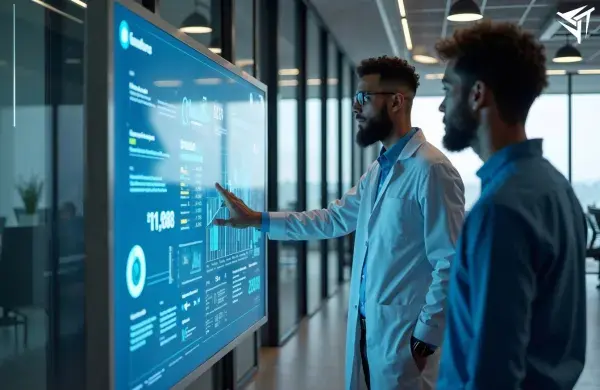
Lean Manufacturing Implementation Plan: 7 Steps to Success
Need to implement a lean manufacturing? A successful Lean manufacturing implementa…
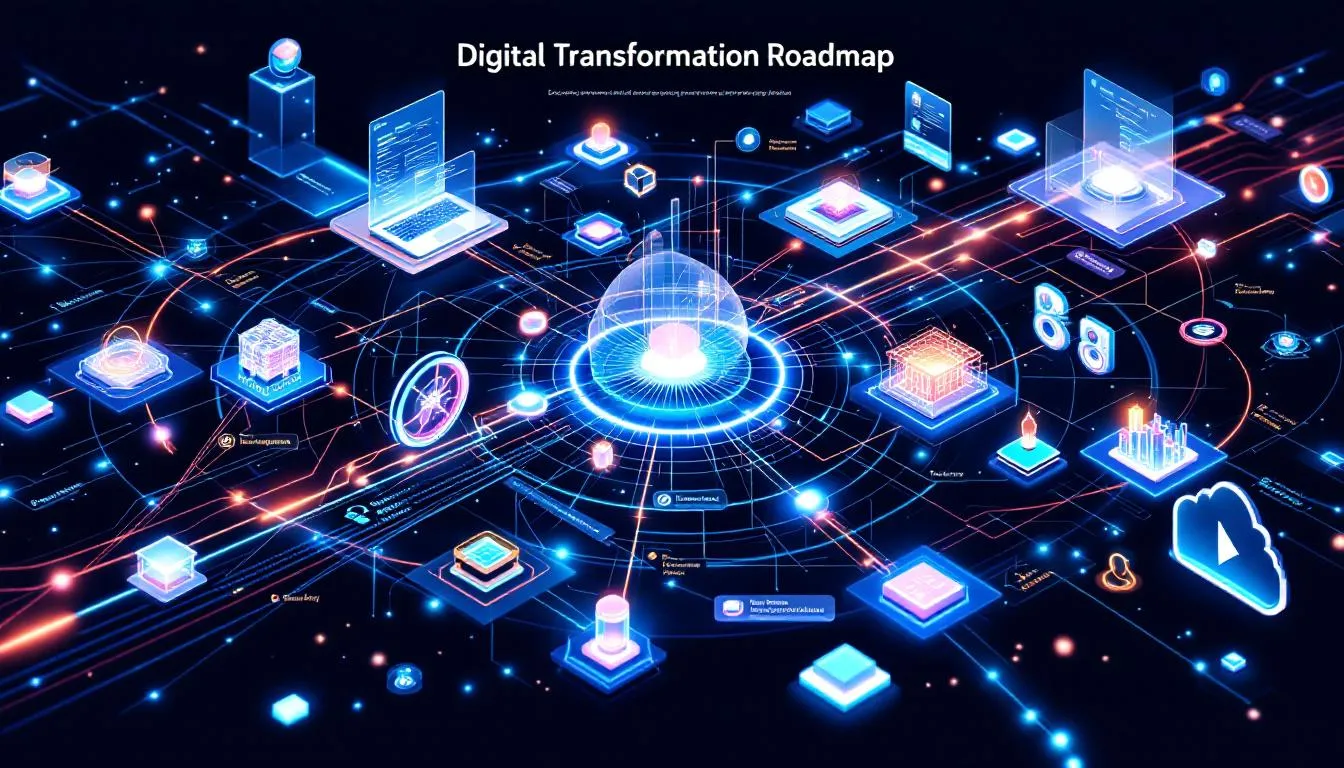
Ultimate Guide to Manufacturing Digital Transformation Roadmaps
Embarking on digital transformation in manufacturing? Start with a manufacturing d…
Frequently Asked Questions
Have Question? We are here to help
What makes a Quality Management System (QMS) crucial in manufacturing?
A Quality Management System (QMS) is crucial in manufacturing because it ensures consistent product quality, compliance with regulations, and encourages continuous improvement.
Can a QMS interface be customized to fit different manufacturing environments?
Yes, QMS platforms offer customizable interfaces and features to accommodate specific industry needs and organizational structures.
How does the 'Do' phase of the PDCA cycle work in a real-world scenario?
During the 'Do' phase of the PDCA cycle, pilot projects are used to test potential solutions on a small scale, allowing for data collection and minimal disruption, which is critical for assessing the changes' effectiveness.
What challenges might an organization face when implementing a QMS?
Implementing a QMS may pose challenges such as resistance to change, communication issues, financial constraints, and supplier resistance. Adaptive strategies and cultural shifts are necessary for successful implementation.
How does supplier management within a QMS contribute to customer satisfaction?
Supplier management within a QMS contributes to customer satisfaction by ensuring consistent delivery of high-quality products and services through the evaluation and monitoring of suppliers, which is essential for optimizing the supply chain.
Partner With Us To Reduce Your Technical Debt
Snic Solutions is recognized as one of the elite organizations partnered with Siemens as a value-added reseller of Opcenter.
/About%20Page/Blake%20Digital%20Transformation%20Solutions.png?width=500&height=500&name=Blake%20Digital%20Transformation%20Solutions.png)
