Essential Guide to Downtime Tracking for Better Efficiency
What is Downtime Tracking
Downtime tracking is crucial for manufacturers to reduce machine downtime and increase operational efficiency. Effective downtime tracking means you need to collect downtime data systematically to find the root causes and take corrective action. Collecting data, whether manually or automatically, is key to downtime tracking and ensures you have the information to analyse.
By tracking machine downtime you can:
-
Get actionable insights into operational inefficiencies
-
Improve equipment effectiveness
-
Cut costs associated with lost production time
-
Use downtime data to make better decisions and drive better outcomes
Downtime is the biggest productivity killer in manufacturing so downtime tracking is essential to boost overall efficiency. It’s also the largest source of lost manufacturing time for most companies, so reducing it is a key focus for operational improvement. A company that does downtime tracking can achieve big gains in productivity and equipment performance.
Why Downtime Tracking
Accurate downtime tracking is key to finding the real downtime causes such as equipment failure, operator error and unplanned maintenance. Knowing these downtime reasons allows you to:
-
Take proactive action to reduce downtime occurrences
-
Improve machine uptime and reliability
-
Achieve higher operational efficiency and lower production costs
Downtime tracking also helps companies get insight into the underlying reasons for downtime, so they can address the root causes and optimise performance.
By understanding real time data and capturing the true downtime, you can make informed decisions to boost productivity and employee morale. True downtime includes both tangible losses, such as lost production, and intangible losses, such as reduced employee morale or customer dissatisfaction, and means capturing all aspects of downtime, including hidden or underestimated costs. Connected devices provide data, analytics, reports and communication tools to tackle production problems.
Types of Equipment Downtime
Understanding the different types of equipment downtime is key to machine downtime tracking and analysis. Equipment downtime can be categorised into three main types: unplanned downtime, planned downtime and production downtime.
Unplanned downtime is when a machine or equipment stops working unexpectedly, often due to equipment failure, operator error or unforeseen issues. This type of downtime is the most disruptive as it stops production and can lead to big losses if not addressed quickly.Planned downtime is scheduled in advance for activities such as maintenance, upgrades or inspections. While planned downtime is necessary to keep machines running smoothly, tracking it ensures maintenance is done efficiently and doesn’t overrun and impact production schedules.
Production downtime is when machines are not producing, even though they are not broken or under maintenance. This can happen due to lack of raw materials, changeovers or other process related delays. By tracking production downtime companies can identify bottlenecks and optimise workflows to maximise machine utilisation.
By categorising and tracking each type of equipment downtime, manufacturers can get deeper insight into when and why downtime occurs, so they can target maintenance better, allocate resources better and improve overall equipment effectiveness.
Data Collection Methods
Downtime data collection methods are manual logging and automated data collection:
-
Manual Data Collection: Operators log downtime events manually which can be prone to errors and inconsistencies due to human error. Manual methods often result in uncontextualised data making it difficult to interpret and analyse production performance accurately.
-
Automated Data Collection: Downtime tracking software linked to machine control systems to track downtime events in real time. Software linked to a machine’s control system ensures accurate start and stop times are tracked automatically for all downtime events. Automated data collection eliminates human error and allows for actionable analysis through focused reports. The data collected through automated systems is the foundation for comprehensive analysis and reporting.
Automated downtime tracking is more reliable and ensures accurate tracking of downtime start and stop times, makes data more accurate and reliable. For companies looking for economical options, low cost solutions such as data loggers are available for downtime tracking.
Downtime Tracking Tools
Implementing downtime tracking software and tools helps manufacturers to monitor and analyse downtime:
-
Downtime Tracking Software: A downtime tracking system is a data collection tool, automates real time tracking of downtime events and improves responsiveness and decision making.
-
Pareto Charts and Analytical Tools: Enables clear visualisation and prioritisation of downtime reasons, focus maintenance resources on the most impactful issues. Downtime reporting should be visual and easy to understand to facilitate actionable insights.
Tracking key metrics such as downtime, OEE, MTBF and MTTR is essential for continuous improvement and understanding operational issues.
Automated downtime tracking tools allows structured categorisation and reporting, gives manufacturers the insights to proactively manage downtime.
Real-Time Tracking
Real-time tracking is a game changer for machine downtime tracking, allows companies to monitor and respond to downtime events as they happen. With advanced downtime tracking software and automated downtime tracking systems, operators and managers get instant alerts when a machine stops, so issues are addressed before they become major disruptions.
By tracking machine downtime in real time, companies can quickly identify the root cause of downtime events, whether it’s equipment failure, process inefficiency or operator error. This immediate visibility into downtime data allows teams to take swift corrective action, reduce lost production time and minimize impact on operational efficiency.
Real-time tracking also allows companies to spot recurring patterns and trends in downtime events, so they can implement proactive maintenance strategies and prevent future occurrences. Leveraging real time data from automated systems helps optimise production processes, improve equipment effectiveness and drive continuous improvement across the plant floor.
With real-time monitoring, companies can ensure every minute of machine downtime is tracked, analysed and addressed, resulting in higher productivity, lower costs and a more efficient manufacturing operation.
Downtime Analysis
Downtime analysis gives you insights into patterns, trends and common downtime reasons. Accurate analysis is key to identifying downtime patterns and data integrity, which leads to better decision making.
Analysis involves:
-
Identifying the most frequent downtime events such as equipment failures, operator errors or planned stoppages and measuring the duration of each event to capture how long downtime lasts
-
Optimising planned maintenance schedules and other planned stoppage categories to minimise downtime and maximise machine uptime
-
Defining clear downtime reason codes for operator reporting, makes data more clear and actionable. Tracking and analysing the differential between planned and actual downtime identifies root causes and helps you plan future improvements in equipment effectiveness. This approach allows manufacturers to identify specific areas to improve and take targeted action to boost productivity.
Machine Downtime
Machine downtime tracking is the process of tracking machine downtime events on individual machines or equipment.
Benefits:
-
Identify machine specific downtime patterns to address unique issues
-
Reduce lost production time through timely maintenance and interventions
-
Improve overall operational efficiency by addressing inefficiencies at machine level
Machine specific tracking means focused resource allocation and targeted improvements, ultimately increases production output and profitability.
Downtime Events
Categorizing each downtime event is key to effective downtime management. Proper categorization of downtime events allows aggregated data analysis to identify patterns and trends for better decision making. Using a centralized system to collect machine data provides clear differentiation between planned downtime and exceedances to that plan.
-
Planned Downtime: Intentional (i.e., scheduled) pause during planned production time, such as maintenance or equipment upgrades.
-
Unplanned Downtime: Unexpected stoppages, including machine failures or operator errors, causing significant disruptions and lost productivity. When a planned stop runs longer than the target time, it may transition into unplanned downtime.
Accurate downtime tracking software helps manufacturers to identify and mitigate unplanned downtime events by providing clear, contextualized, real time data. Unplanned downtime is any time when your line stops unexpectedly. Knowing these downtime events allows companies to proactively manage their resources and minimize downtime occurrences, driving sustained productivity and operational efficiency improvements.
Automated Data Collection
Automated data collection is the foundation of modern downtime tracking. By capturing real time data on equipment stoppages and the reasons behind them, these systems provide a precise and consistent view of production performance. Companies that automate their data collection are often surprised by their true levels of downtime, as automated systems reveal hidden inefficiencies and underestimated stoppages that manual methods might miss.
Instead of relying on manual input—which is prone to delays and errors—automated systems instantly record downtime events, trigger alerts and enable immediate corrective action. This improves responsiveness and empowers teams to reduce unplanned stoppages. Automated data collection via machine monitoring addresses many problems encountered with manual methods, ensuring more reliable and actionable data.
Also automated data collection improves reporting quality. It allows manufacturers to generate actionable insights, spot recurring issues and make data driven decisions to drive continuous improvement. Collecting actionable insights from downtime data requires compiling it into reports that can be easily accessed and queried.
Additionally, automated data collection enables analysis of downtime patterns across different shifts, helping identify inefficiencies and bottlenecks specific to each work period.
Equipment Downtime Reduction
Reducing equipment downtime is one of the fastest way to increase productivity and reduce costs. Monitoring total downtime as a key metric helps identify improvement opportunities and prioritize actions. With accurate tracking in place, teams can analyze the causes of downtime and take targeted action to eliminate them. This approach is often the quickest way to improve Overall Equipment Effectiveness (OEE) scores.
For example downtime data can show patterns of equipment failures, teams can adjust maintenance schedules, upgrade machinery or improve operator training. Manufacturers often experience excessive tool changeover as a common category of unplanned downtime.
Reducing downtime leads to:* More machine uptime
-
Better labor and material utilization
-
Better OEE
Best Practices for Downtime
To get the most out of your downtime:
-
Use automated tools
-
Log downtime and root cause for analysis.
-
Set goals for what you want to achieve—uptime, OEE or unplanned stoppages.
-
Train operators, technicians and employees as key contributors to downtime tracking.
-
Visualize the data through dashboards and reports to take action.
-
Analyze by shift to identify specific issues, such as downtime patterns or inefficiencies during certain shifts.
Analysis should be part of daily operations—not just when problems arise.
Downtime Implementation
To implement downtime:
-
Choose the right system for your plant size and complexity.
-
Train your team on how to use the system and read the data.
-
Set KPIs and goals for downtime reduction, OEE improvement or specific asset performance.
-
Create a feedback loop—use the data to drive continuous improvement and keep teams engaged with regular updates.
Downtime can be a driver of operational excellence.
Conclusion
Downtime tracking isn’t just a maintenance activity—it’s a growth strategy. By automating data collection and analyzing regularly manufacturers can achieve more efficiency, reduce operational costs and gain competitive advantage. In today’s fast paced production environments even small downtime reductions can have a big impact on output, quality and profitability. Minimizing downtime also helps factory teams morale as smoother operations reduce stress and increase job satisfaction.
FAQs
What is downtime tracking?
Downtime tracking is the act of monitoring and recording when and why equipment stops working during production.
How do you measure downtime?
Downtime is measured in minutes or hours and is calculated as a percentage of total scheduled production time. For example if equipment is down for 1 hour during an 8 hour shift that 1 hour of downtime would reduce the uptime percentage accordingly.
How much downtime is 99.9% uptime?
99.9% uptime is 43.8 minutes of downtime per month.
How do you log machine downtime?
Machine downtime can be logged manually via logs or spreadsheets but automated systems are more accurate and scalable.
Share this
You May Also Like
These Related Stories
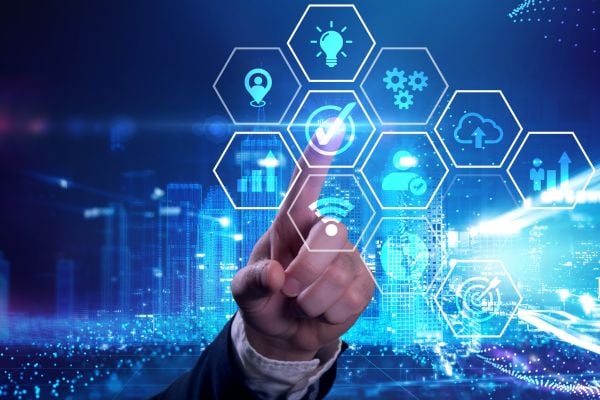
IoT Integration: A Complete Guide to Connecting Smart Devices and Systems
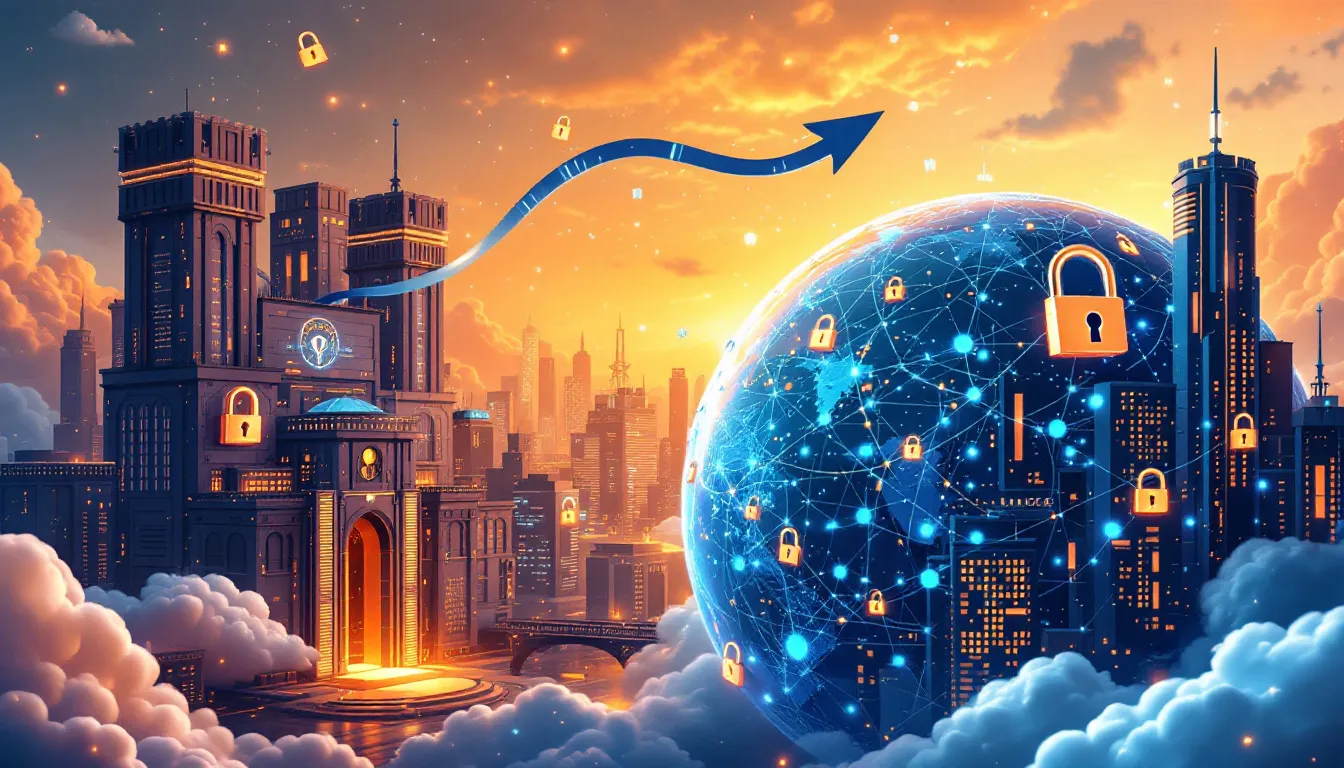
Data Virtualization vs Data Warehouse: Essential Differences Explained
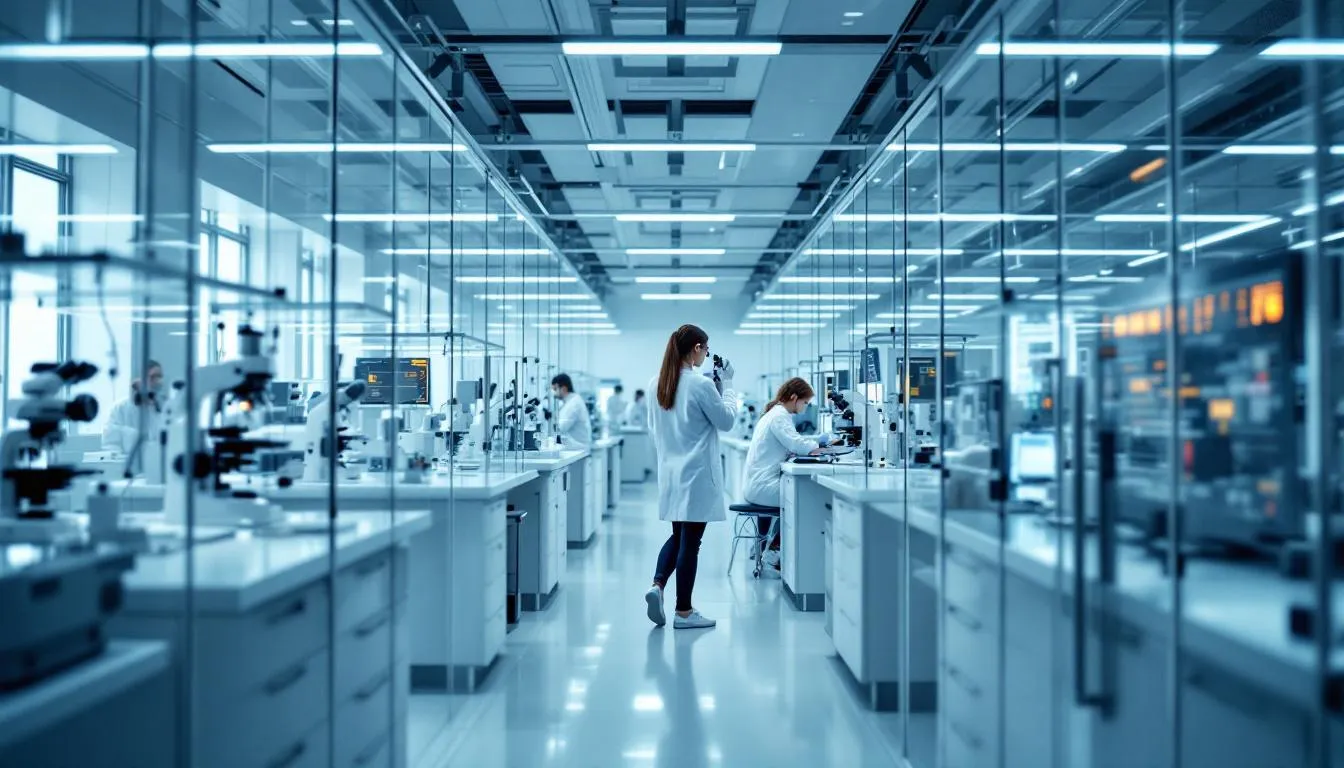
No Comments Yet
Let us know what you think