How to Achieve Sustainable Digital Transformation in Your Organization
Introduction to Sustainable Manufacturing
Sustainable manufacturing is a critical aspect of achieving a sustainable future. It involves leveraging digital technologies to optimize energy consumption, reduce waste, and promote environmentally friendly practices throughout the production process.
By embracing sustainable manufacturing, companies can significantly reduce their environmental impact while simultaneously improving operational efficiency, reducing costs, and enhancing their brand reputation.
Digital transformation plays a pivotal role in this journey. By integrating advanced digital technologies, manufacturers can streamline their operations, making them more resource-efficient and less harmful to the environment. This not only aligns with sustainable development goals but also positions companies as leaders in sustainability initiatives.
What is Sustainable Manufacturing
Sustainable manufacturing is the implementation of practices and processes that have minimal impact on the environment and maximise resource efficiency. This means reducing waste, conserving energy and using renewable resources. Now you know the principles and goals of sustainable manufacturing, you can make informed decisions to make a change.
One of the key aspects of sustainable manufacturing is cleaner production. This means using technologies and practices that reduce pollution and waste throughout the product lifecycle. It also means responsible sourcing of materials and circular economy principles.
Plus sustainable manufacturing creates a safe and healthy work environment for employees. This means worker safety, training and fair labour practices. By looking after employees we can create a more sustainable and socially responsible workplace.
Challenges to Sustainability and Environmental Impact
Despite the importance of sustainable manufacturing there are challenges to achieving your sustainability goals. One of the biggest is the cost of implementing sustainable practices and technologies. While these will have long term benefits the upfront cost can be high and for some manufacturers it’s hard to prioritise sustainability.
Another challenge is the complexity of the supply chain in manufacturing. Many manufacturers have a network of suppliers and partners so it’s hard to ensure sustainability standards are met across the whole supply chain. Collaboration and transparency is key to addressing this challenge and driving sustainability across the industry.
And there can be resistance to change within the organisation. Some decision makers may be reluctant to adopt new technologies or change existing processes if they see it as disrupting their business. Overcoming this resistance requires good communication and education on sustainable manufacturing.
Finally measuring and tracking progress towards sustainability goals can be hard. It requires collecting and analysing data from multiple sources which can be time consuming and complex. But with digital transformation technologies we can simplify this process and give decision makers the insights to drive continuous improvement.
Benefits of Digital Transformation
One of the most significant advantages of digital transformation is enhanced operational efficiency. Manufacturers can optimize processes, reduce downtime, and boost overall productivity by leveraging digital technologies. This leads to cost savings, reduced resource consumption, and minimized environmental impact.
Digital transformation also provides increased visibility and transparency across the supply chain. Manufacturers can track and trace materials, components, and products throughout their entire lifecycle, ensuring sustainability standards are met and responsible sourcing is practiced. This transparency fosters better collaboration and communication with suppliers, partners, and customers, driving sustainability throughout the value chain.
By utilizing data analytics and machine learning algorithms, manufacturers can identify potential issues before they occur and take preventive action. This not only improves operational efficiency but also extends equipment life, reducing the need for replacements and waste.
Technologies like 3D printing and product lifecycle management software allow manufacturers to design products for disassembly and recycling, closing the material loop and reducing waste. This approach not only offers environmental benefits but also opens up new business opportunities and fosters innovation.
Digital Transformation Initiatives
Digital transformation initiatives are crucial for achieving sustainable development goals. By leveraging digital technologies such as cloud computing, machine learning, and the Internet of Things (IoT), companies can optimize energy consumption, reduce waste, and promote sustainable practices throughout their operations. These initiatives help companies understand their environmental impacts and identify areas for continuous improvement.
For example, implementing energy-efficient technologies like LED lighting and smart HVAC systems can significantly reduce energy usage. Data analytics can be employed to monitor and optimize energy consumption, ensuring efficient resource use. Additionally, sustainable supply chain practices, such as sourcing materials from environmentally responsible suppliers, can further minimize the environmental footprint.
By utilizing IoT sensors and data analytics, companies can monitor water usage in real-time and implement measures to reduce consumption. These digital transformation initiatives are not merely about compliance; they are about creating a sustainable future through innovative and responsible practices.
Industry-Specific Strategies
Different industries face unique sustainability challenges and opportunities. Here are some tailored strategies for achieving sustainable development goals across various sectors:
-
Manufacturing: Implement sustainable manufacturing practices by using renewable energy sources, reducing water consumption, and promoting recycling and waste reduction. Digital technologies can help monitor and optimize these processes, ensuring maximum efficiency and minimal environmental impact.
-
Retail: Adopt sustainable supply chain practices by sourcing materials from environmentally responsible suppliers, reducing energy consumption in stores and warehouses, and promoting sustainable packaging practices. Digital tools can enhance transparency and traceability, ensuring that sustainability standards are met throughout the supply chain.
-
Finance: Embrace sustainable investment practices by investing in environmentally responsible companies and promoting sustainable financial products. Reducing energy consumption in office operations and leveraging digital platforms for paperless transactions can also contribute to sustainability goals.
-
Healthcare: Implement sustainable healthcare practices by reducing energy consumption in medical facilities, promoting sustainable medical supply chain practices, and minimizing waste. Digital technologies can support these efforts by providing real-time data and analytics to optimize resource use and reduce environmental impact.
By adopting these industry-specific strategies, companies can make significant strides towards achieving their sustainable development goals.
MOM Software: Enabling Sustainability in Digital Manufacturing
In the journey toward sustainable manufacturing, Manufacturing Operations Management (MOM) software serves as a critical tool for bridging the gap between digital transformation and environmental responsibility. By streamlining operations, optimizing resource utilization, and offering actionable insights, MOM software helps manufacturers meet sustainability goals efficiently.
How MOM Software Contributes to Sustainable Manufacturing
-
Resource Efficiency and Waste Reduction:
MOM software monitors production processes in real-time, identifying inefficiencies and minimizing waste. By analyzing data across operations, manufacturers can reduce raw material usage, optimize energy consumption, and lower their environmental footprint. -
Energy Management and Optimization:
Through integration with IoT devices and energy monitoring tools, MOM software helps track energy consumption at each stage of production. This allows manufacturers to pinpoint energy-intensive processes and make data-driven adjustments to reduce overall energy waste. -
Predictive Maintenance for Equipment Longevity:
MOM software incorporates predictive maintenance features powered by AI, allowing manufacturers to detect and resolve equipment issues before they result in failures. This minimizes unplanned downtime, extends machinery lifespan, and reduces the need for resource-intensive replacements. -
Supply Chain Transparency and Traceability:
MOM software enables end-to-end visibility across the supply chain, ensuring responsible sourcing of materials and adherence to sustainability standards. Manufacturers can trace the origin of raw materials, monitor logistics, and reduce emissions associated with transportation and wasteful supply chain practices. -
Circular Economy Integration:
MOM software supports circular economy principles by facilitating product lifecycle management. It tracks materials, components, and finished goods throughout their lifecycle, enabling manufacturers to plan for reuse, recycling, and waste minimization. -
Data-Driven Sustainability Metrics:
MOM software offers advanced analytics dashboards, allowing manufacturers to measure and track key sustainability metrics such as carbon emissions, energy consumption, and waste reduction. These insights empower decision-makers to set measurable sustainability goals and monitor progress in real time. -
Improved Compliance and Reporting:
Sustainability regulations are becoming more stringent worldwide. MOM software simplifies compliance by automating environmental reporting and ensuring adherence to industry standards and best practices.
Why MOM Software is Key for Sustainable Digital Transformation
-
Holistic Data Insights: Centralizes data from multiple sources for better decision-making.
-
Operational Efficiency: Streamlines workflows to reduce waste and energy usage.
-
Real-Time Monitoring: Tracks environmental impact metrics continuously.
-
Scalability: Adapts to growing sustainability requirements and business needs.
-
Compliance Ready: Simplifies adherence to sustainability standards and regulations.
Empowering a Greener Future with MOM Software
MOM software is not just a tool for operational efficiency—it’s a foundation for sustainable growth. By aligning digital transformation strategies with environmental goals, MOM software empowers manufacturers to build a resilient, resource-efficient, and environmentally responsible future.
Investing in MOM software is not only a step towards smarter manufacturing but also a commitment to a sustainable planet.
Measuring Impact
Measuring the impact of sustainability initiatives is critical for achieving sustainable development goals. Companies can use various metrics to assess their environmental impacts and track progress. Key metrics include:
-
Carbon Footprint: Measure the amount of greenhouse gas emissions produced by a company’s operations. This helps identify areas where emissions can be reduced and track progress over time.
-
Water Usage: Monitor the amount of water used in operations. By understanding water consumption patterns, companies can implement conservation measures and reduce their overall usage.
-
Waste Reduction: Track the amount of waste generated and reduced through various initiatives. This metric helps companies identify successful waste reduction strategies and areas for further improvement.
-
Energy Consumption: Measure the amount of energy used in operations. Optimizing energy consumption not only reduces costs but also minimizes environmental impact.
By using these metrics, companies can gain valuable insights into their sustainability initiatives, set measurable goals, and continuously improve their environmental performance. This data-driven approach ensures that sustainability efforts are effective and aligned with broader sustainable development goals.
Future of Digital Transformation for Sustainable Manufacturing
As technology moves forward there are several future trends in digital transformation for sustainable manufacturing.
One of them is the use of artificial intelligence (AI) and machine learning (ML) in manufacturing optimisation. AI and ML can analyze vast amounts of data in real-time, and find patterns and anomalies that humans can’t. By using AI and ML you can be more resource efficient and reduce waste.
Another is the use of blockchain for supply chain transparency. Blockchain is a decentralized and immutable ledger for secure and transparent transactions. By using blockchain in the supply chain you can have product traceability and authenticity and reduce counterfeiting.
Augmented reality (AR) and virtual reality (VR) are being integrated into manufacturing operations. AR and VR can provide real-time information and guidance to operators to be more efficient and reduce errors. These technologies can also enable remote collaboration and training and reduce the need for travel and carbon footprint of manufacturing operations.
Digital twins will be connected to more IoT devices so real-time monitoring and control of physical assets will be possible. You can then optimize your operations and make data-driven decisions for sustainability.
So all good! AI, blockchain, AR/VR and digital twins.
FAQs
What is sustainable digital transformation?
Sustainable digital transformation is the integration of digital technologies and processes to increase operational efficiency and reduce environmental impact. It’s about using digital to achieve sustainability goals like reducing energy consumption, optimise resource use and lower carbon emissions. By embedding sustainability into digital transformation you can drive long term success and a more sustainable future.
How do you achieve digital transformation?
Digital transformation can be achieved by taking a strategic approach and adopting modern technologies like cloud, data analytics and artificial intelligence. Focus on increasing operational efficiency, energy usage and resource efficiency. Invest in digital skills and a culture of innovation and you’ll navigate the transition to a digital and sustainable economy.
What are the 5 pillars of digital transformation?
The 5 pillars of digital transformation are:
-
Customer Experience: Digitalising customer interactions and engagement.
-
Operational Efficiency: Digitalising processes and productivity.
-
Business Model Innovation: Creating new revenue streams and business models through digital innovation.
-
Data-Driven Decision Making: Using data insights and analytics to inform decisions.
-
Digital Culture and Skills: A culture that accepts digital change and upskills employees.
How do you go digital?
To go digital, organisations should embed sustainability into their digital transformation. This means optimise energy use, reduce waste and minimise the environmental impact of digital. By using energy efficient devices, cloud and predictive maintenance you can reduce your environmental impact and grow sustainably.
Share this
You May Also Like
These Related Stories
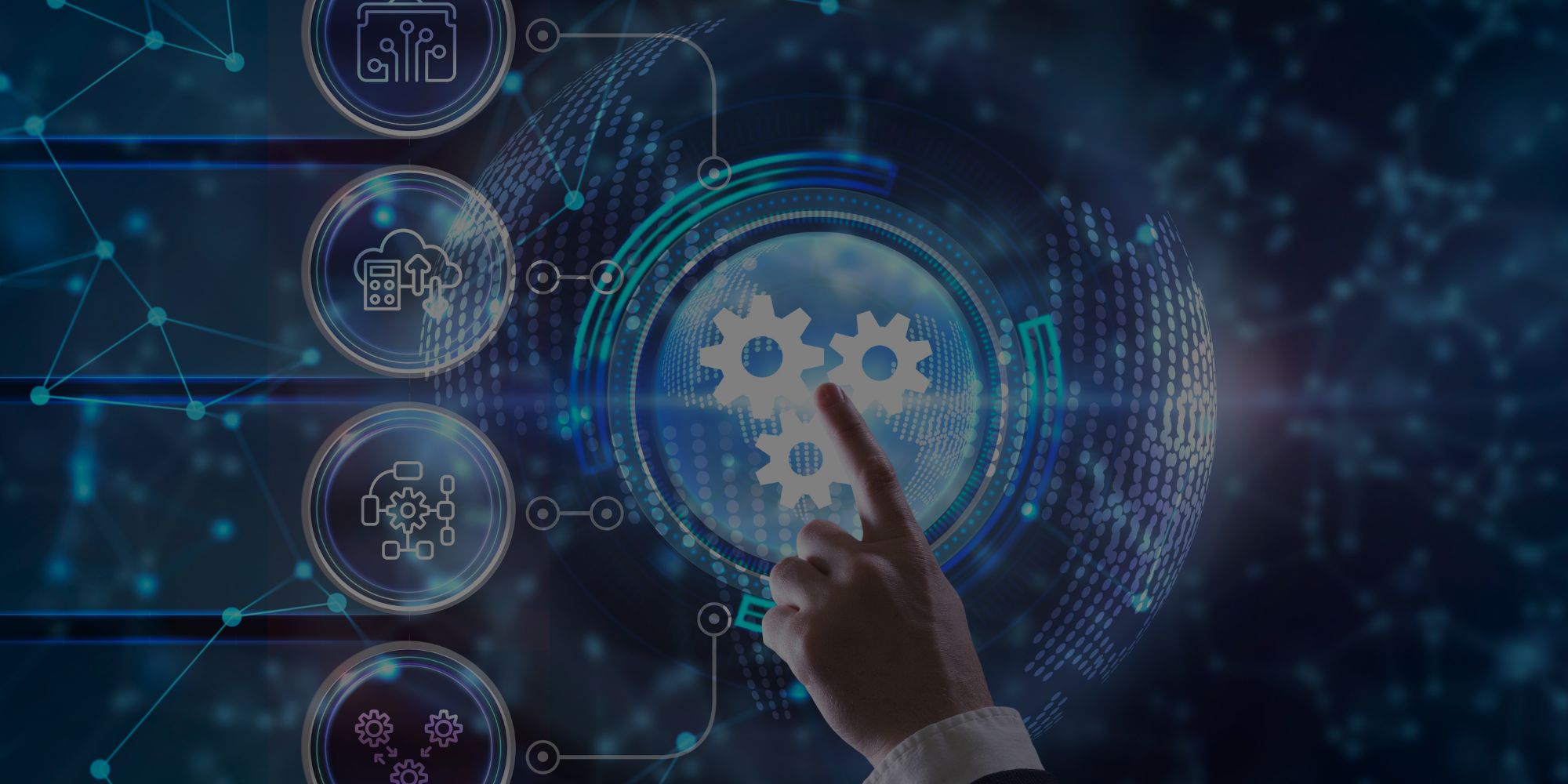
Manufacturing Operations Technology is Changing the Modern Factory
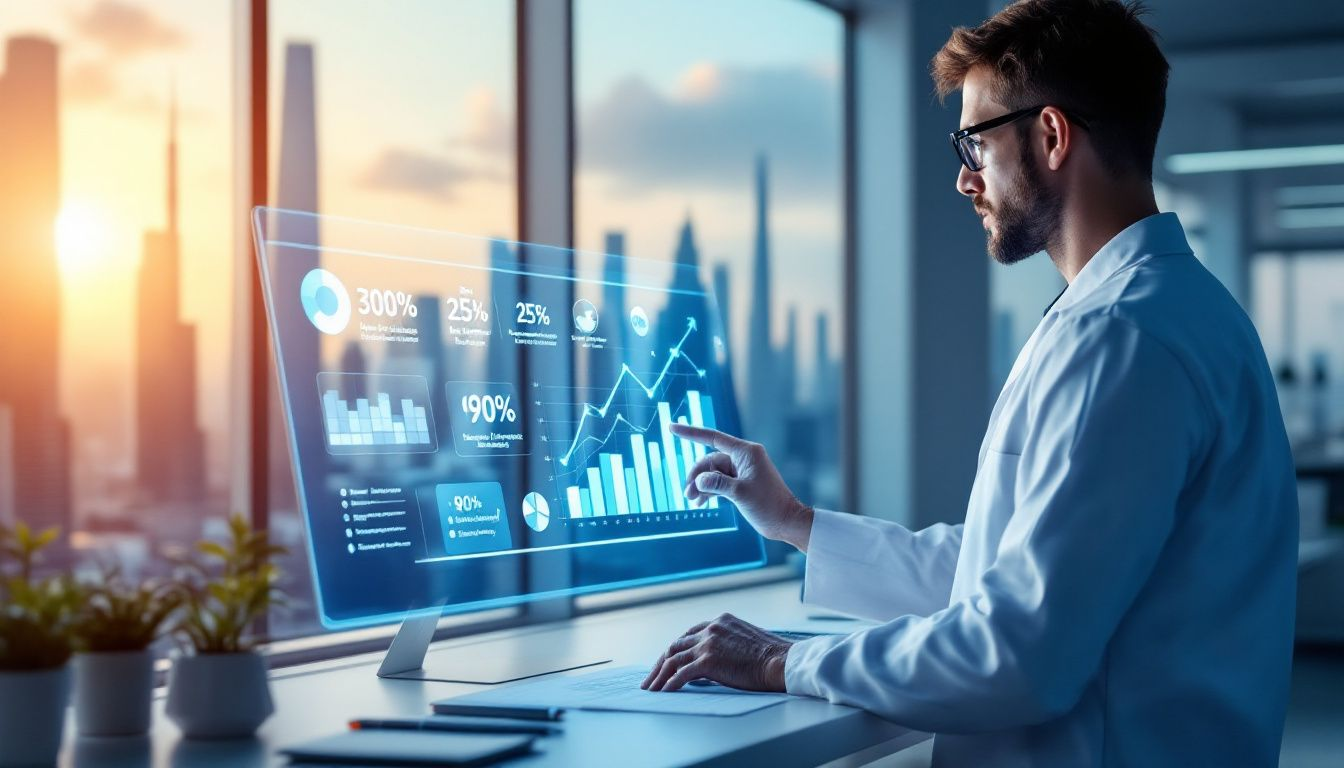
Top 7 Advantages of LIMS for Modern Laboratories
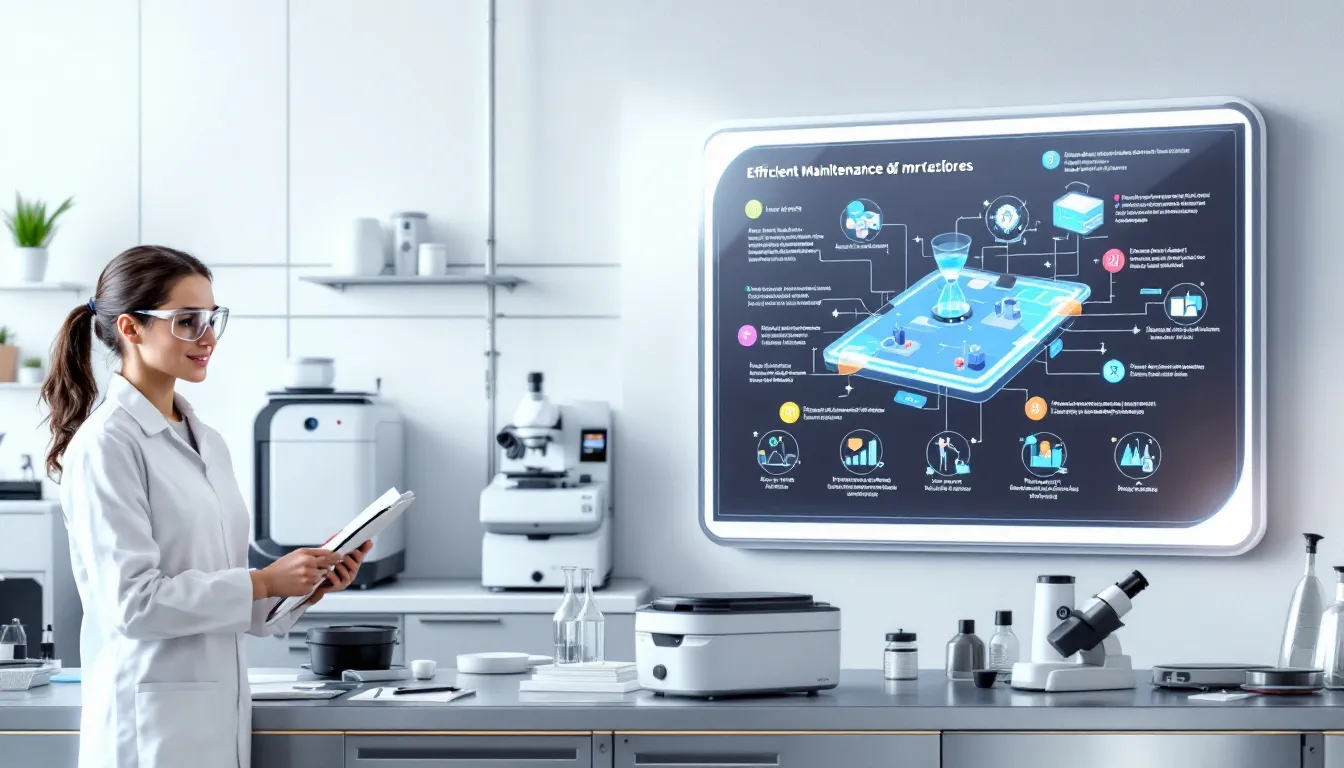
No Comments Yet
Let us know what you think