Advanced Planning and Scheduling
An Advanced Planning and Scheduling (APS) system enhances smart manufacturing by optimizing production plans and schedules, ensuring efficient resource utilization and on-time delivery.
By integrating advanced algorithms and real-time data, APS can quickly adapt to changes in demand, production capacity, and supply chain disruptions.
Production Planning & Scheduling Challenges
Manufacturers can face challenges such as balancing demand forecasts with production capacity, ensuring timely material procurement, and optimizing resource utilization to avoid delays and bottlenecks.
Unforeseen disruptions like machine breakdowns and supply chain issues further complicate the process. Maintaining efficiency while adapting to changing market demands requires strategic investments in advanced planning and scheduling (APS) systems to provide structured forecasting, resource allocation, and real-time monitoring.
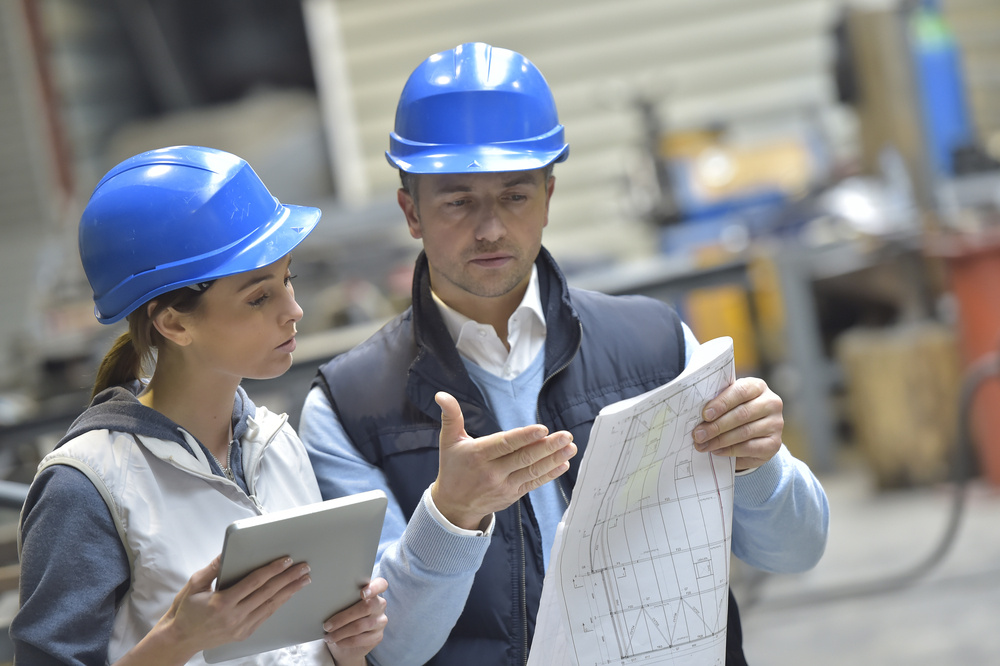
What Does a APS Software Do?
APS (Advanced Planning and Scheduling) software optimizes production planning by considering constraints like capacity, lead times, and material availability. It ensures efficient resource use and prevents overloading, keeping production schedules on track.
Additionally, APS software monitors material availability and adjusts schedules based on inventory levels and anticipated deliveries. It factors in machine maintenance, workforce availability, and deadlines to minimize production costs and enhance overall efficiency.
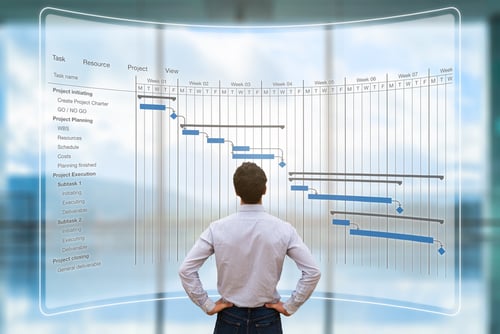
Features
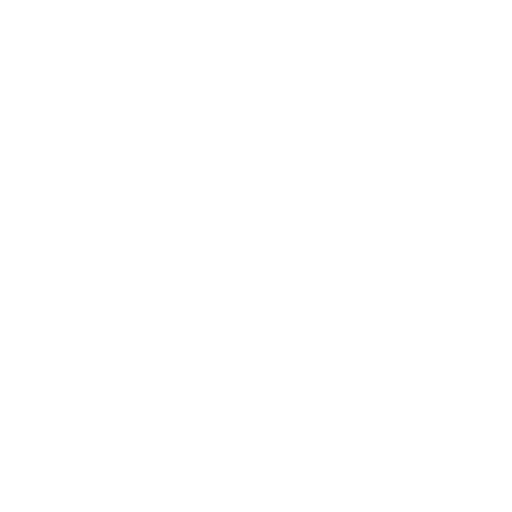
Resource Allocation and Capacity Planning
Optimizes the allocation of machinery, labor, and equipment based on capacity constraints. By balancing workloads and adjusting schedules, it maximizes resource utilization and minimizes production bottlenecks.
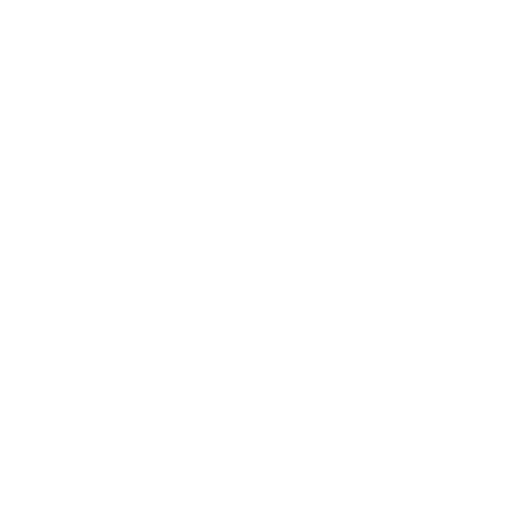
Customer Demand Prediction
Enables accurate predictions of customer demand using historical data and market trends. This feature ensures production aligns with anticipated orders, minimizing overproduction and stock shortages.
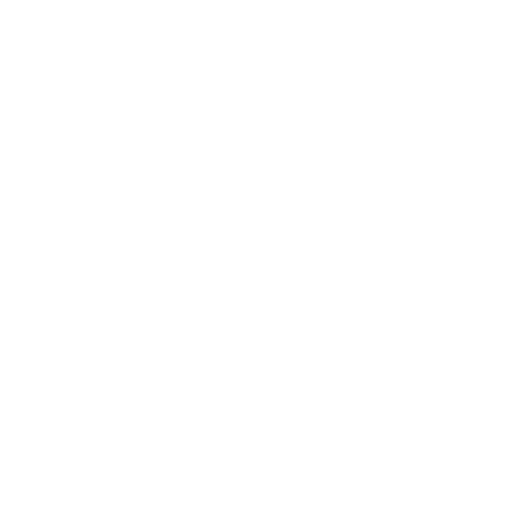
Real-Time Production Adjustment
Offers the ability to adapt production schedules dynamically based on real-time shop floor data, enabling manufacturers to handle unexpected changes in demand or production constraints.
Benefits
Production Efficiency
APS software optimizes resources and eliminates bottlenecks for smoother workflows and faster production cycles.
On-Time Delivery
Predicts timelines and aligns them with customer demands to ensure timely order fulfillment.
Reduced Inventory Costs
Aligns production with demand forecasts to minimize excess inventory and reduce storage costs.
Better Resource Utilization
Addresses capacity constraints for effective use of machinery, labor, and materials.
Increased Flexibility
Allows swift responses to demand changes, supply disruptions, or capacity constraints.
Data-Driven Decisions
Advanced analytics provide insights into production performance and resource utilization.
Siemens Opcenter APS
Snic Solutions is recognized as one of the elite organizations partnered with Siemens as a value-added reseller of Opcenter.
/About%20Page/Blake%20Digital%20Transformation%20Solutions.png?width=500&height=500&name=Blake%20Digital%20Transformation%20Solutions.png)

APS Integration
Advanced Planning and Scheduling (APS) systems are essential in the smart manufacturing ecosystem by integrating with systems like ERP, MES, MOM, and QMS.
What happens when you integrate?
Integrating APS improves production efficiency and flexibility, allowing real-time adjustments to plans based on current data. This ensures that changes in demand, capacity, or supply chain conditions are promptly reflected across all systems, optimizing resources and maintaining synchronization throughout the manufacturing process.
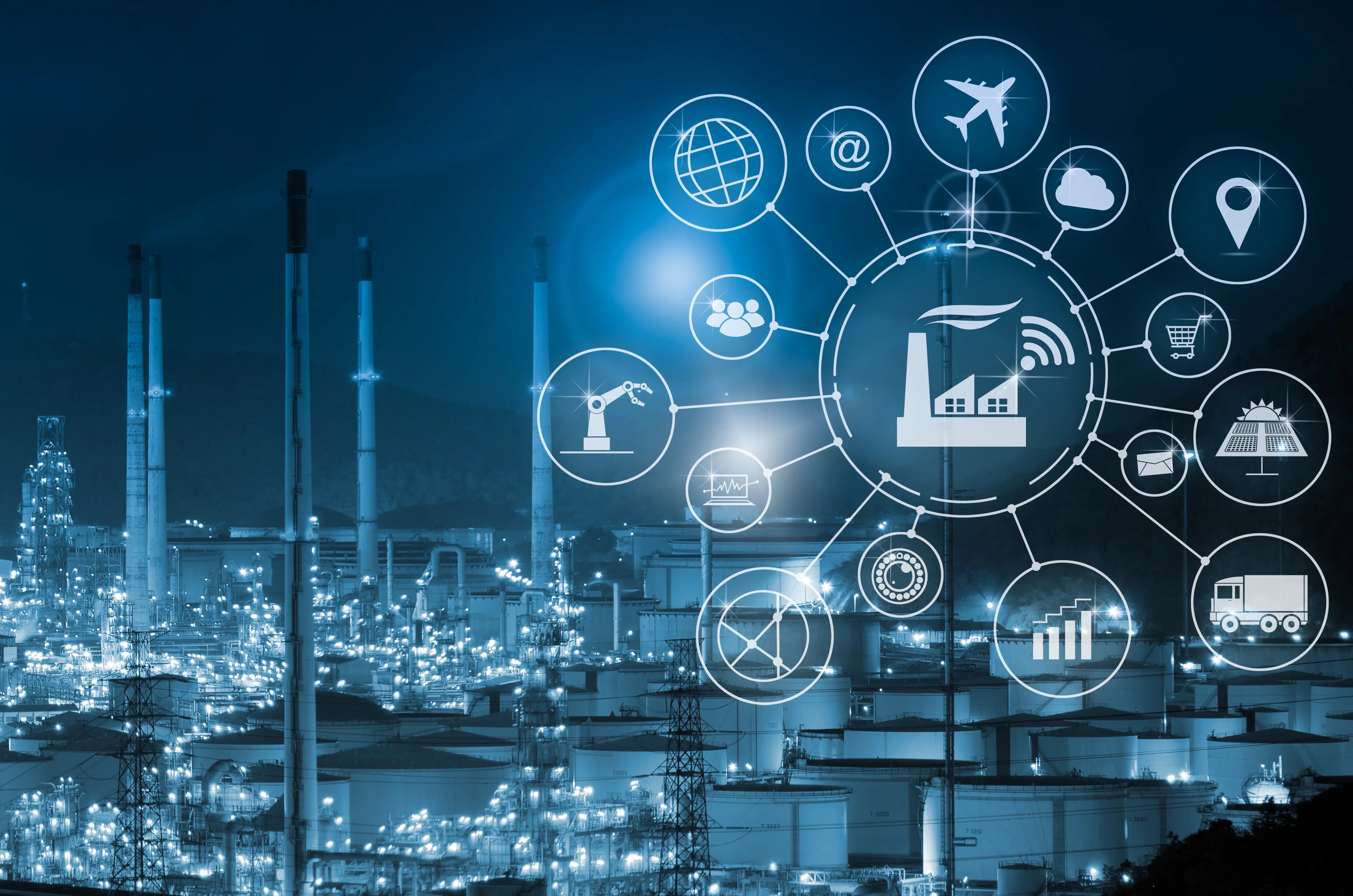
From Our Blog
Stay up to date with what is new in our industry, learn more about the upcoming products and events.
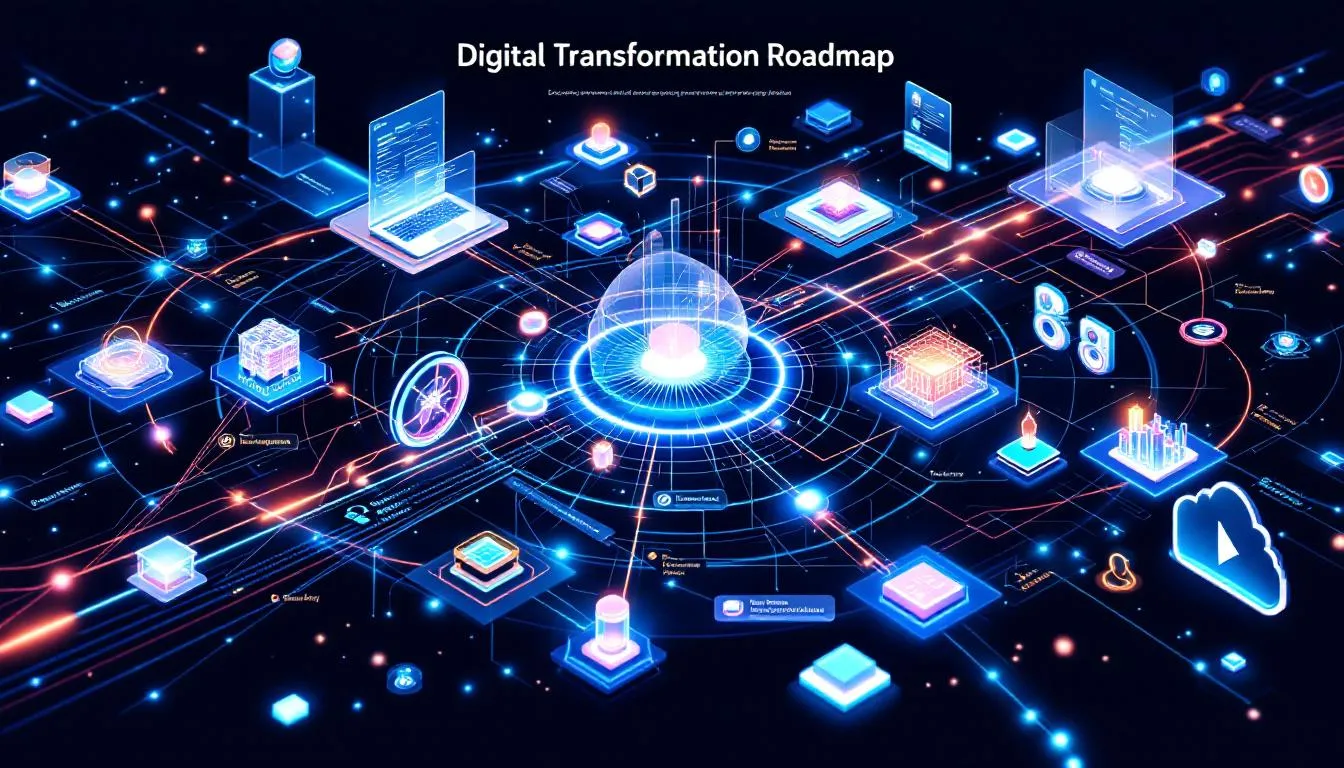
Ultimate Guide to Manufacturing Digital Transformation Roadmaps
Embarking on digital transformation in manufacturing? Start with a manufacturing d…
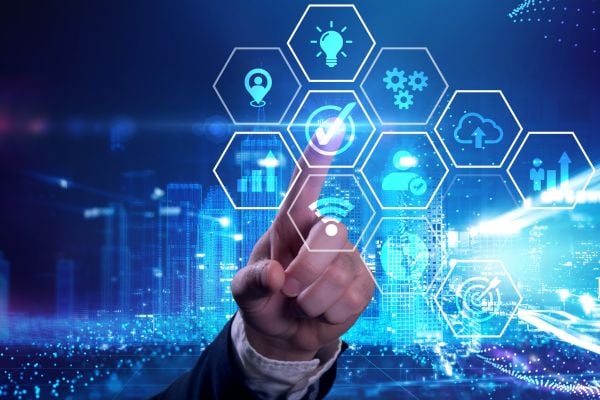
IoT Integration: A Complete Guide to Connecting Smart Devices and Systems
By 2025, over 27 billion IoT devices will flood the networks, changing the way bus…
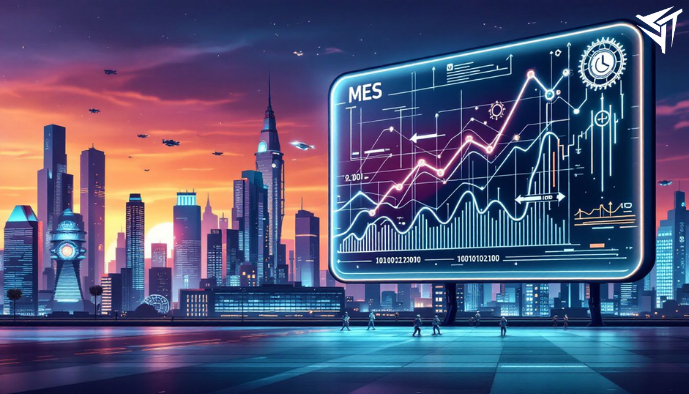
Essential Guide to Downtime Tracking for Better Efficiency
What is Downtime Tracking Downtime tracking is crucial for manufacturers to reduce…
Frequently Asked Questions
Have Question? We are here to help
What are the major components of an advanced planning and scheduling system?
An advanced planning and scheduling (APS) system includes key components like demand forecasting, master production scheduling, capacity planning, and production scheduling. These elements work together to ensure accurate demand prediction, optimal resource utilization, and efficient production sequencing to meet customer demand efficiently.
How is APS Different from ERP or MES?
APS focuses specifically on detailed planning and scheduling. Unlike ERP (Enterprise Resource Planning), which provides overall business management, or MES (Manufacturing Execution System), which controls shop floor operations, APS integrates with both to provide detailed scheduling for efficient production.
What Industries Benefit the Most from APS?
APS is beneficial across multiple industries, especially those with complex supply chains or production processes, like automotive, electronics, consumer goods, food and beverage, and pharmaceuticals.
How Does APS Optimize Scheduling?
APS uses advanced algorithms and simulations to balance demand and capacity, identify production bottlenecks, and maximize resource utilization. It provides real-time adjustments based on current data.
Can APS Software Handle Complex Supply Chains?
Yes, APS can integrate with various systems to offer end-to-end supply chain visibility. It manages changes in lead times, forecasts demand, and ensures timely delivery by synchronizing production with supply chain needs.
What Improvements Can I Expect from APS?
APS typically results in reduced production lead times, lower inventory costs, increased on-time delivery, and optimized equipment and resource utilization.
Partner With Us To Reduce Your Technical Debt
Snic Solutions is recognized as one of the elite organizations partnered with Siemens as a value-added reseller of Opcenter.
/About%20Page/Blake%20Digital%20Transformation%20Solutions.png?width=500&height=500&name=Blake%20Digital%20Transformation%20Solutions.png)
