Opcenter Advanced Planning and Scheduling
Opcenter APS, formerly known as Preactor APS, is a powerful software solution that helps manufacturers plan, schedule, and optimize their production processes.
What is Opcenter APS?
Opcenter APS is an advanced planning and scheduling (APS) tool designed to refine manufacturing operations. It enhances production efficiency through sophisticated algorithms and data analytics, producing optimized schedules that consider machine, material, and labor constraints.
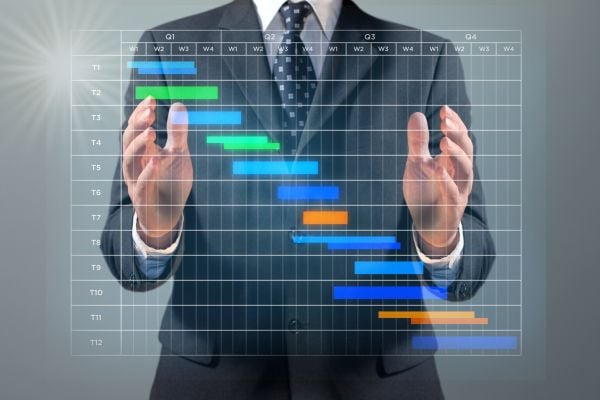
Enhanced Manufacturing With Opcenter APS
Opcenter APS integrates data from various systems, including enterprise resource planning (ERP), manufacturing execution systems (MES), and direct shop floor inputs.
This comprehensive data collection is analyzed to develop a precise production schedule, optimizing the balance between costs, lead time, times, and resource utilization.
The software's powerful algorithms provide a strategic overview, allowing for cost minimization and enhanced efficiency, while its real-time tracking capabilities enable ongoing adjustments to keep production aligned with goals.
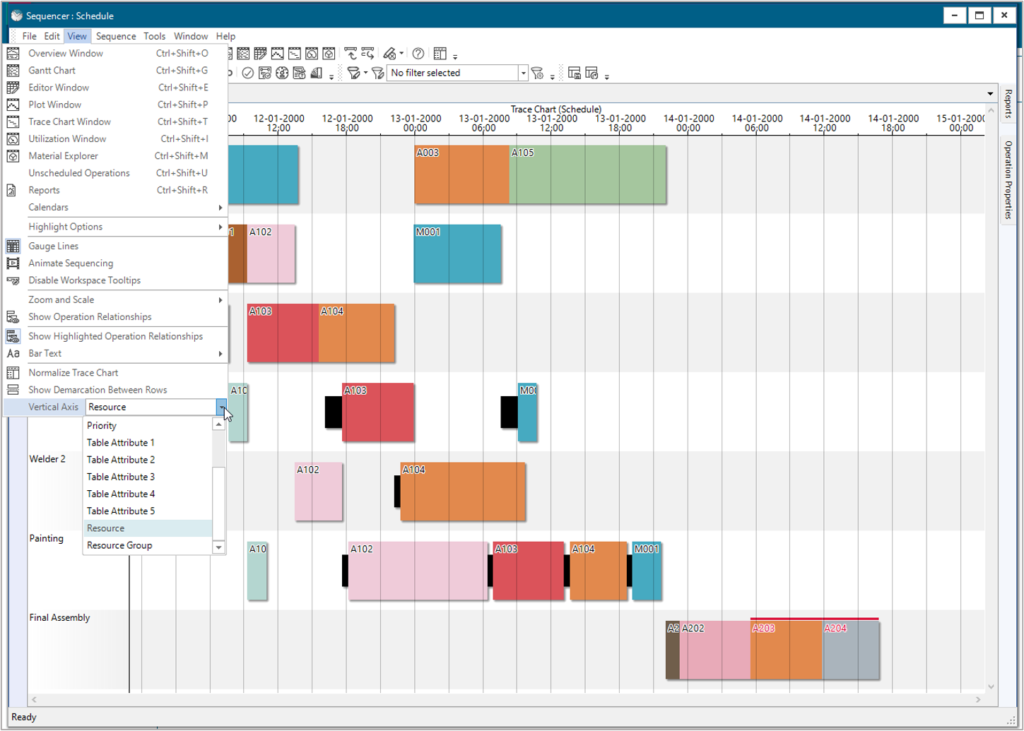
Opcenter APS Reviews
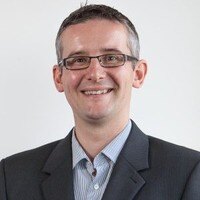
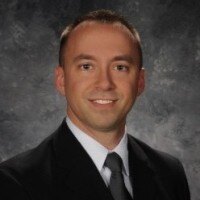
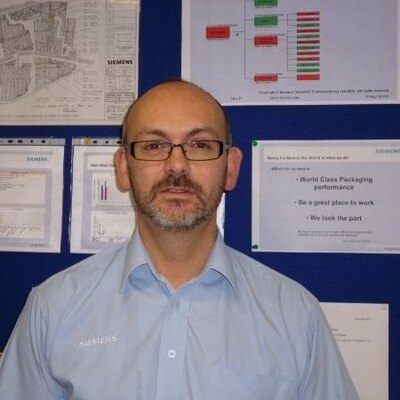
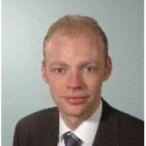
Key Advantages of Opcenter APS
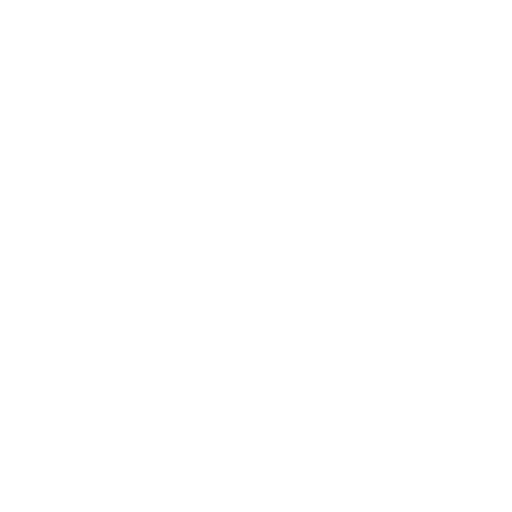
Medium-term Tactical Planning
Reduces manual tasks by automating the sequence of operations for samples and tests.
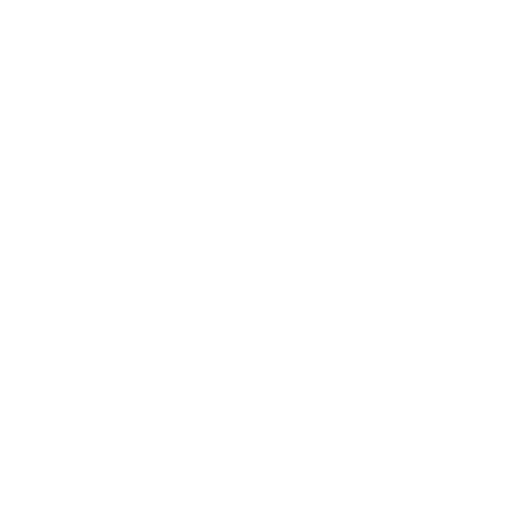
Long-term Strategic Planning
Plan production months and years in advance, ensuring alignment with future demand projections.
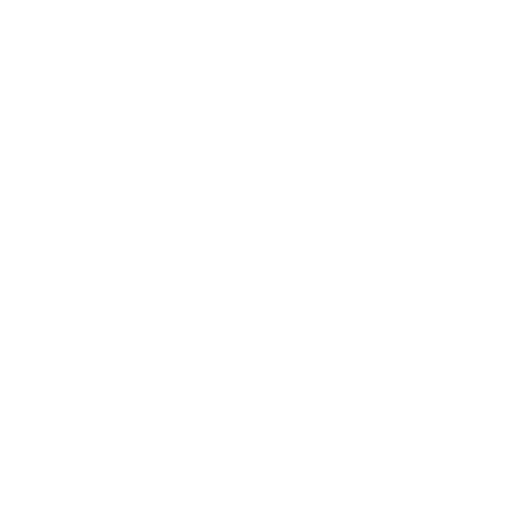
Inventory Management
Reduce waste, identify potential shortages, and optimize the flow of raw materials throughout the production cycle.
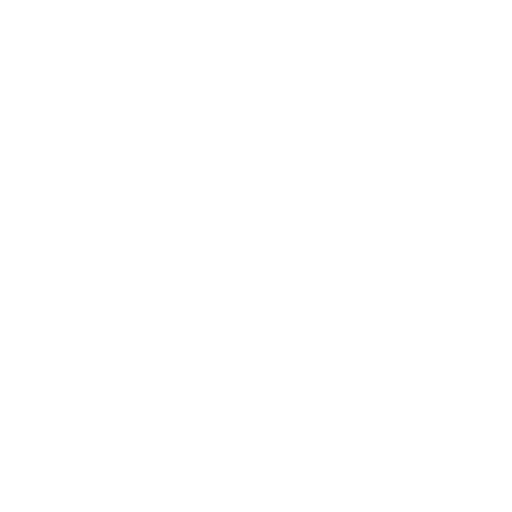
Detailed Sequencing and Scheduling
Enhances production by planning and scheduling tasks, reducing idle time and maximizing resource utilization.
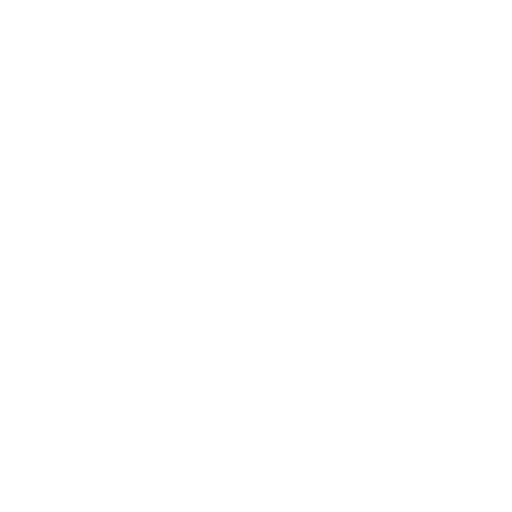
Productivity Improvements
Pinpoints and alleviates bottlenecks, shortens setup times, and optimizes machinery use, resulting in increased productivity and lower operational costs.
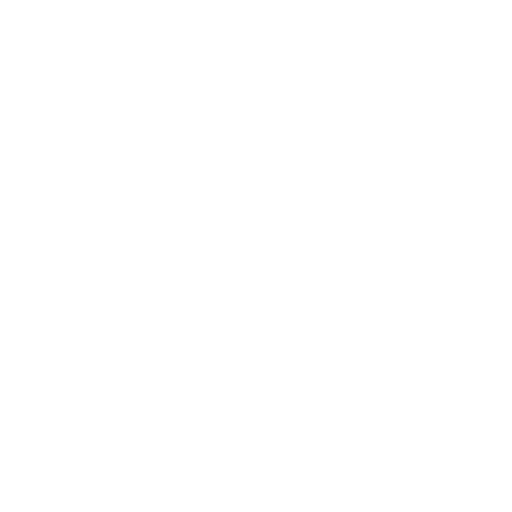
On-time Delivery
Meet customer demands more effectively while reducing lead times by enhancing availability and efficiency in production processes
/Profile%20Pictures/Nikhil%20Digital%20Transformation%20Solutions.png?width=500&height=500&name=Nikhil%20Digital%20Transformation%20Solutions.png)
Implementing Opcenter APS
Most Enterprise Resource Planning (ERP) systems operate on the premise of infinite capacity and employ backward scheduling. However, they can't foresee problems from too much work or understand how changes affect capacity and order timelines.
What are the benefits of implementation?
Incorporating Opcenter APS not only with ERP but also with Product Lifecycle Management (PLM), Manufacturing Execution Systems (MES), and other third-party tools enhances material flow and enriches information sharing across departments. This integrated approach improves visibility into operations, enabling more effective management of unforeseen events.
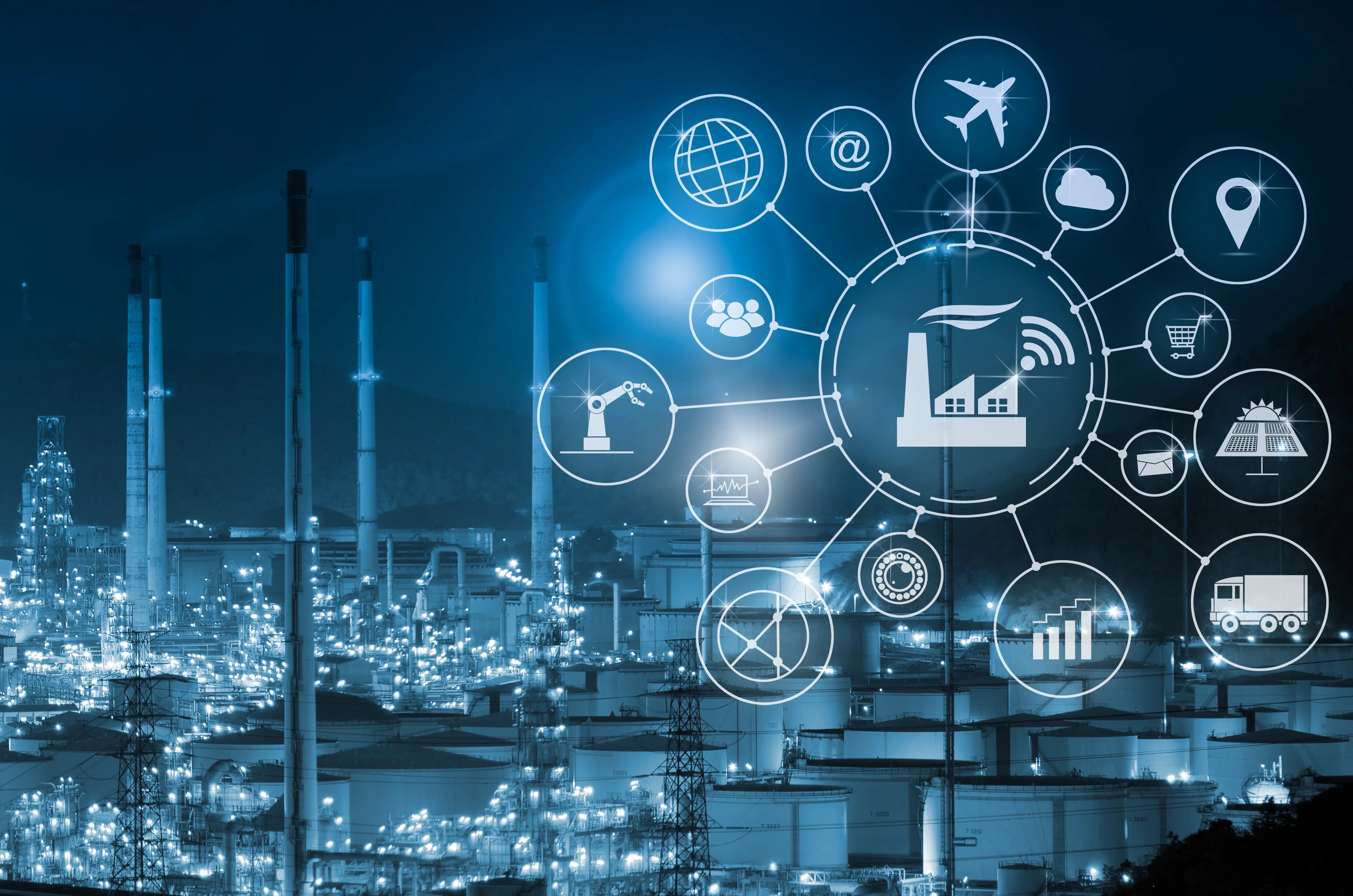
Signs You Need APS
Implementing an Advanced Planning and Scheduling (APS) solution like Opcenter APS can be a game-changer for companies striving to optimize their manufacturing processes. Here are key signs that indicate your company might be in need of an APS solution:
Difficulty Adapting to Changes
Manufacturing is dynamic, with frequent changes in demand, production capacity, and supply chain disruptions. If your current system can't quickly adapt to these changes, causing delays and inefficiencies, an APS solution can provide the flexibility and real-time adaptability you need.
High Inventory Levels and Waste
Excess inventory ties up capital and space, while insufficient inventory leads to production halts. If you're experiencing high levels of inventory that don't match production needs or significant waste, APS can help balance and optimize inventory levels based on actual demand and production capacity.
Inefficient Production Scheduling
If your company struggles with creating efficient production schedules that take into account various constraints like machine availability, labor hours, and materials, it's a clear sign you need an APS solution. These systems optimize scheduling to ensure that resources are utilized efficiently, reducing downtime and bottlenecks.
Poor Delivery Performance
Struggling to meet delivery deadlines can harm customer satisfaction and your company finished product's reputation. An APS solution improves on-time delivery rates by providing more accurate and achievable production schedules.
Downtime and Underutilization
If your production lines are frequently idle or certain resources are underutilized, it indicates inefficiencies in your scheduling and planning. An APS solution can help optimize the use of all resources and reduce lead time, minimizing downtime and improving overall productivity.
Limited Visibility Across Operations
Lack of visibility into production status, inventory levels, and capacity utilization makes it difficult to make informed decisions. APS solutions offer real-time insights into your manufacturing operations, enhancing transparency and decision-making.
Partner With Us To Reduce Your Technical Debt
Snic Solutions is recognized as one of the elite organizations partnered with Siemens as a value-added reseller of Opcenter.
/Profile%20Pictures/Nikhil%20Digital%20Transformation%20Solutions.png?width=500&height=500&name=Nikhil%20Digital%20Transformation%20Solutions.png)

Opcenter APS Products
.jpg?width=370&height=208&name=Opcenter%20APS%20(1).jpg)
Opcenter Scheduling
Opcenter Scheduling elevates production planning from a complex challenge to a streamlined, scientific process. This advanced scheduling tool enhances decision-making, ensuring efficient resource allocation, on-time deliveries, and reduced inventory costs.
.jpg?width=370&height=208&name=Opcenter%20Execution%20(1).jpg)
Opcenter Planning
Opcenter Planning is crucial for manufacturers looking to improve production, reduce costs, and meet customer delivery deadlines while adapting to market changes. It optimizes the use of machines, materials, and labor, boosting productivity.
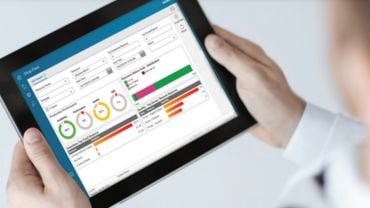
Opcenter Scheduling SMT
Opcenter Scheduling SMT streamlines electronics manufacturing by integrating machine configurations, work orders, and material availability data. It optimizes SMT line productivity, minimizes setup time, and swiftly addresses potential line-down scenarios.
Opcenter APS Free Trials
Opcenter Scheduling Standard
Opcenter Scheduling SMT
Opcenter APS for CPG
From Our Blog
Stay up to date with what is new in our industry, learn more about the upcoming products and events.
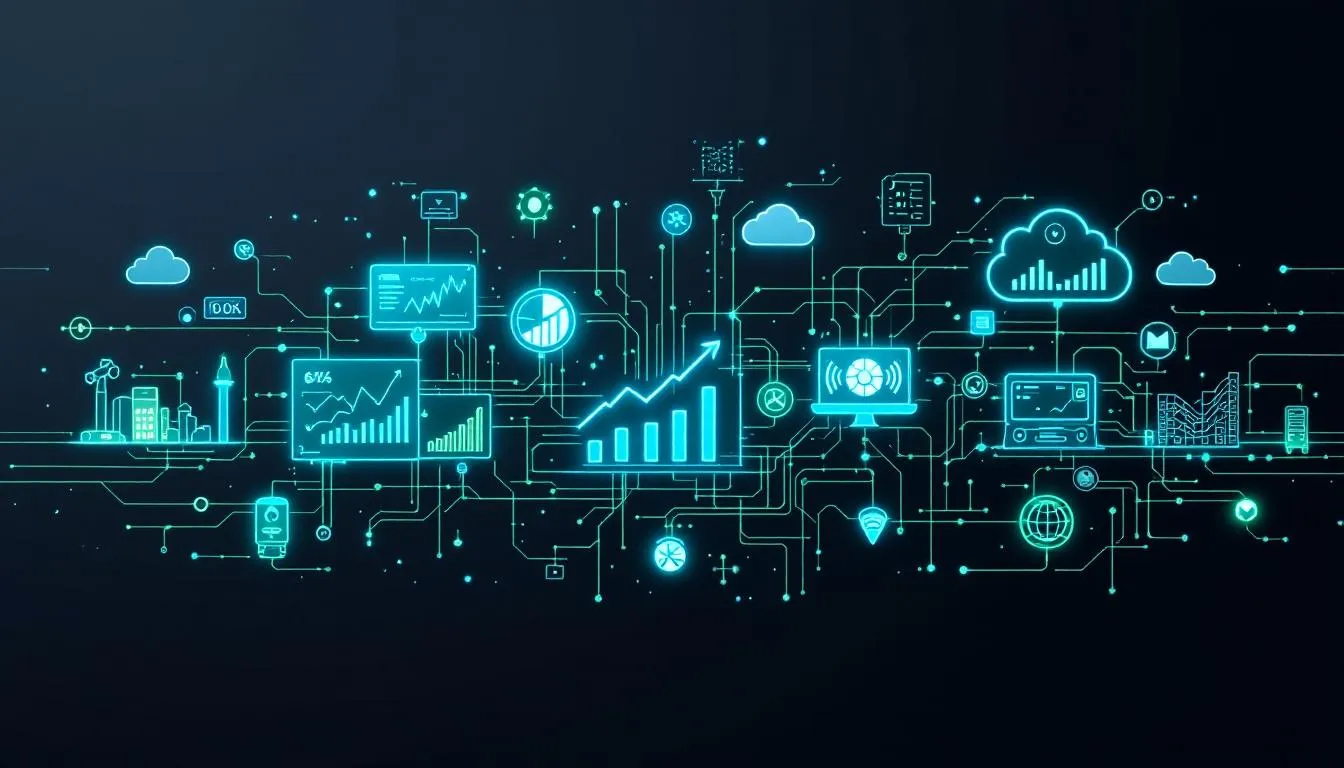
Maximizing Efficiency with Predictive Analytics in Manufacturing
Predictive analytics in manufacturing uses data to forecast trends and disruptions…
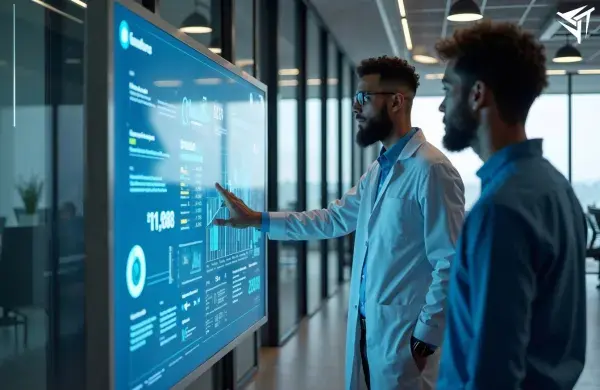
Lean Manufacturing Implementation Plan: 7 Steps to Success
Need to implement a lean manufacturing? A successful Lean manufacturing implementa…
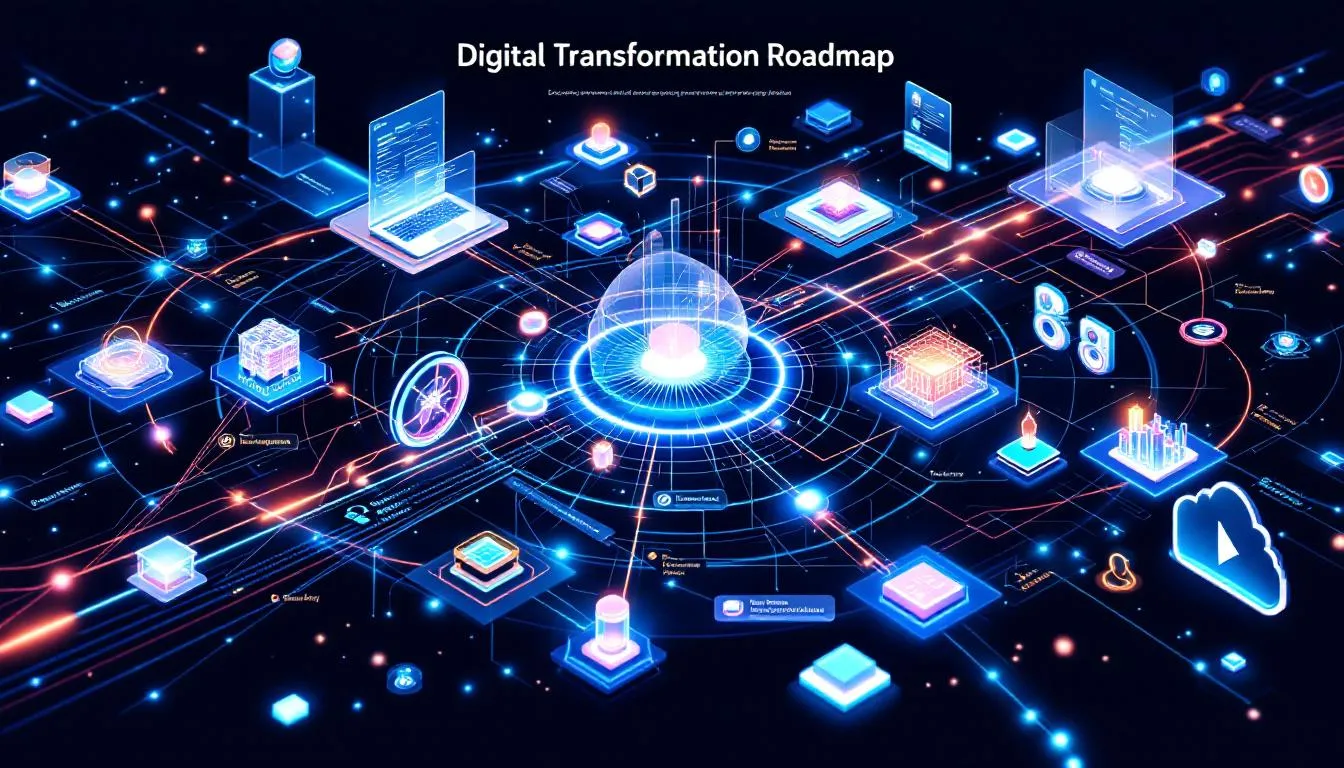
Ultimate Guide to Manufacturing Digital Transformation Roadmaps
Embarking on digital transformation in manufacturing? Start with a manufacturing d…
Frequently Asked Questions
Have Question? We are here to help
What is Opcenter APS?
Opcenter Advanced Planning and Scheduling (APS) is a software solution by Siemens that helps manufacturers optimize their production planning and scheduling. It is part of the Siemens Opcenter suite, which addresses various aspects of manufacturing operations management (MOM).
How does Opcenter APS improve production processes?
Opcenter APS enhances production by using sophisticated algorithms to create optimized schedules that account for machine availability, material requirements, labor resources, and other constraints. It offers real-time visibility and adaptability, enabling manufacturers to efficiently manage their resources and respond to changes quickly.
Can Opcenter APS integrate with existing systems?
Yes, Opcenter APS is designed to integrate seamlessly with various systems, including Enterprise Resource Planning (ERP) systems, Manufacturing Execution Systems (MES), and shop floor control systems. This integration allows for the synchronization of data across the manufacturing enterprise for more informed decision-making.
What types of manufacturers can benefit from Opcenter APS?
Manufacturers across a wide range of industries can benefit from Opcenter APS, including aerospace, automotive, consumer products, electronics, pharmaceuticals, and more. Any manufacturing operation looking to optimize production scheduling and improve operational efficiency will find Opcenter APS valuable.
How does Opcenter APS handle changes in production demands or disruptions?
Opcenter APS is equipped to quickly adapt to changes in production demands or unexpected disruptions. It allows manufacturers to adjust production schedules in real-time, ensuring that resources are allocated efficiently and that delivery timelines are met.
Does Opcenter APS support scenario analysis?
Yes, Opcenter APS supports scenario analysis, enabling manufacturers to simulate different production scenarios and assess their impact. This feature helps in making informed decisions by evaluating various 'what-if' situations without affecting the actual production schedule.
How user-friendly is Opcenter APS?
Opcenter APS features a user-friendly interface that simplifies the viewing and management of production schedules. Its intuitive design ensures that users can easily navigate the software, making it accessible to all levels of technical proficiency.
Can Opcenter APS help reduce production costs?
Yes, by optimizing production scheduling, reducing lead times, and maximizing resource utilization, Opcenter APS helps manufacturers significantly reduce production costs. It identifies bottlenecks and inefficiencies, allowing for cost-effective production planning and execution.
How can I get Opcenter APS for my manufacturing operations?
To acquire Opcenter APS for your manufacturing operations, consider reaching out to Snic Solutions, an authorized Siemens partner. Snic Solutions can provide you with detailed information, guide you through the purchasing process, and offer comprehensive support for implementation and integration with your current systems. Additionally, you can schedule a demo with Snic Solutions to see Opcenter APS in action and understand how it can benefit your manufacturing operations.
Siemens Opcenter APS
Snic Solutions is recognized as one of the elite organizations partnered with Siemens as a value-added reseller of Opcenter APS.
/Profile%20Pictures/Nikhil%20Digital%20Transformation%20Solutions.png?width=500&height=500&name=Nikhil%20Digital%20Transformation%20Solutions.png)
