Opcenter X
Empower your manufacturing operations with Opcenter X, the scalable, easy-to-integrate solution designed for the modern SMB. Experience a seamless transition to digital efficiency and quality, supported by our expert team every step of the way.
What is Opcenter X?
Opcenter X is a modular, cloud-based manufacturing operations management (MOM) solution designed for SMBs, offering scalable digital tools to optimize productivity, ensure quality, and reduce costs.
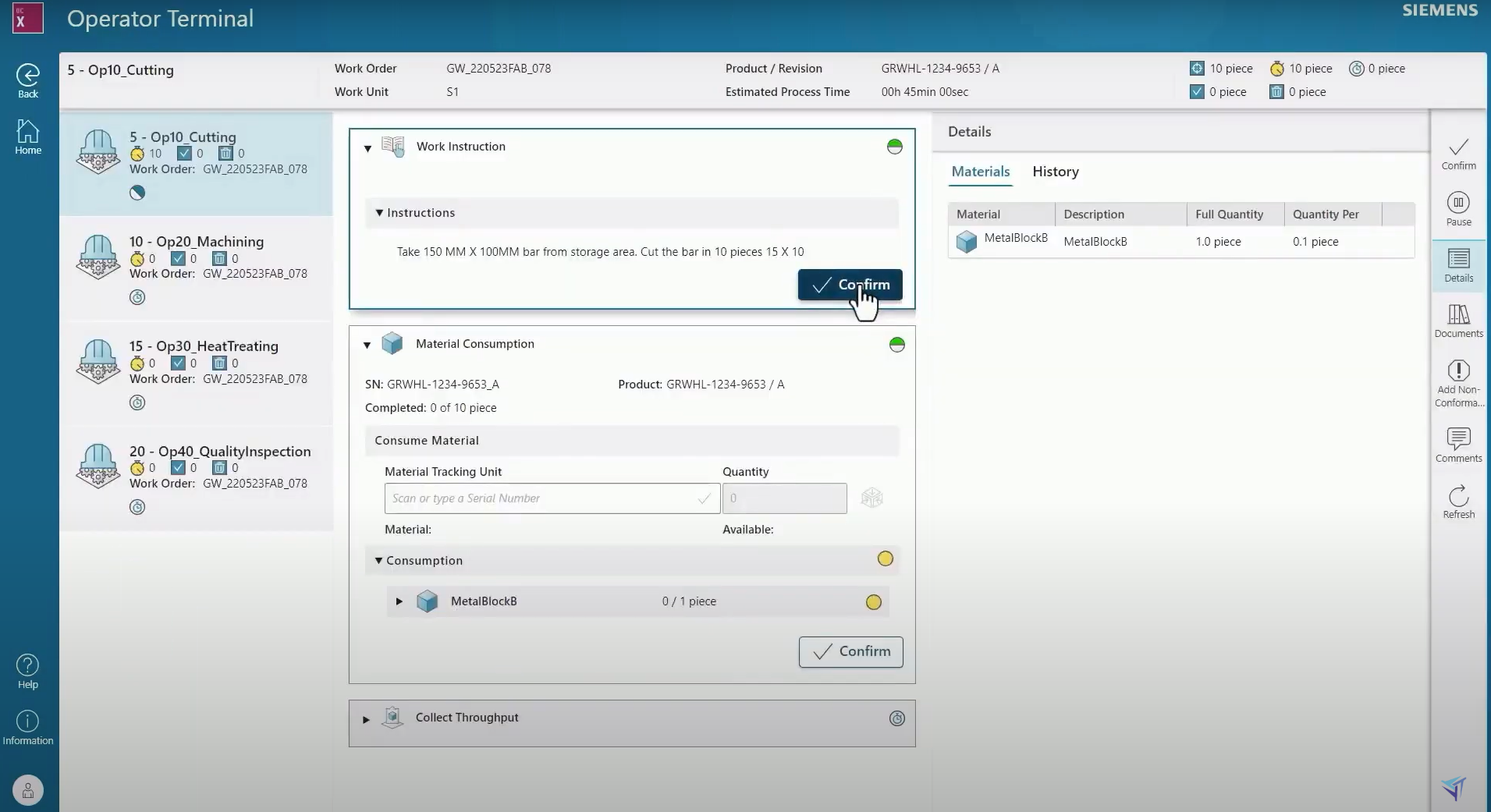
Enhanced Manufacturing With Opcenter X
Opcenter X revolutionizes manufacturing for SMBs by integrating critical operations into a unified digital platform, enhancing efficiency and data accuracy.
Opcenter X's modular and scalable nature allows businesses to start with essential features and expand functionality as needed, supporting growth without major system overhauls.
Its cloud-based, "pay as you grow" model reduces initial investments and ongoing IT costs, making advanced manufacturing tools accessible and financially manageable for SMBs.
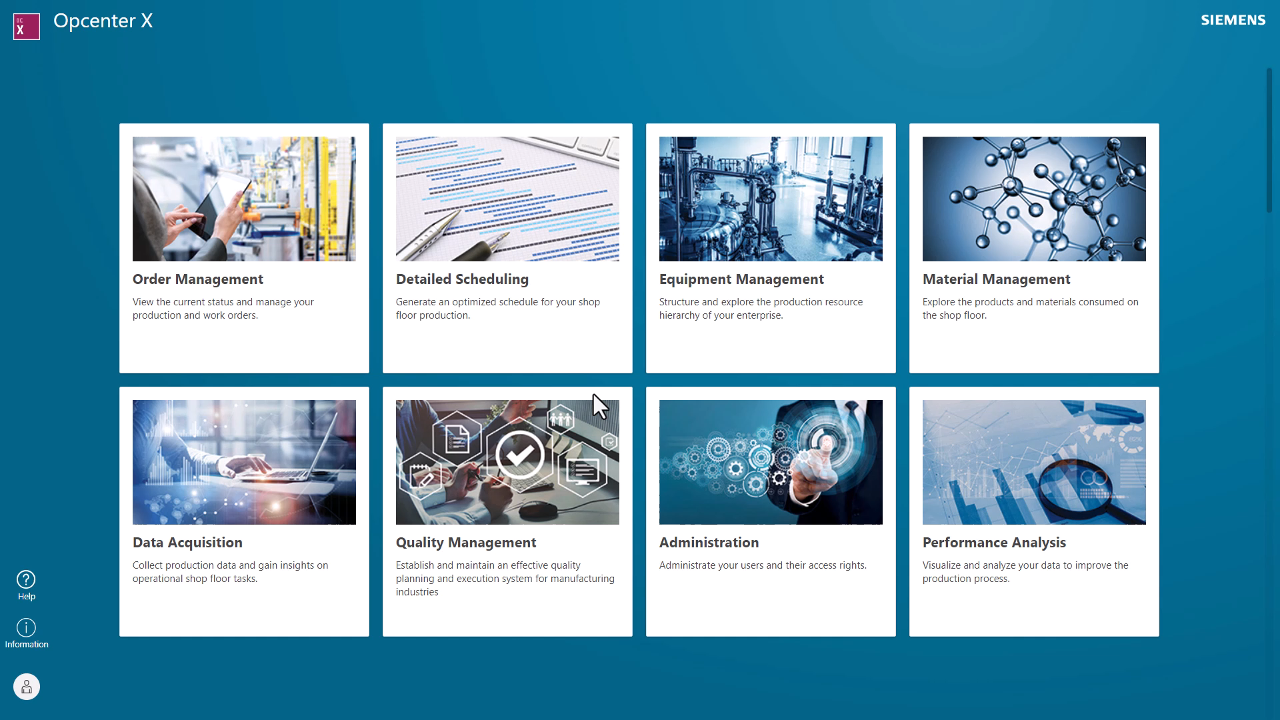
Key Advantages of Opcenter X
Opcenter X offers significant benefits designed to support SMBs in optimizing their manufacturing operations effectively and efficiently.
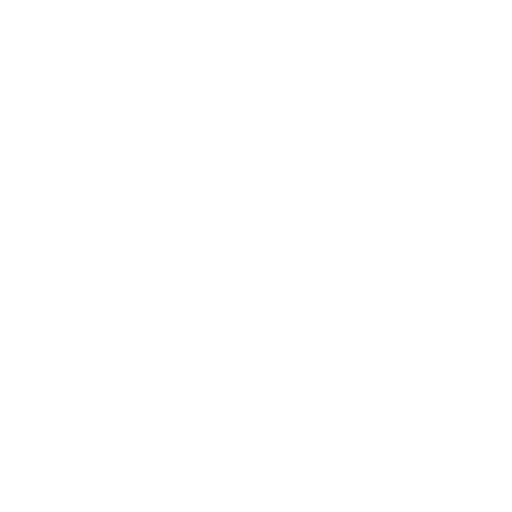
"Pay as You Grow" Model
Start small and scale up, minimizing initial expenses and funding future growth.
Compliance Support
Tools like audit trails and quality checks help meet industry standards, essential for regulatory compliance.
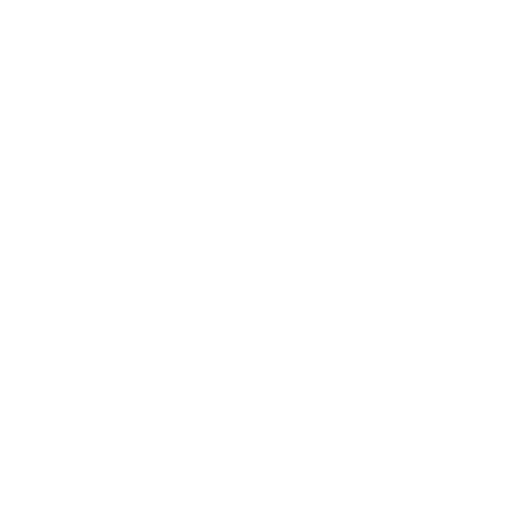
Financial Flexibility
Invest in high-impact areas with the option to add modules as needed, boosting efficiency and growth.
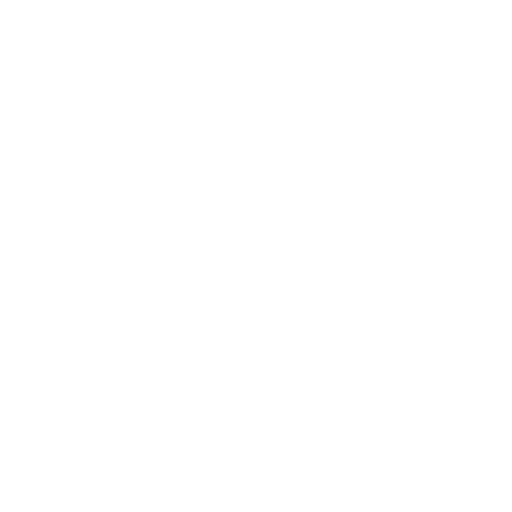
Downtime Reduction
Real-time monitoring and predictive maintenance reduce downtime, maintaining high productivity levels.
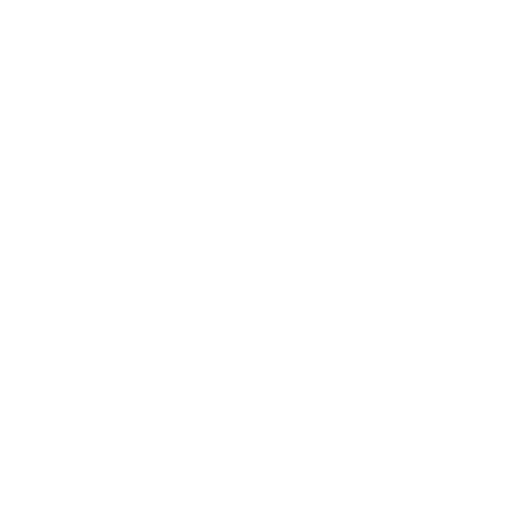
Data-Driven Insights
Consolidates manufacturing data to provide actionable analytics, enabling quicker, more informed decisions to improve operations and adapt to market changes.
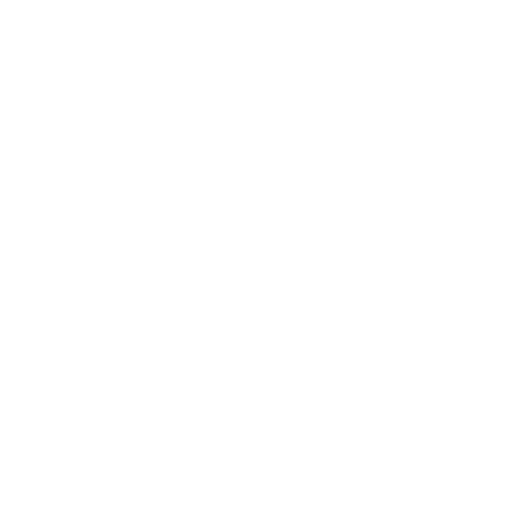
Streamlined Operations
Combines various manufacturing processes into one platform, simplifying management and accelerating operations.
/About%20Page/Blake%20Digital%20Transformation%20Solutions.png?width=500&height=500&name=Blake%20Digital%20Transformation%20Solutions.png)
Implementing Opcenter X
Opcenter X is built with integration in mind, facilitating seamless connections with existing business systems. The platform supports various APIs and standard protocols, making it compatible with a wide range of enterprise software systems.
What are the benefits of implementation?
Integrating various systems into Opcenter X eliminates the need for multiple standalone applications, simplifying workflows and reducing the chances of errors. This leads to more efficient operations with fewer interruptions.
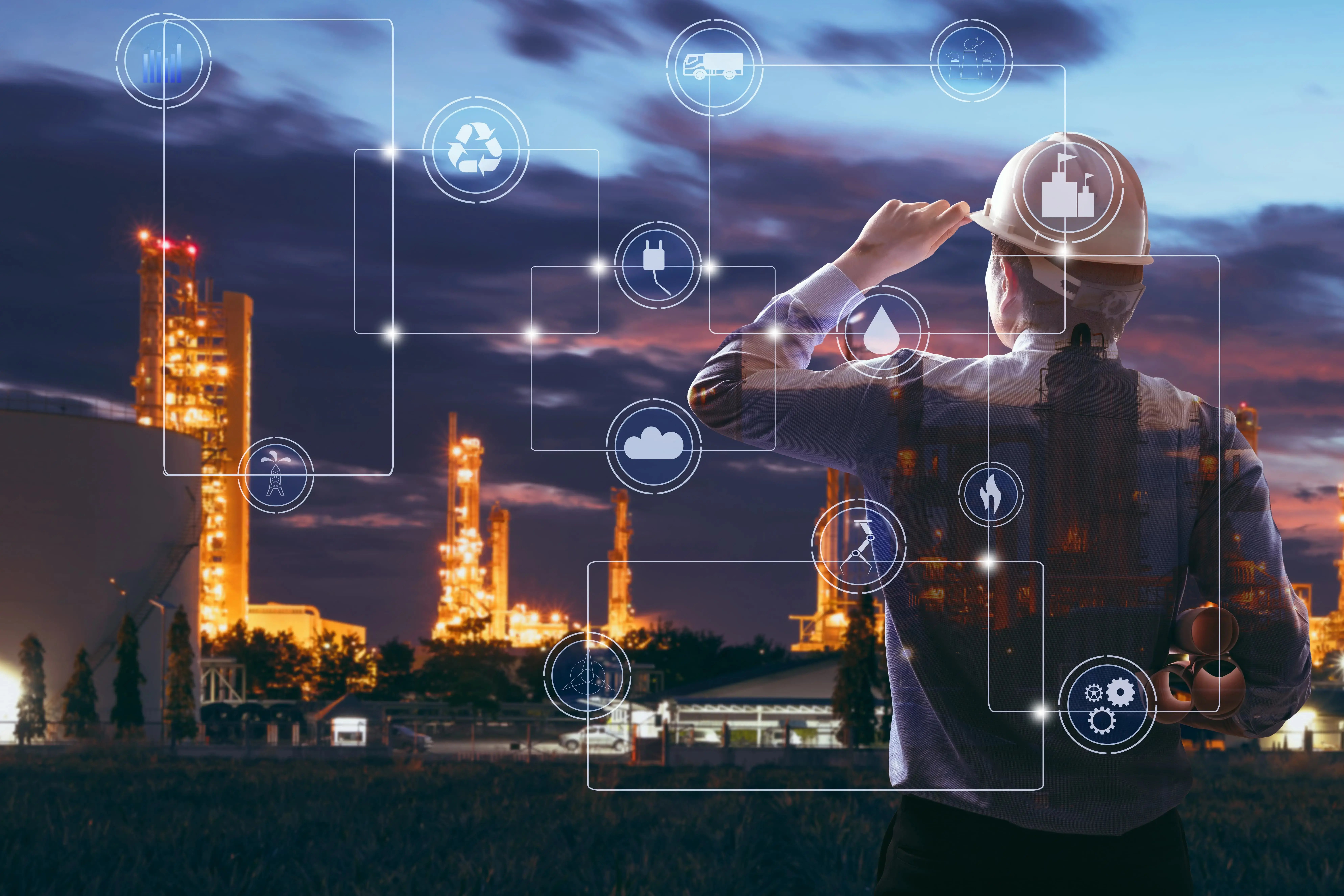
Signs you need Opcenter X
For small to medium-sized businesses (SMBs) in manufacturing, recognizing the need for a system like Opcenter X can be crucial for timely and strategic growth. Here are the top signs that indicate an SMB manufacturer might need to implement Opcenter X
Inefficient Workflow Management
If current processes involve multiple disjointed systems or excessive manual intervention, leading to inefficiencies and increased error rates, it’s a sign that a more integrated solution like Opcenter X could streamline operations.
Difficulty Scaling Operations
Struggling to manage increased production demands or expand operational capacity without significant disruptions indicates a need for the scalable solutions provided by Opcenter X.
High Operational Costs
Experiencing escalating costs due to inefficiencies, maintenance of legacy systems, or redundant processes suggests that Opcenter X could help optimize operations and reduce expenses through its efficient, cloud-based platform.
Data Silos and Inconsistent Information
If an SMB faces challenges with data being scattered across various systems without a unified view, Opcenter X’s integrated data management can provide a single source of truth, enhancing decision-making and operational transparency.
Challenges with Compliance and Quality Control
Difficulty in maintaining consistent quality standards or complying with industry regulations due to inadequate system support is a clear indicator that Opcenter X, with its robust compliance and quality management modules, would be beneficial.
Inadequate Reporting and Analytics
The inability to generate timely and accurate reports for analysis and decision-making can significantly hinder performance and competitiveness. Opcenter X’s comprehensive analytics and reporting capabilities address this need effectively.
Siemens Opcenter
Snic Solutions is recognized as one of the elite organizations partnered with Siemens as a value-added reseller of Opcenter.
/About%20Page/Blake%20Digital%20Transformation%20Solutions.png?width=500&height=500&name=Blake%20Digital%20Transformation%20Solutions.png)

Opcenter X Bundles: Essentials and Standard
Opcenter X offers two primary bundles tailored to meet different levels of need and investment for small and medium-sized businesses: Opcenter X Essentials and Opcenter X Standard. Each bundle is designed to provide specific functionalities that cater to varying operational complexities and budget considerations.
Opcenter X Essentials
The Opcenter X Essentials bundle is designed for businesses seeking to streamline their manufacturing operations with core functionalities. This package includes essential modules that help businesses manage their orders, track and trace materials, and handle non-conformance issues effectively.
Order Management: This feature increases operational efficiency, reduces lead times, and improves overall customer satisfaction by managing and tracking manufacturing orders from creation to completion efficiently.
Track and Trace: Enhances visibility across the manufacturing process, improving quality control and facilitating quick resolution of production issues. It helps in monitoring and recording the movement, location, and status of raw materials, components, and finished products throughout the entire manufacturing process.
Non-conformance Management: Maintains product quality, meets regulatory requirements, and ensures customer satisfaction by identifying deviations, investigating root causes, and implementing corrective and preventive actions to prevent recurrence.
This bundle is ideal for businesses that need fundamental manufacturing operations management capabilities without a significant upfront investment.
Opcenter X Standard
The Opcenter X Standard bundle is a more comprehensive package that builds upon the Essentials by adding advanced functionalities for businesses ready to take their operations management to the next level. This bundle includes everything in the Essentials package plus additional features such as genealogy, statistical process control, scheduling, and process modeling.
Genealogy: Provides a complete view of the activities performed to produce final material. It supports advanced analysis and recall campaigns by offering backward and forward genealogy with configurable nesting level and context information for work orders, users, and equipment.
Statistical Process Control: Helps monitor and control the quality of a production process through statistical methods. Businesses can define characteristics to be analyzed, set up inspection and control plans, and execute them to ensure that the process operates efficiently, producing more specification-conforming products with less waste.
Scheduling: Optimizes the use of available resources, meets customer demand, minimizes production costs, and adheres to delivery deadlines with production scheduling capabilities.
Process Modeling: Analyzes, optimizes, and simulates the flow of activities, resources, and information within the production environment to understand and improve manufacturing processes.
The Opcenter X Standard bundle is suited for businesses that require a deeper integration of their operations management systems with advanced capabilities to further enhance efficiency, quality, and productivity across their manufacturing processes.
From Our Blog
Stay up to date with what is new in our industry, learn more about the upcoming products and events.
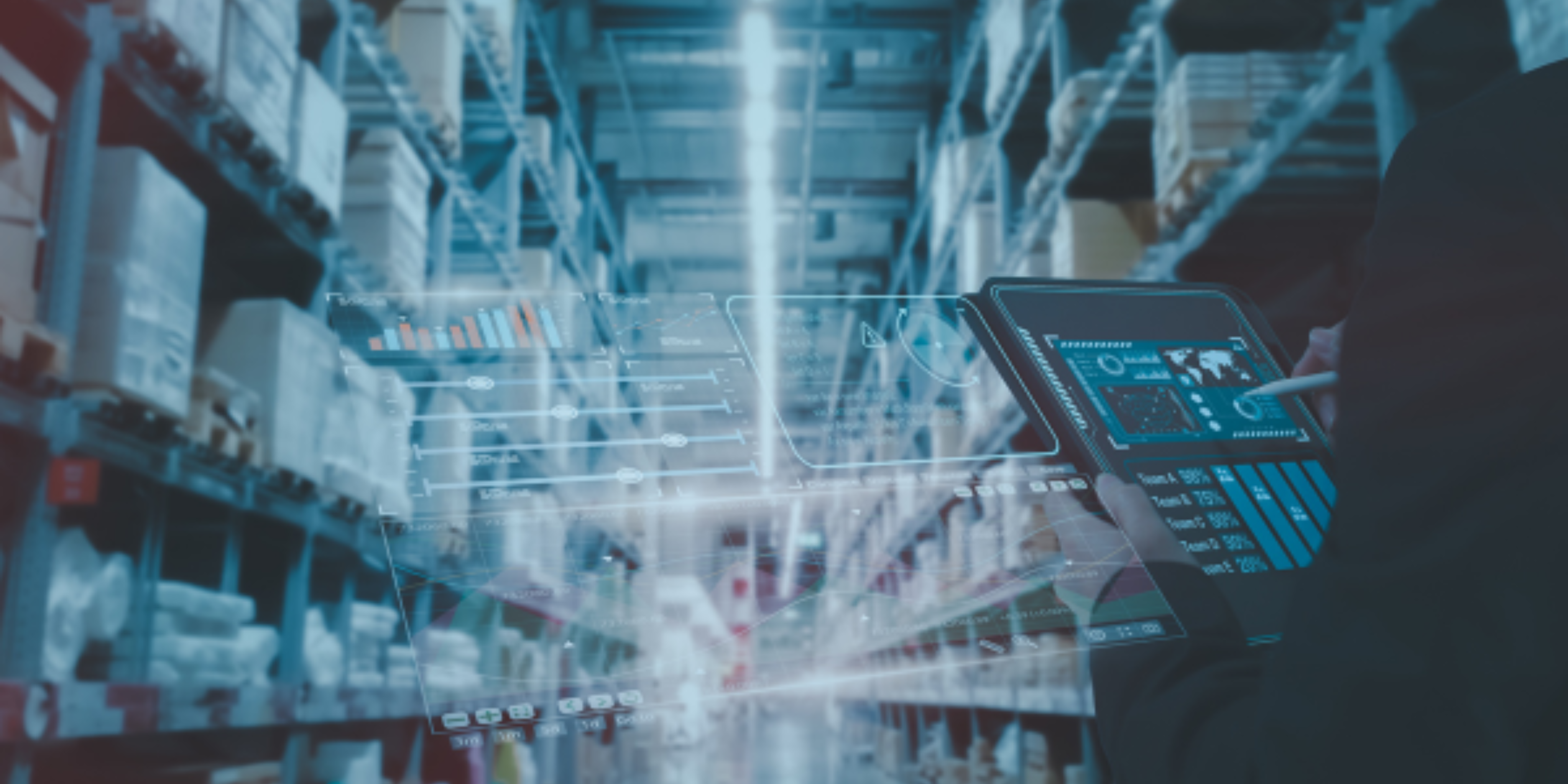
Best Practices for Manufacturing Process Monitoring
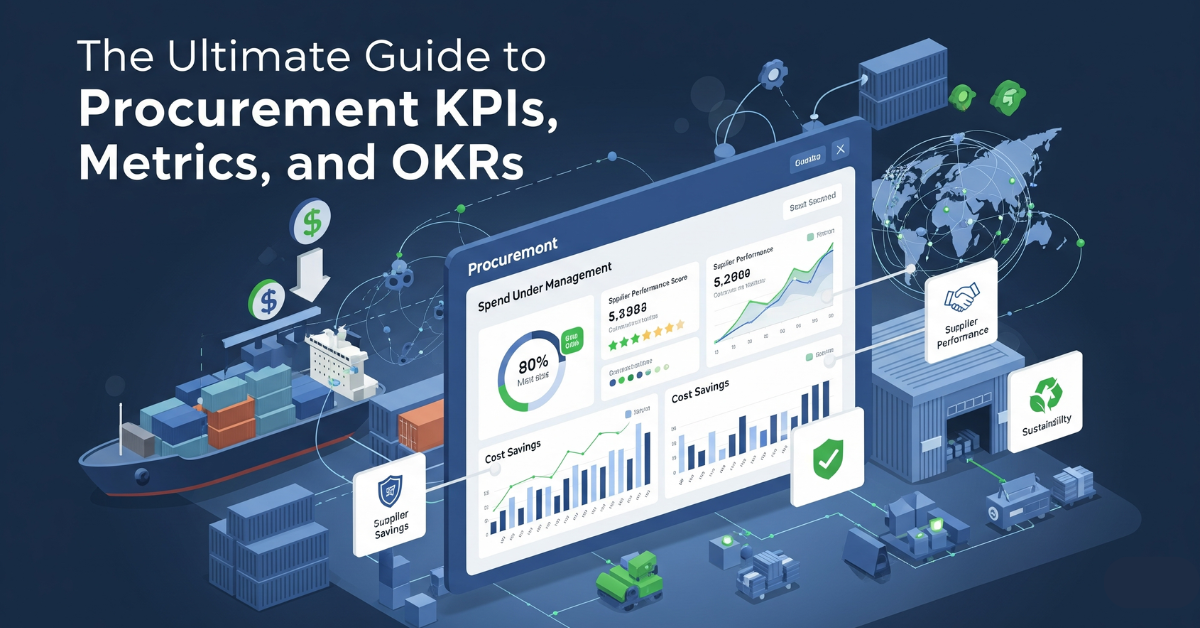
The Ultimate Guide to Procurement KPIs, Metrics, and OKRs
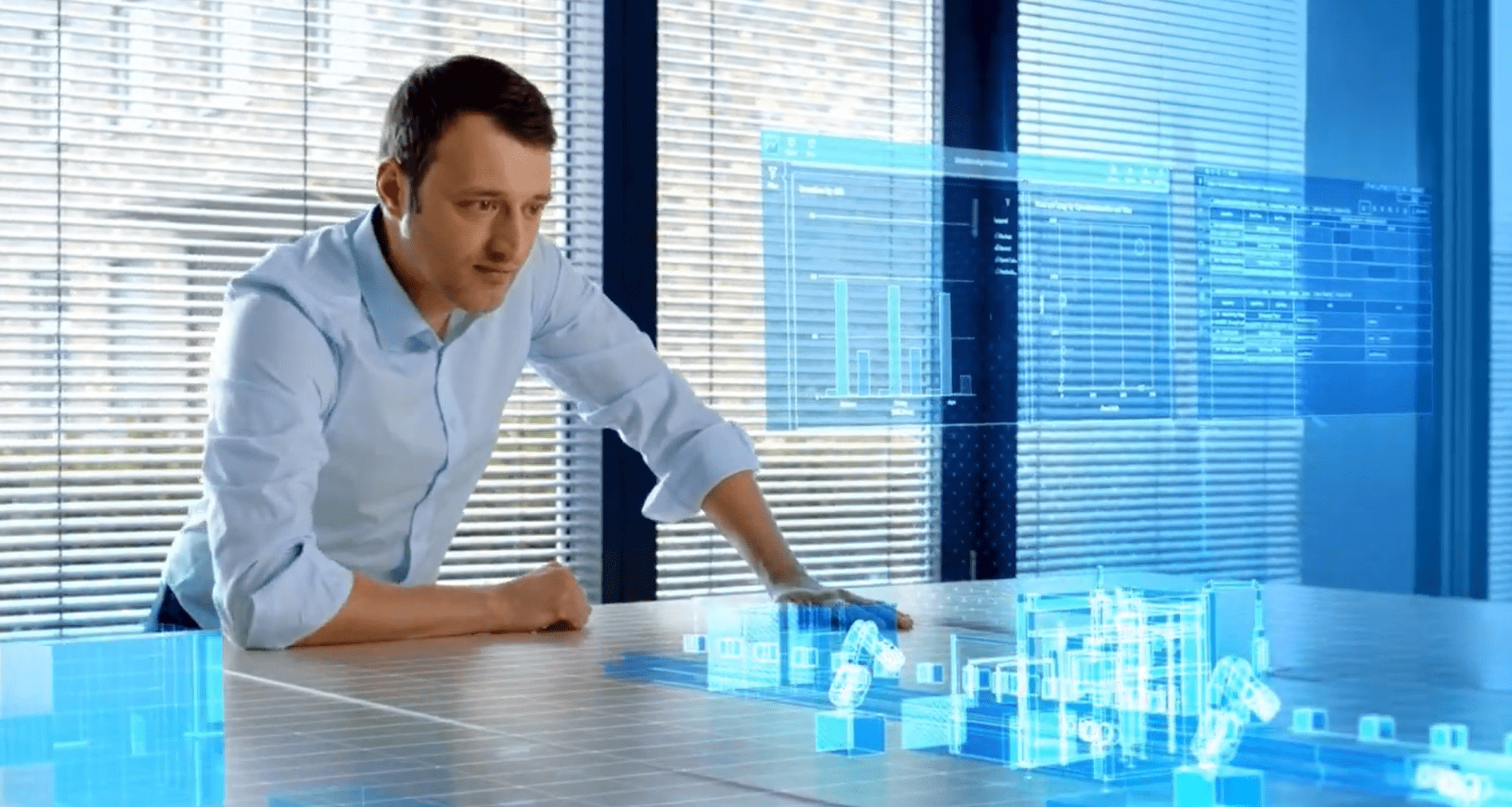
The Ultimate Guide to Benchmarking in Manufacturing
Frequently Asked Questions
Have Question? We are here to help
What makes Opcenter X a good fit for SMBs?
Opcenter X is particularly suited for SMBs because of its scalability, modular structure, and SaaS delivery model. These features ensure that SMBs can start small, minimize initial investments, and scale their solutions as their business grows, without substantial upfront costs.
How long does it take to implement Opcenter X?
Implementation times can vary based on the specific modules chosen and the existing IT infrastructure, but Opcenter X is designed for quick deployment. Many SMBs can go live within a few days to a few weeks, thanks to pre-configured templates and a user-friendly interface that reduces the learning curve.
How does Opcenter X ensure the security of our data?
Opcenter X adheres to the highest standards of data security and privacy. Being a cloud-based solution, it benefits from robust cybersecurity measures, regular updates, and proactive threat monitoring to ensure your data remains secure.
What happens if we need to add more features or modules later?
Opcenter X’s modular design makes it easy to add features or modules as your business needs change. This flexibility ensures that your investment is future-proof, allowing you to expand your MOM capabilities without needing to overhaul your entire system.
Can Opcenter X integrate with existing systems in my business?
Yes, Opcenter X is designed to integrate seamlessly with existing business systems, such as ERP, MOM and CRM software. It supports various APIs and standard protocols, ensuring that data flows smoothly between systems without requiring extensive customization.
Siemens Opcenter X
Snic Solutions is recognized as one of the elite organizations partnered with Siemens as a value-added reseller of Opcenter X.
/About%20Page/Blake%20Digital%20Transformation%20Solutions.png?width=500&height=500&name=Blake%20Digital%20Transformation%20Solutions.png)
