Improving Supply Chain Management
Find out how an APS system can benefit your organization in supply chain management, including production planning, production efficiency, and customer service.
What is Advanced Planning and Scheduling (APS)?
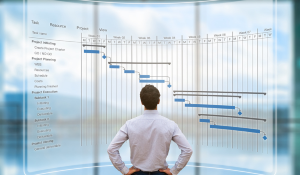
Advanced Planning and Scheduling (APS) is a sophisticated software tool designed to enhance the efficiency of production planning and scheduling processes. Unlike traditional planning methods, APS systems leverage real-time data, complex algorithms, and optimization techniques to make informed decisions that align with organizational goals. By integrating advanced planning into their operations, manufacturers can create optimized production schedules, ensure efficient resource allocation, and meet customer demand more effectively. APS systems provide a comprehensive approach to managing production capacity, raw materials, and labor resources, ultimately leading to improved productivity and profitability.
Production Planning and scheduling
Advanced Planning and Scheduling (APS) in manufacturing is key to production planning and detailed scheduling (PPDS). With APS systems you can create accurate schedules that take into account machine capacity, material availability and labour resources, optimise production processes. APS systems also consider production capacity to create schedules, to ensure efficient resource allocation and on time delivery of customer orders. By incorporating a scheduling system, you can create achievable production schedules that manage real-time changes in production while optimizing efficiency. This means better resource coordination and allocation, more efficiency and shorter lead times.
Also APS allows manufacturers to respond quickly to changes in demand or supply disruptions by giving real time visibility into production schedules. This helps companies to identify bottlenecks or constraints and take action to address them. Overall APS simplifies production planning and scheduling processes, resulting in more productivity and profit.
Inventory Management
Another benefit of aps in supply chain management is inventory management. APS software provides demand forecasting and inventory optimization, so manufacturers and suppliers can keep the right inventory levels with minimal carrying costs and stockouts. Data management is key to accurate demand forecasting and inventory optimization.
With APS manufacturers can adjust inventory levels dynamically based on demand and production schedules. This ability reduces inventory and waste and ensures there is enough stock to meet customer orders on time. By optimizing inventory management manufacturers can save costs, and improve cash flow and overall supply chain efficiency.
Order Fulfilment
Advanced Planning and Scheduling enables manufacturers to improve order fulfilment by scheduling production and aligning to customer demand. APS systems improve customer service by improving on time delivery rates and reducing lead times. By predicting demand patterns and considering all constraints APS software reduces order lead times and on time delivery performance.
Through APS manufacturers can allocate resources, prioritise production orders and minimise production bottlenecks. This means customer orders are fulfilled on time and customer satisfaction and loyalty increase. By managing and improving order fulfillment manufacturers can gain a competitive edge and be seen as a reliable supplier.
Logistics Operations
Also integrating advanced planning systems into supply chain management simplifies logistics operations. These planning systems optimise routes and reduce transport costs by using advanced prediction and optimisation algorithms. APS software gives real time visibility and control into transport and logistics activities, so manufacturers can optimise routes, consolidate shipments and reduce transport costs.
By using APS manufacturers can plan and schedule transport activities more effectively, taking into account delivery windows, carrier availability and capacity utilisation. This reduces transport lead times, freight costs and overall logistics efficiency. Simplifying logistics through APS means faster order fulfilment, lower costs and higher customer satisfaction.
Customer Satisfaction
One of the ultimate goals of supply chain management is to increase customer satisfaction and Advanced Planning and Scheduling can help achieve that. APS systems manage supply chain disruptions by giving visibility into the supply chain and allowing manufacturers to adjust production plans, to deliver products on time. By optimizing production planning, inventory management, order fulfillment, and logistics operations APS enables manufacturers to meet customer expectations on product availability, on-time delivery, and responsiveness.
Through APS manufacturers can deliver customers the right products, in the right quantities, at the right time. This increases customer satisfaction and customer loyalty. By meeting customer demand and delivering great service manufacturers can differentiate themselves in the market and gain a competitive edge.
While Advanced Planning and Scheduling (APS) software has many benefits for production planning, inventory management, order fulfilment and logistics operations, for example, it’s worth noting that APS doesn’t cover demand planning, resource distribution planning (RDP) and material requirement planning (MRP). If your focus is on outcomes aligned with Sales & Operations Planning, RDP or MRP then these specific functionality are generally not part of APS.
Implementing Advanced Planning and Scheduling
Implementing an APS system requires a strategic approach to ensure it aligns with the organization’s supply chain management goals. Here are the key steps to a successful implementation:
-
Define the Scope and Objectives: Clearly outline the goals and objectives of the APS implementation project to ensure alignment with the overall business strategy.
-
Identify Key Stakeholders: Engage key stakeholders from various departments to ensure their roles and responsibilities are clearly defined.
-
Assess Current Processes: Conduct a thorough assessment of the existing supply chain management processes to identify areas for improvement.
-
Select the Right Vendor: Choose an APS vendor that meets the specific needs and requirements of the organization.
-
Develop a Project Plan: Create a detailed project plan and timeline to guide the implementation process.
-
Conduct Testing and Training: Ensure thorough testing of the APS system and provide comprehensive training to users to facilitate a smooth transition.
By following these steps, organizations can effectively integrate an APS system into their supply chain management processes, leading to enhanced efficiency and better customer service.
Overcoming Common Challenges in APS Implementation
Implementing an APS system can present several challenges, but with the right approach, these can be effectively managed:
-
Data Quality and Integrity: APS systems rely on accurate and timely data. Ensuring data quality and integrity is crucial for making informed decisions.
-
Change Management: Significant changes to business processes and procedures are often required. Effective change management strategies are essential to engage stakeholders and ensure their commitment.
-
Integration with Existing Systems: Seamless integration with existing ERP and other systems is necessary to ensure smooth data exchange and minimize disruptions.
-
User Adoption: Comprehensive training and support are critical to ensure users are comfortable and proficient with the new APS system.
By addressing these challenges proactively, organizations can maximize the benefits of their APS systems and achieve their supply chain management goals.
Measuring Success in Supply Chain Management
To measure the success of supply chain management initiatives, including APS implementation, organizations should focus on key performance metrics:
-
Inventory Turnover: This metric measures how often inventory is sold and replaced over a specific period, indicating the efficiency of inventory management.
-
Fill Rates: This measures the percentage of customer orders that are filled completely and on time, reflecting the effectiveness of order fulfillment processes.
-
Lead Time: This metric tracks the time it takes for products to move through the supply chain, from raw materials to delivery, highlighting areas for improvement.
-
Customer Satisfaction: Measuring customer satisfaction levels provides insights into how well the organization meets customer expectations and can drive improvements in service quality.
By regularly monitoring these metrics, organizations can gauge the effectiveness of their supply chain management strategies and make data-driven decisions to enhance performance.
The Future of Supply Chain Management
The future of supply chain management is poised to be transformed by several emerging trends and technologies:
-
Artificial Intelligence (AI) and Machine Learning (ML): These technologies will enable organizations to analyze vast amounts of data and make real-time, informed decisions, enhancing overall supply chain efficiency.
-
Internet of Things (IoT): The proliferation of IoT devices will provide real-time visibility into supply chains, allowing for more precise tracking and management of assets.
-
Blockchain: This technology will enhance transparency and security in supply chains, reducing the risk of counterfeiting and increasing customer trust.
-
Sustainability: There will be a growing focus on sustainable supply chain practices, driven by the need to reduce environmental impact and meet regulatory requirements.
By staying ahead of these trends and adopting innovative technologies, organizations can position themselves for success in the evolving landscape of supply chain management.
Scope of APS
It’s important to understand the limitations of APS in supply chain management. APS is great at efficiency and productivity through scheduling and resource coordination but plays a key role in supply chain planning by helping organizations overhaul their current planning IT to strengthen global supply chains and get the most out of their transformations. MRP is designed for material requirements and procurement processes. Sales & Operations Planning provides a broader strategic view that includes demand forecasting and financial planning which may not be fully covered by APS.
So to get a complete supply chain management approach it’s best to combine multiple tools and strategies that complement APS. By combining the strengths of different systems and methodologies businesses can address the many challenges of modern supply chain operations and get best-in-class performance across the whole value chain. A rounded approach that uses the strengths of APS with other specialist tools is the key to efficiency, cost reduction, and customer satisfaction.
ERP - APS - MES for business model transformation
Connecting Enterprise Resource Planning (ERP) systems with Advanced Planning and Scheduling (APS) software and the communication between APS and Manufacturing Execution Systems (MES) Architecture can transform manufacturing business models. By using data analytics in this integration process you can optimize production processes, reduce costs, and increase profitability. This connected approach gives operational agility and flexibility so manufacturers can respond quickly to market changes, optimize processes, and improve overall efficiency.
By connecting ERP to APS manufacturers can synchronize data across departments, streamline information flow, and make better decisions. This integration allows for planning, development, scheduling, and resource allocation to be coordinated seamlessly, resulting in optimized production schedules and better resource utilization. By connecting APS to MES Architecture you can monitor production in real-time, automate workflows, and see into the shop floor.
This connected system solution not only improves operational efficiency but also enables manufacturers to respond to disruptions, reduce downtime and meet customer expectations more accurately. By leveraging the synergy between ERP, APS and MES Architecture manufacturing businesses can be more agile, innovative and competitive in today’s fast paced market.
The five ingredients of a successful APS supply chain transformation
Almost 60 percent of IT-transforming supply chain planning takes longer or more time or money than anticipated, or is not achieved in a timely or cost effective manner. The winning method of transformation requires integrating four ingredients to deliver an at-scale impact (Exhibit 1). Often vehicles have all their equipment but without some component missing, it cannot function properly. All of our sites are accessible for disabled persons. If you have questions, we can help. Please contact Mckinney Website accessibility at www.mckinsley.org to request a copy.
FAQs
What is APS in the supply chain?
APS, or Advanced Planning and Scheduling, is a supply chain system that uses advanced algorithms to plan and schedule across the company and supply chain. It improves demand forecasting, supply planning, production scheduling and distribution planning to get better efficiency and effectiveness.
What does aps mean in logistics?
APS in logistics means using advanced algorithms to plan and schedule transportation, warehousing and distribution. It ensures goods are delivered on time and efficiently by co-ordinating all logistical support activities.
What does aps mean in manufacturing?
APS in manufacturing means scheduling of production processes to get better efficiency and productivity. It creates detailed production plans taking into account capacity, lead times, materials and resource availability.
Share this
You May Also Like
These Related Stories
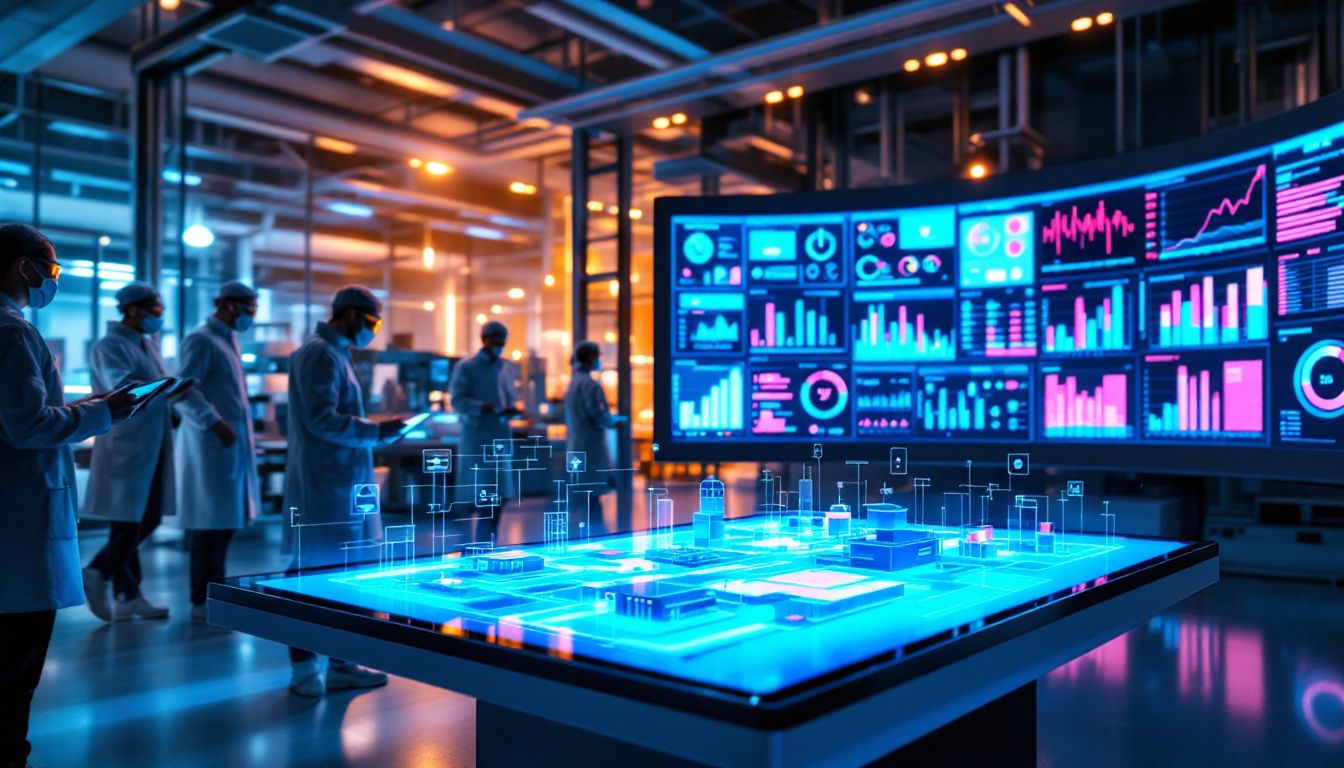
Manufacturing Scheduling Software for Small Business
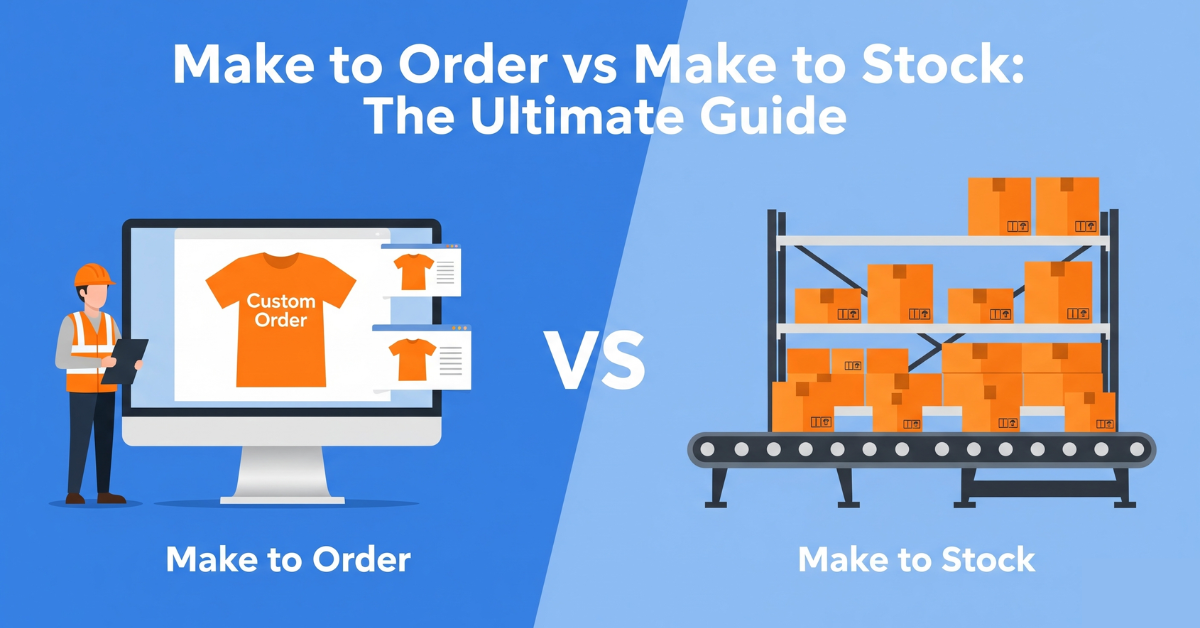
Make to Order vs Make to Stock: The Ultimate Guide
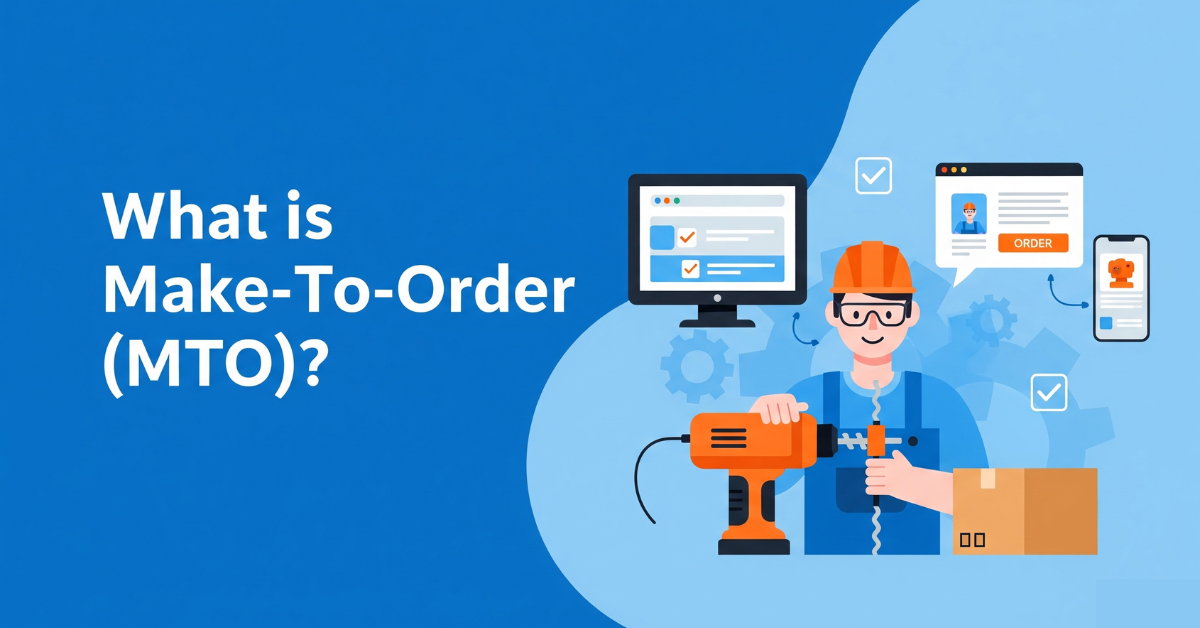
No Comments Yet
Let us know what you think