Manufacturing Operations Technology is Changing the Modern Factory
The Rise of Digitalization
The rise of digitalization has transformed manufacturing operations through the integration of IoT (Internet of Things) technology. IoT devices, like sensors and cameras, are embedded in machines and equipment to collect data across the manufacturing process, which is crucial for managing manufacturing operations to minimize costs, improve efficiency, and ensure streamlined processes.
The collected data can then be analyzed in real time, providing insights into production efficiency, machine maintenance needs, and other key performance indicators (KPIs). The integration of IoT in manufacturing has unlocked new possibilities, boosting productivity, reducing costs, and enhancing industry competitiveness.
The deployment of machine learning and artificial intelligence further enhances data analysis and automation within smart manufacturing practices. Leveraging AI and ML-enabled technology to refine the insights gained from IoT devices and improve decision-making processes, artificial intelligence plays a crucial role in Industry 4.0 by enabling predictive maintenance, efficient supply chain management, and workplace safety through its ability to analyze large amounts of data in real-time.
Embracing Smart Manufacturing Practices
By embracing the digitalization of smart manufacturing, manufacturers can be empowered to make data-driven decisions and proactively identify areas of improvement. The benefits achieved by manufacturers who switch to smart manufacturing are as follows:
-
Reduce downtime
-
Detect bottlenecks and inefficiencies
-
Improve quality control
-
Reduce waste
-
Cut costs
-
Predictive maintenance
-
Maximize equipment utilization
-
Streamline and optimize all manufacturing activities
Manufacturers leveraging these innovative approaches can achieve operational excellence, deliver high-quality products, and stay competitive in today's fast-paced market.
What is Manufacturing Operations Management?
Manufacturing Operations Management (MOM) is a comprehensive approach to overseeing and optimizing the entire production process within a manufacturing facility. It involves the coordination of various functions such as production planning, scheduling, quality management, and inventory control to ensure efficient and effective manufacturing operations. By integrating people, processes, and technology, MOM aims to enhance productivity, reduce waste, ensure product quality, and meet customer demands. This holistic approach allows manufacturers to streamline their production processes, improve operational efficiency, and achieve better overall performance.
Benefits of Implementing Manufacturing Operations Management
Implementing Manufacturing Operations Management (MOM) can bring a multitude of benefits to a manufacturing facility. One of the primary advantages is improved productivity and efficiency, as MOM systems streamline workflows and optimize resource utilization. Enhanced quality control and compliance are also significant benefits, as MOM ensures adherence to industry standards and regulatory requirements. By reducing waste and operational costs, MOM contributes to increased profitability and competitiveness. Additionally, real-time data and insights provided by MOM facilitate better decision-making, while improved communication and collaboration among teams lead to higher customer satisfaction. Ultimately, MOM helps manufacturers achieve operational excellence and maintain a competitive edge in the market.
The Top Manufacturing Trends
Several notable trends have emerged in the manufacturing industry, shaping the way businesses operate and compete in the global market. Organizations that want to stay competitive and avoid issues that have plagued others in the past must educate themselves on these trends.
Talent Shortages & Employee Retention
A major challenge for manufacturers is the dwindling labor force and the company' ongoing struggle to attract and retain skilled professionals. As the industry advances, companies are adopting innovative strategies and investing in employee-centric initiatives to create a compelling work environment. By investing in employee development and providing growth opportunities, manufacturers can ensure the retention of skilled workers and sustain their competitive edge in the industry.
Sustainability as a Game-changer
Secondly, sustainability has become a paramount concern for the manufacturing sector. Companies are increasingly incorporating eco-friendly practices, embracing renewable energy sources, and adopting circular economy principles to reduce their carbon footprint and enhance environmental stewardship. This not only aligns these industries with the growing environmental consciousness of consumers but also helps companies achieve cost savings and regulatory compliance.
Navigating Supply Chain Issues & Reshoring
Thirdly, supply chain issues and the recent surge in reshoring have taken center stage. With the disruptions caused by global events, manufacturers are reassessing their supply chain strategies, emphasizing shorter and more localized supply chains to mitigate risks. This shift not only minimizes the impact of global disruptions but also enables faster response times, greater control, and improved customer satisfaction.
The Rise of Smart Factories
Smart factories are transforming the manufacturing industry through the adoption of advanced technologies such as the Internet of Things (IoT), automation, and artificial intelligence (AI) within modern manufacturing systems. These technologies are enhancing the efficiency of production processes, minimizing errors, and significantly increasing productivity.
At the heart of this technological revolution is computer numerical control (CNC), which is essential for precision manufacturing and machining. CNC technology controls tools like laser cutters and plays a pivotal role in the automated design and production of mechanical parts.
Further integrating a manufacturing execution system (MES) allows for the real-time tracking and management of the production process. This system is vital for optimizing operations, ensuring adherence to industry standards, and improving the quality, productivity, and agility of manufacturing. It provides a comprehensive view and control over factory operations, facilitating continuous improvement and supporting the development of new business models and best practices.
AI further enhances these capabilities by analyzing data from machines, equipment, and production lines. It processes this information to detect patterns and trends that help preempt quality issues and optimize production processes. This leads to greater accuracy, more customization options, reduced downtime, and less waste, ultimately resulting in higher product quality and efficiency.
Types of Manufacturing Operations Software
There are various types of manufacturing operations software available, each designed to address specific needs and challenges in the manufacturing process. Production Management Software provides real-time data on operating jobs, orders, labor status, materials, machine status, product shipments, and delivery schedules, ensuring smooth and efficient production management. Performance Analysis Software offers accurate metrics at the machine, operations line, plant floor, and factory levels for situational or historical analysis, helping identify areas for improvement. Quality and Compliance Software promotes operations compliance against set standards and specifications for operational processes and procedures, ensuring high-quality output. Human Machine Interface (HMI) Software enables plant operators and managers to effectively coordinate industrial processes and interact with specific process control machinery using a computer-based interface. Lastly, Manufacturing Execution System (MES) software enhances manufacturing productivity, quality, and flexibility by providing plant operators, production engineers, and plant managers with the necessary insights to act and optimize.
Implementing Manufacturing Operations Management Software
Implementing manufacturing operations management software requires careful planning and execution. The first step is to define clear objectives and goals for the implementation, ensuring alignment with the overall business strategy. Next, assess current manufacturing processes to identify areas for improvement and determine the specific needs that the MOM software should address. Choosing the right MOM software that meets these needs is crucial for a successful implementation. Develop a comprehensive implementation plan and timeline, outlining the steps and resources required. Providing training and support to employees on the new software is essential to ensure smooth adoption and effective use. Finally, monitor and evaluate the effectiveness of the MOM software, making adjustments as needed to optimize performance and achieve desired outcomes.
The Rise of Advanced Manufacturing Technologies
Snic Solutions has over 15 years of experience in the manufacturing industry. We have seen the rise and fall of many trends. Having the correct manufacturing technology in place, including manufacturing operations management systems, can undoubtedly bring you closer to achieving a competitive advantage and adapting to the evolving dynamics of the industry. To assist manufacturing businesses in gaining this edge, we provide industry-tailored software solutions.
Manufacturing Operations Management (MOM) software is one of the cutting-edge technologies that is shaping the future of manufacturing. It plays a crucial role in tracking and enhancing the performance of manufacturing equipment, utilizing tools like Real-Time Location Systems (RTLS) and manufacturing execution systems (MES) software. Additionally, MOM solutions incorporate quality and compliance software, ensuring operational compliance with industry standards and enhancing adherence to strict quality standards from governing bodies like the International Standards Organization. You will see as you continue reading how effective manufacturing operations management can bridge the gap between the above-mentioned trends and organizational success.
Revitalizing the Labor Force
Given the struggle of attracting and retaining talent, leveraging technologies can enhance productivity and reduce the dependency on manual labor. MOM software helps alleviate the impact of a shrinking labor force by automating repetitive tasks and optimizing workforce utilization.
By implementing intelligent scheduling and resource allocation algorithms, MOM systems can maximize the productivity of available labor.
Additionally, MOM technology can contribute to talent retention by providing employees with user-friendly digital tools and streamlined workflows, enabling them to work more efficiently and effectively. It provides a sense of purpose and value to employees.
Enhancing Sustainability
The role of MOM technology extends beyond operational efficiency; it actively supports sustainability initiatives by optimizing energy consumption, reducing waste, and promoting environmentally friendly practices. Through data analysis and process optimization, MOM can identify opportunities for energy conservation, track and minimize material waste, and enforce compliance with sustainability standards.
Bridging the Gap for Supply Chain
By offering real-time visibility into manufacturing operations, MOM solutions empower companies to enhance their supply chain management with improved monitoring and effective management capabilities.
Through integrating supply chain data with production planning and inventory management systems, MOM helps identify potential bottlenecks, anticipate demand fluctuations, and streamline material flow. This enhanced visibility and control facilitate the reshoring efforts by enabling companies to assess the feasibility of responding quickly to disruptions.
The Smart Factory Revolution
As the foundation of smart factories, MOM seamlessly integrates the diverse array of interconnected devices and systems within the manufacturing environment. It enables real-time monitoring for continuous process improvement, which allows manufacturers to leverage the power of different types of manufacturing. This includes optimizing and analyzing manufacturing processes to improve efficiencies, track the manufacturing process, provide complete visibility, and optimize end-to-end manufacturing processes for supply chain efficiency. As all parts of manufacturing come together to turn raw materials into finished products, production management plays a vital role in coordinating and optimizing the various stages and resources involved in the production process.
Ultimately, manufacturing operations management (MOM) delivers significant value to organizations by helping them adapt to evolving industry dynamics and achieve sustainable growth in highly competitive markets to produce goods.
See it & Believe it
One example of MOM driving continuous improvement is in the automotive industry where precision, quality, and speed are paramount. It plays a crucial role in ensuring successful production runs and maintaining high standards by optimizing assembly lines, production schedules, and resource utilization, resulting in reduced cycle times, increased throughput, and making informed decisions.
MOM facilitates effective quality control and adherence to industry regulations. It enables automotive manufacturers to implement standardized processes, enforce strict quality checks, and monitor compliance with safety and regulatory standards. This results in ensuring every product meets quality standards, reduces defects, and enhances customer satisfaction.
The automotive industry heavily relies on complex supply chains involving multiple suppliers, partners, and assembly plants. MOM provides end-to-end visibility and control across the supply chain, enabling seamless coordination, communication, and collaboration.
Manufacturing operations management ensures timely availability of parts and components, reduces stockouts, and minimizes supply chain disruptions. This enhances agility and overall responsiveness to customer demands.
Improving Manufacturing Operations
Improving manufacturing operations requires a continuous effort to optimize processes, reduce waste, and enhance quality. Implementing lean manufacturing principles is a proven strategy to eliminate waste and improve efficiency. Leveraging advanced manufacturing technologies such as AI, ML, and IoT can further optimize processes and improve quality. Developing a culture of continuous improvement and encouraging employee participation are key to sustaining long-term operational excellence. Monitoring and analyzing real-time data helps identify areas for improvement and make informed decisions. Implementing robust quality control measures ensures compliance with customer expectations and regulatory requirements. Additionally, developing a comprehensive training program ensures that employees have the necessary skills and knowledge to operate effectively, contributing to overall operational success.
Maximize Success in the Manufacturing Industry
The manufacturing industry is undergoing significant transformations driven by four key trends: investing in talent, building resilient supply chains, prioritizing sustainability, and embracing smart technologies. These trends are reshaping the industry and highlighting the importance of embracing digital transformation and adopting manufacturing operations management.
As labor shortages continue to be a challenge, companies must focus on attracting and retaining talent by implementing innovative strategies such as flexible work arrangements and upskilling programs.
Sustainability is no longer an option but a necessity, as manufacturers recognize the benefits of environmentally friendly practices in terms of cost savings and reputation. The reshoring of supply chains is becoming a prominent trend, as companies aim to reduce dependency on foreign suppliers and minimize risks.
Finally, the rise of smart factories, fueled by technologies like manufacturing operations management, is revolutionizing the manufacturing landscape, enabling greater efficiency, productivity, and agility. To thrive in this changing industry, manufacturers must embrace digitalization and leverage technologies to forge a path toward a more innovative, sustainable, and technologically advanced future.
Manufacturing Technology FAQs
What is a manufacturing operating system?
A manufacturing operating system (MOS) is a collection of software and processes that manage and control the entire manufacturing process from raw material to finished product. It brings together production scheduling, quality control, inventory management and maintenance to maximise efficiency and productivity.
What is a factory operating system?
A factory operating system (FOS) is similar to a manufacturing operating system but focuses on the operations within a single factory or facility. It aims to simplify operations, improve communication across departments and make production activities within the factory more effective.
How has technology changed the process?
Technology has changed the process by bringing in automation, precision and efficiency. Advanced technologies like robotics, artificial intelligence (AI) and Internet of Things (IoT) have automated many manual tasks, reduced human error, increased speed of production and improved product quality. Technology has also improved data collection and analysis allowing for better decision making and predictive maintenance.
What are the benefits of new technology in manufacturing?
New technology:
-
Faster: Automation and process optimisation means faster production times and less downtime.
-
Better: Advanced monitoring and control technology means more consistent and better products.
-
More Flexible: Digital tools allow manufacturers to change processes and switch between product lines easily.
-
Cheaper: Automation reduces labour costs and predictive maintenance avoids costly repairs and downtime.
-
Safer: Robots and automation have taken over the dangerous tasks, reducing workplace accidents.
What is the modern factory?
The modern factory is where technology is used to create a highly efficient, automated and flexible production environment. Modern factories will have robotics, AI and IoT devices to streamline operations and increase productivity. They will also have sustainable practices and technologies to reduce environmental impact. Industry 4.0 technologies with advanced data analytics and connectivity makes the modern factory more responsive and adaptable to changing market and production requirements.
Share this
You May Also Like
These Related Stories
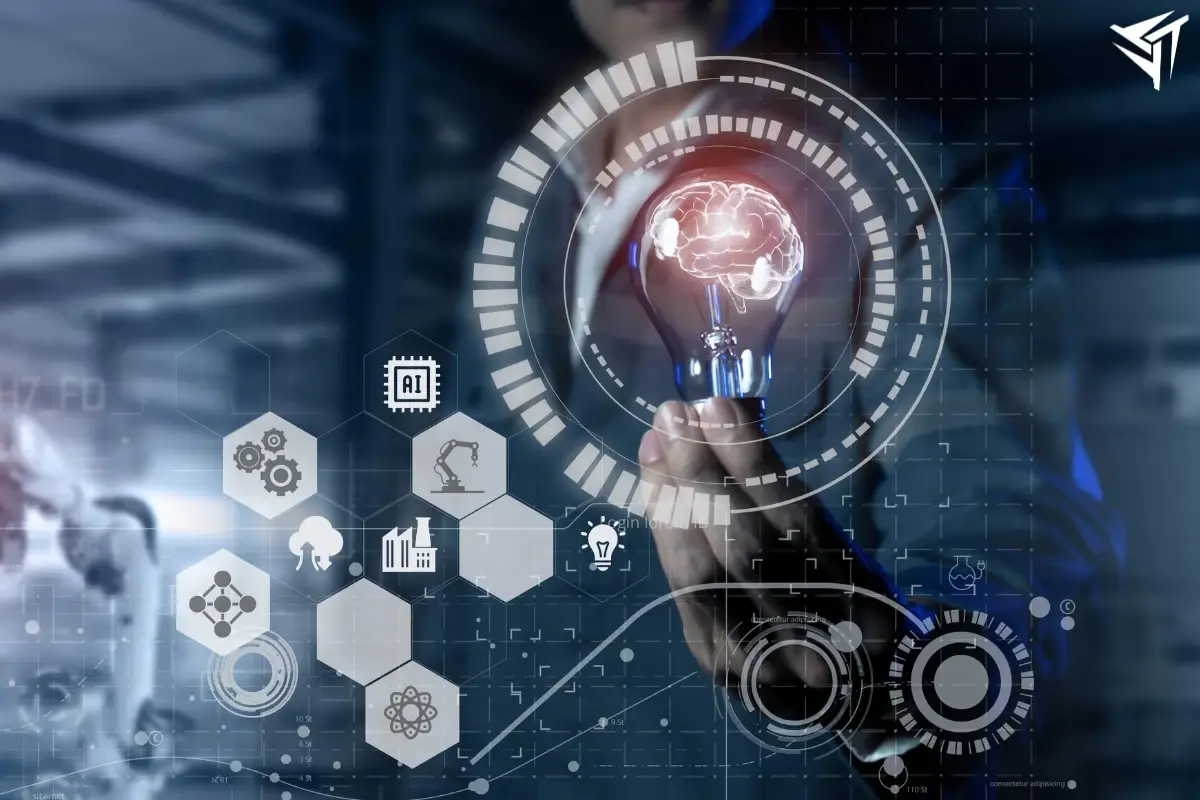
MOM Software for Lighting Manufacturers
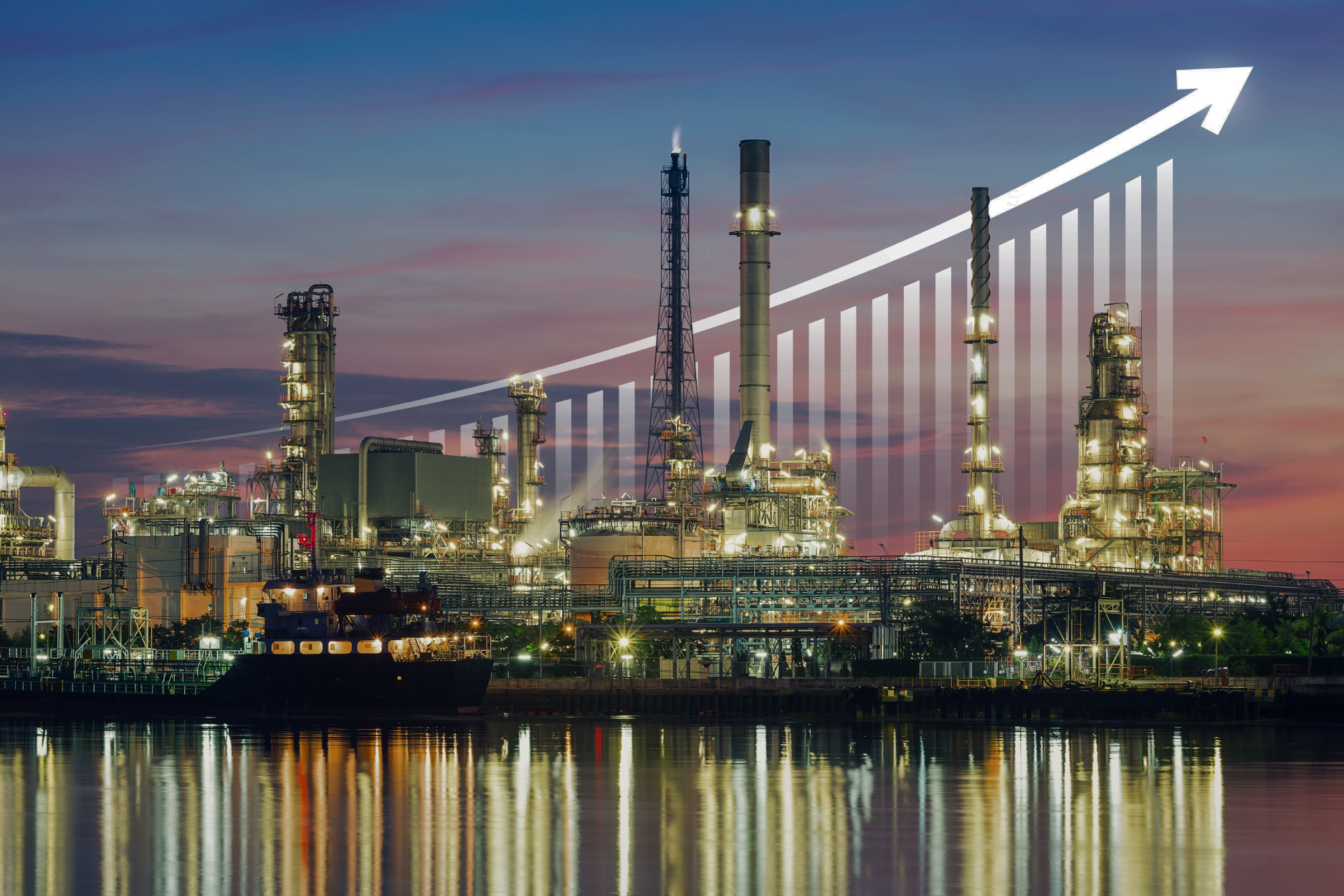
Scaling Production Processes for Small Business Manufacturers
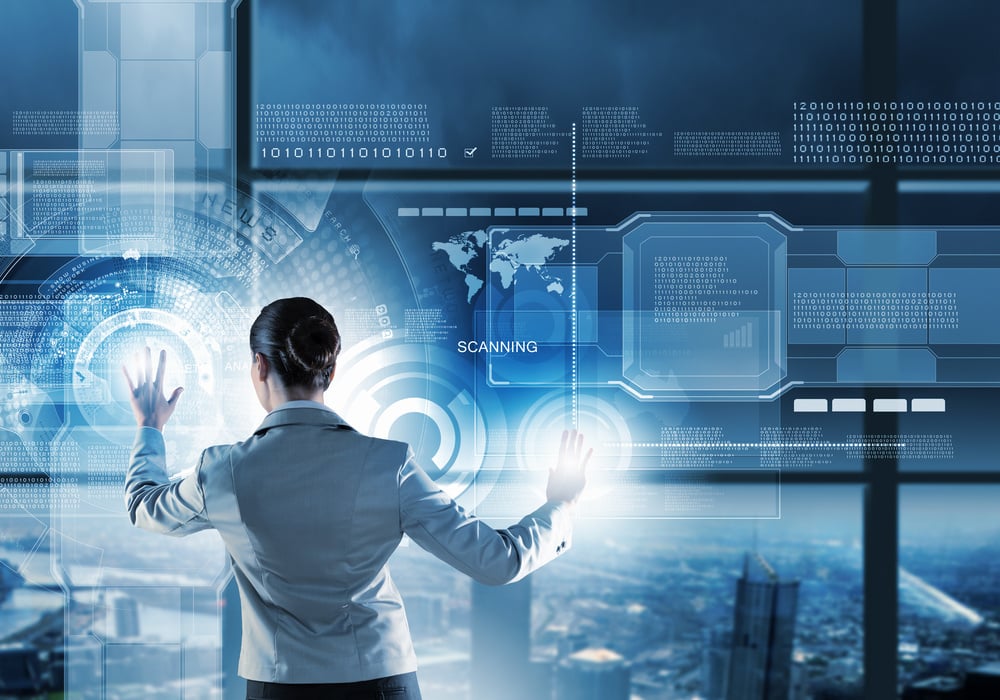
No Comments Yet
Let us know what you think