Navigating the Data Deluge: Strategies for Success in a Complex World
Explore the complex terrain of post-data collection techniques in manufacturing, unveiling the hurdles and revealing strategies to transform raw data into valuable insights.
Overproduction of data is also a waste
The manufacturing industry is embracing digital transformation, leading to many technological advancements and an exponential growth in data generation. From interconnected machines and sensors to advanced systems, manufacturers are collecting vast amounts of data. However, this wealth of information often goes underutilized, posing challenges rather than delivering the expected benefits. In this blog, we explore the hurdles manufacturers face in managing their data and reveal strategies to transform raw data into valuable insights.
The Data Deluge: A Double-Edged Sword
With the rise of automation and IoT technologies, the large amounts of data collected have become easier than ever. But this ease of collection can lead to data overload. Manufacturers are often overwhelmed by the sheer volume of information, struggling to separate valuable insights about customers from noise. This overcollection can:
-
Increase storage and management costs
-
Delay decision-making due to data complexity
-
Lead to underutilization of potentially valuable data
The Cost of Collecting Too Much
Collecting more data than you need doesn’t just add to storage costs—it makes data management and analysis harder. Data analysis is key to managing and analysing big data, so you get valuable insights and informed decision making. Manufacturers need to focus on total cost of ownership (TCO) by prioritising high value data. This means:
-
Collecting data that supports business objectives
-
Not data hoarding by setting data collection thresholds
-
Effective data storage and management solutions
The Slow Path to Value: IT-Driven Data Governance
Historically IT has managed manufacturing data. While this ensures data security and compliance it often slows down the process of turning data into action. Common challenges with patient data are:
-
Data processing delays due to IT bottlenecks
-
Business users can’t get real time data
-
Inefficiencies between business and IT teams
Data Analytics and Data Security Tools limitations
Data analytics tools are used in manufacturing to extract insights from the vast amounts of data across the operation. However these tools have limitations that can hinder their effectiveness in solving problems in a manufacturing environment. Common limitations are:
-
Unstructured data such as machine logs and sensor outputs
-
Real time analysis for timely decision making
-
Integrating data from multiple sources
-
Limited user access, requires special skills to use effectively
Collaborative Ecosystem
To enable agile data driven decision making a collaborative approach between business users and IT teams is key. By working together both sides can leverage their strengths to manage data better. Here:
-
Cross functional teams of IT professionals and business users
-
Training programs to upskill employees in data management and analysis to improve data literacy
-
Investing in collaborative tools to enable seamless communication and data sharing
Closing the Gap: Organising Data for Actionable Insights
Even with good data collection systems in place many manufacturers struggle to turn data into actionable insights. The missing link is often in organising the data. This means:
-
Structuring the data so it’s easy to access and analyse
-
Using data cataloging tools to create a single source of truth for data assets
-
Data visualisation to surface patterns and trends
Avoiding the Traps: Lessons from Early Adopters
Manufacturers just starting their digital journey can learn from early adopters' practices. One common trap is to dive straight into implementing enterprise applications without first ensuring their underlying data is organised and accessible. This leads to inefficiencies, data silos and missed opportunities for optimisation.
Collecting new data from multiple data sources such as sensors and mobile devices is key to unlocking the value of your data investments.
A better approach is to start by organising and making sense of your data before investing in enterprise tools created for specific business processes. By structuring your data, making it clean and accessible you set yourself up for any future enterprise applications. Your teams will be able to get the most out of these tools when the time comes, so implementation will be faster, decision making will be better and ROI will be higher.
By taking this step-by-step approach, manufacturers can avoid the common risks and pitfalls of early digital transformation efforts and achieve better, more sustainable outcomes.
Turning Data into a Strategic Asset
In today’s manufacturing landscape, data is a strategic asset that can drive decision-making, fuel innovation, and optimize operations. However, realizing the full potential of data requires overcoming significant challenges. Manufacturers must adopt a unique business model to effectively navigate the complexities of data-driven products and services. By adopting a collaborative approach to data science, investing in advanced data management tools, and learning from the experiences of early adopters, manufacturers can transform their data into a powerful tool for driving business value.
Ready to Turn Data into Actionable Insights?
Don't let your data go underutilized. Contact us today to discover how our expertise in manufacturing data virtualization can help you optimize your operations, reduce costs, and make smarter, informed decisions, faster. Whether you're just beginning your digital transformation journey or looking to get more value from your existing data systems, we're here to guide you every step of the way. Let's transform your data into a powerful asset for your business.
Learn more - What is Data Virtualization?
MOM Software: Turning Data Deluge into Actionable Insights
In the era of digital transformation, Manufacturing Operations Management (MOM) software has emerged as a critical tool to address the challenges posed by growing rapidly the data deluge in modern manufacturing. With vast amounts of data being generated from sensors, IoT devices, and automated systems, manufacturers need a structured approach to turn raw data into actionable insights. MOM software provides that structure, acting as the central hub for managing, analyzing, and operationalizing data.
How MOM Software Helps Solve the Data Deluge Challenge
-
Centralized Data Management:
MOM software consolidates data from multiple sources into a single, accessible platform. This eliminates data silos and ensures that all relevant information is available for analysis and decision-making. -
Real-Time Data Processing:
With AI and machine learning integration, MOM software processes data in real time, enabling manufacturers to respond proactively to issues like machine failures, production bottlenecks, or inventory shortages. -
Data Prioritization:
MOM software helps manufacturers focus on high-value data that directly supports business objectives. It filters out unnecessary noise and emphasizes actionable insights. -
Improved Data Visualization:
Advanced dashboards in MOM software offer clear and intuitive visualizations of key performance indicators (KPIs), patterns, and trends, making it easier for teams to understand and act on data-driven insights. -
Predictive Analytics Integration:
MOM software leverages predictive analytics to identify potential issues before they arise, reducing downtime, improving maintenance schedules, and ensuring efficient resource allocation. -
Seamless IT and Operations Collaboration:
MOM software bridges the gap between IT and operational teams by providing tools and interfaces that are accessible to both technical experts and frontline operators. This fosters collaboration and improves data literacy across teams.
Real-World Example of MOM Software in Action
Imagine a manufacturing plant facing production delays due to inconsistent machine performance. MOM software collects and analyzes data from machine sensors, identifying a pattern of performance drops during specific time intervals. Predictive analytics flag an upcoming machine failure, allowing the maintenance team to address the issue proactively, minimizing downtime and avoiding costly disruptions.
Why MOM Software is Essential for Managing the Data Deluge
-
Efficiency: Reduces the time spent sorting through unstructured data.
-
Clarity: Provides clear, actionable insights through advanced visualization tools.
-
Scalability: Handles increasing data volumes as manufacturing operations grow.
-
Compliance: Ensures data security and regulatory compliance standards are met.
-
Collaboration: Creates a unified platform for cross-functional teams.
From Raw Data to Strategic Decisions
MOM software doesn’t just store and display data—it transforms it into actionable intelligence. By automating data collection, refining analytics, and prioritizing insights from various sources, MOM software empowers manufacturers to navigate the data deluge effectively. This enables them to make informed, timely decisions, reduce costs, and improve operational efficiency.
Incorporating MOM software into your data science strategy is not just about managing information—it’s about unlocking the full potential of your data to drive growth, innovation, and long-term success.
FAQ: Data Overload
What is a data deluge?
A data deluge is when the amount of data is so big it’s beyond an one company or organization’s ability to manage, analyze or use it effectively. For example, social media platforms generate terabytes of data daily from user interactions, photos, videos and messages, a massive amount of unstructured data that requires advanced analytics to make sense of.
Where does the big data deluge come from?
-
Internet of Things (IoT): Sensors and devices generating continuous streams of data.
-
Social Media: User generated content like posts, comments, videos and images.
-
Business Operations: Enterprise data from transactions, customer interactions and supply chains.
-
Scientific Research: Big datasets from experiments, simulations and observational studies.
-
Healthcare: Electronic health records, medical imaging and wearable device data.
How do organizations deal with data deluge?
Organizations can manage data deluge by:
-
Data Governance: Setting policies for data quality, security and lifecycle.
-
Data Filtering: Filtering out relevant and actionable data and discarding the rest.
-
Scalable Infrastructure: Cloud based storage and processing solutions.
-
Advanced Analytics: Using AI and machine learning to process and extract insights quickly.
-
Automation: Automating data integration, reporting and workflow to reduce manual intervention.
What are the challenges and opportunities for organizations with this data deluge?
Challenges:
-
Storage Costs: It’s expensive to store so much data.
-
Data Privacy: Compliance with data protection regulations like GDPR.
-
Complexity: Analyzing and integrating unstructured data from multiple sources.
-
Decision Fatigue: Decision makers are overwhelmed with too many data points.
Opportunities:
-
Better Decision Making: Insights from big data to make informed and timely decisions.
-
Personalization: Customer experiences through data driven strategies.
-
Innovation: Finding trends and opportunities for new products and services.
-
Efficiency: Streamlined operations and resource management.
-
Data Scientist Role: Data scientists are key to managing and analyzing large datasets to drive innovation and growth.
By dealing with these challenges organizations can unleash the power of big data for innovation and growth.
Share this
You May Also Like
These Related Stories
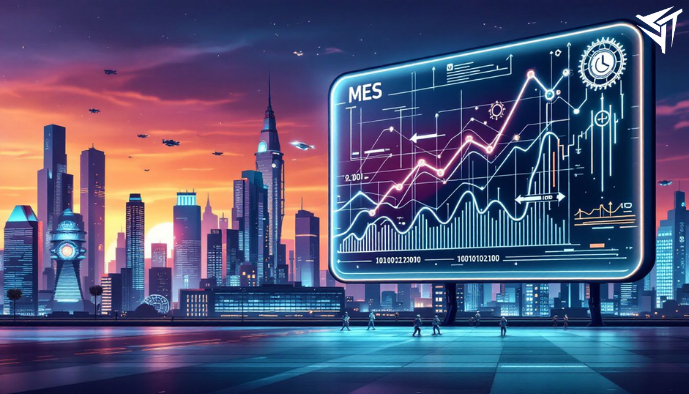
Essential Guide to Downtime Tracking for Better Efficiency
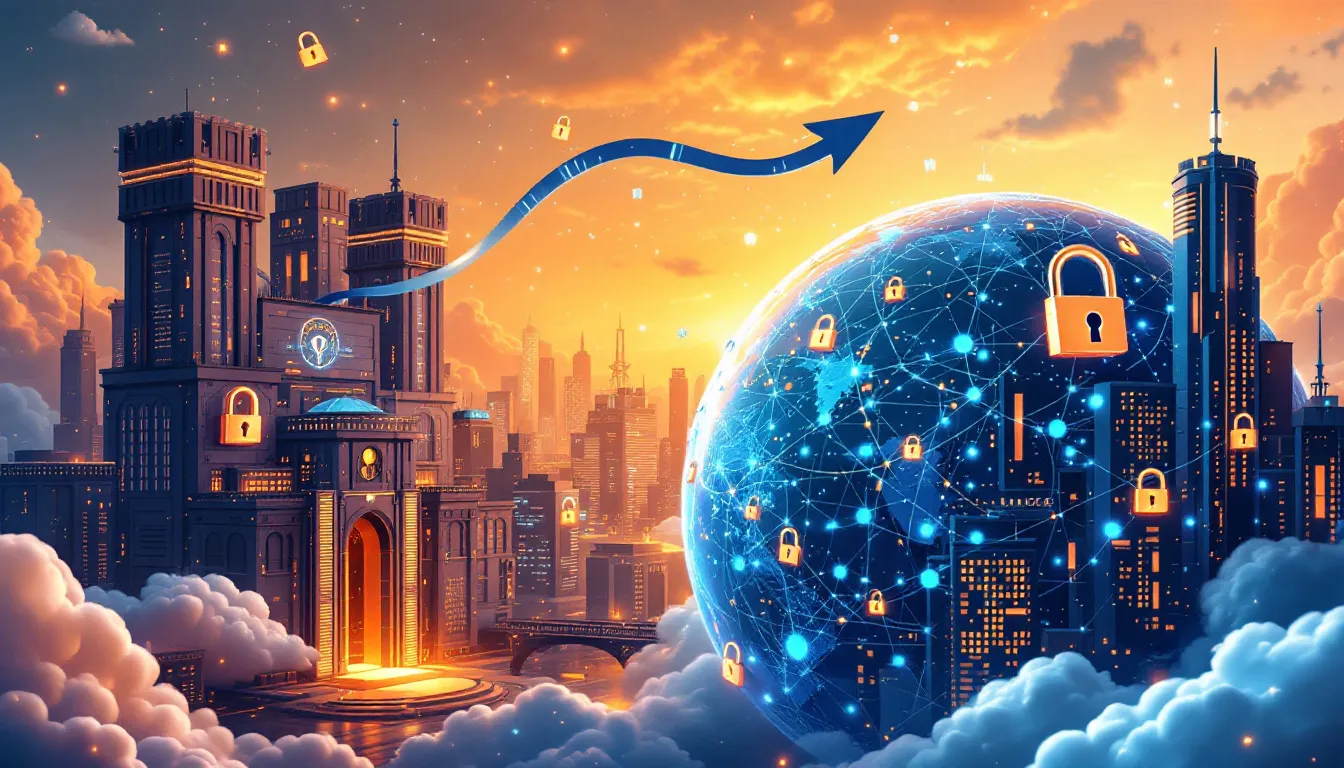
Data Virtualization vs Data Warehouse: Essential Differences Explained
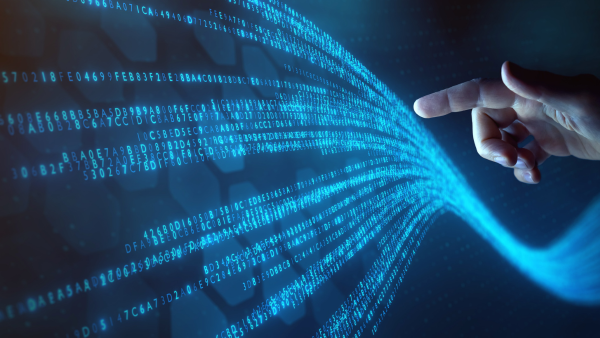
No Comments Yet
Let us know what you think