Top Principles of Lean Manufacturing Every Professional Should Master
Looking to elevate your manufacturing processes? Lean manufacturing is designed to enhance efficiency, minimize waste, and significantly improve product quality. Master these core principles to streamline your operations and achieve sustained success.
Looking to elevate your manufacturing processes? Lean manufacturing is designed to enhance efficiency, minimize waste, and significantly improve product quality. Master these core principles to streamline your operations and achieve sustained success.
Top Lean Manufacturing Principles:
1. Identifying Value Streams
A critical step to optimizing processes involves clearly defining value from the customer’s perspective. Value stream mapping helps visualize every step involved in delivering a product, highlighting activities that add value and removing those that do not.
2. Eliminating Waste
Waste in manufacturing refers to anything consuming resources without contributing value to the final product. Lean manufacturing targets various forms of waste, including overproduction, excess inventory, unnecessary movement, and downtime, to enhance operational efficiency and reduce costs.
3. Ensuring Maximum Quality
Quality assurance is central to lean manufacturing, emphasizing error prevention and continuous improvement. Techniques such as process control charts and Poka-Yoke (error-proofing) ensure high product quality, reduce defects, and enhance customer satisfaction.
4. Continuous Improvement (Kaizen)
Continuous improvement encourages incremental enhancements in manufacturing processes, driven by employee suggestions and ongoing evaluations. Kaizen fosters a proactive culture focused on constantly refining processes and reducing waste.
5. Continuous Flow Production
Maintaining continuous flow minimizes delays and disruptions in manufacturing, improving efficiency. The goal is to ensure seamless transitions between steps in the production process, avoiding bottlenecks and downtime.
6. Facility Organization (5S Methodology)
The 5S approach—Sort, Set in Order, Shine, Standardize, Sustain—promotes workplace organization, improves productivity, and creates an efficient working environment.
7. Kanban Workflow Management
Kanban systems visualize workflows, manage task assignments, and enhance team communication, promoting accountability and reducing inefficiencies.
8. Takt Time Alignment
Takt time synchronizes production rates with customer demand, ensuring timely product delivery while minimizing excess production and waste.
9. Advanced Statistical and Control Methods (SPC)
Statistical Process Control (SPC) monitors manufacturing consistency, identifies variations, and facilitates corrective actions, significantly improving product quality and operational efficiency.
10. Ongoing Professional Education
Continuous education and training empower teams to effectively implement lean principles, adapt to new technologies, and maintain competitive advantage.
Understanding the Core Principles of Manufacturing
Manufacturing principles serve as the bedrock of efficient and productive factory operations in advanced manufacturing . These principles encompass the core truths explaining how manufacturing processes work and are essential for any manufacturing engineer or professional aiming to streamline operations and enhance product quality. Lean manufacturing principles, for instance, focus on saving money and improving efficiency across various sectors. Understanding value from the customer’s perspective is paramount, as it shapes the entire manufacturing strategy, providing a fundamental basis for success. The Principles of Manufacturing are a set of elements common to all manufacturing industries that revolve around the concepts of flow and variations.
Mastering these principles in the mechanical engineering department requires fundamental skills and highlights the fundamental skills needed for success in manufacturing.
The lean manufacturing system, which aims to deliver better value, reduced costs, and near-perfect goods, as taught in the mitx micromasters program is built on five essential principles. These principles include identifying value streams, eliminating waste, and ensuring maximum quality. Each of these elements common to successful manufacturing systems will be explored in detail to provide a comprehensive understanding of how they contribute to the overall efficiency and effectiveness of manufacturing enterprises. Manufacturing involves production in volume with a continuous flow of new materials going through a system of unit processes.
Both the research and practical applications have shaped the development of these core manufacturing principles.
Identifying Value Streams
Identifying value streams is a critical step in optimizing manufacturing processes. A value stream encompasses the sequence of activities that deliver value to the customer, and if an activity doesn’t add value, it doesn’t belong in the value stream. Value stream mapping allows manufacturers to visualize and optimize their operations, aligning them more closely with customer expectations.
Accurate forecasting and a pull system, driven by actual demand, align production with customer needs and minimize waste.
Eliminating Waste in Manufacturing Processes
In the lean manufacturing context, waste refers to any activity or material that consumes resources or space without adding value. Identifying and eliminating waste enhances efficiency and reduces costs for manufacturing firms. Necessary waste may require refinement, while pure waste should be eliminated.
This approach not only optimizes manufacturing systems but also ensures that resources are used effectively. Minimizing unnecessary movement of resources and optimizing inventory management are key strategies in this regard.
Ensuring Maximum Quality
Ensuring maximum quality through feedback control methods is at the heart of lean manufacturing. The focus is on delivering a perfect product through productive workflows and minimal waste. Lean manufacturing emphasizes both quality and the elimination of errors to ensure maximum quality product excellence. Costly defects lead to wasted raw materials and finished products, increased customer returns, and reduced perceived value.
Process control charts are vital tools used to analyze quality in lean manufacturing, helping organizations identify weak links and streamline operations.
Optimizing Manufacturing Systems for Efficiency
Optimizing manufacturing systems is essential for achieving efficiency and meeting customer demand. Implementing strategies like continuous flow, organizing the manufacturing facility, and adjusting takt time based on customer demand can significantly enhance operational performance. Continuous flow in manufacturing minimizes delays and enhances overall production efficiency, ensuring steady operation of every production step and avoiding bottlenecks. This approach is crucial for maintaining productivity and reducing waste.
Effective use of business information supports decision-making and strategic planning in manufacturing operations by linking business objectives with production activities and improving management across areas such as marketing and finance.
Organizing the manufacturing facility is another critical aspect of optimizing systems to operate systems. A well-organized workspace can significantly enhance productivity and reduce operational inefficiencies. The 5S system and tools like Kanban boards serve as effective frameworks for organizing workplaces in lean manufacturing.
Additionally, adjusting takt time based on customer demand ensures that controlling temporal production rates align with market needs, minimizing waste and enhancing efficiency.
Continuous Flow in Manufacturing
Continuous flow production is most effective in environments where products are consistently created through defined steps. This approach ensures steady operation of every production step, controlling flows and avoiding bottlenecks and hold-ups.
Investments in the bottleneck yield the best returns in manufacturing, as unreliable machines can fail and stop production, affecting nominal production rates. Identifying and addressing defects promptly can prevent significant waste of materials and resources.
Organizing the Manufacturing Facility
A well-organized manufacturing facility is essential for optimizing production processes.
The 5S system consists of:
-
Sort
-
Set in Order
-
Shine
-
Standardize
-
Sustain
This system helps eliminate waste, enhance productivity, and ensure that tools and materials are readily accessible.
Additionally, Kanban boards serve to visualize workflow and enhance team communication, making it easier to manage tasks and responsibilities.
Adjusting Takt Time Based on Customer Demand
Takt time is a crucial measurement in manufacturing, determined by business dynamics statistics, for the time needed to produce each product based on customer demand within a time system. Understanding and implementing proper takt time management helps align production rates with customer demand, minimizing waste and enhancing efficiency.
Designing processes for smooth workflows helps manufacturers meet customer demand and maintain optimal capacity through product engineering and product and process design. This process design program aids in achieving efficiency.
Leveraging Lean Manufacturing Techniques
Lean manufacturing techniques are essential for enhancing critical processes and reducing waste in manufacturing industries. These techniques include Poka-Yoke for error prevention, Just In Time inventory management, and engaging employees with lean tools. Embracing lean manufacturing principles not only leads to optimal inventory management but also fosters a culture of continuous improvement. Organizations adopting lean manufacturing should focus on technology and training to engage employees and drive efficiency.
Poka-Yoke techniques aim to design processes that prevent errors before they occur, ensuring maximum quality in production. Just In Time inventory management relies on actual customer demand to drive production schedules, reducing inventory levels, and improving cash flow.
Engaging employees through tools like Kanban boards and Gemba Walks enhances accountability and fosters direct communication, promoting a culture of continuous improvement.
Implementing Poka-Yoke for Error Prevention
Poka-Yoke is a lean technique that prevents errors through simple mechanisms. Designing processes to prevent errors ensures maximum product quality. This approach not only reduces defects but also enhances overall production efficiency and reliability.
Just In Time Inventory Management
Just In Time inventory management is a key component of lean manufacturing, aligning production schedules with actual customer demand. This practice reduces inventory levels, leading to lower costs and improved cash flow. Eliminating waste and enhancing overall efficiency, Just In Time inventory management plays a crucial role in optimizing supply chains and manufacturing.
Engaging Employees with Lean Tools
Engaging employees is crucial in lean manufacturing. Tools like Kanban boards and Gemba Walks play a significant role in this process. Kanban boards serve as a visual representation of task status, responsibilities, delays, and due dates, enhancing accountability among employees.
Gemba Walks involve observing factory operations firsthand and foster direct communication, thereby enhancing employee engagement and promoting a culture of continuous improvement.
Advanced Statistical and Control Methods in Manufacturing
Advanced statistical and control methods are essential for maintaining consistency and quality in manufacturing processes. Statistical Process Control (SPC) is a method that helps monitor and control the manufacturing process to ensure consistency and quality. Statistical methods in SPC analyze variations, identifying when processes are out of control, and enabling corrective actions to maintain quality. Integrating SPC with data analytics allows manufacturers to enhance process control, reduce waste, and improve overall product quality. Technology developers play a key role in implementing these advanced statistical and control methods to improve manufacturing processes. Statistical process control is a method used to optimize quality over large flows when testing all produced parts is either too costly or impossible.
Data-driven decision-making leverages analytics to optimize manufacturing systems, leading to improved operational decision-making and resource allocation. Data collection and analysis enable manufacturers to make informed decisions, boosting production efficiency and quality. Real-time data collection is essential for timely adjustments in manufacturing operations, ensuring that processes remain efficient and effective.
Statistical Process Control (SPC)
Statistical Process Control (SPC) is utilized to monitor and enhance manufacturing processes by identifying temporal and spatial variation and ensuring manufacturing process control and process stability. The primary goal of SPC is to maintain process consistency and improve product quality.
Process control charts are utilized to visualize process performance and variability over time, helping manufacturers identify and address issues promptly.
Data-Driven Decision Making
Effective data analysis is essential for making informed decisions in manufacturing, allowing for the optimization of systems based on real-time insights. Analyzing data enhances decision-making by providing insights into production efficiency and quality.
Real-time data collection enables timely adjustments in manufacturing operations, ensuring that processes remain efficient and effective while providing up to date information.
Designing Optimal Supply Chain Systems
Designing optimal supply chain systems is crucial for efficient manufacturing processes. Organizations that succeed in the supply chain industry focus on using resources efficiently. They also emphasize the management of streamlined processes. Effective supply chain design and planning are essential for optimizing manufacturing processes and ensuring product availability. This involves managing inventory, planning capacity, and network design to enhance supply chain performance.
Inventory analytics plays a crucial role in managing supply chain efficiency and ensuring that customer demand is met. Analyzing inventory data helps manufacturers maintain optimal levels, cutting costs and boosting productivity. Methods for modeling inventory, such as the News Vendor Problem and Economic Order Quantity Model, help optimize inventory management and enhance overall supply chain performance.
Supply Chain Design and Planning
Effective supply chain design and planning are crucial for optimizing manufacturing processes and ensuring product availability. A supply chain engineer managing inventory and planning capacity and network design are key components of this approach.
Efficient supply chain strategies enhance operational efficiency and reduce costs for manufacturers.
Inventory Analytics for Supply Chains
Inventory analytics plays a crucial role in managing supply chain efficiency and ensuring that customer demand is met. In volume manufacturing, i ventory acts as a buffer, allowing operations to continue during machine downtime and enhancing productivity.
Methods for modeling inventory, such as the News Vendor Problem and Economic Order Quantity Model, help optimize inventory management and enhance overall supply chain performance.
Continuous Improvement in Manufacturing
Continuous improvement is a cornerstone of lean manufacturing, especially for new manufacturing firms driven by methodologies like Kaizen and Six Sigma to enhance operations. The ultimate goal is to enhance customer experience, reduce steps in the product life cycle, and minimize costs and waste. Continuous improvement is not a project but a system that fosters ongoing enhancements to processes. However, focusing too much on cutting waste can negatively affect employee wellbeing and overlook future needs.
Monitoring progress with key metrics and engaging in continuous improvement initiatives are essential strategies for achieving continuous improvement. Key performance indicators (KPIs) are essential for tracking manufacturing performance and optimizing processes.
Creating a culture of continuous improvement requires open communication and encourages team members to suggest enhancements.
Monitoring Progress with Key Metrics
Key performance indicators (KPIs) are essential for tracking manufacturing performance and optimizing processes. Common KPIs in manufacturing include throughput, cycle time, and inventory turns, which help assess operational efficiency.
Effective monitoring in lean processes often involves using key performance indicators to assess various operational levels and identify areas for improvement.
Engaging in Continuous Improvement Initiatives
Creating a culture of continuous improvement relies heavily on employee involvement and proactive problem-solving methods. Tools like Gemba Walks, which involve observing factory operations firsthand, and encouraging team members to suggest enhancements, foster a culture of continuous improvement. Underutilized talent can result in waste if skilled individuals are not assigned appropriate tasks.
Open communication and feedback loops facilitate adjustments and innovations in manufacturing processes, ensuring that improvements are continuously made.
Frequently Asked Questions
What are the key principles of lean manufacturing?
The key principles of lean manufacturing include identifying value streams, eliminating waste, ensuring maximum quality, and engaging employees through the use of lean tools. These principles collectively enhance operational efficiency and drive continuous improvement. Lean manufacturing enhances customer satisfaction by increasing value while keeping prices low.
How does Just In Time inventory management work?
Just In Time inventory management effectively aligns production schedules with actual customer demand, thereby minimizing inventory levels and enhancing cash flow. This approach allows businesses to respond quickly to market needs while reducing waste and costs.
What is the importance of Statistical Process Control (SPC) in manufacturing?
Statistical Process Control (SPC) is crucial in manufacturing as it monitors and controls processes to maintain consistency and quality by identifying variations, which allows for timely corrective actions. Consequently, this leads to reduced defects and improved overall efficiency in production.
How can continuous improvement initiatives enhance manufacturing processes?
Continuous improvement initiatives, utilizing methodologies such as Kaizen and Six Sigma, enhance manufacturing processes by fostering ongoing efficiencies and cost reductions. This leads to streamlined operations and increased productivity.
Share this
You May Also Like
These Related Stories
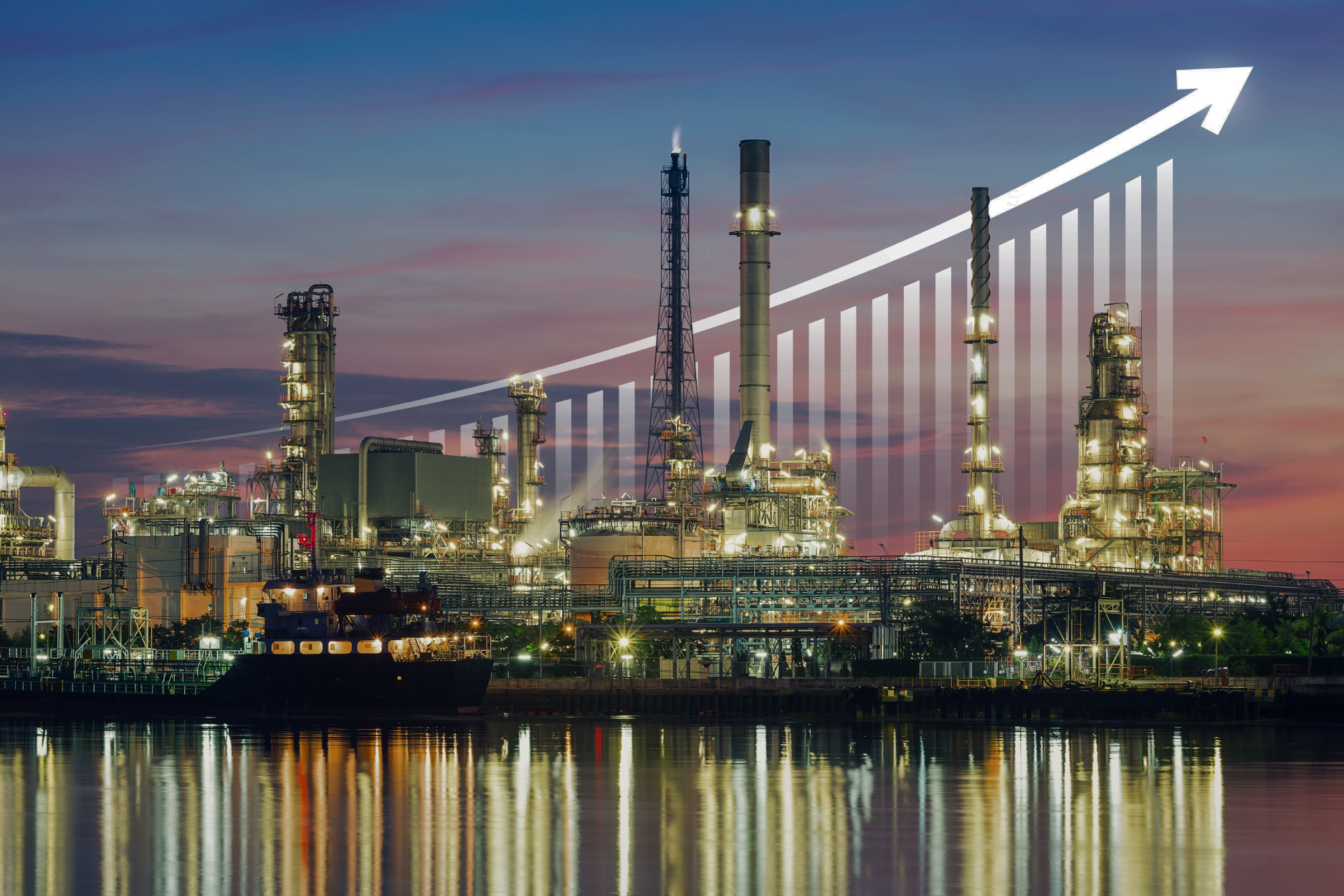
Scaling Production Processes for Small Business Manufacturers
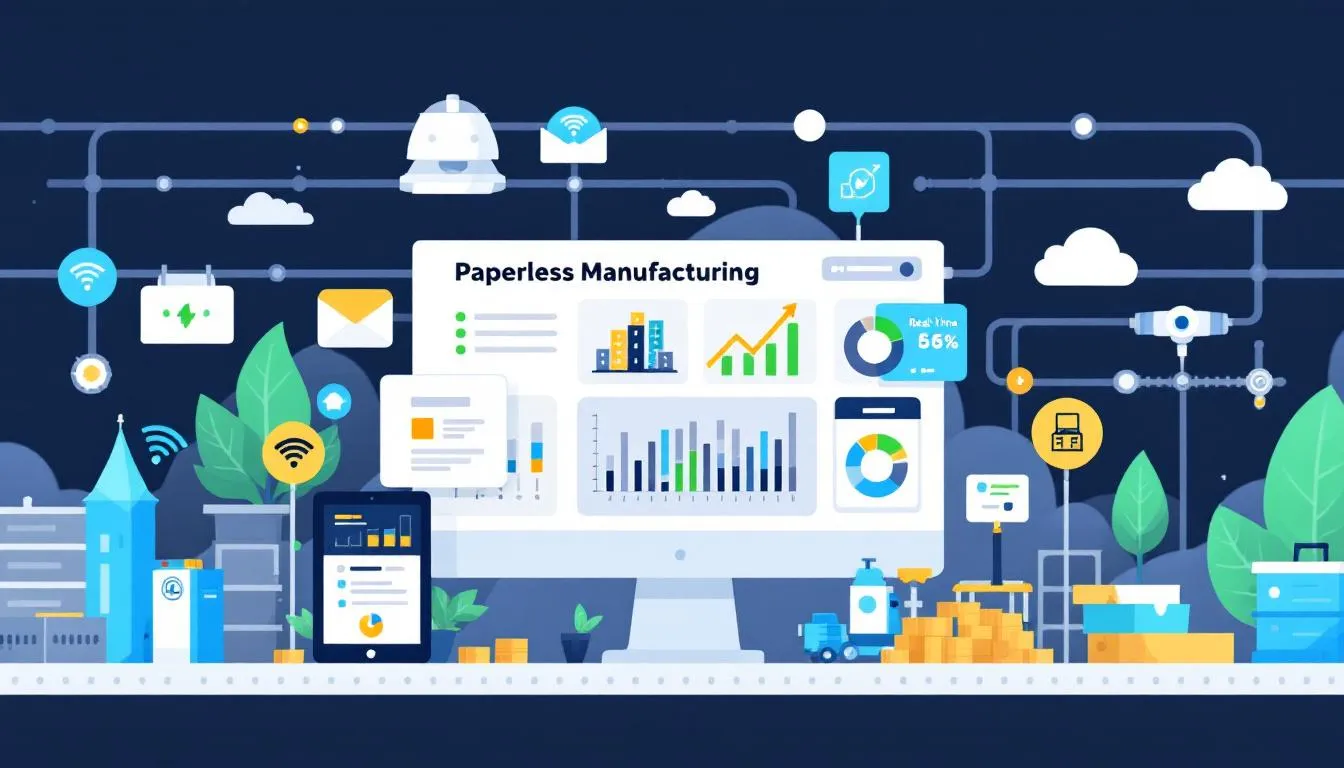
How to Go Paperless in Manufacturing: A Practical Guide
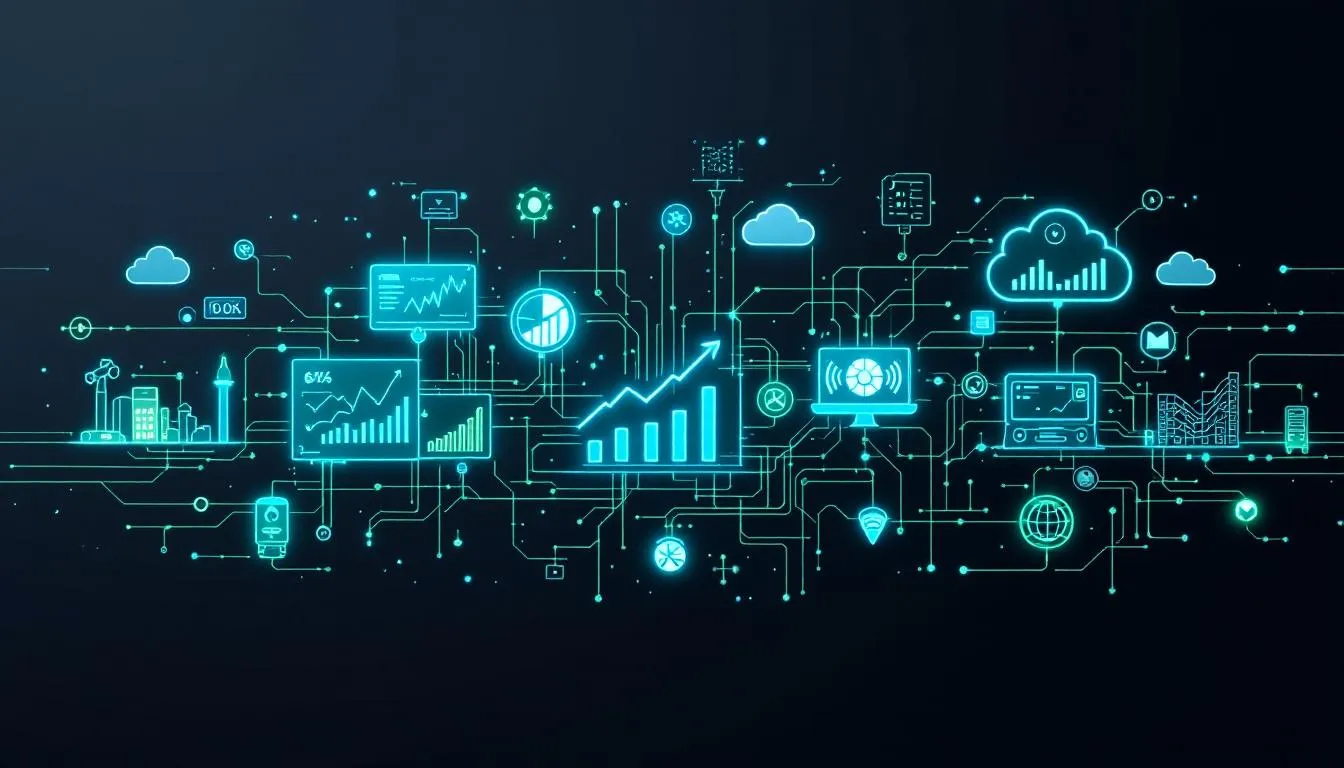
No Comments Yet
Let us know what you think